Manufacturers of goods ranging from automotive parts to housewares increasingly seek to incorporate recycled plastics in their applications to reduce costs, differentiate their products from those of their competitors or satisfy demands from retailers and consumers for sustainable products.
To meet the needs of these manufacturers, suppliers of recycled resins can face major challenges in developing materials that deliver targeted performance and processing characteristics. Because recycled plastic streams typically contain a mix of materials—even polyethylene terephthalate (PET) bottles, the most consistent stream—recyclers must fine-tune their resins for each application. While blending is a common approach, additives targeting specific properties can offer greater precision and consistency and less trial and error in producing optimized resins.
Adjusting resin properties
When requesting materials from a recycler for a given application, manufacturers specify properties, such as stiffness, tensile strength, modulus and melt flow, based on the characteristics of the virgin resin. However, the performance properties and aesthetics of recycled plastics usually differ from those of virgin materials. They can be degraded or changed by numerous factors, including additives that were previously used, cross-contamination with other resins and exposure to heat or other environmental stresses. To deliver what the customer is asking for, recyclers can use additives such as peroxides, antioxidants, chain extenders, elastomers, colorants, performance modifiers and nucleators to restore diminished properties or to compensate for undesirable attributes.
For instance, clear recycled PET bottles will discolor (yellow) after melting and reforming. Other causes of color shifting may include low levels of residual nylon from multilayer bottles and the presence of additives, such as ultraviolet (UV) light blockers, acetaldehyde
Another issue with recycled PET bottles is the breakdown of polymer chains that occurs when the resin goes through multiple heat cycles. As the chains degrade under repeated remelting and reprocessing, PET’s intrinsic viscosity (IV) drops. As a measure of molecular weight, IV reflects chain length and mechanical properties such as flow. High IV is important for optimizing the injection stretch blow molding process used for PET bottles, as it enables thinner walls needed to control packaging costs without sacrificing strength.
To meet growing demand from beverage makers for significant amounts of recycled content in their bottles, recyclers use chain extenders to raise PET’s IV. These additives are molecules that attach to the ends of broken polymer chains, reconnect them and produce the longer chains needed for
Downsides of chain extenders can include cost and the limited availability of products that are food-contact compliant.
Switching processing methods
Another common challenge for recyclers is adapting materials originally formulated for one process to be used effectively for a different one. For instance, extruded packaging film and thermoformed consumer products made with polypropylene (PP) often are recycled for use in injection-molded industrial parts, such as pallets and crates, and outdoor furniture, planters and the like. The main disparity between these processes is melt flow. Extruded and thermoformed products require high melt strength to optimize properties such as drawdown and sag. Achieving high melt strength calls for a high molecular weight, which reduces melt flow. (The typical melt flow range for extrusion/thermoforming is two to 10.)
Switching to injection molding changes these parameters dramatically. Injection molding requires a high melt flow (10 to 80) for high throughput and complete mold filling. Intrinsic high melt flow also reduces the amount of heating needed and associated energy costs.
The traditional way to reduce recycled PP’s molecular weight (thereby increasing melt flow) is to add peroxide, which severs polymer chains (scission). However, a side effect of chain breakage is its negative impact on PP stiffness and impact properties. Good impact strength (ability to withstand a suddenly applied load) and impact resistance are needed for applications such as auto bumpers and appliance parts.
To help restore impact performance, recyclers add rubber or other elastomers to the resin. These impact modifiers, however, can be expensive. As more elastomers are added, the price of recycled PP can approach that of virgin resin, eliminating the recycler’s price advantage. Also, elastomers make the recycled resin soft and viscous, reducing its stiffness and its suitability for many applications.
Adding advanced compatibilizers
A novel additive can resolve the dilemma of how to boost PP’s melt flow without degrading impact strength or loading up on costly elastomers. Milliken’s new Delta-?Max compatibilizer is a unique additive that targets three separate properties simultaneously—melt flow, stiffness
Increasing stiffness
Although the DeltaMax compatibilizer helps to retain PP’s inherent stiffness by reducing the effects of peroxide and rubber, sometimes a recycler’s customers require additional stiffness. Talc is widely used in automotive and appliance parts to increase the stiffness of recycled PP. Advantages include the ability to control talc particle size and shape to influence the resin’s morphology. Talc also is inexpensive.
Enhancing the stiffness of recycled PP enables thin-wall designs that reduce material usage to drive down costs. It also allows recycled PP to be used in place of more expensive virgin or wide-specification resins.
Going beyond blending
Rising resin prices, combined with environmental concerns, are driving demand for recycled content in plastic products. To meet
Milliken continues to be a leader in the development of additives that give recyclers new tools to meet customer requirements regarding performance, processability
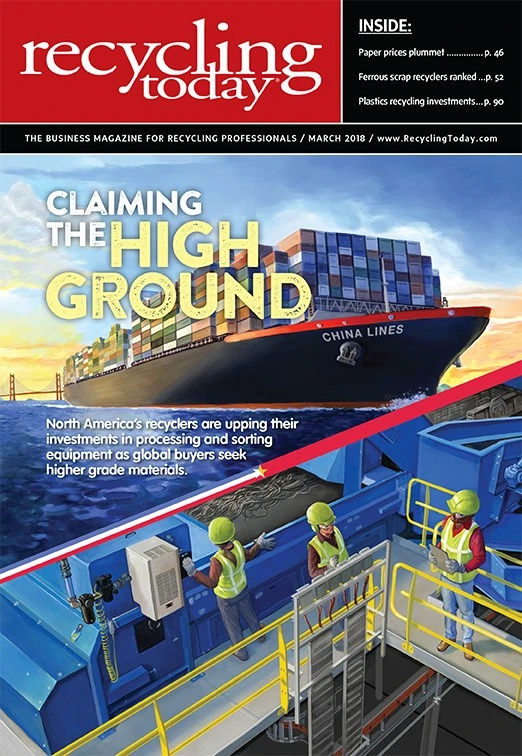
Explore the March 2018 Issue
Check out more from this issue and find your next story to read.
Latest from Recycling Today
- Cyclic Materials to build rare earth recycling facility in Mesa, Arizona
- Ecobat’s Seculene product earns recognition for flame-retardant properties
- IWS' newest MRF is part of its broader strategy to modernize waste management infrastructure
- PCA reports profitable Q1
- British Steel mill subject of UK government intervention
- NRC seeks speakers for October event
- LME identifies Hong Kong warehouses
- Greenville, Mississippi, launches aluminum can recycling program