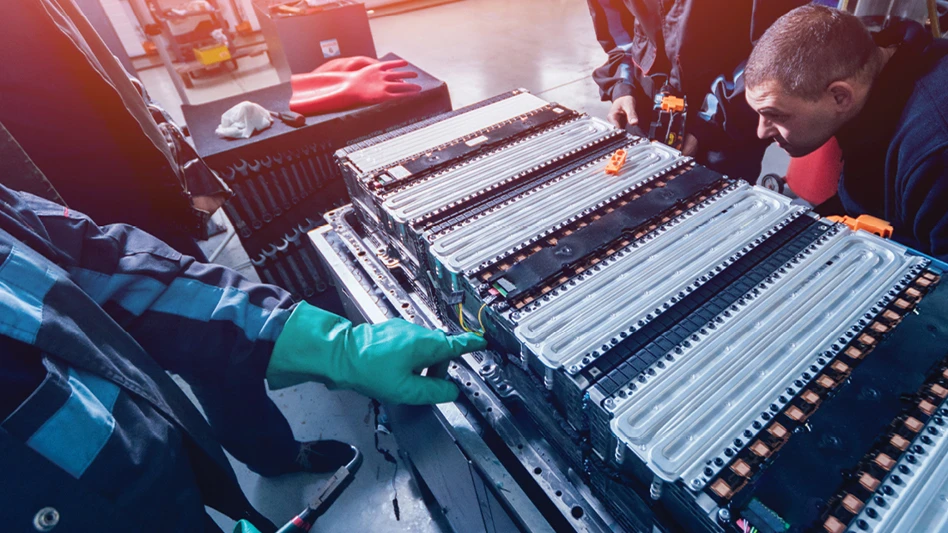

The rechargeable batteries from electric and hybrid vehicles present challenges and opportunities for the recycling companies that deal with them. While a limited quantity of these batteries currently is being recovered from end-of-life vehicles, that number will increase as manufacturing and sales of electric vehicles (EVs) grow.
The profile of lithium-ion battery (LIB) recycling has grown in recent years largely because of the potential growth in EV production. In 2021, President Joe Biden’s administration announced a goal to have 50 percent of all vehicles sold in the U.S. by 2030 be zero-emission vehicles, while automakers such as General Motors and Ford have announced plans to expand EV production capacity. Manufacturers will need recycled feedstock to supplement the virgin material they use in EV battery production. The LIBs used in EVs present risks for the recycling community that is challenged to find solutions for safely recovering these large-format batteries, said Eric Fredrickson, vice president of operations at Call2Recycle, headquartered in Atlanta.
“There’s a Venn diagram of compliant and safe,” he said of handling end-of-life rechargeable batteries. “You can be compliant without being safe, and you can be safe without being compliant. If your organization is struggling with what to do with these batteries and how to do it, then Call2Recycle oftentimes is a great resource for you to better understand the risks associated with what you’re doing.”
Fredrickson moderated a panel that included representatives from across the LIB value chain at the inaugural Battery and Critical Metals Recycling Conference in Atlanta this June.
Bringing recycling to the fore
“We didn’t really think about recycling until recently,” Ascend Elements Vice President of Global Marketing and Government Relations Roger Lin said regarding LIB manufacturing. “And it’s been brought on by a big wave of demand for electric vehicles.”
Westborough, Massachusetts-based Ascend Elements produces battery materials using elements reclaimed from end-of-life LIBs using its patented Hydro-to-Cathode direct precursor synthesis technology to produce new cathode materials. Ascend has a recycling facility in Covington, Georgia, and is building a second plant in Hopkinsville, Kentucky, that it says will be the largest EV battery recycling and engineered materials manufacturing facility in the U.S.
Recovering the materials used to produce LIBs and keeping them in the supply chain is one of Ascend Elements’ goals and what Lin said attracted him to the company, adding that economic drivers and supply chain security concerns are driving the growth in the EV battery recycling space.
Auto parts recyclers are “the frontline for EV recovery,” said Derick Corbett, senior vice president of external affairs at Atlanta-based Pull-A-Part. “It all, for the most part, starts with us. And we’re not new to this,” he added, noting that established mechanisms are in place for companies like his to supply companies like Ascend Elements with the commodities recovered from EVs.

Establishing processes
Corbett said Pull-A-Part is the largest privately owned auto recycler in the U.S., operating 36 yards across 16 states.
When the company receives an EV at the end of its life, “it is up to us to figure out how to dismantle it and make sure that all of the valuable pieces get somewhere,” he said. “You have to come up with new processes; you have to come up with new procedures. And that’s what the auto recycling industry has been working on over the last couple of years.”
Corbett said when an auto recycling facility receives an EV, it must first “power down,” or discharge, the LIB. “That’s no easy task because they magically repower themselves,” he added.
To remove the battery, which weighs 1000 pounds and is about 6 feet long, it must be decoupled from the vehicle before the chassis is lifted off the battery. “Then you have to find a way to store [the battery] safely,” Corbett said. He noted that processing an EV for reuse is not much different from processing an internal combustion engine (ICE) vehicle, though there are differences. In addition to discharging the battery and lifting the vehicle off the battery pack, he said storage also presents a challenge, adding, “You can’t just throw the battery next to the rest of the cars because it could explode.” Regulatory responsibilities and obligations also affect shipping the battery. “Your obligations are, when you ship it, it’s hazardous material—it costs a little more money to get it where it’s got to go,” he said. “You’ve got to be careful not to do it wrong.”
Corbett also stressed the importance of letting local fire departments and first responders know what you have at your facility should they have to respond to an emergency.
“But once you have established those processes, your costs are very nominal,” he added.
Onto the shredder
Once companies like Pull-A-Part have harvested the valuable parts and components for reuse and the high-value nonferrous metals for recycling, the cars are sent to an auto shredder such as the one operated by SA Recycling in Atlanta.
Bobby Triesch, vice president and regional general manager for Orange, California-based SA Recycling, said the company operates 21 auto shredders and processes about 1 million vehicles annually, roughly 300,000 of which are shredded at its Georgia-region operations and put back into the economy.
SA Recycling also receives end-of-life vehicles that were not first processed by an auto parts recycling company, Triesch said. “For whatever reason, the value of those parts is not enough to have a delta in price for them to get more money selling it to a Pull-A-Part,” he explained.
In SA Recycling’s Georgia region, Triesch said an EV has yet to come into SA Recycling’s operations, though the company has received hybrid vehicles.
“As we go forward, with the trend of having more and more electric vehicles, 10 years from now, five years from now, 20 years from now, certainly it’s going to be different,” he said. “You would expect that 20 years from now … there may be electric vehicles that for whatever reason still don’t have enough of a residual value other than to get scrapped out. … If one comes to us, we have to be prepared to be able to safely separate that battery from the rest of the metal and then shred the metal.”
Triesch said the company’s Atlanta shredder yard processed a hybrid vehicle not knowing it was a hybrid, resulting in sparking in the shredder and a very loud noise. Fortunately, a combustion event did not occur.
Considering the OEMS’ role
When asked about the automotive original equipment manufacturer’s (OEM’s) role in the process, Corbett said they don’t play a role in end-of-life currently, rather, “It’s a market-driven commodity.”
He said it would take 45 minutes to talk about the role OEMs want to play in automotive recycling as the transition to EVs occurs and the potential of extended producer responsibility, or EPR, adding that some aspects of EPR “are really not good.”
“Unfortunately, automakers don’t have a great history of designing for recycling,” Triesch said.
“The OEMs do not plan to manufacture to recycling specifications or needs or requirements or anything to make it easier, but they have always sought to maintain control over the commodities that are in the vehicle; they have always wanted to find a way to close that loop and make sure that they can maintain control of those commodities,” Corbett said. “Batteries are going to be in the same conversation. And you know, auto recyclers, scrap guys, we see the value, we see the free-market-driven recycling industry, and we don’t want to be shut out of that.”
Lin said Ascend has told battery manufacturers if they make it hard for recyclers and processors to extract the valuable materials in an EV battery, “we’re going to have to dock you that much money as we process it for you.”
Triesch said he sees more potential for automotive OEMs to design with recycling in mind given the scarcity issue for the metals and minerals used in these batteries. “There really is a good chance because it’s in their self-interest to design the power systems and batteries for being able to be as cost-effectively and efficiently recycled as possible,” he added.

Exploring remanufacturing
Corbett said Pull-A-Part treats the EV batteries it encounters as it would another car part, selling its LIBs and nickel-metal-hydride batteries to the auto repair sector.
“But lithium-ion batteries and nickel-metal-hydride batteries are unique from car parts because they have a dual function,” he added. “A lot of the batteries that get resold aren’t resold as auto parts. They’re resold as energy storage units. There’s this whole market out there for these commodities that competes with the recycling market, which is good. But as we focus all of our energy infrastructure on lithium-ion batteries, well, demand is going to do what demand is going to do, and we’re going to have multiple competing partners for these commodities.”
Lin noted that hybrid EV battery cells are of a lower voltage and less volatile than LIB packs, which makes them easier to refurbish and replace in a battery pack. Today’s LIB packs typically are welded together, while older packs are more modular in design. That modularity means if a pack is recovered from a vehicle, good battery modules could be harvested for reuse elsewhere, he said.
With the value contained in a LIB, Lin said battery OEMs, automotive OEMs and others are converging in the recycling space to determine how to control the value of these metals given the forecasted supply chain crunch around lithium, nickel and cobalt and securing that supply for future manufacturing.
“This whole idea of remanufacturing is a very elegant and excellent idea,” he continued. “It’s all going to come down to the execution of that idea. Yes, there’s more value in a working battery than there is in shredding it to black mass and extracting elements. … But what about that refurbished battery? Where does it go? Is it being used within originally designed parameters? Was it assembled properly? Are there any issues with the way you’re busing the different cells and modules together? We all know that lithium-ion batteries can be volatile and hazardous. … There are a lot of ways they can go wrong. I think reman is interesting. I think if we don’t do it right, there’s going to be problems either from a safety perspective [or] performance perspective, which will likely cause challenges for the players in that market. And then market application will rapidly degrade to third-world countries … and then we go back to supply chain issues. We’re going to see leakage of things like lithium, nickel cobalt that you want to have in this economy.”
He added that battery manufacturers need to design their batteries with reuse in mind from the start to facilitate this process, noting, “If it’s done deliberately, intentionally, again, from the get-go … then you can say that it could be viable, and you might be able to take those battery packs, all strung together, let’s say and then put them in the Georgia power grid.”
A shifting landscape
EV battery remanufacturing offers the best profit margins today, Corbett said, “But the deficit figures for lithium over the next 10 years, and then again over the next 20 and 30 years, are incredible. So, the only way to make that deficit up is through Ascend Elements and those like it feeding that feedstock back into the manufacturing chain. And so that demand is going to shift that value structure in a way that tilted toward recycling.”
While EVs will have fewer of the traditional parts and components that auto recyclers like Pull-A-Part harvest and resell, Corbett said there’s still a lot of other “good stuff” that can be recovered and sold.
“Smart guys are going to figure out how to work on their own cars,” he added. “Even though it doesn’t have an engine and a radiator and a four-barrel carburetor, it’s going to have whatever kind of switches and buttons that Tesla or whatever other EV has, and folks can figure out how to buy those parts and pieces and reuse them in the cars that they repair.”

Explore the September 2023 Issue
Check out more from this issue and find your next story to read.
Latest from Recycling Today
- Greenville, Mississippi, launches aluminum can recycling program
- Cotton Lives On kicks off 2025 recycling activities
- Georgia-Pacific names president of corrugated business
- Sev.en Global Investments completes acquisitions of Celsa Steel UK, Celsa Nordic
- Wisconsin Aluminum Foundry is a finalist for US manufacturing leadership award
- MetalX announces leadership appointments
- Sofidel agrees to purchase Royal Paper assets
- US Plastics Pact report charts expansion path for recycled content in packaging