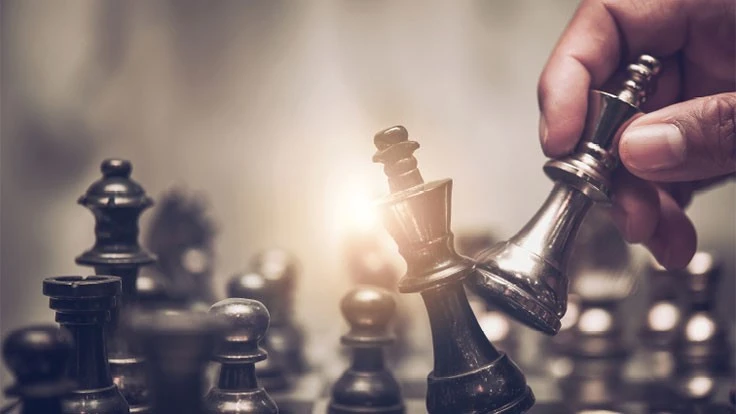

During the previous two decades, China emerged and then solidified its role as the leading producer and consumer of nearly every basic material, including base metals, plastic and paper and board.
The global shift in resources also entailed China becoming a magnet for secondary raw materials, including millions of tons annually of paper, metal and plastic scrap imported from other nations.
In the closing years of this decade, however, several factors seem to be combining to slow down and reverse this pattern, which has largely dictated how recyclers in North America conduct business.
Decisions made in Beijing, Washington, other world capitals, state capitals and in corporate board rooms around the world are contributing to a series of moves and countermoves reminiscent of a chess game—each move of a piece can dictate where tons of scrap paper are shipped and consumed.
No longer welcome here
In financial and political press coverage, President Donald J. Trump’s willingness to impose tariffs on materials and goods from overseas—and the responses of other nations—have been of keen interest to some of America’s largest business sectors.
Several months before the Trump trade wars started, however, the business model of recyclers was met with a severe shock when China’s government quickly enacted restrictions and outright bans on a long list of scrap materials.
Recyclers of plastic were immediately hit in the broadest manner. However, the Chinese government’s swift targeting of the mixed paper grade also caused severe headaches in the North American recovered fiber market.
As China essentially closed its ports to the grade, material recovery facilities (MRFs) in the U.S. and Canada were soon producing stockpiles of baled mixed paper with nowhere to go. Soon after, the value of mixed paper plunged to zero.
Statements by the Chinese government, in particular its Ministry of Ecology and the Environment (MEE) and the General Administration of Customs in China (GACC), and coverage in China’s largely state-dominated media, have portrayed mixed paper (and plastic scrap) as “foreign garbage.” Stated and implied in the media coverage is that China has been a dumping ground for the world’s trash.
This characterization of the scrap trade focuses on the single-digit residuals percentage of a mixed paper load while ignoring the 95 percent or more of the material that is a vital raw material at paper mills.
The medium-to-long-term future of tariffs and trade disputes can be difficult to discern, especially from the U.S. perspective, where lobbying and electoral politics can create quick policy reversals. The tariffs have caused supply chain disruptions, but many decision-makers are essentially waiting it out.
Chinese government policy is far from transparent, but it has become easier to trace to just one person: President Xi Jinping, who has accumulated government and Chinese Communist Party titles as he has consolidated his power since 2012.
Xi’s antipathy toward imported scrap materials reportedly is connected to his viewing of a 2016 documentary film titled “Plastic China,” which portrays worker exploitation and environmentally unsound practices connected with sorting and reprocessing imported plastic scrap. The film was essentially designed to evoke “China as a dumping ground” feelings.
Other statements from Chinese government agencies, however, have pointed to boosting China’s internal recycling programs and goals as a reason to restrict scrap imports, lending more of a trade protectionist angle to the policy.
Entering the fourth quarter of 2018, few signals have emerged that the Chinese government is having second thoughts about its scrap restrictions and bans. The potential permanence of this policy has caused reevaluations throughout the global paper manufacturing and recycling supply chain.

Supply line shuffle
An immediate effect of China’s spurning of mixed paper was an oversupply of the grade at North American MRFs. Mixed paper has been almost exclusively an export grade, with the vast majority of that export market in China.
As the stockpiles accumulated, MRF operators looked for buyers, and many papermakers in India sensed an opportunity.
Naynesh Pasari of New Delhi-based Shree Krishna Paper Mills says his company is one of many in 2018 that has increased its buying of American-produced mixed paper. Pasari spent some time in early 2018 visiting plants operated by one of America’s largest MRF operators, and he ultimately signed a contract to buy a guaranteed amount of mixed paper going forward several months.
Pasari says Indian government statistics show Shree Krishna was not alone in its actions. In the first three months of 2018, he says, Indian mill buyers brought in about 475,000 metric tons (about 496,040 tons) of mixed paper. “Since the ban [in China], mixed paper imports in India have been up by at least 50 percent monthly,” he says.
Although American recyclers welcome the opening of this spigot, India’s total consumption of recovered fiber does not come close to equaling the volumes Chinese mills have imported annually since the start of this century.
The sheer tonnage of mixed paper produced at MRFs seems likely to require either an adjustment in how scrap paper is collected in the U.S. or investments by mill companies to enable its consumption closer to home. From mid- to late 2018, many such investments have been announced.
Georgia-based containerboard producer Pratt Industries, a subsidiary of Australia’s Visy Industries, has been a U.S. leader in consuming mixed paper. In the second half of this decade, Pratt has expanded its ability to do so by opening a new mill in Indiana in 2015 and building another one slated to open in 2019 in Ohio. Those two mills combined can produce nearly 900,000 tons annually of containerboard.
Atlanta-based Georgia-Pacific, a subsidiary of Wichita, Kansas-based Koch Industries, has been piloting a system it calls “Juno Technology” to be able to use mixed paper as feedstock at its mill in Toledo, Oregon. Should the system prove capable, the firm may be able to consume some 100,000 tons per year of mixed paper at the mill starting in 2020.
The news is welcome by Pacific Coast region recyclers, where state governments have reportedly met to discuss their options for consuming scrap paper and plastic that formerly headed to China.
Another mixed paper destination in the making is a mill operated by Mexico’s Copamex. In early August, the firm announced it was converting its paper machine in Anáhuac, Mexico, from producing printing and writing paper to containerboard. The stock prep system to be installed, made by German company Voith, will allow the facility to use mixed paper (along with old corrugated containers, or OCC) to feed the 260,000-tons-per-year machine.
Hong Kong-based Nine Dragons Paper Co. Ltd., which has most of its mill capacity in China, also has made 2018 investments in paper and pulp capacity in the U.S. In May 2018, Nine Dragons purchased mills in Maine and Wisconsin from Canada-based Catalyst Paper. The two mills have a combined annual capacity of about 1 million tons of pulp or paper.
Three months later, Nine Dragons announced its U.S.-based subsidiary, ND Paper LLC, which now owns the former Catalyst mills, purchased a 220,000-tons-per-year pulp mill from Canada-based Resolute Forest Products Inc. Ken Liu, CEO of ND Paper, says the company intends to make investments in the mill that will “expand its current capabilities and inject growth into the West Virginia economy, particularly in the surrounding community.”
During the same week Nine Dragons added a West Virginia mill to its portfolio, a U.S. subsidiary established by China-based Shanying Paper purchased an idled paper mill in Kentucky. That mill, formerly owned by Ohio-based Verso Corp., will have about $150 million invested into it so that it will be capable of producing pulp and kraft packaging paper.
Verso Corp. is investing in new capacity, with the longtime printing and writing paper producer having invested about $19 million to convert a paper machine in Maine to be able to produce about 200,000 tons per year of linerboard.

Time to come home?
To what extent the series of mill and mill technology investments in 2018 will continue in 2019 and beyond will likely help determine the future of the mixed paper grade. The causes and the effects of these investments could tie into a much broader trend, though.
Among the factors that caused Trump to separate himself from other Republican presidential candidates in 2016 was his willingness to question the global trade regimen and its effects on the American manufacturing sector.
In relation to China, the North American Free Trade Agreement (NAFTA) and beyond, the Trump administration has been eager to demand changes in how U.S. trade arrangements are structured.
The president has said consistently his goal is to increase industrial output in the U.S., whether that involves steel and aluminum, automobiles and their components or, most recently, urging Apple to reconsider China as its manufacturing hub.
Reversing the decades-long trend of Fortune 1000 companies to seek out the lowest offshore labor and manufacturing costs would have seemed inconceivable just three years ago. However, a number of circumstances could yet lead to some rethinking of the global geography of manufacturing.
Wider factors causing some companies to reconsider their strategies with China include cyber security and access to global websites; intellectual property protection; and increasingly unpredictable (and often swiftly enacted) regulations introduced by the Chinese government. China’s trade policies also play a role, and nowhere more so than in the secondary raw materials sector.
The scrap restrictions chaos has caused initial investments in pulp and papermaking capacity in the U.S., but a wider shift in manufacturing activity away from China would cause greater shifts yet in the containerboard sector.
As parts of America’s manufacturing sector have fled to Mexico, China and other nations, America’s containerboard industry has lost out on producing the boxes that used to hold large and small appliances, clothing, shoes and enormous quantities of other items no longer made in the U.S.
One result has been that even in a stable and growing economy this decade, containerboard producers have chosen to run their plants at an industrywide 97 percent capacity rate while remaining unconvinced to invest significantly in new capacity.
Signs, however, point to increased confidence by papermakers to invest in North America. In addition to the investments by Chinese companies and the front-end mill changes to accept mixed paper at new mills, 2018 also has witnessed investments in paper machine conversion projects and one new containerboard mill.
Wisconsin-based Green Bay Packaging announced in June that it planned to move from a 71-year-old papermaking site and invest $500 million at a new, nearby location that will house a 100-percent-recycled-content containerboard production facility. The front end of the new paper machine, supplied by Voith, will allow it to accept OCC and mixed paper as feedstock.
Economists are largely skeptical as to what extent the globalization genie can be put back into the bottle. However, it is fair to ask how many economists forecast in 1975 that just 30 years later, nearly all the toys, shoes, small appliances, televisions and clothes Americans purchased would be made in China.
It is unclear how or whether various seemingly unrelated factors—including political populism; national security; circular economy, plastics in the ocean and sustainability issues; and automation that minimizes the impact of labor costs—could shift the geography of manufacturing just as dramatically. Clearly, though, paper recyclers and the mills they feed have direct stakes in the outcome.
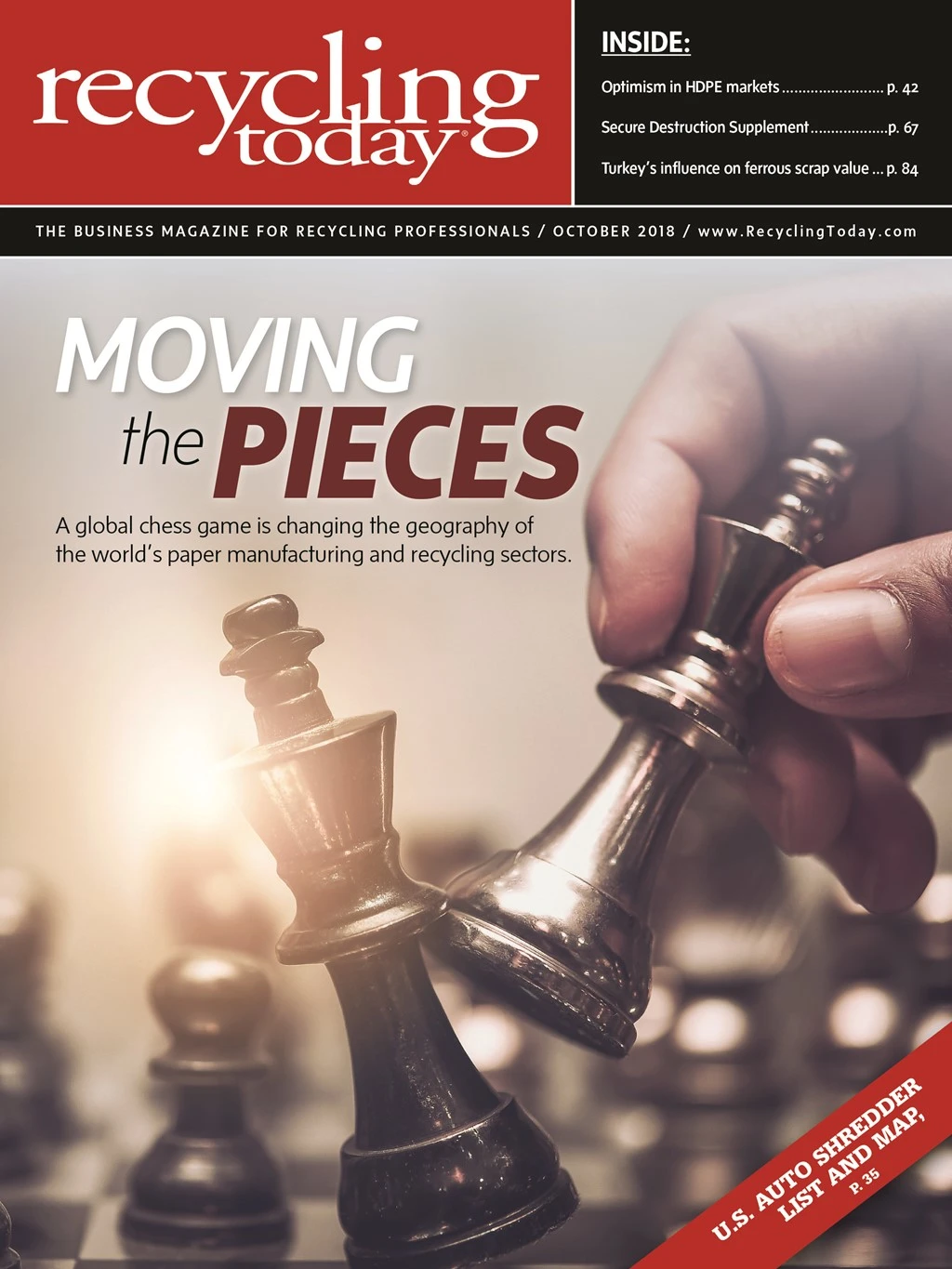
Explore the October 2018 Issue
Check out more from this issue and find your next story to read.
Latest from Recycling Today
- Aqua Metals secures $1.5M loan, reports operational strides
- AF&PA urges veto of NY bill
- Aluminum Association includes recycling among 2025 policy priorities
- AISI applauds waterways spending bill
- Lux Research questions hydrogen’s transportation role
- Sonoco selling thermoformed, flexible packaging business to Toppan for $1.8B
- ReMA offers Superfund informational reports
- Hyster-Yale commits to US production