
If you don’t know how neodymium, dysprosium
Pretty soon, each of these minor metals could affect your recycling operations, especially if you deal with electronics.
These metals with the tongue-twisting names are rare-earth elements. And they might be worth a lot of money to recyclers who recover them.
_fmt.png)
The price of neodymium has fluctuated on world markets largely because of changes in Chinese production. In mid-2011, it sold for about $500 per kilogram; but, by the end of that year, the price had fallen to less than $350 per kilogram, or 35 cents per gram ($9.92 per ounce). Pricing has continued to slide, fetching less than 4 cents per gram ($1.13 per ounce) as of late November 2017.
China plays a huge role in rare-earth elements—one that is forcing users of these metals to look for recycled sources. For instance, China produces more than 90 percent of the world’s neodymium.
High-tech companies’ interest in finding secondary sources of neodymium indicates it is worth a recycler’s time to consider whether to get involved in recovering rare-earth elements.
Hidden potential
Rare-earth metals are found in
Preston Bryant, CEO of Momentum Technologies, Dallas, definitely says it is. “This is a new way to think about recovering electronics,” he says.
His company, working together with the Materials Science and Technology Division of the Oak Ridge National Laboratory (ORNL) in Tennessee, developed a way to recover 97 percent of the rare-earth materials from the magnets found in hard drives and
After electronics recyclers remove the precious metals and plastics from the material stream, these companies then can turn to Momentum Technologies or a similar outfit to recover rare-earth metals.
Demand for these materials is huge. The electric motor in a Toyota Prius uses about 1 kilogram of neodymium in its permanent magnets. The Massachusetts Institute of Technology (MIT) says a wind turbine rated at 3.5 megawatts of electricity contains 600 kilograms, or 1,300 pounds, of rare-earth metals.
The technology developed at the Department of Energy’s (DOE’s) ORNL uses a combination of hollow fiber membranes, organic solvents
In laboratory testing, the membrane extraction system demonstrated the potential to recover more than 90 percent of these three elements in a highly pure form from scrap neodymium-based magnets. Bryant puts the figure closer to 97 percent. The resulting product is a 99.6 percent pure combination of rare-earth materials, he adds.
Keep in mind that the typical magnet—just the magnet—in a hard drive consists of 30 percent to 33 percent rare-earth elements, Momentum Technologies says. As mentioned previously, manufacturers of
Although iron and boron must be removed from the rare-earth elements during recovery, most end users are satisfied with a rare-earth metal product that includes a mixture of neodymium, dysprosium
“We are providing raw material that can be used across the board,” Bryant says.
Currently, 35 percent of used hard drives are shredded in the United States because of data security concerns, according to the DOE. Recycling those drives could result in recovery of about 1,000 metric tons of magnet material per year, according to Timothy McIntyre, project lead and program manager in ORNL’s Electrical and Electronics Systems Research Division.
Exceeding limitations
Membrane extraction is an efficient process compared with mining. To reclaim 1 kilogram of rare-earth metals requires about 3 kilograms of magnets. “You are getting high density,” Bryant says. “You don’t have to deal with a huge amount of material as you do with mining.”
He is referring to the earth-moving sort of mining. Urban Mining, Jacksonville, Florida, does a different kind of mining. The company provides secure destruction of electronic media and recovery of recyclables. Urban Mining also has rare-earth metals in its sights.
“We believe it is economically viable and environmentally sustainable,” Steven Kaufman, CEO of Urban Mining, says of recovering these materials for recycling.
_fmt.png)
The company is working on establishing a public-private partnership with the University of Florida to research recovery technology Urban Mining has developed.
Urban Mining focuses on electronic refurbishing and recycling. Kaufman confirms the company has funded the research and is hopeful for a positive outcome. He says he expects that, once the technology is commercialized, it will become part of Urban Mining’s offering and may be licensed to other companies down the road.
Recycling critical materials from electronic scrap has been limited by processing technologies that are inefficient, costly and environmentally hazardous, says ORNL’s Ramesh Bhave, who led the membrane solvent extraction research and development. He says the team’s new simplified process eliminates many of these barriers.
“Our single-step process to recover rare-earth elements from scrap magnets is more environmentally friendly and has the potential to be a more cost-effective approach compared to conventional routes, such as precipitation,” Bhave says.
Recycling rare-earth metals
Momentum received two
The company first licensed ORNL’s membrane extraction technology, which uses a combination of hollow fiber membranes, organic solvents
The second license is for ORNL’s automated process to recover magnets from hard drives. It employs a system to sort and align hard drives on a conveyor for processing. The method uses a mapping station with barcode scanning and a coordinate measuring machine to populate a database of each make of hard drive, positioning the devices for correct robotic disassembly.
The process is designed to recover the magnets, their permalloy brackets, circuit boards, aluminum and steel, CMI says, while automatically destroying data storage media to ensure security.
_fmt.png)
The recovered magnets can be directly reused by hard drive manufacturers or in motor assemblies, used in other applications through resizing or reshaping or processed back to rare-earth metal. This recovery method also can be adapted to target other consumer goods containing rare-earth magnets, such as used electric motors, appliances and heating and air conditioning systems, ORNL says.
In a news release announcing that Momentum obtained this second license, Bryant says, “Bringing together these CMI technologies allows us to create a sustainable business model, something that many rare-earth companies struggle to achieve.”
In that same news release, CMI Director Alex King says, “Hard disk drives are the second-biggest use of neodymium magnets, and they are the most readily available source for recycling.”
Hurdles yet to overcome
Magnets use a considerable amount of rare-earth elements. In August 2016, CMI created a table of more than 460 U.S. patents, available at http://cmi.ameslab.gov/sites/default/files/rare-earth-magnet- patents-august-29-2016.pdf, that address rare-earth magnet compositions.
Rare-earth metals are among the most difficult elements to process and the hardest to do without, CMI researchers say. They rank at the top of all lists of critical materials today, and the difficulty of working with them, or working around them, contributes significantly to this. CMI says it is addressing three major technical challenges associated with rare-earth metals recycling: recovery, separation of one rare-earth metal from another and converting the ore to metal.
From a recycler’s point of view, the biggest hurdle to recovery is purification. But technology companies are happy to get blended materials, as long as that blend meets their manufacturing requirements.
Bryant says Momentum Technologies has processed these materials at scale, sending the resulting product to 10 manufacturers for evaluation. “They said our product is something they can use,” he says.
The company was relieved to find that manufacturers are willing to take a combination of all three rare
Developing new chemical separation methods that offer high efficiency, low cost and low environmental impact will allow the materials to be processed more widely.
Nobody sees demand for rare
“Those that are aware of the issue recognize that it is an issue and that it will grow over time,” Kaufman states.
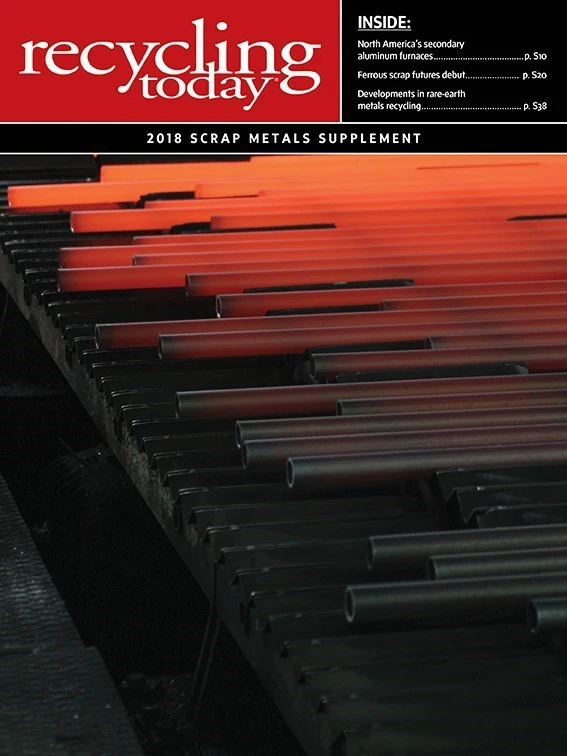
Explore the January 2018 Scrap Metals Supplement Issue
Check out more from this issue and find your next story to read.
Latest from Recycling Today
- South Carolina launches recycling app
- Resource Recycling Systems transitions to employee ownership model, refreshes branding
- APR upgrades PCR certification program
- WM completes $40M automation project at Philadelphia MRF
- Speira commissions new furnace in Germany
- ABB report portrays paper sector circularity, emissions reduction
- RMDAS and Davis Index numbers portray stalled ferrous market
- Attero adds NGO veteran to its board