The 1970s television show “The $6 Million Man” speculated on how that amount might be invested in technology to “to build the world’s first bionic man . . . better than he was before. Better, stronger, faster.”
In 2009, Cincinnati-based Rumpke Recycling invested $6 million to retrofit its Cincinnati materials recovery facility (MRF) to achieve essentially many of the same goals—to make it better, stronger and faster than it was before.
Rumpke, a regional solid waste and recycling company that operates five MRFs in Ohio and one in Kentucky, had been seeing the volume of material flowing into its Cincinnati MRF increase steadily. Upgrading the MRF became even more critical when Rumpke anticipated that communities in Ohio were preparing for a state-mandated municipal solid waste landfill diversion target of 50 percent.
A SOLID VETERAN
The Rumpke Recycling Cincinnati MRF is located in a century-old industrial building the company converted into a MRF in 1991.
According to Rumpke’s Director of Recycling Steve Sargent, the MRF’s first retrofit occurred in 2002, when it was converted from a dual-stream plant to a single-stream facility. The plant’s single-stream capacity from 2002 to 2009 was 14 to 15 tons per hour, says Sargent.
“We were at maximum capacity at the plant, and we were getting more demand for recycling services from our customers,” says Rumpke Corporate Communication Coordinator Molly Yeager about the situation in 2009. Sargent and Yeager say more material was coming in from communities and counties that were reacting to the state of Ohio’s 50 percent diversion mandate as well as from Rumpke Recycling’s growing presence in the collection of commercial single-stream materials.
“In Ohio, we not only service urban contracts, such as the Cincinnati curbside contract, but also rural counties that also have the mandate to reach a 50 percent diversion rate,” says Sargent. “Many of these districts are consulting with us on how to increase the recycling rate. In some cases, single-stream is the key, while in rural areas drop-off sites may be the way to go.”
The retrofitted MRF also is seeing material collected from office buildings and other commercial sites. “There is new interest in commercial single-stream collection at small offices,” says Sargent. “Generally, it’s a very clean stream with a very limited amount of glass. The challenge from this portion is you get a lot of shredded paper, which can be a challenge for a single-stream system.”
MUCH TO SEPARATE
To retrofit the MRF so it could handle its increased volume and wide range of materials, Sargent and others at Rumpke began to “travel the country and inspect several systems” as it set about to make important purchasing decisions.
Although part of the investment was going to be in sorting technology, the volume growth at the MRF also entailed installing a new concrete tipping floor, a new compressor room, new duct work and new air filtration systems.
Rumpke Recycling also designed the MRF as a site to host public tours by installing a mezzanine walkway.
The investment in increased capacity has been designed to allow the MRF to sort and process up to 28 tons per hour. According to Sargent, the MRF has already operated at the new target level (in the 26-to-28-tons-per-hour range) in its first 90 days after the retrofit. “Naturally, that $6 million investment begins to look better when you can run more volume,” he comments.
On the technology side, mechanical sorting equipment used in the Cincinnati MRF includes a drum feeder at the start of the process, followed by conveyors that pass in front of manual sorters who pull out contaminants.
Disc screens and multiple screening decks are next, as they perform fiber/container/broken glass separation and then fiber separation by grades. An angle screen directs smaller paper away from the container stream.
Magnets and eddy current separators perform their sorting roles for the metal container stream.
A key technology investment in the 2009 retrofit has been the installation of three TiTech optical sorting scanners.
The optical units have been deployed to identify and separate the plastic container stream—a set of tasks that in the 14-tons-per-hour setup had been performed by manual sorters.
One function of the TiTechs has been to separate clear or natural No. 2 HDPE (high-density polyethylene) containers from white or colored ones, as those materials go to different end markets.
It’s just one of several sorting tasks confronting Rumpke as it takes on a diverse stream of plastic containers. (The Cincinnati MRF even accepts No. 3 through No. 7 plastic bottles and jugs.)
The TiTEch optical units were supplied by Van Dyk Baler Corp., Stamford, Conn. The company’s Scott Jable, who works from a regional office near Chicago, says one advantage the optical units have is identifying the targeted material no matter its shape and size.
While a manual sorter may be looking for a rounded milk jug, “the optical units don’t care about the shape or size—they’ll identify it anyway,” says Jable. “Not all the containers that show up on the tip floor are whole, round bottles. An optical unit can find that flattened bottle or can.”
GLASS HALF FULL |
In some recycling programs and in many material recovery facilities (MRFs), glass is considered a problematic material. Recyclers in geographic areas without a nearby consumer of the material may quickly conclude that the problems of broken glass contaminating other materials and “sand-blasting” screening equipment may outweigh the end-market potential. Cincinnati-based Rumpke Recycling is in a better position relative to glass recycling, according to Rumpke Director of Recycling Steve Sargent. Glass separated at the company’s Cincinnati and Dayton, Ohio, MRFs is combined at a Dayton facility that cleans and upgrades the material to prepare it as a feedstock for fiberglass insulation. The cleaned, recycled glass is shipped to the Johns Manville fiberglass insulation factory in Defiance, Ohio. The process is documented in a video clip on the Rumpke Recycling Web site at www.RumpkeRecycling.com/glassrecyclingvid.html. |
KEEPING UP WITH CHANGES
The use of the optical sorters was just one of several considerations in a retrofit as major as the one at the Cincinnati plant, say Sargent, Yeager and Jable.
“A process like this doesn’t happen overnight; you do a process flow and consider each component,” says Jable. That process, he notes, allows a recycler to buy larger capacity screens at the front end of the plant and smaller ones toward the back end as material streams are split into fractions.
The MRF in Cincinnati also has been configured to consider wider trends in materials entering the plant—such as less of the old newspapers (ONP) grade and more of the old corrugated containers (OCC) grade.
“The fiber stream is absolutely changing,” says Sargent. “There is less ONP and more mixed paper. And with a combination of our commercial single-stream programs and more people working from home and receiving UPS shipments, the plant had to be designed to incorporate a larger amount of OCC at the front of the system.”
Sargent says the retrofit has produced good early results. “We’ve been pleased with the initial success of the TiTech units,” he comments. “As markets continue to change, the technology in areas like optical sorting is evolving almost daily to adapt.”
Although it just doubled in capacity, Sargent says the Cincinnati retrofit was nonetheless “designed for future expansion” when needed. He remarks, “We’re still making changes to the plant, but so far, so good.”
The author is editor-in-chief of Recycling Today and can be contacted at btaylor@gie.net.
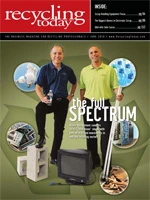
Explore the June 2010 Issue
Check out more from this issue and find your next story to read.
Latest from Recycling Today
- IDTechEx sees electric-powered construction equipment growth
- Global steel output recedes in November
- Fitch Ratings sees reasons for steel optimism in 2025
- P+PB adds new board members
- BlueScope, BHP & Rio Tinto select site for electric smelting furnace pilot plant
- Magnomer joins Canada Plastics Pact
- Out of touch with reality
- Electra names new CFO