Knowing the chemistry of a heat is vitally important to a steel mill, particularly to flat roll mills. If scrap processors could provide material of a known chemistry to these mills—not just material that meets a particular physical description—they would save the mills time and money. In turn, the steel mills would be willing to pay a premium for scrap material of a known chemistry.
Process control instrumentation can help recyclers deliver such a product to their flat roll mill customers. The CrossBelt Recycled Metal Analyzer from Thermo Gamm-Metrics, which is distributed by Gamma-Tech LLC of Cincinnati, is one such instrument. The analyzer uses prompt gamma neutron activation analysis (PGNAA) technology to perform a real-time, composite analysis on shredded scrap metal.
Currently, only two companies use these units to determine the chemical composition of their shredded ferrous products, which they market to steel mills as Gamma Shred: River Metals Recycling, headquartered in Fort Mitchell, Ky., and Morris Recycling Inc. (MRI), New Albany, Miss.
GETTING INLINE. "We installed the first analyzer in the country—in the world—in late 2001 and made our first shipment to the marketplace in November of 2002," Alan Crouch, president of River Metals Recycling (RMR), says. RMR is a wholly owned venture of Cincinnati-based The David J. Joseph Co.
Crouch says it took RMR roughly a year of testing raw material, doing dead heats at steel mills to verify the process.
RMR has since added a CrossBelt analyzer to its Louisville location in 2004 and is in the process of adding a unit to its Henderson, Ky., facility. Crouch says the company was able to produce marketable material from its Louisville installation almost immediately. "We did all the development work with our first installation," he says.
River Metals and MRI have installed their process control equipment on the downstream side of their shredders at the exit conveyor.
"We put it in after the stacking conveyor," Crouch says. "It has to be an inline process."
MRI installed its analyzer in December of 2003 on one of its four stacking conveyors. "The first two conveyors are shakers, the first of which has a surge hopper on it where we load shredder material into the system with a bucket loader, crane or our radial stacker from the shredder," Jed Morris of MRI says. "The third conveyor is the one that the analyzer is mounted around and is designed to speed up and slow down based on the burden of material delivered to it. The last conveyor is a radial stacker, which we use to either load trucks or stack material for future loading."
Crouch says that such an analyzer can easily be added to an existing plant. "It doesn’t require major changes to a facility, depending on the layout," he adds.
MAKING THE GRADE. The analyzer helps RMR and Morris Recycling to understand the chemical makeup of their scrap metal, but Crouch is careful to point out that it is River Metals’ staff that is actually creating the product. It’s up to the RMR staff to add the metal units necessary to create the desired composition, he says. The analyzer just confirms the chemical composition of the final product.
"Without the bulk analyzer," he says, "there is no way to tell what the copper level is. You can try to keep it to a minimum, but you cannot predict what the final chemistry will be."
Volume Analysis |
Austin AI of Austin, Texas, manufactures a bulk analyzer and sorter that uses QXR technology, a combination of optical and energy dispersive x-ray fluorescence (EDXRF) discriminators, or a circuit that can be adjusted to accept or reject signals of different characteristics. The unit can be mounted above the conveyor downstream from the shredder. QXR technology can be used to sort and separate metal from non-metal while also separating alloys according to general classification, such as steel, zinc and red metals. According to Austin AI, its continuous online system can classify up to 15 different material types and synchronize with various diverting mechanisms, such as air jets. "The QXR is an up-and-coming system/technology with speed and accuracy unmatched by current market offerings," Dianne Hillhouse, MarComm manager for Austin AI, says. "We actually have several purchase orders and are in the process of building/installing several of the QXR systems." Austin AI says its QXR technology is capable of sorting material at rates ranging from one to 10 tons per hour, depending on the material type and separation requirements. The company says its QXR can identify pieces in as few as 100 milliseconds with belt speeds up to 300 to 400 feet per minute. |
Ben Morris, president of MRI, says this type of process control equipment helps MRI "to effectively control the product quality and truly manufacture material specific to the needs of our consumers."
For MRI, that means creating a shredded ferrous product with a 0.12 or 0.15 copper content.
The addition of this kind of process control equipment has not slowed down operations at RMR. "The processing rate for the machine ranges up to 200 or 300 tons per hour," Crouch says. "It will not impede the production of your shredder."
Jed says MRI typically runs between 200 and 250 tons per hour of shredded material.
River Metals is currently testing for copper, manganese, nickel, chrome and zinc, all of which, Crouch says, have a meaning to steel mills. "The essential level is the copper level. It’s a tramp metal," he says. "Once it is in the steel mill’s mix, there is no way to get it out."
Crouch says that excessive copper can cause the steel produced by flat roll mills to crack.
MRI is also concerned primarily with copper. "Other elements are of concern, but typically do not give us trouble with the standard shredder feedstock that we run," Jed says.
When a steel mill knows the chemistry of its incoming scrap metal, it can vary the scrap material that it puts into a charge to produce a mixture that will hit its preferred chemical ranges.
Ben and Crouch say flat roll mills are willing to pay a premium for their material in light of its known chemistry.
RMR and MRI benefit from process control equipment in other ways, as well.
SEEING RETURNS.RMR is also capable of moving its Gamma Shred regardless of market conditions, Crouch says, thanks largely to the company’s ability to guarantee a particular chemistry. "It gives us a name in the industry and helps us to market our other products because of the reputation that we produce a quality product. People aren’t suspect of what they are going to get."
Ben says MRI has also reaped intangible benefits from being able to control the chemical composition of its shredded ferrous scrap.
"We are building better relationships with out customers because we are trying to help them build the quality of their infeed," he says.
"If our customer is successful, it’s good for us," Ben adds. "It doesn’t work to get paid more if you are not giving [the customer] value in return."
While RMR has seen the benefits of adding process control equipment to its shredding plants, Crouch says the technology is not for every scrap processor.
"It’s a niche process," he says. "Normal bar mills don’t see the advantage."
OFFERING ADVICE. Crouch says prior to installing process control equipment like a bulk analyzer, scrap processors must understand their customer base and where they would move the resulting product. "For us, it was a no brainer to put the unit in," he says, citing the number of mill customers located along the river system.
Ben says scrap processors considering the addition of process control equipment should be willing to change some internal processes to aid quality control.
Crouch says, "We are very proud of what we do. And even though the ultimate user is going to be our competitors, I believe it is the direction all scrap companies have to move in." He adds that such a move on the part of scrap metal processors will help U.S. steel mills to succeed in the long run, helping to ensure the strength of the scrap processing industry, as well.
The author is managing editor of Recycling Today and can be contacted at dtoto@gie.net.
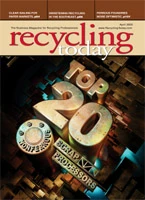
Explore the April 2005 Issue
Check out more from this issue and find your next story to read.
Latest from Recycling Today
- Fitch Ratings sees reasons for steel optimism in 2025
- P+PB adds new board members
- BlueScope, BHP & Rio Tinto select site for electric smelting furnace pilot plant
- Magnomer joins Canada Plastics Pact
- Out of touch with reality
- Electra names new CFO
- WM of Pennsylvania awarded RNG vehicle funding
- Nucor receives West Virginia funding assist