Today Waste Management handles more than 7.5 million tons of material through our MRFs (material recovery facilities) and through our brokerage business. We have more than 30 single-stream facilities. We have more than 100 recycling facilities throughout North America, and we continue to make significant investments in the development of these endeavors. We have two large facilities under construction today.
Twenty years ago, recyclables often were collected in multi-compartment trucks and possibly in two-compartment trucks. Newsprint was newsprint. And we did a little QC (quality control) on it and we were good. I should point out that the single-serve plastic bottle didn’t exist at that time. We could actually use a trommel to separate aluminum cans from plastic. Life was simple.
If we roll the clock forward, you can see what things look like today and the diversity of material collected. Municipalities require us to collect these materials in our inbound streams today. And when you look at the ability to try to get these separated into all their different components, it’s a daunting task to say the least.
RESPONDING TO CHANGE
We try to look at where things are going, where we expect them to be. How [do] we react to that and how do we try to get ahead of that?
Clearly, newspaper readership is declining. The newspapers are also thinner and smaller than they were 10 to 20 years ago. We see e-commerce is increasing. That means our residential mix has much greater levels of corrugated cardboard. Glass packaging is going down and being replaced in many cases with plastic packaging. The many forms of plastic packaging today present their own challenges.
You also have to look at all the things that are happening with packaging size and weight, because everything we collect today is different than it was yesterday. It doesn’t matter what we are talking about, whether it’s corrugated cardboard [or] plastics. PET bottles today weigh about two-thirds what they did five years ago. Newsprint is 55 percent of the material stream today.
COLLECTION COMPLICATIONS
Collection trends have changed significantly. A lot of this is driven by the idea that people want to divert more materials from the waste stream. The ability to collect things separately becomes hampered, but people also are asking, “How do you lower costs?” A lot of costs are being lowered by people going to carts, people going to every-other-week collection, and the result of that is that you now have materials that are never looked at when they are put in the truck.
There’s good and bad that comes with these things. We get a lot more materials, but it also means that it is much more difficult to control the inbound quality.
We’ve got all kinds of ways now that we collect materials. We have mail-back programs. We have kiosks that allow for home collection of plastic bottles and aluminum cans. And a lot more [collection] comes from the commercial side.
Everybody is asking us, whether it is fiber or containers or anything [recyclable], how do we get more? How do we get it cleaner? How do we get it cheaper? The materials are there to be mined. The question is, how do we do it, and how do we do it efficiently and effectively, both from a cost and from a quality standpoint?
And what is driving the trend? Obviously online communication drives people to get information in other ways than they used to. It allows people to purchase things online without heading to the store. A lot of [the drive] surrounds the green movement, diversion goals and customer demands. It really has a lot more to do with cost. When Walmart goes to Hamburger Helper and asks them to reduce the size of their packaging, it is about sustainability, but it is [also] very much about cost. They are going to meet their sustainability goals as they drive down price.
Many more materials are recovered today, but there is a decrease in quality and a tremendous difference in the composition of the materials produced today.
TWEAKING TECHNOLOGY
The capital investments that are made today are daunting, to say the least. We are putting two facilities in as we speak. The capital investment is tremendous, and it really gets down to a lot of technology but also a lot of old-fashioned sorting. We’ve got drum feeders on the front of these [systems] providing a very consistent feed rate. The equipment only performs well when it is fed at the right rate, and [a drum feeder] allows us to do that very effectively.
We use optical sorting in a number of ways, both to clean up our fiber as well as to sort containers. With the fiber, to do our final cleanups, we also put Paper Magnets in these [systems]. It is a new piece of equipment (from Lubo USA, Stamford, Conn.) that is basically a perforated belt we can suck the paper to, allowing the containers to roll off. When we look at our split, we’re able to actually push more paper toward the container side and recover it in a different way, which allows us to get cleaner fiber. And we split that material by different sizes because an optical sorter performs better with certain sizes, and a paper magnet performs better with other sizes.
We are always looking at how to change our screen designs. Our newest designs stack the screens in a different way, which we believe is going to be more effective. We also are looking at new disc technology. We are testing new discs today that we expect to cause a lot less wrapping. We get a tremendous amount of plastic bags wrapped in these screens, and their performance degrades very quickly. It also creates safety issues and labor issues in terms of trying to keep [the screens] clean. We also put our plants on very strict replacement schedules for those discs. We use a computerized maintenance management software and we have every one on hourly schedules as to when to replace impact zones and when to replace full screen decks. The maintenance of these [discs] is a huge challenge. We placed one order for $800,000 worth of discs, so the amount of money that goes into these plants is tremendous.
We have very long presort [lines]. We get tremendous amounts of rigid plastics in our mix. We get bulk metals. We get a lot of film and a lot of things that don’t belong there. We’ve also included secondary presorts, so once we get the residue out off the beginning, then we scalp off the large stuff with a corrugated screen. We get another look at [the material] and find that to be very effective. It’s also the most effective place for us to pull the brown [paper] out before it hits a bunch of screens and splits down three or four different conveyor belts. We’ve got vacuum hoods in all these [presort lines], so as the film plastic comes down, we just flip it up and it just gets all vacuumed and dumped into the same bin. And obviously there are multiple QC stations.
Today, we buy more equipment to do what other equipment doesn’t do. It’s phenomenal. It requires that we build these huge facilities that are in this hub and spoke arrangement that allow us to transfer material in to feed the beast, to try to do all these things with a balance of technology and labor.
In the ideal world, we would get much better separation. We would get smaller facilities that would be closer to the point of collection, and we would be able to recover more materials.
Municipalities ask us every day [to accept a wider range of materials for recovery]. We’ve got people asking us to put hairdryers and toasters in our single stream and [these conditions] are a requirement of the bid.
There are often a lot of barriers separating collection, the MRFs and [producing] the actual recycled paper or other commodities, and it is not limited to paper. I think if we can all work together, I think there is a tremendous opportunity for us to make a difference.
OPPORTUNITY IS KNOCKING
We’ve seen improved diversion in certain commodities. Paper continues to increase. Aluminum cans continue to increase. PET bottles are stagnant. Everybody is going about his or her own way of investing dollars to capture his or her own little piece of the pie, and if we could work together somehow and get the industry groups to collaborate as one to educate the consumer and actually make a difference on the quality of what we get in, that’s a huge difference.
A bale of newsprint today isn’t newsprint. I would say that I am not sure that No. 8 news ever existed. It’s one-quarter or 1 percent out-throws and 0 percent prohibitives. Even in the good ol’ days, that didn’t’ exist. What it is today, though, is office paper, magazines—anything bleachable. It becomes almost the acceptable grade, if you will, today.
We need something different in the future in terms of technology to recover these grades so we can use sorted white ledger for tissue or turn newsprint back into newsprint. If we can all work together and put our heads together, there’s an opportunity here. We’ve got some problems and we all need to work together to come up with a solution.
The author is vice president of operations support at Houston-based Waste Management. He can be contacted at kmockros@wm.com.
Editor’s Note: This is an edited transcript of a presentation given by Karl Mockros, vice president of operations support for Houston-based Waste Management, at the 2010 Paper Recycling Conference & Trade Show, held in mid-June in Chicago.
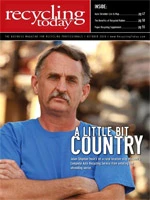
Explore the October 2010 Issue
Check out more from this issue and find your next story to read.
Latest from Recycling Today
- ReMA board to consider changes to residential dual-, single-stream MRF specifications
- Trump’s ‘liberation day’ results in retaliatory tariffs
- Commentary: Waste, CPG industries must lean into data to make sustainable packaging a reality
- DPI acquires Concept Plastics Co.
- Stadler develops second Republic Services Polymer Center
- Japanese scrap can feed its EAF sector, study finds
- IRG cancels plans for Pennsylvania PRF
- WIH Resource Group celebrates 20th anniversary