
Auto shredding plants represent a significant investment in capital equipment, so the buyers and managers of these plants greatly prefer to hear them running rather than to see a maintenance worker making an adjustment or replacing a wear part.
Maintenance work has an important “bigger picture” aspect, however, that is just as critical to the return on investment (ROI) for the shredding plant as the number of operating hours it accumulates each day.
Machinery inspection and preventive maintenance tasks can be keys to preventing the catastrophic failure of a shredding plant. These tasks also help optimize the output of the plant during its operating hours, thus tying into two critical aspects of the plant’s ROI.
Bobby Triesch, a vice president with Newell Recycling Southeast, East Point, Georgia, has been with that scrap processing firm for more than 12 years. Previously he spent five years as a vice president and shredder specialist with Metal Management Inc. (now part of Sims Metal Management). In his current role, he helps oversee the management of the five auto shredding plants operated by Newell Recycling Southeast.
In the following interview, Triesch offers his responses to questions pertaining to designing and managing a maintenance program at an auto shredding facility.
Recycling Today (RT): How many people (and with what job responsibilities) should be responsible for creating and adhering to a shredder maintenance program?
Bobby Triesch (BT): The shredder maintenance program should be created by the person in the company most knowledgeable about the shredder and its safe and productive operation and maintenance. At many companies, that would be the general manager of the shredder facility or the maintenance manager, if the facility has one. It really depends on the depth of experience and knowledge at the company.
RT: What steps can companies put in place to ensure maintenance tasks are not sacrificed either to a) production schedules in busy times or b) cost-cutting measures in slow times?
BT: Maintenance is a daily responsibility around shredders. For every hour of operations, you usually need to have a half- to three-quarters of an hour of maintenance. So if you shred eight hours, plan on at least four to six hours of maintenance.
If volumes are low, you can shred one day and then spend the next day doing maintenance.
Back when our industry was busy, and we shredded daily, we would shred 12 hours per day and perform maintenance for eight hours, so it was almost an around-the-clock operation.
RT: To what extent have automated control systems for shredders changed the way maintenance tasks are carried out?
BT: We do not use automated systems for telling us when maintenance is required, although there are some automated systems that track tons run and notify you of the threshold tons and remind you of upcoming predictive replacement and/or maintenance.
We choose to use spreadsheets to track tons produced versus the life of castings, replacement parts, fluids and filters, as well as mechanical and electrical systems, and we visually inspect our shredders and equipment on a daily basis.
Sponsored Content
Labor that Works
With 25 years of experience, Leadpoint delivers cost-effective workforce solutions tailored to your needs. We handle the recruiting, hiring, training, and onboarding to deliver stable, productive, and safety-focused teams. Our commitment to safety and quality ensures peace of mind with a reliable workforce that helps you achieve your goals.
There is no way to completely automate this process.
RT: What guidelines serve as indicators that it is time to flip or change out hammers? What about grates?
BT: Hammers last for about 5,000 to 6,000 tons of production when using a 12-hammer pattern, so hammers are flipped or moved almost on an every-other-day basis.
One has to look at the insides of the shredder daily to look for anything wrong, like cracks. These, if not caught, can cause a casting to break during production, which can cause substantial structural damage to the machine.
Grates last much longer but still need to be inspected on a daily basis. The same is true for rotors.
RT: How does a shredder maintenance plan tie in with the downstream equipment? Should there be a unified maintenance plan all the way through a system?
BT: The shredder takes big pieces and makes them small, while the downstream separates the pieces. So while you need both systems to work when you are planning operations, the downstream maintenance must be done on a daily basis to have greater uptime and less downtime.
RT: Should maintenance records be kept? What can they tell owners about the state of their equipment?
BT: It is important to keep good records. If you do not track, measure and analyze what you are doing, you will not know what you should be able to accomplish.
Get curated news on YOUR industry.
Enter your email to receive our newsletters.
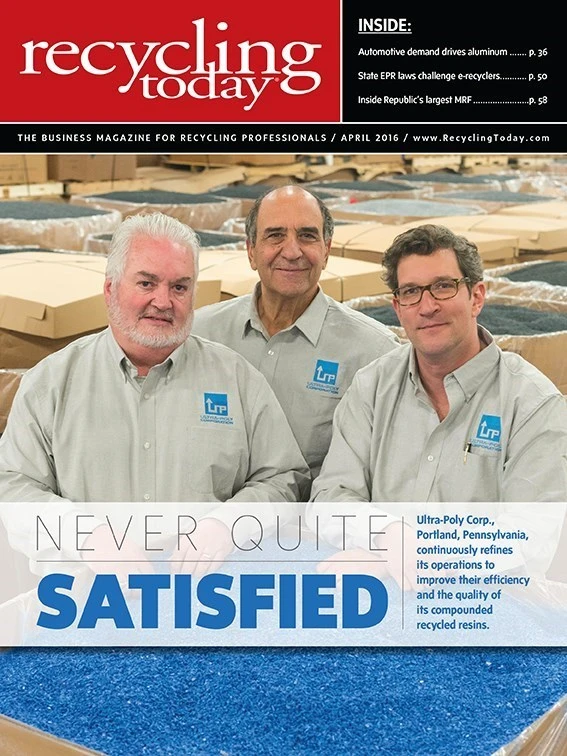
Explore the April 2016 Issue
Check out more from this issue and find your next story to read.
Latest from Recycling Today
- Returpack reports increased DRS activity in Sweden
- Trade groups align against European export restrictions
- Construction, auto sectors show mixed signals
- Politics in Turkey threaten recycled steel outlet
- Toppoint Holdings expands chassis fleet
- Lego creates miniature tire recycling market
- Lux Research webinar examines chemical recycling timetables
- Plastics producer tracks pulse of wire recycling market