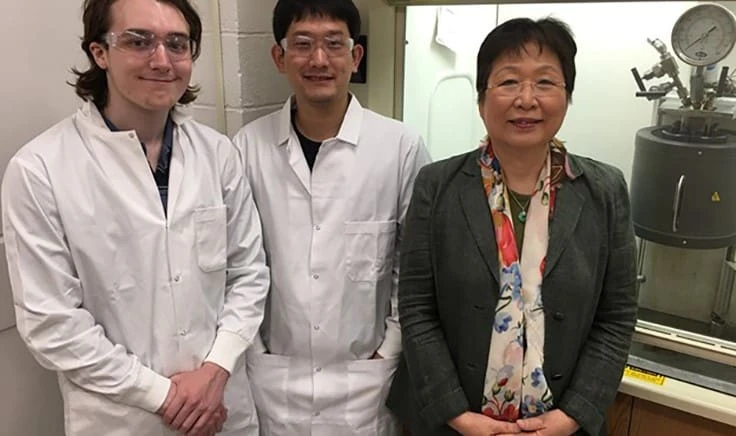
Photo courtesy Linda Wang
Single-use plastic scrap continues to be a growing problem internationally with only 9 percent of the 8.3 billion tons of plastic produced in the last 65 years being recycled. One of the biggest contributors to this issue is polyolefins, such as polypropylene and polyethylene.
Researchers at Purdue University are working to solve that problem by commercializing a new process of recycling plastics called low-pressure hydrothermal processing. Purdue University researcher and developer Linda Wang says the process is an economically and environmentally safer way to recycle polyolefin plastics than other methods, such as pyrolysis and depolymerization.
Wang says her method of recycling polyolefins can create products like gasoline, diesel fuel and other high-value items.
“Our hope is that by turning these plastics into other valuable resources, we can make recycling them into something economically valuable,” she says.
Low-pressure hydrothermal processing works by melting plastic in supercritical water using low pressure to convert plastic into naphtha. Once converted, it can be used as a feedstock for other chemicals or further separated into specialty solvents or other products. The process can recycle up to 90 percent of polyolefin plastics and takes about 45 minutes to complete, Wang says.
Because the process primarily uses water, Wang says it can cut equipment and maintenance costs while also reducing the number of resources needed to recycle the material. Right now, it is unclear how much the process will cost compared with other methods of advanced recycling like pyrolysis. Wang says the team is in the middle of bringing the process to commercial scale.
Wang says she believes the process creates a more environmentally friendly product, also. According to research done by Wang’s team, the conversion process saves 92 percent of energy compared with producing fuels from crude oil. The process also reduces greenhouse gas emissions by 71 percent compared with using crude oil in fuels.
The project is in the process of being commercialized by Hasler Ventures LLC. That company is working with American Resources Corp. to build a plant in Fishers, Indiana. Dan Hasler, the company’s president, says the small-scale plant will go live in about two years. If the project is successful, Hasler will begin to look for investors for commercialization which could take another three years.
“What caught my eye about this process is the need for it more than anything,” he says. “This is just one possible way to help solve what is a huge problem for the world as we continue to bury ourselves in plastic waste. My hope is that this provides an additional avenue that encourages people to collect plastic waste and turn it into high-value products.”
Wang is working on this project with two other researchers, Kai Jin, a graduate student, and Wan-Ting (Grace) Chen, a postdoctoral researcher at Purdue. Wang began working on this project in 2011 when someone asked her about recycling polycarbonate. After developing a method to restore certain polymers into pristine polycarbonate, Wang turned her attention to finding a way to recycling polyolefins.
“After we developed the process for polycarbonates, we realized that we were barely making a dent in the world’s growing plastics crisis,” Wang says. “It’s estimated that by 2050, there will be more plastics in the ocean than there are fish, according to the World Economic Forum. That’s why we started looking at ways to recycle polyolefins.”
While the process is still far from being available for plastic scrap recyclers, Wang says she hopes her technology will stimulate the recycling industry to reduce the rapidly rising amount of plastic scrap. She also hopes her method will raise awareness with consumers and the consequences of using single-use plastics.
Latest from Recycling Today
- Aqua Metals secures $1.5M loan, reports operational strides
- AF&PA urges veto of NY bill
- Aluminum Association includes recycling among 2025 policy priorities
- AISI applauds waterways spending bill
- Lux Research questions hydrogen’s transportation role
- Sonoco selling thermoformed, flexible packaging business to Toppan for $1.8B
- ReMA offers Superfund informational reports
- Hyster-Yale commits to US production