
Legislative and public demand for greater recycling efforts is gaining steam.
Most people recognize that simply discarding used items is a waste of natural resources. They also appreciate that manufacturing replacements for discarded items means using extra energy and emitting more CO2. These costs are even greater when the manufacturing chain begins with new materials rather than with recycled ones.
Recycling is fundamental to sustainability, but to be a viable business, recycling companies need to make a profit. That can be difficult for a variety of reasons.
First is the wildly fluctuating value of recyclables. The price of copper or aluminum, for example, can drop suddenly, making recycling less profitable.
Increasing energy prices also are eating into the sector’s profits. Reducing energy consumption has become vital to staying profitable and meeting increasingly stringent carbon emission targets.
Another challenge is the recycling market’s complexity and rapid rate of change. New materials, processes and technologies require constant investment in expensive equipment, which adds to capital and maintenance costs.
Heavy duties, harsh forces
To understand how wearfacing addresses these problems, first we must look at the nature, function and operating conditions of the machinery. Although recycling is a complex, multisegmented industry, common processes apply to each specialized area:
- collecting materials and transporting them to the recycling site;
- transporting or moving materials within the recycler’s site;
- crushing and/or shredding to the size required for the next process;
- sorting material into different streams;
- further processing, like refining; and
- supplying recycled material to users according to their specifications.
In each activity, contact between materials and equipment results in wear and damage—especially at the contact surfaces. Wearing and damaging forces encountered include abrasion, erosion, impact, fatigue and vibration stress.
Replacing worn parts is costly, and managers must consider not only the price of the new part but also labor costs and the loss of income while the machine is down. Lost output is even higher in the case of unplanned downtime that occurs because of the failure of a worn component during operation.
In key components such as the cutting elements in shredding machines, wear also can lead to inefficiency. A worn cutting edge is less effective, so material could have to be fed through the shredder more than once to reduce it to the required size. That means extra running time, energy consumption and wear for the machine, as well as extra labor to operate and feed it.
In some equipment, more force—therefore more energy—must be applied to a worn blade than a sharp blade.
In each case, using more energy adds to carbon emissions and leads to higher power bills.
Wearfacing is the answer
Recyclers can reduce costs by extending component life through wearfacing, also known as hardfacing.
Protective treatments can be applied to surfaces during the manufacturing or assembly process and can be retrofitted as part of a repair, which restores and improves the component, giving it a second, longer service life.
Although similar machinery and processes can be found across the spectrum of recycling operations, each presents a different set of conditions and needs. Variable factors include the types of materials handled, as well as wear patterns, pressures, temperatures and the presence of corrosive substances.
This creates wear problems that can be solved by a wide range of wearfacing technologies and products. Each can be modified in terms of structure and composition to meet specific requirements. No two jobs are the same.
Today, the main recyclable material segments are ferrous and nonferrous metals, paper, glass, plastic, tires and rubber, textiles and electronic scrap.
While hard materials such as metals could seem especially challenging, even soft substances such as paper have substantial wearing effects on equipment. The same is true for household plastics, and ground glass is particularly abrasive.
Collection vehicles and containers often are the first surfaces exposed to recyclables and their wearing effects.
At material recovery facilities (MRFs), grapples, dumpers, grab trucks, bulldozers and conveyors move materials between processes, and each is vulnerable to wear and abrasion. The same is true for feeder chutes, hoppers, pumps and pipework through which materials pass.
Crushers and shredders typically feature rotating shafts armed with cutting discs, blades, knives, teeth or hammers. Not surprisingly, these can very quickly become blunt and worn out of shape.
In addition to harsh abrasion and constant heavy impacts, machines are subjected to strong vibration forces. Vibration also can be a factor in sorting processes, especially where vibrating conveyors are used. Along with relatively simple sorting using screens of different sizes, more sophisticated methods include magnetic drums for ferrous metals, eddy currents for nonferrous metals, cyclone separators for dust removal, laser techniques to separate materials by color and using X-rays or flotation tanks to separate materials according to density. These technologies require expensive equipment that needs to be maintained and protected.
After sorting, further processing can occur. For example, grinding is used in glass recycling to reduce the material’s size. It is then mixed with other ingredients before proceeding to the glassmaking furnace. Glass grinding and mixing machines face powerful abrasive and erosive effects from these materials.

Comprehensive solutions
For many of the equipment surfaces described, a simple protective approach is to line them with steel wear plates, such as those made with CDP, or CastoDuro Diamond Plates. These plates are hardened with alloys and can be applied to line bulldozer and grab buckets, conveyor sides, chutes and any other containment or transport surfaces in a MRF or recycling facility.
It’s possible to compare alternative solutions using Castolin Eutectic’s EcoTest calculator, which shows cost and CO2 emissions savings for proposed wear protection solutions.
Highly resistant to abrasion, impact and vibration, these types of wear plates can last up to five times longer than original equipment manufacturer linings. They can be cut, shaped and fitted easily to protect any surface using screws, rivets or spot welding. Standard plates are available, or they can be supplied as precut and formed sections matched to the equipment’s size and shape. This latter point is particularly important when lining the cylindrical or conical parts of a cyclone or the inner surfaces of glass crushing, grinding and mixing machines.
A range of wear plates, wearfacings and coating variants exist for different circumstances, with the optimal choice depending on the materials being processed as well as the forces at play.
Pipework requires another ready-made solution, such as tube sections, elbows and Y-joints with alloy-reinforced lining. Known as CastoTubes, various diameters and section lengths are available and simple to assemble.
For the crushing and cutting elements of crushers and shredders, a range of alloy and polymer wearfacing coatings and welding wires can be applied to reinforce surfaces. Ideally, they should be applied to new equipment as a preventive measure, but they can be used in repair and restoration in some cases.
In some cases, the original shape and sharpness of a cutting surface can be restored. However, for large hammers that have lost many pounds of metal through wear, replacement of such a heavy loss by welding is uneconomical. Here, it is important to increase the life of the replacement hammers by applying a wearfacing preventive treatment.
Wearfacings can be used to reinforce and protect grapples, which can suffer aggressive wear from metal-to-metal contact and shocks. Ceramic surfacing polymers also have multiple uses in protecting valuable equipment.
Specialists ready to help
Wearfacing products can be purchased for use by a customer’s own engineers or applied by the supplier’s field engineers, who also can be called for advice, to assess wear problems, recommend solutions and provide training.
This type of advice from suppliers often becomes more valuable over time as they become familiar with a company’s equipment and its health and maintenance history.
Get curated news on YOUR industry.
Enter your email to receive our newsletters.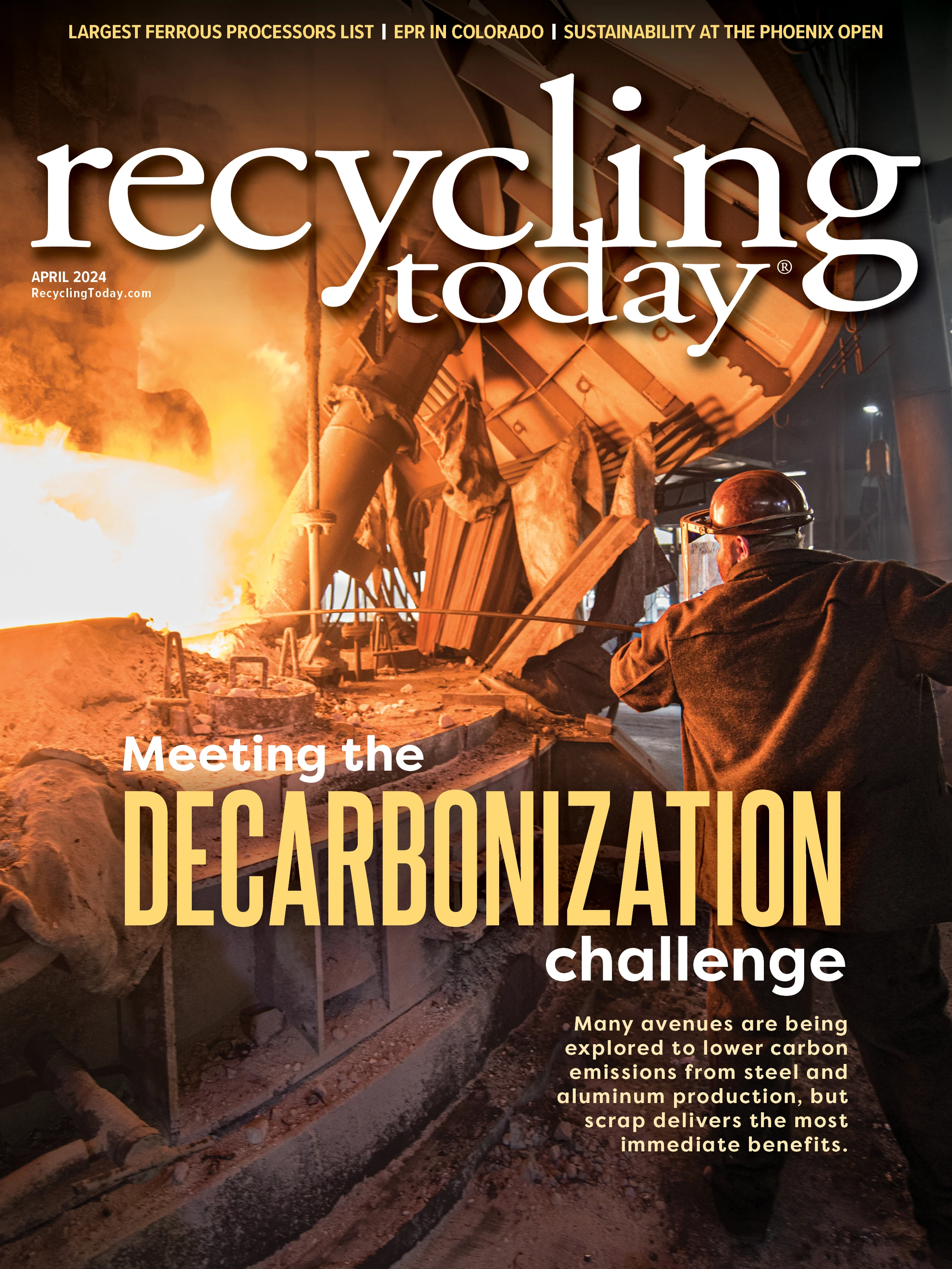
Explore the April 2024 Issue
Check out more from this issue and find your next story to read.
Latest from Recycling Today
- Athens Services terminates contract with San Marino, California
- Partners develop specialty response vehicles for LIB fires
- Sonoco cites OCC shortage for price hike in Europe
- British Steel mill’s future up in the air
- Tomra applies GAINnext AI technology to upgrade wrought aluminum scrap
- Redwood Materials partners with Isuzu Commercial Truck
- The push for more supply
- ReMA PSI Chapter adds 7 members