
Huge investments have been made in the recycling industry in the last 25 years, and with mixed results, Nat Egosi said in his opening remarks at the second annual MRF & Recycling Plant Operations Forum in Chicago Oct. 10.
Egosi led the one-day forum, which brought together 170 attendees, from
“Our focus is on the ‘process’ in the collect, process
The sessions at the MRF & Recycling Plant Operations Forum focused on plant processes, from employee safety to separation of materials. Material recovery facility (MRF) operators and equipment providers, among others, discussed ways to improve procedures, best practices for certain sorting equipment, how to effectively manage tipping floors and retrofits as well as using data to improve operations.
The day flowed in a conversational-style format, allowing attendees to ask questions of the panelists or comment during any of the presentations.
This article summarizes the MRF & Recycling Plant Operations Forum’s Separating Do’s and Don’ts sessions. These back-to-back panel discussions, one focusing on fiber and the other on containers, dug into industry best practices for three key equipment classes: screens, ballistic separators
Separating Do’s and Don’ts
Fiber. Moderator Egosi started the session by noting China’s proposed ban on certain scrap imports, including mixed paper, is mostly because of contaminated loads of imported baled recyclables. Cleaning up quality is a must, he said.
“China is not very nice to us these days,” said Pieter Eenkema van Dijk, CEO of Van Dyk Recycling Solutions, Stamford, Connecticut, and a speaker on the fiber panel.
Van Dijk said he has seen two actions occurring at MRFs that are affecting the way recyclers sort paper: Some recyclers are changing to
“There’s a new way to approach single stream today, a completely different way,” Van Dijk said. “Instead of sending smaller material to screens, send it to an optical sorter. I think, eventually, we’re going away from screens because you can positively sort the paper, and negatives can go to optical.”
In reference to China’s import ban and its proposed 0.3 percent limit on contaminants, panelist Rich Reardon, managing director of Max-AI for Bulk Handling Systems (BHS), Eugene, Oregon, asked, “Who didn’t see this coming?”
Reardon said investing in plants and ensuring the entire system is “commissioned to perform” as it should is important. This includes “making sure the screen is set to the specification provided and that discs are in good shape,” he said.
“We need to rethink our process flow to adapt to what we’re getting in the bin.” – Michael Drolet, Steinert US
As for using screens to collect more old corrugated containers (OCC) from the stream, Reardon suggested operators change screen openings in different zones.
“Should we be focusing on one mixed paper grade and pull out OCC, or can screens be modified?” Reardon asked. “You need to look at the opening on screens by looking at the balance on the system.”
Speakers said plastic film can make up about 5 percent of MRFs’ inbound streams. Reardon suggested using optical sorters and air to remove
Van Dijk said
Panelist David Marcouiller, executive vice president of sales engineering at Machinex Industries Inc., Plessisville, Quebec, confirmed the difficulty of removing
He said the bulk of labor in MRFs today is spent on the fiber line, pulling out film and OCC.
Regarding fiber quality concerns, Marcouiller said using ballistic separators also can be helpful. “As soon as you separate the material by size, you can really attack the problem in a different way,” he said of ballistic separators.
When collecting material in colder climates—where snow and ice, and therefore wetness, thrive—speakers suggested lowering the incline of screens. Additionally, Marcouiller said agitating the material more often can make a real difference.
“Packer trucks are getting better at packing material. … [You] need to agitate material throughout the system,” he said.
Containers. Speakers on the containers panel said it was a matter of space and capital investments in equipment that would permit MRFs to sort flexible packaging and glass, as well as containers, more efficiently.
Nick Davis,
“Flexible packaging is here, and I don’t think it’s going away,” Davis said.
He continued, “There are a lot of different things to consider. It will require
A decade ago, the containers MRFs sorted were mostly used beverage containers (UBCs), said panelist Michael Drolet, solution sales manager for Steinert US, Walton, Kentucky. Today, inbound streams include UBCs, plastics Nos. 3-7, glass
“We need to rethink our process flow to adapt to what we’re getting in the bin,” Drolet said.
He said drum magnets in MRFs started as a trend about five years ago. “The right drum magnet will always be more expensive but will give you cleaner steel.”
However, Davis recognized the reality of accepting any and all materials at the MRF, saying, “We don’t have space to store every possible commodity. There’s market economics and also physical economics.”
Speakers addressed the question, “Can I improve something to better introduce material to optical equipment?”
Panelist Scott Jable, director of North American sales for Stadler America LLC, Colfax, North Carolina, suggested adjusting the angle of the screens. “I always adjust the angle first; the steeper you run your screen, the less contamination.”
He said star screens and ballistic separators have the same idea in mind: trying to get 3D material to go airborne. But for these devices to work properly, they cannot be overrun with
“Try to run your system at what it was designed to,” Jable said. “If you overrun your screens, you’ll bury everything.”
He said most of the issues with optical sorters are mechanical. Overrunning the sorter and not cleaning valves or putting them in the wrong place can cause processing disruptions.
Davis said CP Group has seen a number of MRFs add optical sorters as alternatives to using disc screens.
“Optical sorters, fed correctly, can do everything we’re asking them to do; it takes space and money,” he said. “Nobody has really been willing to spend that much money.”
Davis added, “There are a lot of competing issues working on the economic side, but optical sorters are going to continue to evolve.”
As for robotics, Davis said he sees this type of equipment and optical sorters as competing and also complementary to each other.
The 2017 MRF & Recycling Plant Operations Forum was Oct. 10 in Chicago at the Chicago Marriott Downtown Magnificent Mile.
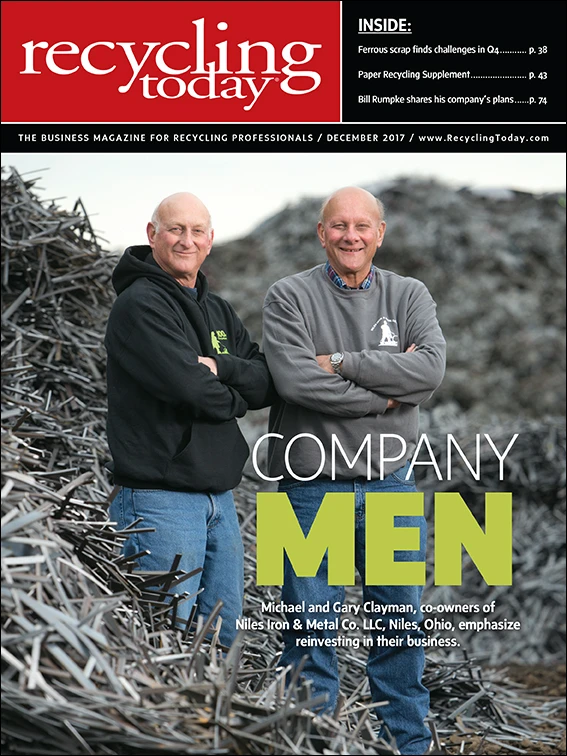
Explore the December 2017 Issue
Check out more from this issue and find your next story to read.
Latest from Recycling Today
- Athens Services terminates contract with San Marino, California
- Partners develop specialty response vehicles for LIB fires
- Sonoco cites OCC shortage for price hike in Europe
- British Steel mill’s future up in the air
- Tomra applies GAINnext AI technology to upgrade wrought aluminum scrap
- Redwood Materials partners with Isuzu Commercial Truck
- The push for more supply
- ReMA PSI Chapter adds 7 members