Life cycle material system efficiency depends on minimizing resource and energy use and undesirable emissions to land, water and air, while satisfying market demand for material. Recycling is a key component contributing to the efficiency of the material system life cycle.
Aluminum recycling, which has been practiced since the 1940s, developed without any benefit of sophisticated sensor-based sorting technologies. Development of automated metal separation and sorting technologies dates back to the 1970s, and sensor-based sorters arrived in the 1980s. In the 1990s, there were common predictions that a sustainable aluminum life cycle would require sorting of aluminum by alloy. These led to the development of elemental composition analysis sensors for automated particle sorters. Yet adoption of these light metal scrap sorting technologies by the scrap or aluminum industries has been slow.
This article explores current aluminum recycling systems and identifies true recycling system needs as well as opportunities for profiting from scrap upgrading.
LIGHT-METAL SCRAP MARKETS
New aluminum scrap generated internally at semi-fabrication rolling and extrusion plants is remelted and generally batched into compatible rolling or extrusion alloy. Prompt aluminum casting scrap is also closed-loop recycled in the foundry or back at a secondary smelter. New manufacturing scrap is often traded on the international scrap market and comes to the remelt or a secondary smelter with less reliable pedigree. It is usually batched together with post-consumer scrap into secondary alloys.
Currently, the aluminum packaging, building, automotive and steel deoxidants markets consume the available post-consumer aluminum scrap. To satisfy product demand, remelts and secondary smelters have to supplement the old scrap feed by purchasing new manufacturing scrap and even prime-metal-based ingot.
SYSTEM-EFFICIENT USE OF SCRAP
In a situation where markets are short of scrap, sustainable system-efficient use of scrap does not require closed-loop recycling of products or alloys but only minimization of losses to oxidation, refining or landfill.
In the life cycle of aluminum, metal losses to landfill can occur in material delivered there from consumers, scrap yards, shredders and dross processors. Sensor-based sorters can help minimize these system losses.
Getting an Upgrade |
Upgrading of aluminum scrap using sensor-based sorting could provide additional profit opportunities when in the form of batching the magnesium die casting AZ91 alloy from magnesium recovered from shredder nonmagnetic metal concentrate. Since steel desulphurization can still consume all post-consumer magnesium scrap, there is little financial incentive to develop a system to efficiently recover this scrap. However, with aluminum recyclers insisting on elimination of free magnesium from aluminum scrap, and the quickly rising use of magnesium die casting for consumer electronic housings and for automotive applications, this situation is quickly going to change and there will be a need to develop a secondary post-consumer magnesium-alloy application. The magnesium AZ91 alloy that contains 9 percent aluminum, 1 percent zinc and greater than 0.3 percent magnesium is a good candidate for such a secondary alloy. It is also the most widely used of all magnesium alloys. A recently developed secondary magnesium alloy AZC1231 that includes 12 percent aluminum and 3 percent zinc can accommodate recycling impurities such as copper and some nickel and iron without runaway corrosion and with excellent castability. For post-consumer scrap that may contain a variety of exotic alloys, a particle-sorting plant equipped with an elemental concentration sensor sorting circuit will likely be required to technically accomplish this AZ91 batching task. There also will be an economic incentive to accumulate and sort the residue stream, which contains exotic strontium, calcium, cerium, lanthanum, neodymium and other high value alloying elements. |
Recovery of Recyclables from Landfilled Post-Consumer Waste. By far the largest of these losses is in landfilled post-consumer material. U.S. Environmental Protection Agency (EPA) figures for 2006 show that U.S. landfills consumed 1 million metric tons (1,000 kilotons) of aluminum cans and another 1,500 kilotons of other aluminum items in municipal solid waste (MSW). These aluminum loss figures account for neither industrial waste nor for construction and demolition waste (CDW).
Sensor-based sorters figure prominently among the technologies required for “dirty” material recovery facilities (MRFs) that can process the landfill-bound MSW. With the aluminum being dispersed in 140,000 kilotons of MSW and another 100,000 kilotons of CDW in the United States, it is clear that these facilities cannot be economical only by cherry picking metal scrap, but have to attempt to recover all the recyclable components of the materials. In municipal recycling facilities, sensor-based sorters pick out the residual metals missed by magnets and eddy current rotor separators. They also sort out plastics and sort paper and cardboard by grade for recycling.
Residual Metal Removal from Shredder Residue. Primary shredder feed consists of steel containing approximately 25 percent nonmetallic particles and from 5 to 10 percent nonmagnetic metals. Even a small concentration of nonmagnetic metal in the nonmetallic residue can represent significant loss of recovery of the nonmagnetic metals. Eddy current coil (ECC) sensor sorters inspect and recover the residual metal from nonmetallic residue. The dual energy X-ray transmission (DE-XRT) sensor has the capability to separate light from dense metals, replacing the function of the dense media sink-float plants. Dual sensor ECC and DE-XRT sensors have the resolution and capability to inspect shredder fines residue that still contains small copper wires and small aluminum particles.
Dross Processing. Dross is a partially oxidized residue from the light metal melting operation. With typical metal recoveries on melting ranging from 92 to 99 percent, and nearly 70 million tons of light metals being melted annually around the world, there is a lot of metal to be recovered from dross. Prior to being remelted in rotary furnaces, aluminum metal is typically concentrated by crushing dross and by eddy current rotor separation (ECS). This mechanical separation is sometimes repeated for the rotary furnace dross, or salt cake. The oxide and salt residue still contains metal inclusions too small to be separated by ECS. There are no reliable figures on the quantity of metal lost in this stream, as dross processors seldom track and never publish data on the metal content of their oxide/salt residue. United States Geological Survey (USGS) data for 2006 reports more than 600 kilotons of metal recovered from dross and skimmings. We estimate that the U.S. residue consists of more than 1,500 kilotons of nonmetallics containing up to 30 kilotons of metal.
Dual sensor ECC and DE-XRT sorters have the resolution and capability to inspect crushed oxides for residual metal.
Separation of Bare and Painted Scrap. De-coating of bare scrap is a waste of effort and energy, while melting of painted scrap results in excessive melt losses. The used beverage container (UBC) provides an extreme example. Melting of painted cans in a rotary furnace rarely gives a metal recovery of more than 85 percent, whereas careful decoating and vortex submergence melting routinely give net metal recoveries of 97 percent. Aluminum from old post-consumer scrap is a mixture of bare and painted items. USGS data for 2006 reports 215 kilotons of non-UBC wrought old scrap and 155 kilotons of old cast scrap were consumed by U.S. smelters. Much of it could benefit from bare/painted separation and decoating of the painted fraction.
A particle sorter equipped with a color camera sensor is sufficient to perform this separation after the material is shredded and sized. Reduction in melt losses is more than adequate to offset the additional processing costs.
Separation of Nonmetal Contaminants and Attachments from Scrap Metal Products. As is the case with paint, residual paper, plastic and rubber particles and attachments in aluminum scrap burn during remelting, leading to oxidation and melt losses. The 190 kilotons of aluminum recovered from shredder metal concentrate and consumed in U.S. in 2006 could have been melted with lower melt losses if the residual contaminants were sorted out of the furnace feed. Another 1,000 kilotons of other old aluminum scrap consumed in U.S. in 2006 would need to be shredded to permit removal of contaminants and attachments. In 2006 there also were 2,000 kilotons of new manufacturing trim scrap in the U.S., some of which could have been recycled to applications using alloys closer to the original alloy composition if contaminants were identified in, and removed from, the nominally source segregated scrap. A particle sorter equipped with a DE-XRT sensor is up to this task.
Separation of Magnesium-Based Scrap from Aluminum Scrap Products. Magnesium components are still a small fraction of light-metal scrap coming back from consumers. Some estimates put it as high as 2 percent of aluminum coming back in end-of-life automobiles or approximately 1 percent of the light metal shredder output. If this material finds a path all the way to secondary foundry aluminum smelters, it will more than double the amount of chlorination required and associated melt and time losses.
The quantity of the magnesium-alloy components entering the consumer market is rising steadily and unless magnesium-aluminum separation is implemented, related losses will continue to mount in the future. Without aluminum-magnesium separation, 200 kilotons of magnesium die castings that have entered the automotive market will contaminate more than 5,000 kilotons of aluminum automotive castings and will lead to losses of the 200 kilotons of magnesium and similar amounts of aluminum in refining by chlorination. In the near future, aluminum-magnesium separation will become imperative to maintain the efficiency and sustainability of the light-metal life cycle.
Options for aluminum-magnesium segregation are either density separation in a dense media plant or sensor-based sorting. Only a few media plants are left in North America and no new ones are being built. This leaves sensor-based particle sorting, where a combination of color and DE-XRT sensors can do the sort.
Separation of Aluminum Alloys with High Magnesium (or Lithium) Content from Those with High Silicon, Copper or Zinc in Aluminum Scrap. There is much more magnesium in aluminum scrap as an alloying element than as free magnesium-alloy particles. The current level of refining by chlorination and the associated losses can be substantially reduced by sorting out aluminum-alloy particles rich in magnesium and batching them into secondary wrought alloys. 3X04 can body sheet and 3105 building sheet are suitable candidate alloys. The second output stream will be high in silicon, copper and zinc and low in magnesium, giving it an added value when batching foundry alloys.
Such a sort can be performed by a sorter equipped with an elemental analysis sensor based on laser-induced plasma spectroscopy (LIBS). The first industrial plant based on this technology was commissioned in 2004 by Huron Valley Steel Corp. in Belleville, Mich., and has been successfully operating since then on a feedstock of aluminum recovered from shredder metal concentrate.
Separation of Magnesium Alloys with Strontium, Calcium or Rare Earth Alloying Element Content from Those with Magnesium and Zinc in Magnesium Scrap. Exotic magnesium-based alloys containing calcium, strontium or rare earth elements, such as cerium, neodymium, lanthanum, gadolinium, and europium, are being developed for the creep resistance required by automobile power train applications. These are composition incompatible with the common magnesium die casting alloys, which are based on aluminum, zinc and manganese alloying elements. The first application in BMW engine blocks put 7 kilotons of such alloys in the 150 kiloton automotive magnesium component market in 2006. Other applications are under development.
As mentioned above, virtually all recovered post-consumer magnesium scrap is used for steel desulphurization, which results in consumption of the metal and hence permanent loss of the expensive exotic alloying elements.
As applications using magnesium for automotive components grow, separating the magnesium alloys with exotic alloying elements will be mandatory to enable recycling of magnesium and its alloying elements as magnesium alloys.
Two elemental analysis sensor technologies are technically feasible for this task—X-ray fluorescence and LIBS.
VALUE-ADDED USES OF SCRAP
In the case of light metals, additional recovery of scrap from waste replaces prime metal with secondary metal, the melting and treating of which requires only about 5 percent of the energy required to produce prime metal from ore. This vastly improves the sustainability component of the light-metal life cycle.
Once the scrap is upgraded to the point where all of it can be remelted and reused, any additional processing consumes additional energy and resources without further reduction in prime demand and, hence, is counterproductive from a global material life cycle perspective.
However, there are regional, national or company strategic considerations that often trump the global sustainability point of view and may justify further scrap upgrading. Europe and the U.S., having shut down much of their primary light-metal production facilities and having exported much of the low-tech, labor-intensive foundries to Asia, must import prime metal to keep producing beverage cans, building products and automotive sheet in rolling mills that took billions of dollars of capital investment.
Adding value to scrap is another measure of the efficiency of scrap use. Although closed-loop alloy or product recycling is seldom a requirement of a sustainable recycling system, there are opportunities to profit by recovering the value locked up in the scrap composition.
Currently there are small differences between the prices paid by the remelts and the secondary smelters for upgraded aluminum scrap products or between the prices of various types of remelt ingot that would justify scrap sorting by alloy.
Sensor-based sorting can still uncover additional opportunities for profit. The price of scrap changes as it is recovered and upgraded. Scrap in waste bound for the landfill has a negative value, i.e. the landfill tipping fee. Scrap at the curbside has a zero value to the consumer. In 2007, cans recovered from curbside recyclables at the MRF were sold for about $1 per kilogram to the scrap dealer, who collected truckload quantities and sold the same UBCs at closer to $1.75 per kilogram to the UBC remelter.
Auto scrap shows a similar story. A customer with a wreck on his or her hands pays for towing it to the dismantler. The dismantler, after scavenging spare parts, sells the flattened hulk for about $100 per ton to the shredder. The shredder sells the aluminum content in the nonmetallic metal concentrate to the sorter or media plant at about $1 kilogram, which in turn in 2007, sold its aluminum “twitch” product to secondary smelters for about $1.80 per kilogram.
Clearly a remelt operator who installs scrap sorting and upgrading equipment can buy scrap earlier in the value chain and pocket the profit. Such action satisfies regional and company strategic objectives by locally retaining the low-cost raw materials for the benefit of local industry, employment and economy.
Conversely, scrap collectors and shredders at the beginning of the value chain can increase their take by integrating downstream and investing in shredding and scrap sorting. However, they are free to sell the upgraded scrap to the highest bidder—often an Asian scrap importer supplying Asian foundries. The local economy suffers and the global light-metal life cycle absorbs the energy charge of long-distance transportation and losses associated with refining out the magnesium from aluminum foundry alloys.
MISSED PROFIT OPPORTUNITY
The current global recession severely impacted the recycling industry. In the fall of 2008, many Asian consumers stopped buying scrap and the scrap market could not be supported by the remnants of the local North American and European secondary metal industry. Scrap prices collapsed and shredders stopped shredding.
It took billions of dollars of government incentives in the form of “cash for clunkers” programs to refuel the stream of scrap passing through the auto shredders. With scrap supply exceeding demand, the price margin between the scrap and the prime based alloys increased and would have provided a rich profit opportunity for any rolling mill or extrusion press remelt, or secondary smelter equipped to upgrade scrap, now cheap and easily available, to its output product composition specifications.
Alas, in the five years previous to the onset of the global recession, the hot seller’s market in scrap shipped to Asia has dissuaded metal remelters and refiners from investing in the scrap sorting circuits.
Consequently, there are very few companies beyond Huron Valley Steel that are equipped to profit from this economic downturn and the glut of lower-cost scrap.
We can only hope that this lesson will spur the metal producing and recycling industry to retain local plants in North America and Europe and to invest in scrap upgrading circuits, including sensor-based sorters.
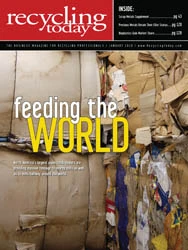
Explore the January 2010 Issue
Check out more from this issue and find your next story to read.
Latest from Recycling Today
- Nucor receives West Virginia funding assist
- Ferrous market ends 2024 in familiar rut
- Aqua Metals secures $1.5M loan, reports operational strides
- AF&PA urges veto of NY bill
- Aluminum Association includes recycling among 2025 policy priorities
- AISI applauds waterways spending bill
- Lux Research questions hydrogen’s transportation role
- Sonoco selling thermoformed, flexible packaging business to Toppan for $1.8B