
BD Plast screen changer features three sliding filter plates
CleanChanger: Italy’s BD Plast Filtering Systems Srl has developed the CleanChanger, a continuous-flow, backflushing screen changer for plastics recycling and compounding, as well as for fine filtration in film, sheet and profile extrusion. Designed to meet demanding filtering needs, it has laser microperforated filter elements and is appropriate for postconsumer and postindustrial polyolefins, as well as engineering resins. Contaminated polymer flows through three channels to the unit’s three sliding filter plates then through downstream channels to the extrusion die. During automatic cleaning (backflushing) or screen replacement, two of the three plates remain in the working position, minimizing downstream pressure fluctuations and allowing for uninterrupted production. Innovative Recycling Solutions is the U.S. distributor for BD Plast.
What’s new? The CleanChanger and its three sliding filter plates. It is available in the U.S. after debuting in Europe.
Benefits: Cost and labor savings. The automatic CleanChanger minimizes the need for operator involvement, eliminates downtime for filter replacement and reduces polymer waste. The compact system is engineered to be easily integrated into all types of extrusion lines and features optimized flow channels with no dead areas. Additionally, the screens can withstand more than 300 backflushing cleaning cycles before needing to be replaced.
Innovative Recycling Solutions, Greer, South Carolina, 864-675-0775, www.irecyclingsolutions.com

CMG granulators tailored for thermoforming scrap
GT Series: Italy’s CMG SpA has launched a line of granulators designed for inline recycling of thermoforming scrap, including sheet, skeletal sheet and reject parts. The line consists of four models, with throughputs ranging from 441 pounds to 2,205 pounds per hour. The granulators have a low profile for positioning directly underneath equipment, such as conveyor belts. CMG granulators are available in North America through Universal Dynamics.
What’s new? The series and its specialized blade configuration. The rotor blades are positioned at 50 degrees in relation to the bed blade for cutting precision. Additionally, each granulator’s screen is oriented horizontally directly under the cutting chamber for minimal residence time of the regrind. The machines also feature a full-vacuum evacuation system.
Benefits: Robustness, precision cutting and high throughputs. The special blade configuration results in dimensional homogeneity of the regrind and minimal dust creation. The granulators’ evacuation system preserves the integrity of the regrind by conveying it under negative pressure in large-diameter pipes. Additionally, the machines are fully insulated for quiet operation.
Universal Dynamics Inc., Fredericksburg, Virginia, 703-490-7000, https://unadyn.piovan.com, www.cmg-granulators.com

Kreyenborg system tackles tough odors
IR-Fresh: Kreyenborg’s modular IR-Fresh system can be retrofitted to existing extrusion lines to remove unwanted odors from postconsumer plastic flakes and pellets. It is appropriate for treating a wide variety of resins, including polypropylene, high-density polyethylene (PE), low-density PE, thermoplastic elastomers, polystyrene and polyamide. The system is effective at eliminating smells left by food, cleaning agents, cosmetics, chemicals and fuel. It can be used to treat plastic flakes before they enter an extruder for processing and pelletizing or can be set up after the pelletizing step to treat finished pellets. In the U.S., IR-Fresh is distributed by eFactor3.
What’s new? The IR-Fresh system, which employs a two-step process. In the first step, it constantly rotates the plastic in a drum while heating it via an infrared light module. In the second step, any remaining odors are eliminated using heat and air flow in the IR-Fresh conditioner. In addition to being retrofittable to extrusion lines, IR-Fresh can operate as a continuous or discontinuous stand-alone process.
Benefits: High-quality recycled pellets and flakes. The system uniformly treats materials to safely and efficiently remove odors that can’t be eliminated by washing alone. It requires no vacuum and protects polymer properties with short residence times. The company says gas chromatographic analyses confirm a significant reduction in the presence of volatile organic compounds after the IR-Fresh process. Also, recovered heat from the air exhaust in the first step is applied to the second step for energy-efficient operation.
eFactor3, Charlotte, North Carolina, 704-944-3232, www.efactor3.com, www.kreyenborg.com

BCA electric shredder operates cleanly
ES2000: BCA Industries manufactures a wide range of fixed and portable industrial shredders and recycling equipment, with models offering 10 horsepower (hp) to 800 hp. Traditionally, hydraulically powered shredders have been the choice for plastics processors recycling in-house plastic scrap and for recycling facilities dealing with oversized parts, such as totes, barrels or white goods, and hard materials, such as thick-gauge metals.
What’s new? The ES2000 line of electric-powered models. While hydraulic shredders provide slightly more torque than electric shredders, they can be overkill for parts made exclusively of polypropylene, polyethylene or polyethylene terephthalate. Electric models can deliver more than 100,000 foot-pounds of torque per knife. The electric shredders offer programmable functions and diagnostics via touch screen, as well as auto-reverse and overload protection.
Benefits: Cleaner operation. Electric-powered shredders are less expensive than comparable hydraulic versions. They also bypass the need for inspection and maintenance tasks associated with fluid leaks and ruptured hoses and avoid the potential for slip and fall injuries caused by hydraulic fluid leaks. Chamber sizes range from 4 square feet to as large as 4 feet by 6 feet, with models providing 100 hp to 800 hp. Electric shredders also operate at a lower decibel level than their hydraulic counterparts.
BCA Industries, Milwaukee, 414-353-1002, www.bca-industries.com/shredders

Efficient Pallmann pulverizer creates
high-quality powder
PKM800: Pallmann Industries’ new pulverizer can process extruded poly- vinyl chloride (PVC) scrap at rates up to 2,000 pounds per hour so that it can be mixed with virgin PVC and returned to the manufacturing process. The machine uses segment cutting technology, which features different types of serrations for different applications, making it adaptable to many different plastic materials.
What’s new? An enclosed, pulse jet bag housing that contains the dust. Unlike units with traditional hanging filter bag plenums, the PKM800 blows out air and discharges the dust downward into a container.
Benefits: Cleanliness, efficiency and productivity. Segment cutting technology employs a scissors-cutting action for more efficient use of cutting energy, less heating and the production of fewer fines. The company says the PKM800 outperforms the previous competitive model by 2-to-1 in terms of production. The pulverizer produces a high-quality powder with uniformly sized particles for better finished part quality. Additionally, Pallmann constructs the machine with strong weldments, instead of standard castings, for durability and long service life.
Pallmann Industries, Pompton Plains, New Jersey, 973-471-1450, www.pallmannindustries.com

Ampacet’s OdorClear quells strong smells
OdorClear: Ampacet’s odor-absorbing masterbatches are designed for use with a broad range of recycled polymers and can be formulated specially for injection molding, blow molding, film extrusion and other extrusion processes. The wide-spectrum masterbatches eliminate smells from contaminants or residual contents that degrade during the recycling process. OdorClear products can be used in combination with other products in Ampacet’s R3 Sustainable Solutions family of compatibilizers and masterbatches, including ones that minimize thermal degradation and improve color consistency of recycled materials.
What’s new? Compatibility with more resins. Originally introduced as Odor Scavenger, the expanded OdorClear product line now can be used with postconsumer polyethylene and polypropylene.
Benefits: Sustainability. Undesirable smells can limit the amount of postconsumer plastic that can be used in new products. According to Ampacet, OdorClear masterbatches outperform conventional inorganic odor-scavenging solutions, allowing the use of a larger proportion of recycled content in plastic products.
Ampacet Corp., Tarrytown, New York, 914-631-6600, www.ampacet.com
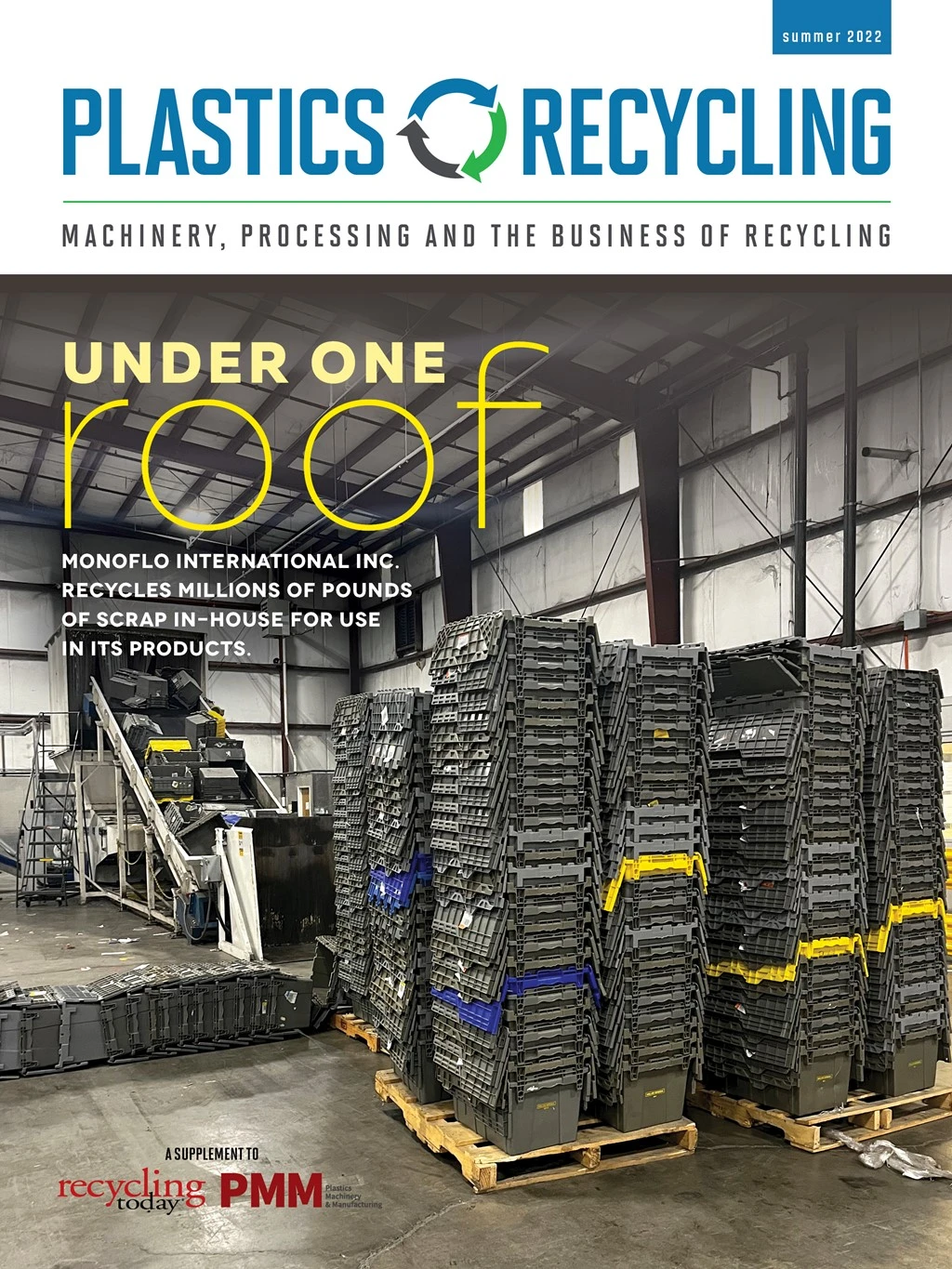
Explore the Summer 2022 Plastics Recycling Issue
Check out more from this issue and find your next story to read.
Latest from Recycling Today
- Lautenbach Recycling names business development manager
- Sebright Products partners with German waste management equipment company
- WasteExpo transitions to biennial format for enhanced experiences
- Study highlights progress, challenges in meeting PCR goals for packaging
- Washington legislature passes EPR bill
- PureCycle makes progress on use of PureFive resin in film trials
- New copper alloy achieves unprecedented high-temperature performance
- Gränges boosts profits and sales volume in Q1 2025