
Multichannel separator collects impurities using negative pressure
Zig-zag: This BoReTech multichannel separator employs negative pressure to collect impurities smaller than 0.2 millimeters in the final stage of the recycling process. When the collection bag is full, the unit triggers an alarm to remind the operator to replace the bag. The pressure is adjustable for different operation purposes. The units are mostly employed in lines that deal with polyethylene terephthalate (PET) or biaxially oriented polypropylene (PP). In the U.S., John Xu represents the Chinese company. He can be contacted at john@bo-re-tech.com or at sales@bo-re-tech.com.
What’s new? The Zig-zag, which came out last year.
Benefits: The recovery of fines and dust that can be further recycled. Dust collected by the Zig-zag can be used through secondary treatment to produce lower-quality recyclate suitable for some applications. The Zig-zag can handle a throughput of about 8,800 pounds an hour, assuming PET flakes are about 10 millimeters to 12 millimeters.
BoReTech Environmental Engineering Co. Ltd., Pinghu, China, 86-573-8513-6190, www.bo-re-tech.com

Screenless, low-speed granulators efficiently process various resins
S-Max 3: This series of screenless, low-speed granulators from Wittmann Battenfeld efficiently grinds engineering resins, styrenic resins, acrylics and glass-fiber-reinforced plastics down to granules from 4 millimeters to 10 millimeters in size. The compact granulators feature a hopper made with sound-dampening material between sheets of stainless steel that reduces noise when plastic pieces hit the hopper walls. They also have audible and visible alarms to alert operators when the regrind bin is full.
What’s new? An optional built-in feeding shaft that is independently driven and keeps large runners and parts in motion. It has elongated hooks to precut the parts and runners and push them into the cutting chamber.
Benefits: Better feeding. The feeding shaft helps prevent bridging and nesting, especially of flat parts and long runners. It reduces downtime from material backing up or overflowing. Additionally, because the shaft size reduces the plastic before it reaches the cutting chamber, the use of a smaller, less-expensive granulator could be possible.
Wittmann Battenfeld Inc., Torrington, Connecticut, 860-496-9603, www.wittmann-group.com

Shredders’ knife technology offers versatility and improved cutting
Shredders: Lindner’s Micromat and Antares series shredders come in several sizes. The shredders also can process a wide variety of plastic scrap.
What’s new? A “smart-system” version of the company’s Mono-Fix knife technology. Originally developed to minimize downtime, Mono-Fix features knives and knife holders that can be changed quickly using only one screw. The company has developed additional pointed and flat knives, as well as plates and special counter knives that can be provided as a turnkey package. Lindner can tailor the packages to the specific shredder model and material. The turnkey packages can be retrofitted to existing Micromat and Antares shredders.
Benefits: Versatility and better cutting. The smart systems can feature pointed and flat knives to avoid common problems that arise when shredding difficult materials, such as large lumps and purgings. The systems’ filler plates can be used to adjust the aggressiveness of the cutting unit, enabling the machine to shred heavy materials at high throughputs. Additionally, it is simple to replace the entire cutting system when needed.
Lindner Recyclingtech America LLC, Statesville, North Carolina, 800-235-1391, www.lindner.com

NIR-sortable black pigment facilitates recycling
NIR Black: Techmer PM’s black pigment for plastics can be sorted by recycling systems that use near-infrared (NIR) light to identify different materials. This is in contrast to commonly used carbon black pigments that absorb NIR light, making it nearly impossible to sort plastics containing them.
What’s new? Improved grades of NIR black colorant that work with high-density polyethylene, PP and PET and are Food and Drug Administration compliant, allowing for use in food containers. Techmer can tailor the pigment to accommodate different resin grades, product thicknesses and the level of postconsumer content.
Benefits: Improved recyclability for black plastics. The new grades facilitate recycling of black plastic products, allowing brand owners to better meet sustainability goals without compromising on color quality.
Techmer PM LLC, Clinton, Tennessee, 865-457-6700, www.techmerpm.com

Liquid-state-polycondensation system offers continual IV adjustments
VacuFil: BB Engineering’s VacuFil liquid-state-polycondensation system processes PET so it can be used in high-end filament and textile fiber products. To achieve a high degree of melt homogeneity, it uses drying, controlled plasticizing, large-scale filtration and controlled vacuum degassing. The system includes an inline viscosity measuring unit that is connected to a vacuum system that allows the intrinsic viscosity (IV) of the resin to be continuously adjusted, creating the specific type of recycled polyester required for each application. It can process bottle flakes, agglomerated spinning waste or a combination of the two into PET granulate, or it can feed downstream processes.
What’s new? An upgrade to a key component, the Visco+ vacuum filter, which removes volatile contamination and ensures a controlled increase in the IV. The new version has a larger filter area and is available as an easily installed component for existing VacuFil systems, as well as for competitors’ PET processing systems.
Benefits: Efficient production of a homogeneous, pure polymer melt. The new filter’s larger surface area improves filter performance, allowing more contamination to be removed without affecting throughput. The Visco+ can be installed in systems that are struggling with IV fluctuations, balancing out irregularities. It also can be used to increase the IV of recycled materials without the negative effects of long residence times.
BB Engineering GmbH, Remscheid, Germany, 49-2191-9510-100, www.bbeng.de

Baghouse filter features improved design
GR Filter: This baghouse filter from Kice is appropriate for use in plastics recycling facilities that generate dust when plastics are ground, shredded or granulated. A temperature rating of 150 F is standard; a maximum operating temperature of 300 F is optional. Additionally, the GR Filter features an energy-efficient 7.5-horsepower blower.
What’s new? The baghouse filter, the latest product in the company’s line of filtration and dust-control equipment. Kice has improved the design with a patented method for controlling and activating the reverse-air cleaning system.
Benefits: Efficiency. Compared with previous products, the GR Filter has a more reliable cleaning mechanism and uses less energy. It offers an extended filter bag life and features a user-friendly design.
Kice Industries Inc., Wichita, Kansas, 316-744-7151, www.kice.com
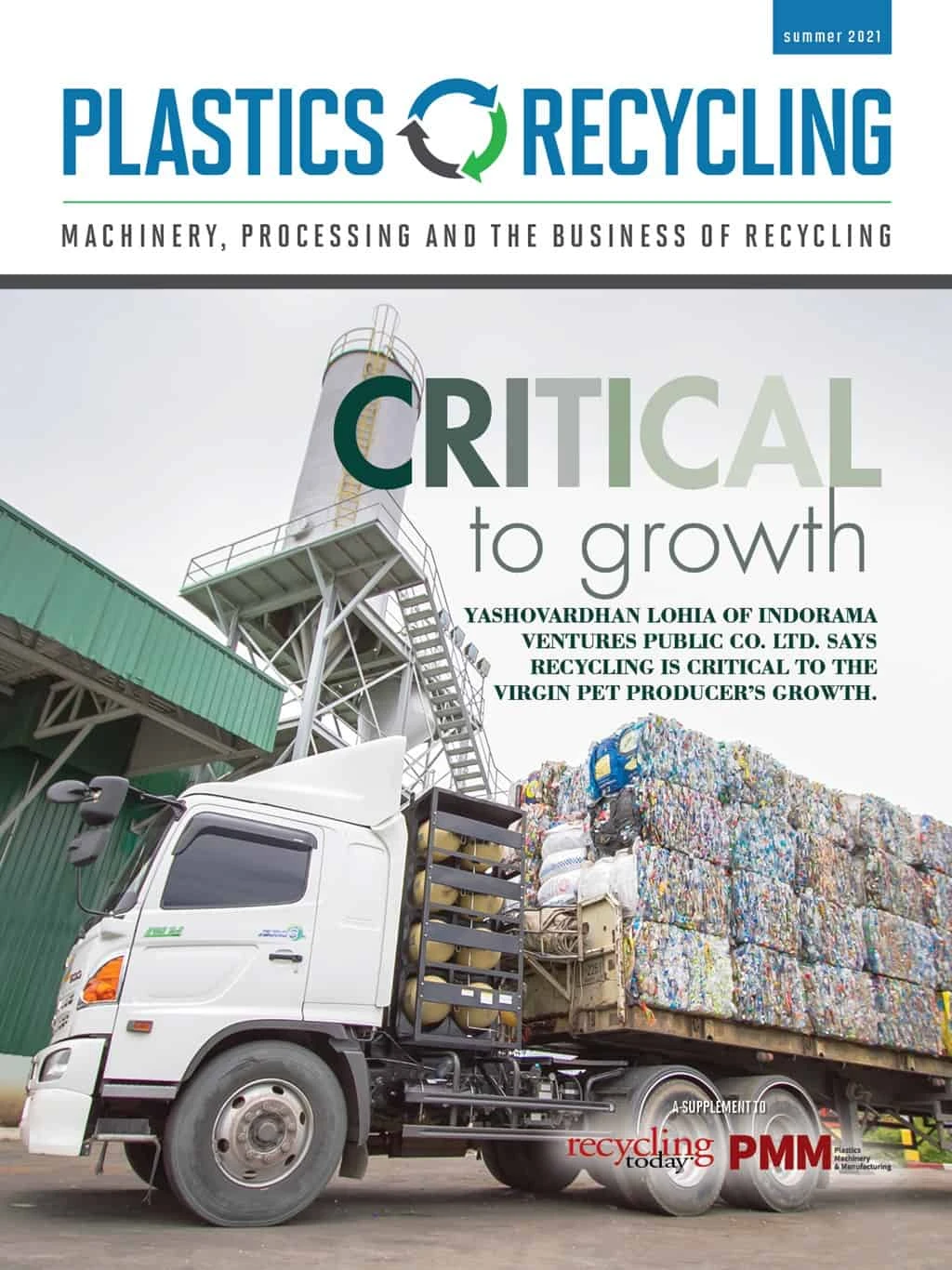
Explore the Summer 2021 Plastics Recycling Issue
Check out more from this issue and find your next story to read.
Latest from Recycling Today
- AF&PA report shows decrease in packaging paper shipments
- GreenMantra names new CEO
- Agilyx says Styrenyx technology reduces carbon footprint in styrene production
- SABIC’s Trucircle PE used for greenhouse roofing
- Hydro to add wire rod casthouse in Norway
- Hindalco to invest in copper, aluminum business in India
- Recycled steel price crosses $500 per ton threshold
- Smithers report looks at PCR plastic’s near-term prospects