
Dewiring machine features optional camera system
Dewiring machines: Cross Wrap’s dewiring machines automatically cut and remove wires from bales of recyclable plastics and then coil them into tight bundles, keeping them out of the recycling stream and eliminating what can be a hazardous job for workers. Designed for throughputs of more than 60 bales per hour, the machines can be customized to fit existing recycling lines.
What’s new? An optional camera system.
Benefits: The new camera system enhances plant security, allows remote machine monitoring and helps with troubleshooting by recording machine operation.
Cross Wrap Oy Ltd., Siilinjärvi, Finland, 358-17-287-0270, www.crosswrap.com

A closed loop for big bags
Big bag recycling line: Starlinger has developed a process for the production and recycling of flexible intermediate bulk containers, known as big bags, used in the shipment of free-flowing materials. The process starts with a proprietary, monomaterial polypropylene (PP) bag, designed by Starlinger especially for recycling. Starlinger’s production and recycling process comprises tape extrusion lines, winding machines, circular looms, coating lines and recycling lines. The process includes a special configuration of Starlinger’s recoStar Dynamic recycling line equipped with two filtration systems to eliminate higher levels of contamination.
What’s new? The possibility of producing and recycling big bags in a closed-loop system. According to Starlinger, the process is the first to provide a circular solution to the problem of the waste created by big bags, which have been treated as single-use products.
Benefits: The reuse of a product that’s typically been regarded as disposable. Normally, big bags are made of multiple materials and feature designs or printing that complicate recycling. They have been difficult to recycle because they come in a variety of forms: with or without a polyethylene liner; coated or uncoated; and with loops and seams consisting of different kinds of plastic. According to Starlinger, about 380 million four-loop big bags are sold each year; about three-quarters of the big bags are used only once before being incinerated or sent to a landfill. Using Starlinger’s bag design, process and lines, manufacturers can produce big bags with recycled PP content of up to 50 percent.
American Starlinger-Sahm Inc., Fountain Inn, South Carolina, 864-297-1900, www.starlingersahm.com

Eddy current separators include new hood design
RevX-E MK3: Eriez’s eddy current separator can remove metals from a material stream. Units are available in widths of about 3.3 feet, 3.9 feet and 4.9 feet. The separators can be configured with a heavy-duty vibratory feeder, feeder support framework, separation shroud/splitter and controls for turnkey installation.
What’s new? Upgrades to two models last year—the ST22 for handling fine materials and the LT2 for coarse materials. The ST22 is appropriate for removing metals from shredded plastics and polyethylene terephthalate (PET) flake. The second upgraded model, the LT2, offers a deep, high-powered eddy current field that allows for the removal of large metal objects, such as crushed aluminum cans, from a PET bottle stream. Both eddy current separator models feature a new hood with an adjustable splitter that allows operators to specify the size of materials the machines should handle.
Benefits: The ability to recover high-value metals and improve the purity of plastic scrap.
Eriez, Erie, Pennsylvania, 814-835-6000, www.eriez.com

Compactor densifies foamed EPS
Styro-Hybrid: Expanded polystyrene (EPS) recycling equipment specialist Brohn Tech has added to its portfolio with this movable EPS compactor. The compactor works in two ways: It has a screw that compresses material, and it reuses exhaust heat to force air from the foam. The Styro-Hybrid can be used by waste-management companies.
What’s new? The compactor. Based on the design of the trailer-mounted Styro-Portapactor, which garnered the National Waste Recycling Association’s 2019 Recycle Equipment Innovator of the Year award, it is now hitting the market. It can be used as a stationary unit or trailer- or hitch-mounted.
Benefits: Cost-effectiveness and efficiency. Powered by a gas engine, the Styro-Hybrid is mobile and does not require access to electricity. The foamed material it processes is transformed into dense plastic that is ready to be used in making new products.
Brohn Tech LLC, Carthage, Illinois, 314-699-4798, www.brohntechllc.com
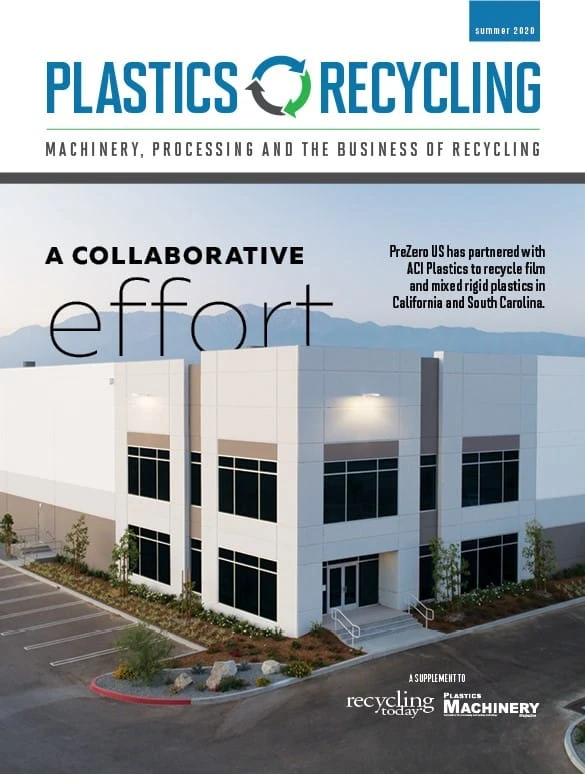
Explore the Summer 2020 Plastics Recycling Issue
Check out more from this issue and find your next story to read.
Latest from Recycling Today
- ICM to host co-located events in Shanghai
- Astera runs into NIMBY concerns in Colorado
- ReMA opposes European efforts seeking export restrictions for recyclables
- Fresh Perspective: Raj Bagaria
- Saica announces plans for second US site
- Update: Novelis produces first aluminum coil made fully from recycled end-of-life automotive scrap
- Aimplas doubles online course offerings
- Radius to be acquired by Toyota subsidiary