
Vecoplan combines shredder, granulator in single unit
VD 1100: Vecoplan’s VD 1100 combines a shredder and a granulator in one unit and is especially suited for shredding lumpy, chunky or bulky material, including large hollow parts, mixed-plastic agglomerates, pipe and films. The machine features a thick-walled, ribbed-steel housing and a durable, balanced rotor with high cutting power for a maximum throughput of about 3,300 pounds per hour. The shredder is powered by a 37-kilowatt (kW) electric motor, and the granulator has a 15-kW electric motor.
What’s new? U.S. availability for the machine, which was introduced last year at the K show. It complements Vecoplan’s existing systems that combine shredding and granulating.
Benefits: The ESC drive lends acompact footprint and energy efficiency. Also, the cutting gap is easily adjusted on the quiet, easy-to-clean machine.

Air filter available in range of sizes
Dust filters: Designed for dust-collection systems, Kice’s air filters can handle volumes of up to 40,000 cubic feet per minute. Within the plastics industry, the Kice Multi-Aspirator collects dust and fines in a cyclone receiver or baghouse filter. Using a fan, it blows off dust from good material produced by grinders or shredders. The Multi-Aspirator is available in diameters ranging from 6 inches to 12 feet.
What’s new? An optional quick-release design for the company’s air filters, which can be used in recycling facilities to handle wet mists, fumes and dust.
Benefits: Easier, safer maintenance. The quick-release design features quick-release laterals that are removed easily without the use of tools for installing filter bags. They provide operators with easy access to filter bags and cages during a bag change.

Self-cleaning melt filter adapted for PET recycling
Laserfilter: Erema has adapted its continuous, self-cleaning melt-filter system for PET recycling. It features a rotating scraper and a discharge unit to control melt flow.
What’s new? Ultra-fine screens, made with a laser by Erema, that can filter materials as small as 70 microns.
Benefits: Very stable filtration with minimum melt losses. The Laserfilter processes input material with a degree of contamination ranging from 4 percent to 5 percent. Recycled material processed by the filter exhibits no black spots as it is only held on the filter screen for a short time. Additionally, to reduce the risk of contamination from frequent screen changes, the screen has been designed to function well over long periods.

Hydraulic dumper empties bulk solids
Tip-Tite: Flexicon’s newest hydraulic dumper is used to empty bulk solids from mobile bins into processing equipment or storage vessels. Within the plastics recycling industry, wheeled tote bins can be used to transport shredded plastic. The tote dumper lifts the wheeled tote and seals its rim against a discharge hood. The hood has a spout that can connect to conveying, blending or other processing equipment. The dumper can accommodate bins up to 44 inches high and 48 inches wide. It is constructed from carbon steel, with stainless steel used for its material handling surfaces.
What’s new? The dumper.
Benefits: Dust-free discharge owing to the pneumatically actuated slide gate valve at the spout outlet.

Granulator series features three models
T50: The three models in this series of granulators from Cumberland are designed to chop up large parts, including injection molded, blow molded and extruded scrap; film and sheet; and automotive moldings, ducts and components. With many optional features and two configurations for the precision-tolerance cutting chamber, the granulators can be tailored to handle products of different densities, wall thicknesses and sizes. Cumberland offers abrasion-resistant packages for high-wear applications and a water-cooled rotor option that limits heat generation. The granulators feature an intelligent control system with a 7-inch, intuitive color touch screen for easy operation. Network connectivity provides remote access to the machines. Throughputs range from about 1,500 pounds per hour to 2,500 pounds per hour.
What’s new? The line of granulators, which debuted in July.
Benefits: Versatility, high-quality regrind and an easy-access design that saves energy and simplifies maintenance. Bed-knife maintenance is easier because operators no longer need to hold the bed knife and the shield at the same time. Additionally, each granulator door has safety features that ensure the rotor is stopped before the door can be opened. The cutting chamber and hopper suppress noise.

Padlock promises extreme durability
HD Type P padlock: Designed for use in harsh environments like recycling facilities, the HD Type P padlock can be integrated into lockout/tagout procedures within a trapped-key, interlocking safety system. It is constructed of heavy-duty 316 steel with a 304 stainless-steel shackle, while the dowel pin key and cylinder are made from 316 stainless steel. As an option, companies can have an alphanumeric code of up to five characters stamped onto the lock and key for easy identification.
What’s new? The padlock, which was introduced in June.
Benefits: Extreme durability. The heavy-duty construction and materials make the HD Type P suitable for extreme industrial settings, and the key is gasketed to keep dust and debris out.

Shredder now available in more robust version
Heavy-Duty Modular Split-A-Part: This line of shredders from Republic Machine comes in 100-horsepower to 300-horsepower models, with rotor diameters of 15 inches and 20 inches and four cutting widths ranging from 42 inches to 72 inches. It features an overtorque limiting clutch assembly and offers easy access for cleaning and maintenance. Additionally, shredders in this line are equipped with a single-piece solid forged rotor and an adjustable anvil for maintaining tight gap tolerances. They also include bolt-in replaceable tool holders and reversible counter knives that can be resharpened.
What’s new? An even heavier-duty, 300-horsepower version, designed for a recycler that handles especially contaminated materials, including bags, baled film and strapping. To create the more robust shredder, which began shipping earlier this year, Republic Machine says it redesigned its 20-inch rotor and beefed up the company’s patented Zoidal cutting system, which is shown at right, using a unique metallurgy for the larger blades and holder.
Benefits: Greater toughness. The custom 300-horsepower Heavy-Duty Modular Split-A-Part machine has been built to withstand damage from repeated contact with metal contaminants.

Grate-style magnet screens out contamination
DSC: Eriez’s new grate-style magnet can be used by plastics recyclers and processors of fine pellets or composite materials to screen out contamination. The screen features the company’s powerful RE7 magnet circuit.
What’s new? The DSC grate magnet.
Benefits: Dust-free separation of metal contaminants. Designed for sanitary operations, the grate is sealed from spillage or leaks. It is easy to clean, and a manual cleaning unit is available; the unit can be converted to an automated system with simple hand tools and a bolt-on kit.

Metals separator targets fine nonferrous metals
EddyC Fines: Steinert’s new metals separator is specially designed to recover fine nonferrous metals, such as aluminum, copper and brass. It can be used by recyclers to perform many tasks, including processing scrapped vehicles and for PET flake recovery. Three sizes of machines are available: 3.3 feet, 4.9 feet and 6.7 feet. The machine combines tried and tested Steinert features, such as the eccentric magnetic pole drum and high-frequency pole changes, with specially developed features for the fine-grain segment, according to the manufacturer.
What’s new? The design, which features a self-supporting frame, lower height and modified edges for easier cleaning and maintenance. It also has a new splitter with precise and reliable settings for extremely fine materials.
Benefits: Efficient sorting. Operating at up to 4,000 revolutions per minute (rpm), the system can sort materials measuring 10 millimeters and smaller and achieve 20 to 30 percent greater outputs than 2,600-rpm separators. Two employees can change the machine’s belt with only a few tools and no lifting equipment in 10 minutes.

Shredders handle a range of materials
M&J FineShred 1550/3550: These new shredders from Metso Corp., Helsinki, can handle a wide range of applications and materials, whether baled, rolled or loose. The multiedged shaft is fitted with a patented knife system and is fed by a pusher that generates minimal heat and requires no water cooling. In the U.S., eFactor3 represents Metso.
What’s new? The shredders, which take advantage of a new service hatch to improve access to the shaft and knives. To increase cycle times, the machines’ hydraulic pushers have been updated with a sickle shape.
Benefits: Uniform shredding, resulting in very small pieces. Changes in the shredders’ design allow easier maintenance, with access to both sides of the rotor. Also, the shredder is designed so that the knives and knife holders are easy to fasten and change.
Get curated news on YOUR industry.
Enter your email to receive our newsletters.
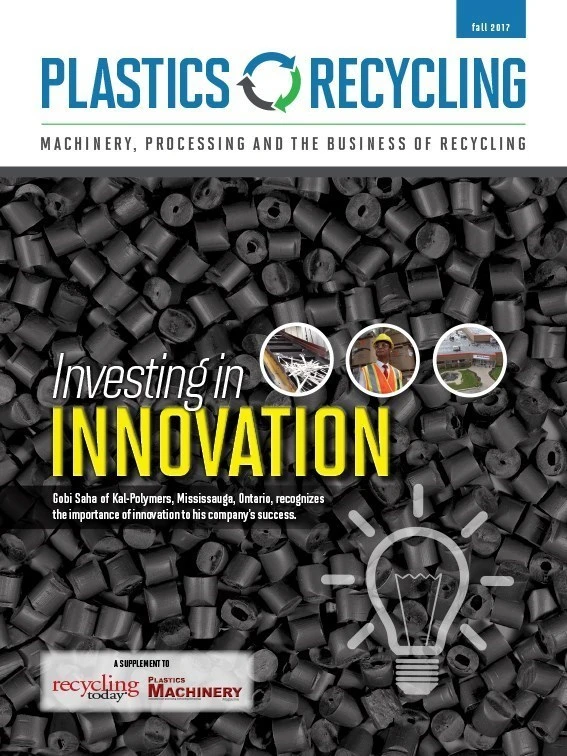
Explore the October 2017 Plastics Recycling Issue
Check out more from this issue and find your next story to read.
Latest from Recycling Today
- AF&PA report shows decrease in packaging paper shipments
- GreenMantra names new CEO
- Agilyx says Styrenyx technology reduces carbon footprint in styrene production
- SABIC’s Trucircle PE used for greenhouse roofing
- Hydro to add wire rod casthouse in Norway
- Hindalco to invest in copper, aluminum business in India
- Recycled steel price crosses $500 per ton threshold
- Smithers report looks at PCR plastic’s near-term prospects