
NGR extruders allow gentle, optimal melting
C:Gran: Particularly suited for moist materials with low bulk density, this series of cutter-compactor-extruders from Next Generation Recycling Machines (NGR) can be used in the recycling of flakes, films or regrind. Shredding, homogenization and drying and heating take place in the cutter bin, and specially arranged feeders provide additional compaction. Centrifugal force and the feeders convey the prepared material to the extruder screw. The C:Gran models come in a variety of sizes and styles, with hourly throughputs ranging from 1,210 pounds to 6,610 pounds. Depending on the application, the machines can be equipped with a wide range of melt filters, such as continuous filters, piston filters or backflush filters, as well as other add-ons, such as a variety of degassing or venting options, a roll feeder or conveyor unit.
What’s new? Numerous updates since the C:Gran debuted in 2012. This year, NGR has added to the portfolio, bringing the total number of models to eight. The machines feature a new auto-pilot control system that automatically adjusts the cutter-compactor, extruder and pelletizing speeds. They also have a shorter processing unit with the option of adding a second filtration stage as needed. For customers that need enhanced drying or degassing performance, the machines can be specified with a new dry-boost feature or Cascade option with a power venting section.
Benefits: The ability to handle moist material, with water content of up to 12 percent, thanks to the heating of the plastic in the cutter bin. When combined with a twin-screw extruder, the system performs recycling and compounding functionalities in one step. The systems’ extruder screw technology allows gentle, optimal melting even at high throughput rates, and the machines produce pellets of a uniform size well-suited for subsequent extrusion and consumer uses. The auto-pilot system guarantees reliability, process stability, quality and efficiency.
Next Generation Recycling Machines Inc., Atlanta, 678-720-9861, https://ngr-world.com
Erema laser filter systems reduce melt loss
sales manager, presented the
DischargePro system at NPE2024.
DischargePro: Erema’s laser filter systems use two parallel laser-drilled screen discs to separate contaminants from the melt stream of postconsumer recycled material.
What’s new? The DischargePro control, which Erema displayed at NPE2024. The controls automatically compensate for fluctuations in the input material, adjusting the speed of the scraper disc and the discharge screw according to demand.
Benefits: Reduced melt loss. Erema says DischargePro has made it possible to achieve up to 50 percent lower melt losses than the company’s previous laser filter control system. DischargePro takes into account the ongoing condition of the filter screen, reacting to pressure drops resulting from higher-viscosity melt by automatically adjusting the setpoint value to ensure a consistent discharge rate. The higher level of automation cuts the need for operator readjustment of the filter, providing greater efficiency and more stable processes.
Erema North America Inc., Ipswich, Massachusetts, 978-356-3771, www.erema.com
Weima drainage presses produce drier material
C.200 and C.200 Duo: These Weima drainage presses remove moisture from a wide range of shredded and chipped materials, including plastic rejects and fines. Depending on the material, a compression ratio of 10-to-1 is possible. Residual moisture in the dewatered material is about 3 percent. The machines are delivered ready to be plugged in and operate. The C.200 press can handle up to 2.6 cubic yards per hour, while throughput for the C.200 Duo is 5.2 cubic yards per hour.
What’s new? The line of drainage presses. On both, output material is pressed into discs with a diameter of about 7.9 inches.
Benefits: The generation of drier material that is easier to recycle or less expensive to haul away, improving recycling efficiency and reducing environmental impact. The built-in PLC, or programmable logic controller, connects the presses to a processing machine so they run only when material is input. The presses work with a hydraulic ram instead of an auger or other moving parts, which eliminates jamming. Height-adjusting feet help to integrate the presses, which can fit under all standard conveyors, into processing lines.
Weima America Inc., Fort Mill, South Carolina, 803-802-7170, www.weima.com/us

Maag gear pump accurately transfers, doses fluids
Chem-X: This Maag gear pump features an advanced gear-tooth design, optimized for minimal hydraulic pulsation and maximum volumetric efficiency. It can be used with compressors, along with other machines, in applications in which plastics and other materials are recycled.
What’s new? The pump, the first released jointly by Maag and Witte after Maag acquired Witte last year. Maag displayed the pump this summer at Achema in Frankfurt, Germany.
Benefits: Accurate transfer and dosing of fluids. The efficient and reliable pump can withstand harsh chemicals and temperatures as high as 752 F without compromising its life span or performance. It can handle materials with a very wide viscosity window under pressures of up to about 5,802 pounds per square inch. It can be set up with an intelligent control system, enabling real-time monitoring and adjustments and ensuring the pump operates at peak efficiency under varying process conditions.
Maag Reduction Inc., Charlotte, North Carolina, 704-716-9000, www.maag.com
Lindner presents 2-rotor friction washer
Twister Duo: This two-rotor friction washer from Lindner is designed to clean highly contaminated plastics. The company says it can remove the finest particles of dirt. Equipped with two rotors and a 100-horsepower drive, it has a throughput of up to 5,000 pounds per hour of PE film.
Sponsored Content
Labor that Works
With 25 years of experience, Leadpoint delivers cost-effective workforce solutions tailored to your needs. We handle the recruiting, hiring, training, and onboarding to deliver stable, productive, and safety-focused teams. Our commitment to safety and quality ensures peace of mind with a reliable workforce that helps you achieve your goals.
What’s new? The Twister Duo. It is believed to be the only two-rotor friction washer available.
Benefits: Rotors are 27 inches in diameter and can be configured for different materials. The large size allows the possibility to process higher amounts of material with higher efficiency of washed flake. Rotor paddles and screens are easily accessible for maintenance and changeover. The housing is made of stainless steel.
Lindner Washtech, Grossbottwar, Germany, 470-819-8281, www.lindner-washtech.com
Lindner Recyclingtech America, Statesville, North Carolina, 800-235-1391, www.lindner.com
Steinert sorting unit claims better purity, increased throughput
UniSort Finealyse: Steinert’s sorting unit is optimized for separating small particles from bulk materials. It consists of a feed and dispensing device with a material hopper, an acceleration conveyor belt, a discharge hood and a compressed air-nozzle bar. It is equipped with a high-resolution and highly selective color detection unit.
What’s new?An improved, higher-resolution system, the UniSort Finealyse+, specifically for processing plastic flakes, electronic scrap and metal fines between 4 millimeters and 30 millimeters. It features high-resolution near-infrared sensor and color camera technologies, automatic white balance and a high-speed conveyor belt. With its Active Object Control, the system can identify materials, as air from air nozzles pushes out rejects.
Benefits: Even better product purity and increased throughput. UniSort Finealyse+ reliably removes incorrect colors and unwanted plastics from plastic flakes. It also is well-suited to color sorting of nonferrous metals in addition to removing unwanted plastics from electronic scrap. With the new system, additional product characteristics can be identified and mapped at the same point, ensuring even more stable detection. The system is capable of split functions, so it can sort multiple material flows or sort and clean products simultaneously.
Steinert US Inc., Walton, Kentucky, 800-595-4014, https://steinertglobal.com
Get curated news on YOUR industry.
Enter your email to receive our newsletters.
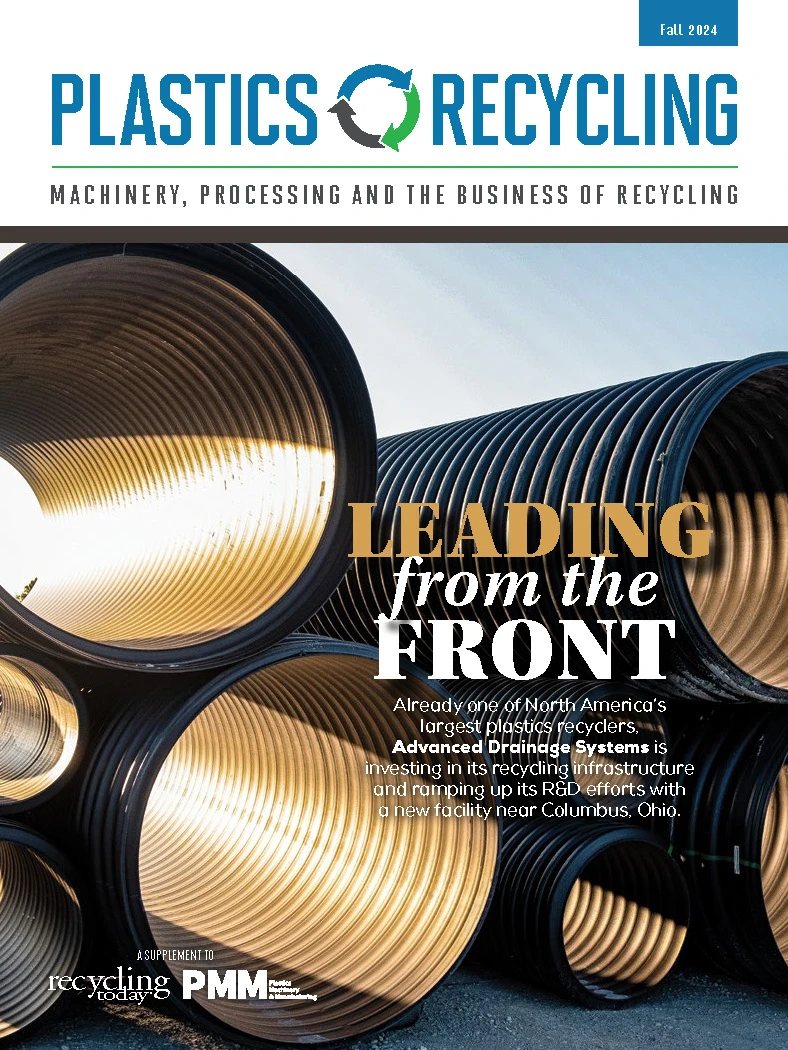
Explore the Fall 2024 Plastics Recycling Issue
Check out more from this issue and find your next story to read.
Latest from Recycling Today
- ReMA opposes European efforts seeking export restrictions for recyclables
- Fresh Perspective: Raj Bagaria
- Saica announces plans for second US site
- Update: Novelis produces first aluminum coil made fully from recycled end-of-life automotive scrap
- Aimplas doubles online course offerings
- Radius to be acquired by Toyota subsidiary
- Algoma EAF to start in April
- Erema sees strong demand for high-volume PET systems