
Continuous screen changer handles a range of recycled resins
DP-XL: High-Technology Corp.’s updated continuous screen changer can be used by compounders of a wide range of recycled resins. The pressure from the extruder head moves the filter screen, so no external driving mechanism is required to advance it. Screen sizes range from 2 inches to 8 inches and are available in 60-foot and 120-foot lengths.
What’s new? Various upgrades, including changes to the control algorithm to more precisely regulate the unit’s heating and cooling cycles, and the use of a higher-tensile-strength filter media.
Benefits: Improvements in a range of capabilities. The filter screen can advance at twice the speed of earlier models, allowing filtration of more highly contaminated melt. The new design is leakproof at temperatures as high as 650 degrees Fahrenheit, and the stronger filter media operates reliably at a constant differential processing pressure up to 2,000 pounds per square inch. The screen changer’s color touch-screen PLC can monitor conditions in real time and adjust the filter screen’s advance to allow for continuous production in response to changing contamination levels.

Software integrates business management and inventory functions
cieTrade.net: The cloud-based software-as-a- service (SaaS) version of cieTrade’s software integrates business management and inventory functions for commercial recycling companies. Users can track their materials in bulk, serially or a combination of the two, keeping tabs on truckloads of scrap plastic as they are sorted or converted into distinct products, such as regrind, pellets and waste, for example. Customers can pay for the software on a per-month basis, and no contract is required.
What’s new? Numerous features, including an app that lets users upload container or material photos and attach them directly to documents in a virtual file. Users also can create recurring invoices that are sent to customers on a monthly or quarterly basis. The software even includes a module for sales prospecting and customer relationship management.
Benefits: Efficient materials tracking. Users can trace a material’s genealogy through each step in the conversion process, all the way back to its original acquisition. The software also saves time and avoids double-entry by eliminating the need for spreadsheets. Also, it can be used anywhere with an internet connection.

Electrostatic separators promise efficiency
EKS: This line of electrostatic separators from Hamos GmbH, Penzberg, Germany, is used to separate mixed plastics, including different types of black polymers and plastics from scrap electronics and cable. In the first step, mixed plastics in a loading unit are electrically charged via the triboelectric method, taking on different charges depending on their type. A vibrating conveyor feeds the mixture toward a high-voltage field that either attracts or pushes the particles away, depending on their charges. The fully automated systems can handle scrap sized from 2 millimeters to 10 millimeters.
What’s new? Availability in the U.S. through exclusive distributor eFactor3.
Benefits: Efficient separation, low processing costs and product purity of greater than 98 percent. Also, the machines are energy efficient and offer flexibility—one piece of equipment can be adapted to handle many different mixtures of plastics.

Pelletron introduces HR45 deduster
HR45: Designed for various environments, including plastics recycling facilities, this Pelletron deduster features patent pending half-round cone technology. With material of average bulk density, such as polyethylene, polyethylene terephthalate, polycarbonate, polymethyl methacrylate and polyamide, it can handle up to 10,000 pounds per hour of pellets or regrind.
What’s new? The deduster, which Pelletron planned to show this month in Orlando, Florida, at NPE2018, the largest trade show for the plastics industry in the U.S. It replaces Pelletron’s XP45 deduster.
Benefits: Power-consumption reduction, lowered equipment costs and high-efficiency cleaning performance. Compared with the XP45, the compact HR45 uses smaller filters and 40 percent less energy. It’s also smaller and employs an automatic inlet flow-control feature that eliminates the need for a rotary valve to control flow rates.

Gneuss upgrades screen-changer line
SFXmagnus: Gneuss has upgraded its SFXmagnus line of fully automatic, pressure-constant screen changers. The devices are especially suited for filtering contaminated recycled plastics, such as polyvinyl chloride, polyethylene and polyethylene terephthalate. The series is characterized by an extra-large active screen surface area and compact design. Also, the machines are designed so production need not halt to replace filter screens. An SFXmagnus 60 is shown.
What’s new? Newly redesigned Allen-Bradley-based controls specifically developed as an option for the North American market, where the brand may be more familiar to users than Siemens controls, which are standard.
Benefits: Production of high-quality recycled resins and more controller options.
_fmt.png)
Tomra sorters use laser and NIR sensors
Autosort Laser: Tomra has two versions of a sorting machine that uses laser and near-infrared (NIR) sensors to detect more material types at the same point simultaneously. Sorting through input materials as small as 8 millimeters, the machines can differentiate between glass and transparent polymers while also separating ceramics, stones and metals from household and commercial waste. The machines are available in two sizes, with electromagnetic sensors as an option.
What’s new? Simultaneous single-point detection, which allows for more efficient detection and sorting of material fractions.
Benefits: Reduced weight sent to landfill and added revenue from reclaimed valuable products. The Autosort Laser’s NIR sensors allow a resolution of within 2 millimeters, and the machines are capable of handling as much as 9 tons per hour. Its compact footprint allows for easy integration.

Eriez system combines magnetic separation and metal detection
Magnetic B Trap/Xtreme Liquid Line: Eriez has expanded its line of Double Team magnetic separator/metal detector systems to prevent metal contamination. The newest system, for use with liquids, including colorants or other additives for plastics, combines a Magnetic B Trap separator with an Xtreme Liquid Line metal detector. The magnet removes ferrous contamination from the liquid, and the downstream metal detector removes nonmagnetic tramp metals, such as aluminum and stainless steel.
What’s new? The system, which debuted at Pack Expo in September 2017 in Las Vegas.
Benefits: Higher product quality and reduced costs. In addition to preventing metal from contaminating the final product, the Double Team system reduces waste and saves money because the magnet removes contaminants before the material reaches the metal detector, which automatically rejects some good product as it removes the contaminants.

Conair granulators feature larger screens
Granulators: Conair’s newest granulators—a portfolio of size reducers in a variety of configurations with rotor diameters of 6, 8, 12, 17 and 23 inches (shown)—boast bigger screens than the company’s previous offerings. Capable of tackling a variety of materials, the portfolio includes everything from press-side units to large central granulators. The biggest models, which are equipped with cooling channels to prevent overheating that could cause smearing or meltdowns, can take on large and bulky scrap. Throughputs range from 80 pounds per hour to 3,800 pounds per hour. Three-blade open rotors are standard for the line, but other rotor designs are available.
What’s new? The granulators, which Conair planned to show in May at NPE2018. A number of different infeed and evacuation configurations is available with each of the five rotor sizes, bringing to 14 the total number of new granulators available.
Benefits: Improved throughputs and ease of use. With screen areas equal to 50 percent of the rotor-diameter size, the granulators handle more scrap than earlier Conair models. The bigger screen areas also result in more consistent regrind with fewer fines. The models have been designed for quiet, efficient operation and long running life, as well as for easy knife changes and simplified maintenance.

Strautmann expands vertical baler line
PP 1208 and PP 1208 Plus 70: German equipment manufacturer Strautmann Umwelttechnik GmbH is marketing its PP 1208 and PP 1208 Plus 70 vertical baler models as ideal for handling recyclables, including plastic film and foam and polyethylene terephthalate. The vertical balers offer a pressing force that ranges from 3.3 to 77.2 tons, and their small footprint allows them to be used almost anywhere, the manufacturer says.
What’s new? Strautmann balers are now distributed in the U.S. by Unlimited Recycling Resources LLC (URR).
Benefits: Economical and energy-efficient operation. The QuickDoor, a swing/sliding door that pushes material into the press chamber, helps to ensure safe operation, while the machines’ CircleSystem is designed to reduce re-expansion of the compacted material for more efficient bale handling.
_fmt.png)
Visual inspection system monitors quality
Max-AI VIS: This visual inspection system from Bulk Handling Systems can be used to verify the quality of end products or to monitor the quantity of recyclables in a recycling facility as they leave the system. While it doesn’t sort materials, Max-AI VIS monitors material composition and quantity. An embedded software package, called the Total Intelligence Platform, tracks the entire process, recording information about material, uptime and downtime and motor amperage, as well as external data, such as inbound and outbound weights and bales on hand.
What’s new? Max-AI VIS and the Total Intelligence Platform, which BHS announced last month.
Benefits: Cost-effective, real-time material identification, as well as access to real-time performance data in an easy-to-use format.
Get curated news on YOUR industry.
Enter your email to receive our newsletters.
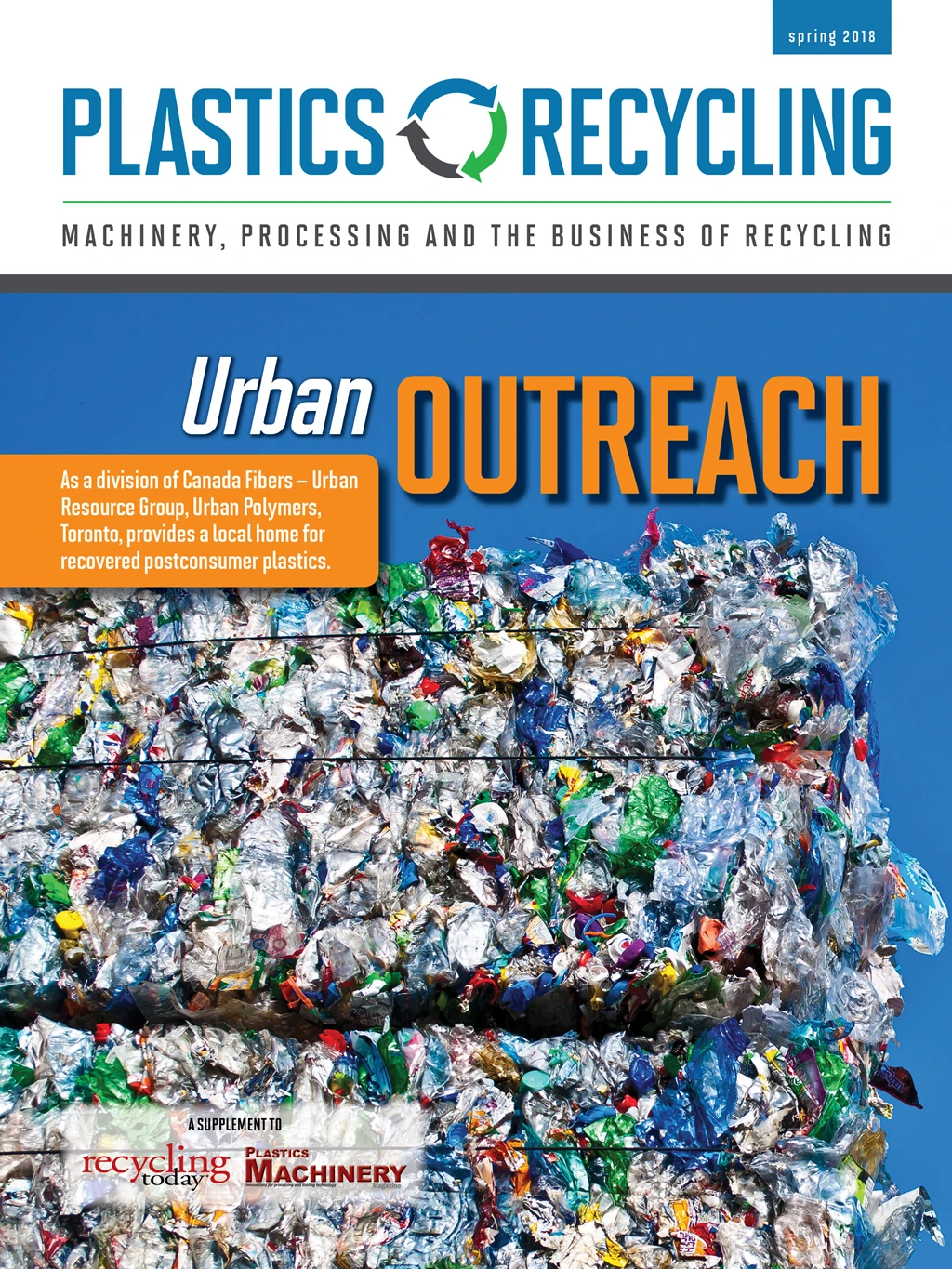
Explore the May 2018 Plastics Recycling Issue
Check out more from this issue and find your next story to read.
Latest from Recycling Today
- GFL opens new MRF in Edmonton, Alberta
- MTM Critical Metals secures supply agreement with Dynamic Lifecycle Innovations
- McClung-Logan Equipment Company joins Tana’s authorized dealer network
- Grede to close Alabama foundry
- Plastics Recycling Conference 2025: Working toward their targets
- SWACO rolls out new commercial recycling and food waste programming
- Updated: Matalco to close Canton, Ohio, plant
- Metso launches electric Anode Weighing and Casting Machine