
Shredder offers low-maintenance design
LSZ 150/100: Arranged in pairs one above the other, the four hardened tool-steel rollers of this Hellweg Maschinenbau shredder provide a working width of about 5.9 inches. They reliably feed even heavily profiled, thermoformed edge trim pieces and shred them in a single step. They require no resharpening, and the shredder needs no blade, screen or infeed device. Edge strips processed by the shredder can be added directly to virgin material.
What’s new? The revamped shredder, which is designed to require little maintenance.
Benefits: The reliable, continuous feeding and shredding of edge strips from trimmed film webs. Such strips are difficult to grip and convey using granulators with conventional feed and chop configurations, but the LSZ 150/100 overcomes these challenges. Boasting an infinitely variable roller speed, the shredder can handle infeed speeds ranging between about 2.6 feet per minute and 19.7 feet per minute. It can produce uniform regrind with an edge length of around 5 millimeters to 10 millimeters.
Hellweg Maschinenbau GmbH & Co. KG, Roetgen, Germany, 49-2471-4254, www.hellweg-granulators.com/en

Pyrolysis system offers flexibility, efficiency
Pyrolysis system: Compounder manufacturer Farrel Pomini and waste-conversion technology manufacturer Lummus Technology have combined technologies to develop a pyrolysis process for end-of-life plastics. As part of the process, Farrel Pomini’s FCM (Farrel Continuous Mixer, shown at right), with features tailored for pyrolysis, melts postindustrial and postconsumer scrap and homogenizes the material under specific temperature and pressure parameters. Pyrolysis then converts the material into gas, oil and pitch; these end products can be further processed in traditional refining and petrochemical assets and turned into monomers for new plastics production. The system also includes a cracker.
What’s new? The pyrolysis process, which Farrel Pomini announced in November of last year.
Benefits: A flexible, efficient and cost-effective way to transform low-bulk-density and contaminated materials into usable products. The continuous process is designed to ensure high-quality pyrolysis using the widest range of postuse feedstocks.
Lummus Technology, Houston, 832-878-5306, Ronald.Herbanek@lummustech.com,
Photos courtesy of Biunting
Drawer magnets updated for seamless compatibility
FF series: Bunting’s FF series of drawer magnets can be used with injection molding machines or extruders to remove ferrous contaminants from resin before processing. The magnets are installed above the opening of the processing machine. Resin passes through the drawers to remove metal, producing a higher-quality end product and protecting the machine from damage that can be caused by tramp metal.
What’s new? Updates to the drawer magnet, which was introduced several years ago. To cut lead times and customer costs, Bunting has standardized its line from six models to just two: High and Low Temperature. A key feature of the new drawer is its universal slotted flange, ensuring seamless compatibility with any square bolt pattern.
Benefits: Greater flexibility and efficiency. The updated design of the FF magnet drawer fits more machines, eliminating the need for customizations, which saves time and costs.
Bunting, Newton, Kansas, 316-284-2020, www.buntingmagnetics.com

Compatibilizer masterbatch increases interfacial adhesion between polymers
Maxiloop HP7AB4780COM: This Gabriel-Chemie compatibilizer masterbatch can be used in recycling applications involving postconsumer and postindustrial multilayer scrap materials or edge trims comprising polyolefins, such as PE and PP; polyamide 6; ethylene vinyl alcohol; or PET.
What’s new? The compatibilizer masterbatch, which increases the interfacial adhesion between different polymers, acting as a molecular bridge and ensuring better dispersion of polymer components during processing.
Benefits: Easier processing of recycled multilayer materials. By using the masterbatch, recyclers can produce resins that cause fewer extrusion errors and exhibit enhanced miscibility and improved mechanical properties when used in extruded films. In blown film production, in particular, fluctuations and instabilities in the bubble can be reduced, improving product quality.
Gabriel-Chemie GmbH, Gumpoldskirchen, Austria, www.gabriel-chemie.com

Erema introduces its largest recycling system for polyolefin regrind
Intarema 2325 T-VEplus RegrindPro: With versions capable of handling both film and bottles, this Erema recycling system can process a wide array of materials, including hard-to-process plastics, such as regrind. It is equipped with a laser filter, a 7.5-foot-long preconditioning unit (PCU) and a 9.8-inch-diameter extruder. The PCU cuts, homogenizes, heats, dries and precompacts the material. Next, the precompacted material fills the tangentially connected extruder. The machine’s Counter Current Technology ensures optimal material intake, process stability and high throughput across a wide temperature range. At the end of the plasticizing zone, a Quattro Laser Filter—at about 1,200 square inches, Erema’s largest filter—cleans the melt before it enters a three-stage degassing process. Throughputs vary by input material. For example, the machine can process between 7,054 pounds and 8,157 pounds of LDPE or LLDPE film in an hour; 5,732 pounds to 6,834 pounds of HDPE film; and 7,936 pounds to 8,818 pounds of PP film. Other materials it can process include HIPS, ABS and PC.
What’s new? The system, which Erema calls the largest ever built for polyolefin regrind. It sports a new 39-foot-long control panel array. With the recycling system’s introduction, the Intarema series now includes 13 sizes for film and nine sizes for regrind applications.
Benefits: The system enables the production of high-quality recycled polyolefin pellets with excellent mechanical properties suitable for end products with high recycled content. In relationship with its throughput, the system’s footprint is compact.
Erema North America Inc., Ipswich, Massachusetts, 978-471-2006, www.erema.com

MAS 110 increases throughput, productivity
MAS 110: This MAS extruder, developed with the assistance of artificial intelligence-supported simulations, is designed for use in recycling and upcycling operations.
What’s new? MAS introduced the MAS 110 in October of last year.
Benefits: A significant increase in throughput and productivity in recycling facilities. In the case of PET, it can process up to 6.6 tons per hour, yet it is compact. The total footprint is 25 feet by 6 feet. The plasticizing unit length is 10 ½ feet. It is suitable for all types of plastics and applications including bottle-to-bottle PET recycling and direct extrusion of films.
MAS America Inc., Charlotte, North Carolina, 704-904-0647, www.mas-austria.com
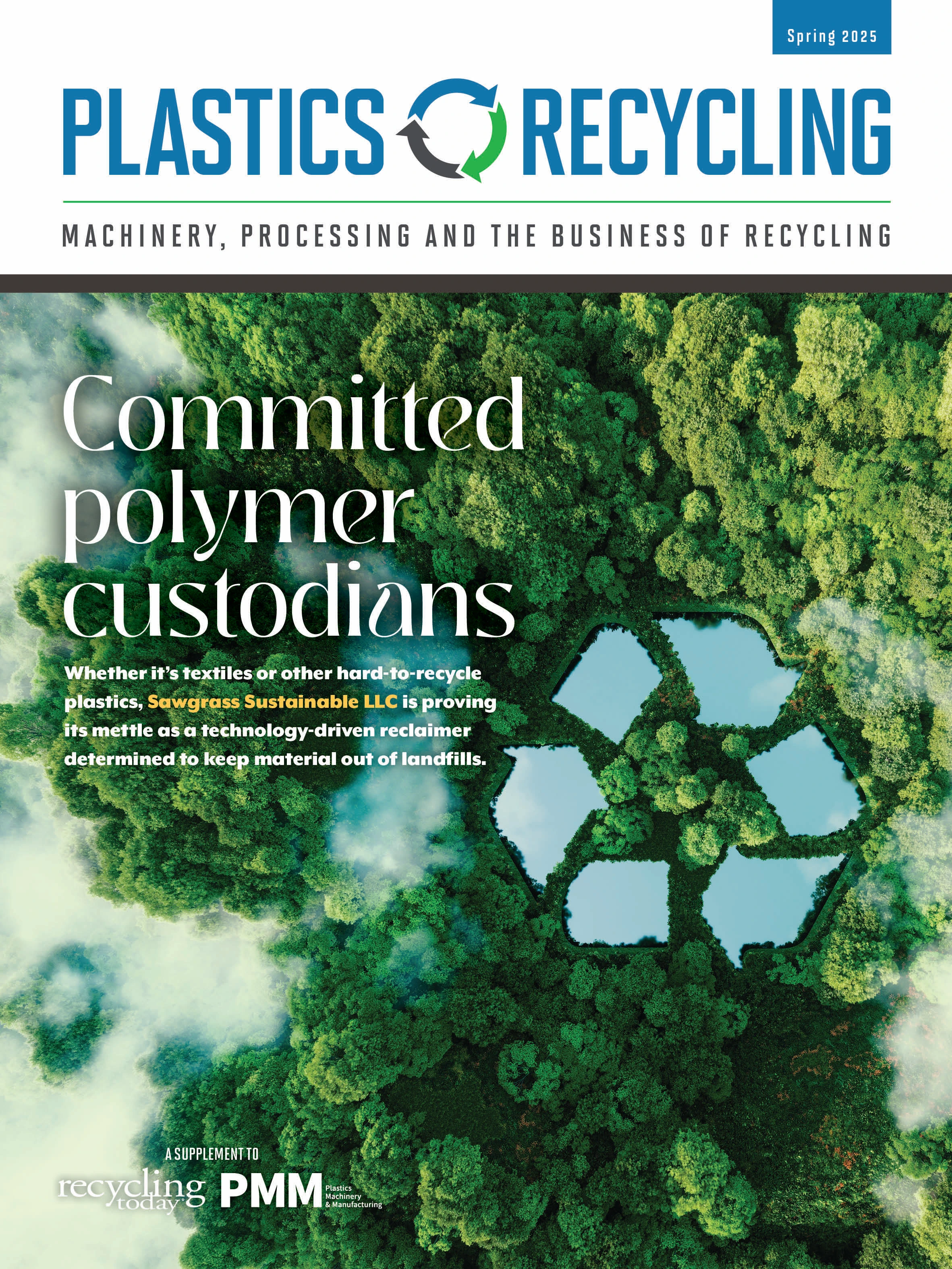
Explore the Spring 2025 Plastics Recycling Issue
Check out more from this issue and find your next story to read.
Latest from Recycling Today
- Lautenbach Recycling names business development manager
- Sebright Products partners with German waste management equipment company
- WasteExpo transitions to biennial format for enhanced experiences
- Study highlights progress, challenges in meeting PCR goals for packaging
- Washington legislature passes EPR bill
- PureCycle makes progress on use of PureFive resin in film trials
- New copper alloy achieves unprecedented high-temperature performance
- Gränges boosts profits and sales volume in Q1 2025