
Herbold Meckesheim adds features to plastcompactor
HV 70: Herbold Meckesheim’s most powerful plast-compactor can agglomerate even low-bulk-density materials into high-bulk-density recycling feedstocks. Its adjustable feeding screw continuously transports granulated material from the machine’s buffer silo into its working zone—which includes a rotating and fixed compactor disc—in a controlled manner. It can handle a range of materials, including thermoplastics such as fibers, fine particles, small tapes, foams, stretch or thin films, powders or shavings, as well as plastics that are difficult to convey, stock or mix. Special dosing units mounted above the feeding screw can be used to incorporate various additives such as lubricants, plasticizers or color pigments.
What’s new? Numerous changes, including a more compact design, new disc geometry and features that automate its operation. The machine has a fully automatic control system that can record settings for various feedstocks.
Benefits: Powerful, fast, versatile compaction with minimal thermal impact on feedstock, resulting in high throughput of feedstocks that offer advantages to processors. Changes to the plastcompactor’s silo and feeding device allow it to process even more complex materials, including materials with low bulk densities and difficult flow characteristics. Using the plastcompactor simplifies the processing of feedstocks, such as polyethylene terephthalate (PET). Once compacted, feedstocks run through the plastcompactor exhibit high bulk density and do not require special silos for storage. They can be easily discharged and conveyed—an advantage over flakes processed with conventional machinery. In addition, the agglomeration process partially crystallizes PET, making the recycled material easier to process in preform injection molding machines or film extruders with gravimetric dosing. Also, the energy consumption for extrusion is lower and the throughput of the extruder is higher. Wear costs of the plastcompactor are low, and the upgrades make the machine more reliable, requiring less manual intervention.
Herbold Meckesheim USA, North Smithfield, Rhode Island, 401-597-5500, www.herboldusa.com

Optional automatic cleaning system extends life of Gneuss vacuum equipment
Vacuum systems: Gneuss vacuum systems play a key role in the devolatilization process in recycling operations. Vacuums suck out monomers, oligomers and other solid particles or sublimates as they’re separated from volatiles, which are extracted from the melt. If the particles reach the pump, they can drastically reduce its operating life.
What’s new? An optional automatic cleaning system for Gneuss’ water-ring pump-based vacuum system and design upgrades that make it easier to maintain. The vacuum systems are offered mainly with Gneuss’ OmniMax systems for polyolefin applications and its OmniBoost systems for polyester applications. An OmniMax system is shown.
Benefits: Improved ease of maintenance and reliability. The systems are robust enough to handle tough recycling applications.
Gneuss Inc., Matthews, North Carolina, 704-841-7251, www.gneuss.com

Wittmann granulator is compact, versatile
S-Max Dual 6: Capable of chopping large sprues and parts, this screenless granulator from Wittmann has been designed for central scrap reclamation. It has two counter-rotating cutting rotors, six blades, eight toothed rollers and a stainless steel feeding chamber. An optional feeding shaft keeps large parts in motion and cuts them to size before sending them into the hopper, reducing the chance for material bridging or overflow. An optional automatic reversing system, which allows the rotor to reverse for better part positioning under heavy load, also is available. Featuring a cutting chamber of 20.8 inches by 18.4 inches, the S-Max Dual 6 can achieve a maximum throughput of 88 pounds per hour.
What’s new? The granulator, which offers improvements over Wittmann’s comparable Junior Double 6 (JD-6) granulator. Like the JD-6, it has two 2.2-kilowatt motors, but to save space, the units are installed vertically. Redesigns of the JD-4 and JD-8 will follow later this year.
Benefits: Compact size, safe operation and the ability to handle a variety of materials, including hard, brittle and glass-fiber-filled parts. The S-Max Dual 6 has been designed to minimize component wear and generation of dust, fines and noise, and it allows free access for maintenance and cleaning from the top.
Wittmann USA Inc., Torrington, Connecticut, 860-496-9603, www.wittmann-group.com/en/usa

Conair granulator control includes predictive maintenance
SG2 Smart Granulator control: Conair’s new optional SG2, designed for use with Conair Viper granulators, uses the company’s common control interface similar to the SG1 control, but the SG2 offers predictive maintenance capabilities. It will be available on the Viper 12-, 17- and 23-series granulators and features a 7-inch color touchscreen HMI.
What’s new? Incorporation of predictive maintenance capabilities for use with Conair Viper granulators.
Benefits: The SG2 control gathers performance data from sensors located throughout the granulator—rotor rpm, motor load/amperage, cutting chamber and screen temperatures and vibration levels. The control compares these data to established “good” data that reflect desired equipment performance. If live performance data diverge from the desirable range, the SG2 alerts operators. Alarms are triggered for situations that require immediate attention, such as low rpm or high amperage, which could indicate a material jam. On-screen reminders indicate upcoming maintenance needs, such as the need to change knives, lubricate bearings or replace a screen. When the SG2 is linked to SmartServices, Conair’s cloud-based Industry 4.0 platform for auxiliary monitoring, measurement and control, reminders can be sent to personnel about needed maintenance work. Conair’s common control interface incorporates the look and feel of other Conair auxiliary controls. The SG2 control adds power-cabinet wiring and connections that integrate easily with other equipment, such as shredders, conveyors, evacuation systems and other support equipment used in central bulk-fed or in-line size-reduction systems. These power cabinet features eliminate the need for custom hardwiring and support the smooth operation of sequential pieces of size-reduction equipment.
Conair Group, Cranberry Township, Pennsylvania, 724-584-5500, www.conairgroup.com

Sesotec Pre-Sort uses two-track system
Pre-Sort: This self-contained Sesotec technology for processing regrind from compounding operations combines sorting, dedusting, material conveying and central control. The compact technology is built upon a mobile base. It includes sensors for color, polymer and metal sorting and can perform sorting applications according to the color, shape or type of plastic and metal, or any combination of those attributes. For more thorough sorting, materials move along two tracks.
What’s new? The Pre-Sort, which made its debut last October at Fakuma. Sesotec plans to introduce the technology in the U.S. by the fourth quarter of this year.
Benefits: Efficiency and flexibility, as well as the efficient recapture of plastics that can be reused. With the flexibility to work with any combination of sensors and a selection of different sorting sequences, the two-track Pre-Sort sorts materials twice—first on one track, then on the second. This ensures the purity of plastics that can be reground. In addition to its sorting accuracy, the Pre-Sort offers flexibility and mobility as it can be transported from one location to another.
Sesotec Inc., Bartlett, Illinois, 224-208-1900, www.sesotec.com/emea/en

Untha upgrades RS shredder line
RS class shredders: Untha’s RS class of shredders can handle a wide range of materials, including plastic containers, bottles, packaging and white goods. The shredders feature a patented four-shaft cutting system that can be customized to the input material, and Untha’s Eco Power Drive stops the cutting shaft as soon as nonshreddable material is detected to prevent damage to the cutting system.
What’s new? An advanced generation of Untha’s RS class of shredders including models RS30, RS40, RS50, RS60 and RS100, two of which Untha displayed at IFAT 2024 in Munich. The new generation features a more solid torsion-resistant construction for added machine longevity, and an LED strip light displays the shredder’s operational status. Custom hopper colors also are available.
Benefits: Improved throughput and reduced clogging thanks to adaptations made to the cutting system symmetry. The electronics have been improved, and the enhanced touchscreen display has been redesigned with an intuitive interface that makes error diagnosis and resolution easier. The new RS shredders include an integrated quick-change screen system that makes screen changes 30 percent faster, while noise levels are 8 percent lower. Service and maintenance access also is easier, improving working conditions for operators while decreasing downtime.
Untha Shredding Technology America Inc., Hampton, New Hampshire, 603-601-2304, www.untha-america.com

PCUplus cleans pellets for use in food-contact packaging
PCUplus: Starlinger’s new downstream pellet flushing unit uses ozone-enhanced process air to flush pellets. It features an optimized air channel design that keeps temperatures within a narrow process window.
What’s new? The unit, which joins the South Carolina-based company’s portfolio of technologies for recycling postconsumer (PCR) polyethylene (PE), polypropylene (PP), polystyrene (PS) and polyethylene terephthalate. Starlinger exhibited the PCUplus at NPE2024: The Plastics Show in Orlando in May as part of a setup (pictured) with its recoStar Dynamic PCR pelletizing line and ViscoZero melt phase decontamination reactor.
Benefits: Effective cleaning and odor reduction. When used with the ViscoZero reactor, the PCUplus pellet flusher produces recycled PE, PP and PS that meets the highest standards for packaging used in direct food contact.
American Starlinger-Sahm Inc., Fountain Inn, South Carolina, 864-297-1900, www.starlingersahm.com

Maag filter technology automates cleaning
Duplex Filter System (DFS): This Maag filter technology, featuring two filter vessels per unit, employs the company’s Micronex candle filter elements to meet the filtration needs of recyclers dealing with a wide variety of polymer types, viscosities, throughputs and filtration levels.
What’s new? The introduction of the new-generation DFS-BF, which can perform an automated backflush cleaning of the filter candles during operation, as well as the use of Maag’s patented DivexPro switch-over valves. The solid valve housing is forged out of one piece, with flow channels drilled into it. It is equipped with an integrated heating cage and includes an integrated drain or vent valve. The valve is available with nominal bore sizes from 2 inches to 8 inches to meet any throughput rate. The DFS-BF joins the standard DFS, which uses only one vessel for filtration, while the other vessel is on standby. For the DFS-BF, a specialized version of the Micronex filter, the Micronex-BF, is available with a special outer guard to protect the pleating during both the filtering process and the backflush process.
Benefits: Cost savings. Duplex filters traditionally can be used for several weeks or months until the contamination builds to a critical level and the candle bundle or the complete vessel are exchanged. However, a growing set of chemical recycling applications bring extremely high contamination levels combined with demand for ultrafine filtration, making the traditional procedure costly. To address this issue, the backflow capability of the DFS-BF allows it to clean clogged candle bundles inside the filter vessel without interrupting the polymer flow, so the candle bundle can perform longer before it must be exchanged for external cleaning. Customers can choose whether the pistons of each valve size are activated with manual, electrical or hydraulic actuators. For chemical recycling applications with low viscosity and high contamination levels, the new generation DFS-BF can perform an automated backflush cleaning of the filter candles during operation.
Maag Reduction Inc., Charlotte, North Carolina, 704-716-9000, www.maag.com
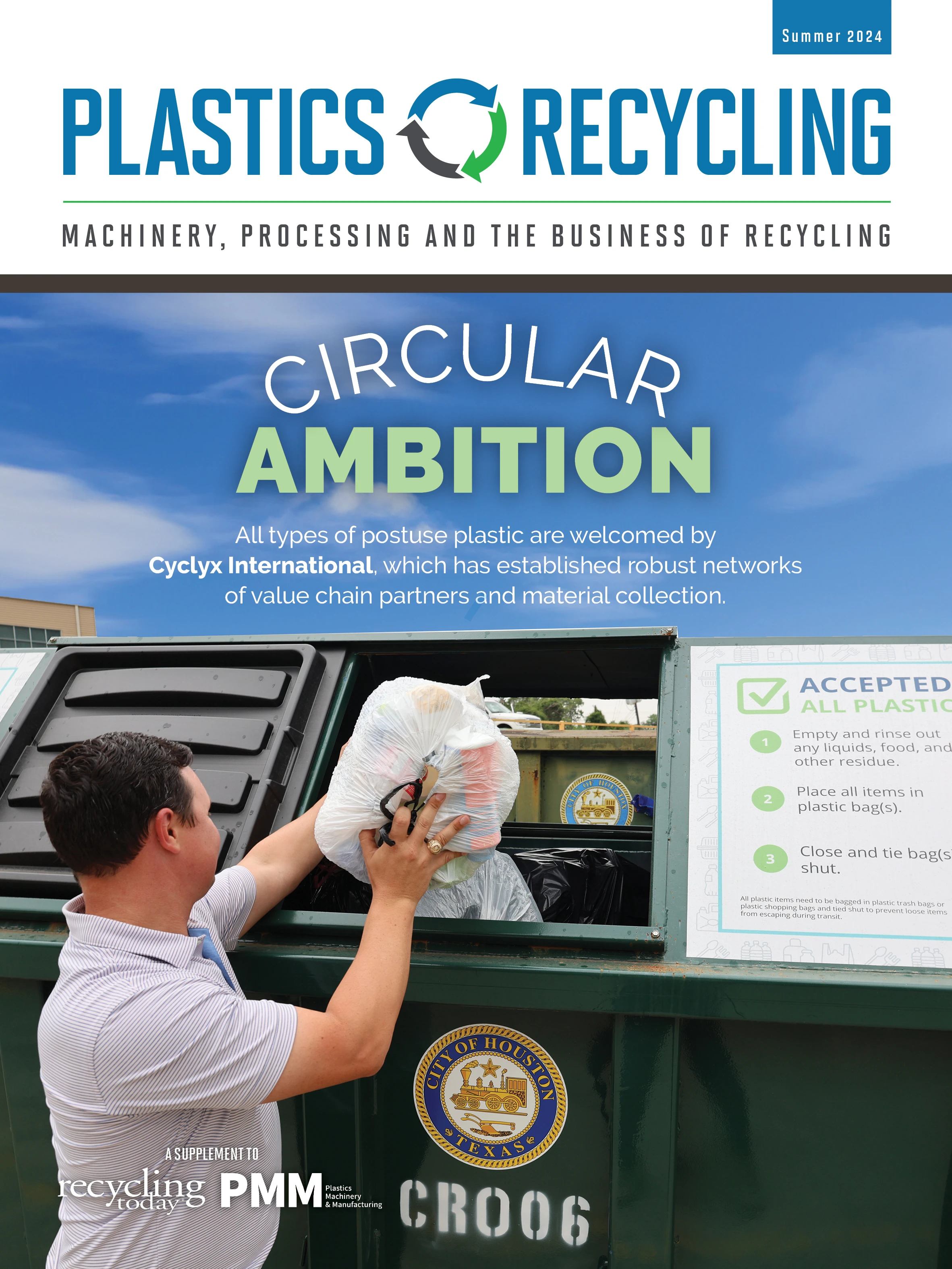
Explore the Summer 2024 Plastics Recycling Issue
Check out more from this issue and find your next story to read.
Latest from Recycling Today
- European project yields recycled-content ABS
- ICM to host co-located events in Shanghai
- Astera runs into NIMBY concerns in Colorado
- ReMA opposes European efforts seeking export restrictions for recyclables
- Fresh Perspective: Raj Bagaria
- Saica announces plans for second US site
- Update: Novelis produces first aluminum coil made fully from recycled end-of-life automotive scrap
- Aimplas doubles online course offerings