Upgrades increase shredder-extruder combination’s throughput by 25 percent

ISEC evo: This shredder-extruder combination from PureLoop GmbH, Ansfelden, Austria, features a single-shaft shredder and double-feed ram and is used to repelletize industrial scrap. It can handle a range of materials, including film, tape, nonwoven fabric and hollow or solid plastic parts. Four models are available; throughputs for processing LLDPE film without degassing range from about 400 pounds per hour to more than 1,600 pounds per hour. In the U.S., ReViV APT represents PureLoop.
What’s new? Numerous upgrades, which debuted in October at the K show, a major plastics industry trade show in Düsseldorf, Germany. The upgrades include an increase in drive power and the addition of a button to actuate the automatic start/stop of the system. The goal is to improve user friendliness and overall performance.
Benefits: The production of high-quality recycled resin pellets, greater flexibility and improved throughputs compared with the previous generation of the machines, then known simply as ISECs. The upgrades have boosted the machines’ throughput by 25 percent, while a new turnable hood provides more options in terms of setup.
Parallel-disc continuous disc filter from MAS Maschinen can boost extrusion line productivity

MAS CDF 500-D disc filter: MAS Maschinen und Anlagenbau Schulz GmbH, Pucking, Austria, has updated its parallel-disc continuous disc filter. It has a filter surface area of about 505 square inches and a maximum throughput exceeding 4,400 pounds per hour. In the U.S., eFactor3 represents MAS.
What’s new? Upgrades of the scraper and contamination-discharge systems, which debuted at the K show.
Benefits: Better ergonomics, thanks to the new design. The system can boost the productivity of extrusion lines in recycling applications, and screens can last as long as six months, depending on contamination levels. The system allows users to produce recycled materials with contamination levels under 5 percent.
Pelletizing system can process a wide range of polymers

PearloFlex pelletizer: Maag’s new underwater pelletizing system is specially made to process a wide range of polymers, including recycled plastics, into spherical pellets of compounds, masterbatches and blends. It encompasses a diverter valve, pelletizer, dryer, process water system and control cabinet, all mounted on one compact frame. The modular system can handle frequent product and color changes with a throughput of up to 1,100 pounds per hour.
What’s new? The pelletizer, which debuted at the K show.
Benefits: Flexibility and ease of use. The system features top-mounted, swiveling and movable machinery that makes changeovers and maintenance easy, with limited downtime.
Shredder preshreds contaminated postconsumer scrap

Micromat shredder: Micromat WS, Lindner’s newest Micromat shredder, is specially designed for preshredding contaminated postconsumer plastic scrap, such as lightweight packaging, bottles or films. In the preshredding process, the wet shredder uses a jet of water directed onto the rotor to detach dirt particles. A frequency converter controls the amount of water; six to eight integrated nozzles can spray between about 528 gallons and 7,925 gallons an hour directly onto the rotor. The water ensures uniform and controlled material discharge. Machines in the series have throughputs ranging from about 3,300 pounds an hour to more than 7,700 pounds an hour. They can be linked by conveyors to washers, dryers and other auxiliary equipment and used inline as part of a recycling operation producing either pellets or film.
What’s new? The shredders, which debuted at the K show.
Benefits: The production of uniform, shredded materials, which minimizes problems for downstream washing operations, at a low operating cost. To minimize possible damage due to foreign matter, they have been equipped with an adjustable slip clutch.
System allows recycling machinery to automatically adapt to plant conditions

S.M.A.R.T. Dialog: NGR’s machine monitoring and communication system provides what it calls Self-Monitoring Analysis + Reporting Technology (S.M.A.R.T.) capabilities. The system collects and uses data to allow machinery within a recycling line to automatically adapt to changing conditions. Data specific to various organizational functions, such as maintenance and quality control, are packaged and stored in the cloud so they are accessible to those who need them.
What’s new? The system, which NGR introduced at the K show as part of its demonstration of its PET recycling line, the P:REACT, pictured at left. It will be commercially available worldwide on all NGR machines by April.
Benefits: Greater access to machine data, which gives users the information they need to improve their production and maintenance practices. Data showing a wide range of parameters can be sent to mobile devices.
For instance, using S.M.A.R.T. Dialog, users have easy access to information about part-production and maintenance history, machine output, energy consumption and melt characteristics. S.M.A.R.T. Dialog also can transfer such data to enterprise resource planning systems, which can provide comparisons and calculations about operating costs, downtime and other issues.
ZeMac masterbatches offer improved resin properties, reduced material costs

ZeMac masterbatches: Vertellus has expanded its copolymer line with the addition of two new masterbatches for upgrading recycled polyamides (PA): ZeMac Extend L65 (shown below at left) for injection molding and Extend ZeMac L68 for film and profile extrusion and blow molding. It also has added ZeMac Extend P62, which can compatibilize PA and recycled PET. The additives can be used by compounders and converters to improve the qualities of recycled resins.
Resins made with the PA-targeted masterbatches can be used in under-the-hood automotive parts and oil and gas pipes, while resins containing ZeMac Extend P62 can be used in products including office furniture, sporting goods and hand tools.
All three additives can be used to complement ZeMac E60-P powder (shown below at far right).
What’s new? The masterbatches, which Vertellus debuted at the K show.
Benefits: Reduced material costs and improved resin properties. The PA-targeted masterbatches facilitate production of a shear-thinning material that costs less to process than conventional high-relative-viscosity PA. With them, the material also is stronger and more flexible and has a higher heat distortion temperature. ZeMac Extend P62 also contributes to greater flexibility.
Get curated news on YOUR industry.
Enter your email to receive our newsletters.
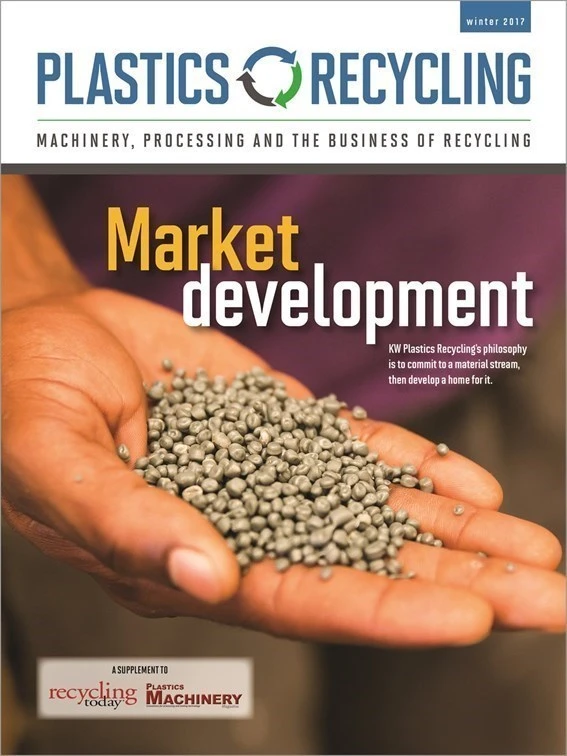
Explore the February 2017 Plastics Recycling Issue
Check out more from this issue and find your next story to read.
Latest from Recycling Today
- Toppoint Holdings expands chassis fleet
- Lego creates miniature tire recycling market
- Lux Research webinar examines chemical recycling timetables
- Plastics producer tracks pulse of wire recycling market
- Republic Services, Blue Polymers open Indianapolis recycling complex
- Altilium produces EV battery cells using recycled materials
- Brightmark enters subsidiaries of Indiana recycling facility into Chapter 11
- Freepoint Eco-Systems receives $50M loan for plastics recycling facility