
Separator offers efficient
removal of metals
Dynamic pulley separator: Eriez has added dynamic pulley separators to its extensive line of equipment for recycling. The separators employ a rare earth permanent magnet that rotates to create an agitating magnetic field that removes entrapped steel from recycled materials. A typical installation positions the dynamic pulley separator upstream from an eddy current separator, which then addresses nonferrous material in the stream.
What’s new? The dynamic pulley separators, which are available in 40-inch and 60-inch widths.
Benefits: Improved material purity and profitability. Efficient removal of metals eases the burden on downstream equipment, boosts the recycled plastic stream’s quality and prevents damage to downstream equipment. The separator also can be fitted with weakly magnetic drums to recover magnetic fines from the material stream.
Eriez Manufacturing Co., Erie, Pennsylvania, 814-835-6000, www.eriez.com

Westeria spreader
uses artificial intelligence
DiscSpreader Automove: This single-disc spreader from Westeria GmbH, Ostbevern, Germany, can be mounted directly on any infeed belt of a recycling sorting unit. The rotating disc helps spread out all kinds of recyclables across a conveyor belt, including plastics and other materials measuring from about 0.04 inch to 15.7 inches long, so they can be sorted more easily without vibratory technologies. Two cameras positioned behind the disc record the current material distribution on the belt; artificial intelligence (AI) uses this data to vary the position and alignment of the disc in real-time. In the U.S., eFactor3 distributes Westeria products.
What’s new? The use of AI to eliminate the need to manually readjust the presentation of materials on a conveyor.
Benefits: Optimal distribution of recyclables on the conveyor belt for sorting that’s more efficient than what’s provided by vibratory technologies. With the DiscSpreader Automove, users can achieve considerable increases in throughput and experience fewer disturbances in process flow. In addition to the sorting benefits it provides, the DiscSpreader Automove is compact.
eFactor3, Charlotte, North Carolina, 877-801-3232, www.westeria.de, www.efactor3.com

Coperion’s ZS-B Megafeed
boosts material throughput
ZS-B Megafeed: Recycling lightweight, high-volume fiber and flake materials can be a difficult task with low throughputs; in some cases, materials offer such low returns that they are considered not worth the effort of recycling. The latest feeder from Coperion is designed to address these problems.
What’s new? A new version of Coperion’s ZS-B side feeder, the ZS-B Megafeed. This new feeder reliably can feed much larger quantities of these lightweight materials into Coperion’s ZSK twin-screw extruders.
Benefits: More efficient production and the ability to process material previously not considered recyclable. For mechanical upcycling processes, flakes and fibers can be fed directly from the ZS-B Megafeed into a ZSK extruder, eliminating steps such as compacting, melting and agglomerating, which lowers investment and energy costs. Using the example of a ZSK 58 MC18 extruder, the company says a ZS-B Megafeed feeder can boost recycling throughputs of polyamide fibers from 154 pounds per hour to 2,204 pounds per hour. The ZS-B Megafeed can be retrofitted to existing Coperion extruders, greatly increasing their throughput rates.
Coperion K-Tron Salina Inc., Salina, Kansas, 785-825-1611, www.coperion.com

Terratek BD features
biodegradable material
Terratek BD: This Green Dot Bioplastics line of biodegradable materials can be used in film extrusion, thermoforming and injection molding to produce packaging and single-use products.
What’s new? The nine compostable resin grades in the line.
Benefits: Faster biodegradability in ambient composting conditions. The new offerings include five starch-blend film grades that can run on traditional blown or cast film equipment without tooling or process modifications to produce items such as bags, bubble wrap and agricultural films. They biodegrade in soil as well as in home composting and industrial composting processes. Three thermoforming grades are optimized for properties including clarity, higher heat performance and greater flexibility for applications such as food-service packaging and takeout containers. Finally, Green Dot Bioplastics has developed one resin grade for injection molding. It offers higher-heat performance and shorter cycle times for products such as caps, closures and take-out containers. Using this resin, the company also has worked with a customer to develop an injection-molded package with a living hinge capable of hundreds of flexural openings and closures, which it says has not been achieved previously with typical bioplastic resins.
Green Dot Bioplastics, Emporia, Kansas, 620-273-8919, www.greendotbioplastics.com
Improved +Zero additive
requires less for same results
+Zero: Riverdale Global’s +Zero additive helps plastics processors deal with the challenges posed by increased use of postconsumer resin (PCR). Parts made with PCR have different flow properties than those using virgin resins, which can slow mold release. +Zero prevents the buildup of static electric charges on the surface of plastic parts during processing and reduces surface tension on the parts to function as a mold release agent. This can result in 25 percent faster cycle times when compared with parts made with untreated PCR.
What’s new? A new formula, which can achieve the same results as the original formula while using 25 percent less of the additive.
Benefits: Cost savings. The new formula allows for the use of a higher percentage of recycled material—up to 100 percent regrind—as well as the use of lower-grade recycled material. Faster cycle times improve production, and the need for less additive means these improved results can be attained more cheaply.
Riverdale Global LLC, Aston, Pennsylvania, 610-358-2900, www.riverdaleglobal.com
_Sarlink__fmt.png)
New Sarlink TPV uses
25-percent-recycled content
Thermoplastic vulcanizates (TPVs): The TPVs in Teknor Apex’s Sarlink line often are chosen for use in making extruded seals and hoses or molded gaskets. They offer great elasticity and long-term performance and can be used to replace thermoset rubber, like ethylene pro-pylene diene rubber, in some cases. They can be overmolded or co-extruded with polypropylene or other thermoplastic elastomers.
What’s new? The incorporation of 25-percent-postindustrial-recycled content in the development of Sarlink R2 3180B TPV. The resin comes precolored black, and the company says its processing and performance are functionally equivalent to comparable virgin resins.
Benefits: Sustainability. This new TPV promotes a circular economy by incorporating recycled content and being fully recyclable at the end of the product’s life. The company says processing trials have proved that, even with the addition of recycled content, its Sarlink TPVs in general have faster cycle times or increased throughput rates when compared with competitive TPV products.
Teknor Apex, Pawtucket, Rhode Island, 401-725-8000, www.teknorapex.com

ThermProtect provides antioxidants to improve part aesthetics, functionality
ThermProtect: Ampacet’s ThermProtect range of products is part of a portfolio of masterbatches designed to support circular economy initiatives. The ThermProtect range contains a multifunctional stabilizer technology that carries a powerful antioxidant, making it appropriate for mixes that include significant amounts of postconsumer resin (PCR). PCR contaminants such as inks, fillers and catalyst residue can cause viscosity changes, black specks, gels and odors that degrade end-product mechanical properties and aesthetics. ThermProtect antioxidants are designed for polyethylene and polypropylene applications, including blow-molded packaging and products, industrial products such as garbage bags and construction products like composite lumber, crates and buckets.
What’s new? ThermProtect 1001145-N, which is used primarily for non-Food and Drug Administration (FDA) film applications, and ThermProtect 1001265-N, which meets FDA requirements.
Benefits: Improved aesthetics, processability and functionality. ThermProtect stabilizes polymers subjected to multiple heat histories and provides thermal stability at high temperatures. It employs specialty radical scavengers, which stop oxidation that can be caused by alkyl radicals, while its acid scavengers eliminate the degrading effects of inks and other contaminants.
Ampacet Corp., Tarrytown, New York, 914-631-6600, www.ampacet.com

Engel process simplifies
use of recycled materials
Two-stage process: The typical process of reusing postconsumer and postindustrial resin (PIR) includes steps for grinding, melting, filtering, degassing and pelletizing. Pellets are then introduced to an injection molding machine (IMM) to be again melted, then molded. At the K show, Engel planned to display a production cell with its new two-stage process using a legacy Engel duo 12060H/80Z/900 IMM with a modified injection unit to produce rolling dolly pallets from PIR. The machine separates the plasticizing and injection steps, with a screw dedicated to each of these steps. Flakes are fed into a first plasticizing screw, then the melt enters a melt filter and degassing unit before crossing through a transfer head to the injection screw. The modification of the IMM is not available as a retrofit.
What’s new? The degassing unit, which is incorporated in the IMM. Engel’s developers focused on this unit because a melt filter alone is not enough to completely remove residual moisture and volatile substances, which can cause surface defects and impair mechanical load-bearing capacity of finished parts.
Benefits: Lower energy use and a decreased carbon footprint. Engel calculates that by eliminating an intermediate pelletizing step, the two-stage process cuts energy requirements by 30 percent. The two-stage process also decreases carbon dioxide emission.
Engel Machinery Inc., York, Pennsylvania, 717-764-6818, www.engelglobal.com
Get curated news on YOUR industry.
Enter your email to receive our newsletters.
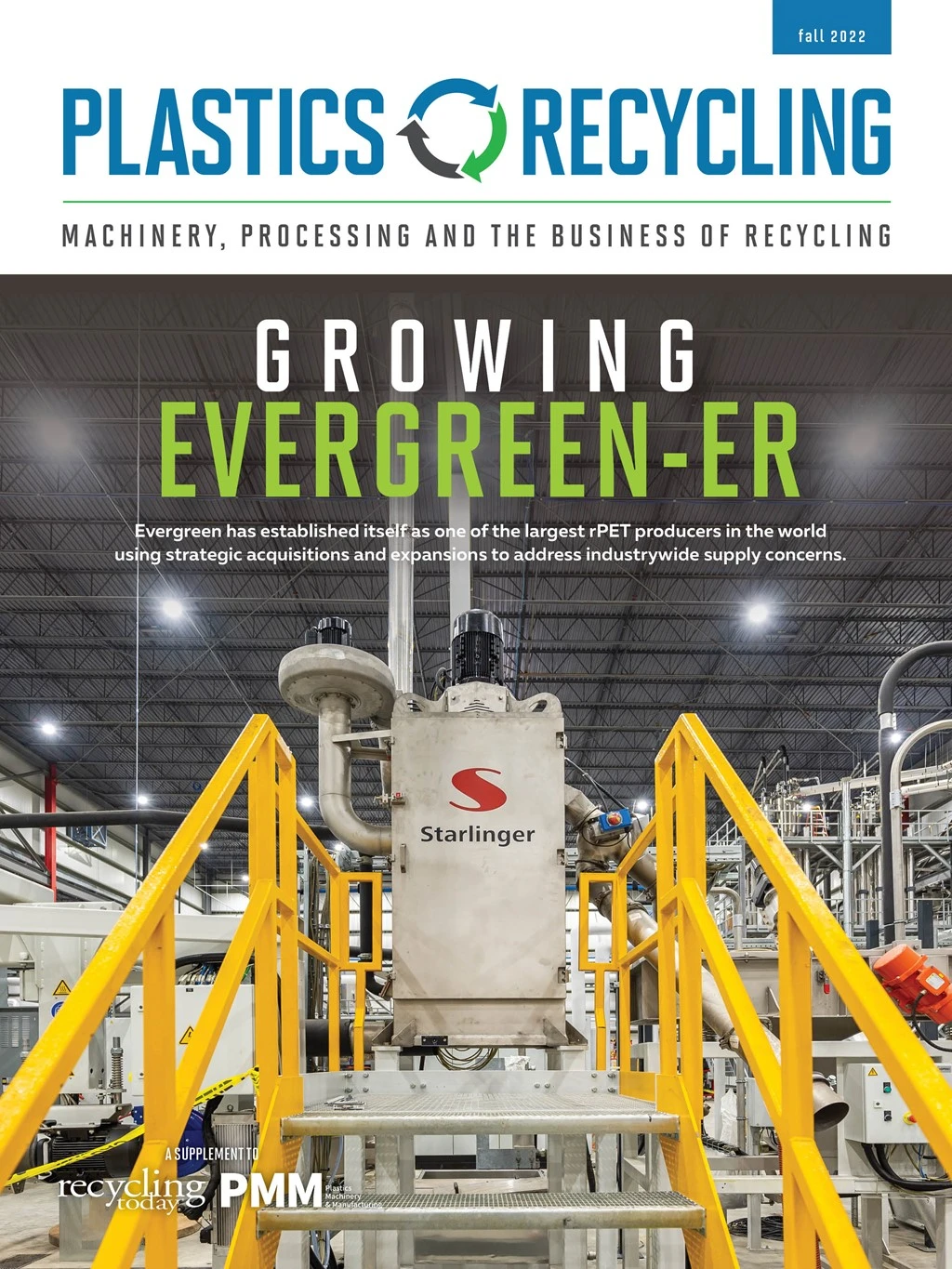
Explore the Fall 2022 Plastics Recycling Issue
Check out more from this issue and find your next story to read.
Latest from Recycling Today
- AF&PA report shows decrease in packaging paper shipments
- GreenMantra names new CEO
- Agilyx says Styrenyx technology reduces carbon footprint in styrene production
- SABIC’s Trucircle PE used for greenhouse roofing
- Hydro to add wire rod casthouse in Norway
- Hindalco to invest in copper, aluminum business in India
- Recycled steel price crosses $500 per ton threshold
- Smithers report looks at PCR plastic’s near-term prospects