
BASF expands additives line
IrgaCycle: BASF has kicked off a line of five new additives that improves the properties of mechanically recycled postconsumer and postindustrial polyolefins. The line includes new plastic additive combinations for recyclers, compounders and processors that mitigate quality issues resulting from thermal and mechanical stress during the recycling process. IrgaCycle PS 030 G enhances the long-term thermal stability of high-density polyethylene (HDPE), polyolefins and mixed polymers for use in rigid applications. The PS 031 G grade improves the processing and long-term thermal stability of low-density polyethylene (LDPE) and linear LDPE for use in films and flexible packaging. IrgaCycle PS 032 G provides processing stability and long-term thermal protection for polypropylene (PP) and polyolefin blends with impurities. IrgaCycle UV 33 DD improves the thermal and processing stability for HDPE and PP blends destined for outdoor products and helps protect them from weathering. Lastly, the XT 034 DD grade for polyolefins helps neutralize impurities and improves processing and long-term heat stability.
What’s new? The five additives, with more in the works.
Benefits: Improved product quality and enhanced sustainability. The additives, which incorporate the company’s antioxidant and light-stabilizer systems, can help boost the percentage of recycled content in packaging and in automotive, building and construction products. Additionally, they come in a granulated, ready-to-use, nondusting form.
BASF, Florham Park, New Jersey, 800-526-1072, www.plasticadditives.basf.com

Compact granulators feature large hopper openings
G-Max: The compact granulators in Wittmann Battenfeld’s G-Max series were created for the closed-loop recycling of sprues, runners and defective parts from injection molding machines. They are appropriate for grinding soft to medium-hard plastics, such as polypropylene, polyethylene, acrylonitrile butadiene styrene and polyurethane, and can handle materials that are still warm from processing. The granulators feature a rotor with open spaces between the rotating knives and the center of the shaft, which provides unrestricted airflow through the cutting chamber. Wittmann Battenfeld offers material screens with different sizes of perforations to accommodate a variety of materials and throughputs. A magnet is a standard feature to prevent the processing of metals.
What’s new? Upgrades to the G-Max 23 and G-Max 33 models that standardize their design based on the line’s smaller G-Max 13 model. The G-Max 23 and G-Max 33 models now come with larger hopper openings and a choice of fixed and rotatable versions of their material outlets. The G-Max 23’s cutting chamber measures 12.2 inches by 9.3 inches, and its motor output is 3 kilowatts (kW). The G-Max 33 has a cutting chamber measuring 18.1 inches by 9.3 inches and a motor output of 4 kW.
Benefits: Quiet, efficient operation and easier maintenance. The granulators’ tiltable material hoppers are simple to clean and service; screen changes can be carried out quickly, without tools.
Wittmann Battenfeld Inc., Torrington, Connecticut, 860-496-9603, www.wittmann-group.com

Additive improves haze and color aesthetics of recycled packaging
ColorMatrix Amosorb 4020R: Avient’s latest oxygen-scavenger additive is formulated to allow the use of up to 100 percent recycled polyethylene terephthalate (PET) content in containers. The oxygen-scavenging polyester concentrate creates an active barrier against the ingress of oxygen through the walls of PET containers used to hold a wide range of oxygen-sensitive products. Compatible with many different grades of recycled PET, the additive can be used in both monolayer and multilayer containers and is added to the PET melt via conventional pellet-handling systems.
What’s new? The ColorMatrix Amosorb 4020R additive. The new additive joins a portfolio of ColorMatrix additives for improved recycling of plastic packaging.
Benefits: High-quality containers made with up to 100 percent recycled content. In addition to providing consistent oxygen-scavenging performance, the additive improves the aesthetics of recycled packaging in terms of haze and color. By creating an active barrier against oxygen ingress, the concentrate also protects a container’s contents and extends product shelf life. The cost-effective and ready-to-use formula comes in air- and moisture-tight sealed containers and requires no drying before use.
Avient Corp., Avon Lake, Ohio, 866-737-2066, www.avient.com

Bulk bag discharger designed to provide mobility and flexibility
Mobile bulk bag discharger: This mobile unit in Flexicon’s Bulk-Out BFF series has a variety of features that help it efficiently empty materials from bulk bags and convey them to downstream equipment or storage vessels via a flexible screw conveyor. The entire bag is elongated, and downward tension is exerted on the bag’s spout. Additionally, the unit’s Flow-Flexer activators impose a steep “V” shape on alternating sides of the bag throughout the emptying process. Its lifting frame allows bulk bags carrying solid materials—such as pellets or powdered additives for plastic recycling—to be raised into place by a forklift, and a vent port with a filter sock controls dust.
What’s new? The mobile bulk bag discharger.
Benefits: Mobility and flexibility. Locking casters allow the discharger to be transported anywhere within a plant, and it can accommodate bulk bags from 3 feet to 7 feet in height. A lower clean-out cap on the conveyor tube comes off easily so the flexible screw can be removed. The tube’s interior can be flushed with steam, water or cleaning solutions.
Flexicon Corp., Bethlehem, Pennsylvania, 610-814-2400, www.flexicon.com

Sorting robots include new data-acquisition station
SamurAI: Machinex’s SamurAI articulated robots use artificial intelligence (AI) to extract recyclables, such as plastics, from a material stream or to remove contaminants from a particular material, such as polyethylene terephthalate (PET). MACH Hyspec optical sorters can be used in plastics recycling facilities to sort PET, high-density polyethylene, polyvinyl chloride, low-density polyethylene, polypropylene, polystyrene and other resins.
What’s new? The company’s latest AI technologies, MACH Vision and Intell platform, which now can be integrated into the SamurAI robot and MACH Hyspec optical sorters as options. MACH Vision is a data-acquisition station powered by AI that can use a combination of technologies, including infrared hyperspectral technology, visual recognition and metal detectors, to analyze material streams. MACH Vision is connected to Intell, a platform that provides real-time data capture so that users can fully comprehend the characteristics of the material stream. It provides key performance indicators, such as flow composition, volume per material type, material trends and total amount of material on the conveyor belt.
Benefits: Improved efficiency and performance. The technologies give facility operators a better understanding of the composition of material streams in real-time. With this information, users can quickly respond to changing trends to optimize sorting performance using a data-driven process.
Sponsored Content
Labor that Works
With 25 years of experience, Leadpoint delivers cost-effective workforce solutions tailored to your needs. We handle the recruiting, hiring, training, and onboarding to deliver stable, productive, and safety-focused teams. Our commitment to safety and quality ensures peace of mind with a reliable workforce that helps you achieve your goals.
Machinex Technologies Inc., High Point, North Carolina, 877-362-3281, www.machinextechnologies.com

Continuous melt filters minimize PET loss
ECO: Maag’s Ettlinger brand includes the ECO line of high-performance continuous melt filters for postconsumer and postindustrial polyethylene terephthalate (PET) recycling. The filters efficiently remove foreign particles, such as gels, black specks, paper, wood, aluminum, copper, rubber, silicone and polymer composites. Typical applications for the melt filters are extrusion systems in which PET bottle flake is converted into food packaging films, tape and fibers, or in compounding and repelletizing processes. The melt filters are appropriate for contamination levels of up to 1.5 percent.
What’s new? The ECO 350, which replaces the company’s ECO 250 model, and the ECO 500, which replaces the ECO 250 Twin. New features include a system that makes the contamination discharge more concentrated, reducing the loss of PET melt. Additionally, the new melt filters provide easier access to the scraper system for maintenance. The ECO 350 has a maximum throughput of more than 5,500 pounds per hour and a total filtration surface of 1.7 square feet. The ECO 500 can achieve throughputs of up to 8,800 pounds per hour and has a total filtration surface of 3.4 square feet. The two new models join the ECO 200, which has a throughput of 2,646 pounds per hour and a total filtration surface of 1.35 square feet.
Benefits: Higher throughputs, effective filtration and operator convenience. The filters provide continuous operation with constant pressure on the outlet side, resulting in extremely low melt losses and consistent melt flow without dead zones or degraded polymer quality. Additionally, users can go weeks or even months without replacing the screens.
Maag Group Ettlinger, Atlanta, 770-703-8541, www.maag.com
Get curated news on YOUR industry.
Enter your email to receive our newsletters.
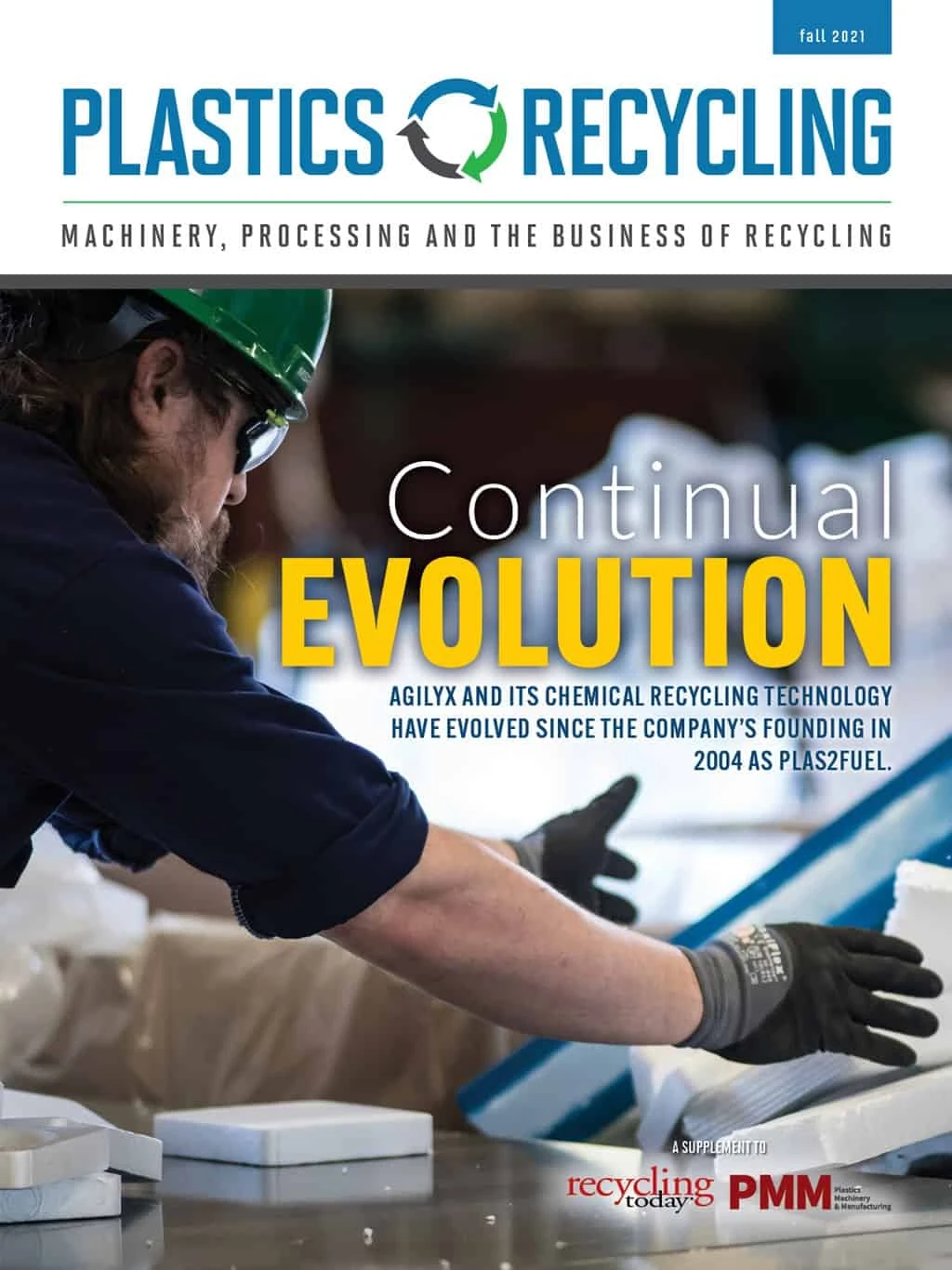
Explore the Fall 2021 Plastics Recycling Issue
Check out more from this issue and find your next story to read.
Latest from Recycling Today
- AF&PA report shows decrease in packaging paper shipments
- GreenMantra names new CEO
- Agilyx says Styrenyx technology reduces carbon footprint in styrene production
- SABIC’s Trucircle PE used for greenhouse roofing
- Hydro to add wire rod casthouse in Norway
- Hindalco to invest in copper, aluminum business in India
- Recycled steel price crosses $500 per ton threshold
- Smithers report looks at PCR plastic’s near-term prospects