
AutoScreen: Melt Filtration Products is in the process of upgrading its continuous screen changer, which has been designed to perform screen changes without disruptions in production or process conditions. It is ideal for handling in-house scrap and also can be used in recycling applications involving light-to-moderate levels of contamination. An HDPE pipe manufacturer installed an AutoScreen to eliminate frequent screen changes and high extrusion head pressures. Using AutoScreen’s pressure-differential system, the company now can extrude within a selectable, consistent pressure range with no deviations because of changes in material densities or contamination levels.
What’s new? Control upgrades that the company expects to make available within the next couple months. With the upcoming features, users will be warned when the system’s exit heater might fail and when the canister containing rolled screen is running low.
Benefits: The ability to better plan maintenance and avoid downtime. The AutoScreen’s upgrades will give users more control over the process.

C series: Virtus’ granulators are tailored to municipal or large-scale recycling applications and for dealing with postconsumer scrap. The granulators have widths ranging from about 1 foot to about 3 feet, 4 inches. The machines are soundproofed and come with replaceable wear plates and an automatic hydraulic system that allows access for cleanouts and maintenance.
What’s new? Two new models, the C25 and C40, with rotor diameters of 10 and 16 inches, respectively. The C40 is pictured.
Benefits: Wear-resistant design and the ability to handle very large items. With its chamber design, aggressive rotors and infeed features, the series can take very big cuts of large blow-molded parts, such as 5-gallon water jugs. A curved rear wall prevents obstructions. For improved safety, the knives can be adjusted outside the machines.

C-20 DeDuster: Pelletron’s new deduster represents an upgrade of the company’s PI series and an earlier version of the C20. It is made for removing labels and dust as part of the recycling process. With discharge capacities between 10 and 50 pounds an hour, it is compatible with every injection molding machine and small extruders. The 12-inch high, 18-pound system fits between the injection molding machine inlet and the hopper.
What’s new? Upgrades, including improved flow-rate control, and a new flexible agitator paddle and combined cyclonic dust-collection module.
Benefits: Cleaning efficiency, easy operation, compact size and cost-effective price, which remains unchanged from 2015. With its new agitator paddle, the device achieves gentler material handling.

Coffin shredder: Republic Machine’s upgraded long-compartment shredder is designed for oversized materials, including sheet and pipe. It features an Allen-Bradley controller and large color touch screen.
What’s new? Upgrades to the ram, which is hydraulically driven and runs the length of the compartment. The rollers that guide the ram are no longer inside the compartment but have been moved outside along a track. Also, the company has expanded the series’ offerings. Square compartment sizes of 32 inches (shown above, with a 25-foot-long compartment), 42 inches and 54 inches now are available, along with the original shredder in the series, a 25-inch model. The company has even made a custom shredder with dimensions of 62 inches by 32 inches.
Benefits: With the ram chain drive’s redesign, it is now more dependable and easier to maintain and clean. The hydraulic drive moves the ram at a constant velocity with closed-loop variable pressure control, allowing both long and short objects to feed into the rotor more consistently. Through this process, the output is more consistent, with less heat generated in the cutting process.

DGD dual-shaft shredder: Hosokawa Polymer Systems’ new series of shredders offers low-speed, high-torque, high-capacity size reduction. The units can shred a wide range of materials and products, including plastics and electronics. The models include the DGD1000, 1500 and 2000. The largest, the DGD2000, has twin 32-inch-diameter cutter discs and a 60-inch-by-78-inch chamber. The motor sizes are designed according to the user’s particular application and have up to 200 horsepower.
What’s new? The product, which Hosokawa introduced at the Plastics Recycling Conference in February in New Orleans.
Benefits: Easy maintenance, less downtime and longer machine life. In addition to the large-diameter cutting discs—which allow for the high-throughput processing of large parts and bales—the machine’s other components, including cutter tips, stator plates and sidewall wear plates, are easily replaced.

ERA: Built to handle highly contaminated plastic, Fimic’s new automatic filtration unit combines two filtering stages within one extruder. It uses two filtering chambers, with steel blades for scraping contamination from two separate screens. The first filtration chamber, which has a punched screen, filters coarse materials, while the second chamber, with a laser-drilled screen, handles finer materials as small as 150 microns.
What’s new? The system, which made its debut last year in Europe and is now available in the U.S.
Benefits: Consistent, fine filtration and the ability to handle higher-value materials. Double filtration allows recyclers to handle a wider range of materials, including PP and HDPE, and replaces the need for tandem extruder lines.

Filtered receiving cyclone: Foremost Machine Builders has introduced a filtered receiving cyclone, which is used with positive-pressure blowers to unload scrap granulators. The cyclone separates the plastic from the conveying air, which is evacuated through the gas exhaust, while the plastic is discharged at the bottom. It features automatic pulse-jet filter cleaning, a 6-inch-diameter discharge and has various options for inlet diameters. It can be used with blowers that move up to 900 cubic feet of air per minute, with line sizes up to 5 inches in outer diameter.
What’s new? The product, which was developed in response to customer requests to resolve dust problems.
Benefits: Convenient, nearly dust-free operation. The cyclone eliminates the need for cumbersome hanging filter bags that require emptying and cleaning and is more economical than a central dust-collection system.

LI-120: Using dual near-infrared vision technology, or NIR, this optical sorter makes it possible to separate plastic flakes, pellets and regrind according to composition rather than by color. Applications include sorting mixed bottle flakes made up of materials such as PET and PVC.
What’s new? Upgrades to the machine that have doubled its throughput. The machine, which was updated in October 2015, has been used by U.S. manufacturers for about one year. It was introduced in Asia about three years ago.
Benefits: Efficient sorting and high throughput at a cost-effective price. The machine’s advanced vision system ensures greater purity and less production loss. AMVT says the system can achieve 90 percent to 98 percent accuracy in PVC sorting.
_(1)_fmt.png)
LM/SM: Weima has introduced a series of heavy-duty granulators for processing a wide range of plastic scrap, including pipes, profiles, bottles, drums, purgings and car bumpers.
What’s new? The product line, which has models in four sizes to accommodate various applications. Previously, Weima had used outside sources to supply granulators to complement the company’s line of shredders.
Benefits: Durability, adjustability and accessibility. The heavy-duty sidewalls and robust structure are designed for tough applications and long machine life. The knives can be adjusted from outside the cutting chamber with a knife jig for reduced downtime. The tilting design allows for quick access to the cutting chamber and screen for easy cleaning and maintenance.

NRT Connect: Users of a range of National Recovery Technologies optical sorters now have access to this optional new, free service. It is available through a software upgrade to users of sorters shipped after January 2015. It provides continuous monitoring of sorters and builds reports and sends alerts automatically. If an operating condition moves outside normal operating parameters, NRT Connect posts an alert on the sorter’s interface. At the same time, it sends a phone alert to the NRT service team, so team members can begin providing assistance remotely. NRT Connect also can be compatible with older sorters, though hardware upgrades might be necessary.
What’s new? The service, which NRT rolled out in mid-February.
Benefits: Proactive machine maintenance. NRT service team members have access to information that can guide them in maintaining optimal sorter performance. The feature provides instantaneous, extensive data to users, as well, so they can track performance and recognize immediately if their systems are experiencing problems.

Plast-Agglomerator, type PFV-PC: Pallmann says its compact agglomerator is well-suited to processing thermoplastics, such as PET bottles and film, and is able to handle materials with a moisture content of up to 10 percent. The feed material is cleaned in a washing system and then introduced into the agglomerator via a screw press or a centrifuge. The machine reduces the moisture content to less than 10 percent, eliminating the need for a costly upstream thermal drying process.
What’s new? The machine, which Pallmann was scheduled to demonstrate at Plastics Recycling Show Europe, held in Brussels late last month.
Benefits: Material integrity, speed and low energy consumption. Processing is performed below the materials’ melting point by means of frictional heat, preserving its properties. The machine can achieve throughput rates of more than 2,200 pounds per hour, though its motor consumes less than 200 kilowatts of power.

Polyfloat: Sicon’s Polyfloat system uses water to separate mixed plastics, such as PVC, ABS, PS and polyolefins. Plastic particles float to the top or sink because of their specific densities. Various equipment options, such as surface rakes, a rabbling mechanism and floor-scraper discharge, make the system suitable for various feedstocks, including films and flakes, and differing particle sizes. The system also has a dissolving station and mechanical drying line. A pretreatment system for washing mixed plastics also is available.
What’s new? Introduction to the U.S. market. Sicon has been selling Polyfloat in Europe for three years and now has adjusted the feedstock preparation portion of the system to accommodate the coarse plastic flake typically available in the U.S.
Benefits: High product yields and purity levels greater than 99 percent. Small particles down to 0.5 millimeters can be separated, unlike with near-infrared sorting.

RecoSTAR universal: Starlinger has upgraded its recoSTAR universal recycling line, which is designed to process a wide range of plastic waste, including film, molded parts, fibers and filaments made from a variety of resins. Options include various degassing and filter systems, depending on the input material, and water-ring, underwater and strand pelletizers.
What’s new? The Active shredder, which can process input material in almost any form without pregrinding. The shredder’s high-performance rotor can be cooled to offset frictional heat that could melt the material and result in clogs. The rotor also can be heated when processing humid materials.
Benefits: User-friendly, energy-efficient operation. The line features completely automatic startup and shutdown operations as well as a self-reversing rotor that removes material buildup automatically during production. Easily accessible service openings and simple knife changes also ensure maximum uptime. The efficient extruder drive and infrared barrel heating save energy.

SAS Series separators: Herbold USA’s new mechanical screw system removes heavy materials from the material flow within recycling systems. The screw creates an upward flow of water and material through a separation chamber. In this process, heavy materials sink to the bottom of the chamber and then are evacuated through a valve; in the meantime, salvageable resources, such as recyclable plastics, are forced upward through an opening at the top of the incline. The systems are available with single- or double-screw configurations and with throughput capacities of up to 4,400 pounds per hour for shredded film and up to 8,800 pounds per hour for rigid plastics. An additional pump and a reservoir are available as options.
What’s new? The system, which Herbold USA debuted last year.
Benefits: Protection of downstream recycling machines, including granulators, from the potential damage caused by heavy materials, such as stone, metal and glass.

Saturn hammermill series: This new series can reduce materials to very small sizes, making the machines well-suited for handling items such as military and information technology products that must be destroyed. They also can be used on medical or bulky waste, and in waste-to-energy applications. Featuring heavy-duty plate steel, the series is available in 3-foot, 4-foot and 5-foot diameters and in a total of five size configurations, with speeds of 900-1,200 revolutions per minute.
What’s new? The series, which was introduced last year. It now is being targeted for the shredding of brittle plastics, such as ABS, and mixed-material plastics.
Benefits: Versatility, compact size and toughness. Compared with traditional shredders, it has a smaller footprint and a moderate tolerance for items considered “unshreddable,” such as products with embedded tramp metal. The hammermills also have several features designed to ensure product longevity. This includes replaceable wear liners.
_fmt.png)
Uni-Shear SR900: The SR900 single-rotor grinder is engineered to downsize and liberate a wide range of preshredded or commingled items in a single pass while producing predictable, consistently sized particles. This rotary grinder is available with 224-kilowatt or 2,978-kilowatt drive options and with rotor lengths of about 6.6 feet or 9.2 feet.
What’s new? The most recent expansion of the Uni-Shear shredder and grinder product line.
Benefits: It uses the same direct drive design found on other SSI products to eliminate unnecessary parts. It features a cutting chamber access system that requires no tools to open for service access. Common cutters are used on the rotor and anvil bead to simplify parts identification and servicing.

V-Eco shredders: Featuring upgrades based on customers’ feedback, Vecoplan’s V-Eco series shredders have been optimized for American and Canadian users. The shredders feature a hydraulically controlled flow for easy cleanouts and maintenance.
What’s new? Numerous upgrades, including re-engineered control panels and mechanical enhancements. Some of the new functions include access to shredding histories and manuals.
Benefits: Simple maintenance and improved safety, ease of use and performance. The new control panels, designed based on North American customers’ requirements and preferences, make the machines more user-friendly.

Varisort: This optical sorting system, which includes state-of-the-art controls, a conveyor and an air-control unit, has advanced sensor technology for metal, color and detection of polymer type. Both two-chute and three-chute sorting tasks are possible on one sorter.
What’s new? A bigger working width of about 9 feet and upgrades to the software for the system, which originally was released in the U.S. in 2007. The upgraded system will debut in Munich from May 30 to June 3 at IFAT, a trade fair for water, sewage, waste and raw materials management.
Benefits: Low maintenance and energy costs and a high level of customizability. The upgrades allow higher throughput rates. In addition, with the control software, operators can make product-specific adjustments.

Water recycling system: Matec’s new fully automated, closed-loop system makes it possible to filter and reuse the water that’s used to wash materials in the recycling process.
What’s new? The system, which has been available since the last few months of 2015.
Benefits: Conservation of fresh water and elimination of discharge. The system produces dry cake that can be hauled easily to a landfill. This lowers the amount of waste that must be hauled and reduces the landfill fees that operators pay for disposing of it. These results mean operators can save money on utility fees while eliminating sewer bills altogether.

Xtreme metal detector Enhanced Platform: Also referred to as an EP, Eriez’s upgraded metal detector features include easy setup and a dedicated event log, accessible through its smartphone-based interface. The EP can be added to new equipment or retrofitted to existing Eriez products. The EP, installed on an Xtreme metal detector, is pictured.
What’s new? Greater detecting sensitivity. The EP builds off Eriez’s Xtreme metal detector technology. The interface also has been redesigned.
Benefits: Greater sensitivity and resistance to vibration, leading to fewer false readings.

ZTS-P: Designed to handle postconsumer waste and waste-to-energy applications, these heavy-duty hybrid shredders cut parts down to a consistent size at a fast rate. The machines are equipped with tough, built-in wear plates. The knives, rotor and stator have rectangular cutting edges for tearing apart material. The series includes a number of sizes and drives with power capacities of up to 400 kilowatts.
What’s new? The product, which was released this year.
Benefits: Wear-resistance and high throughput. The machines’ rectangular cutting edges have been designed to be resilient, and the knives have been arranged to optimize cutting rates.
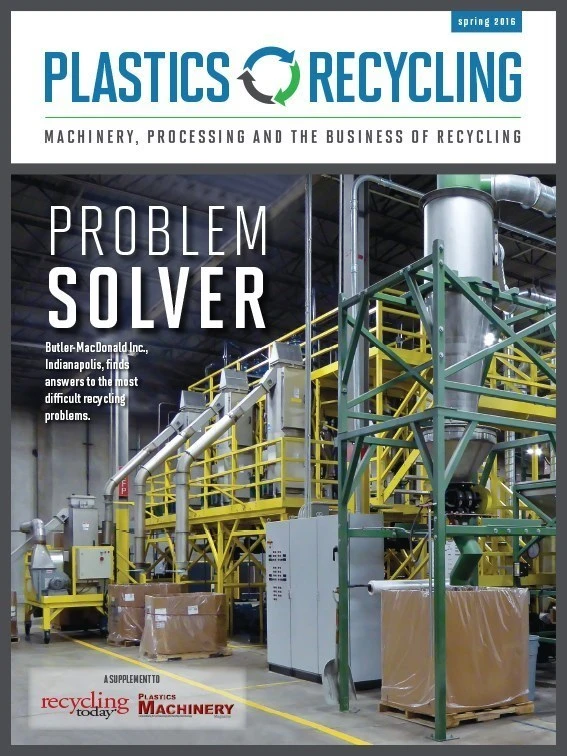
Explore the April 2016 Plastics Recycling Magazine Issue
Check out more from this issue and find your next story to read.
Latest from Recycling Today
- SABIC’s Trucircle PE used for greenhouse roofing
- Hydro to add wire rod casthouse in Norway
- Hindalco to invest in copper, aluminum business in India
- Recycled steel price crosses $500 per ton threshold
- Smithers report looks at PCR plastic’s near-term prospects
- Plastics association quantifies US-EU trade dispute impacts
- Nucor expects slimmer profits in early 2025
- CP Group announces new senior vice president