Waste conversion. A process that converts end-of-life plastics into carbon nanotubes is the subject of a patent application from Trimtabs Ltd. of Swansea, Wales.
The patent application points out disadvantages of conventional methods for turning solid polymers into carbon nanomaterials. It notes that pyrolysis—with or without the use of a catalyst—must be performed at high temperatures, incompletely uses the solid polymers being converted and leaves behind coke or char carbon as waste.
The invention lowers production costs by using unconventional feedstocks instead of precursors derived from petroleum or natural gas. The application notes, “According to the present disclosure, any waste plastic that can be dissolved, dispersed or suspended in a suitable solvent may be utilized as a feedstock.” Raw materials also include biofuels, paints, refrigerants, biopolymers and various other carbon- containing materials.
Carbon nanotubes are produced by forming a mixture from carbon-containing material and a metallic catalyst precursor combined with a solvent. This mixture is injected into a carrier gas and conveyed into a reaction vessel that has multiple independent heating zones. The mixture is heated in stages to a maximum temperature of 1,832 F, which facilitates carbon nanotube growth. The carbon nanotubes are then removed from the reaction vessel.
Patent application 20190375639; published Dec. 12, 2019
Washing method. Anzano del Parco, Italy-based Previero N. Srl seeks to patent equipment and a method for washing plastics and separating them from contaminants, particularly metal.
The method and apparatus are simple from a functional and structural point of view but also are efficient, limiting consumption of washing fluid and energy, according to the patent application.

The invention includes a washing container with inlet and outlet ports that are arranged opposite each other. It also features angled stirring elements driven by variable-speed motors to create turbulence, moving the plastic pieces upward. A speed of between 200 rpm and 400 rpm is most effective for washing and separating the plastic and contaminants.
“The method and the apparatus disclosed above enable high levels of purity to be obtained in the recovered plastics material in reduced time, owing to the immediate continuous removal of the contaminants from the washing container,” the application states. “Owing to the dual function of the mechanical stirring and floating thrust performed by the stirrers … optimum separation of the contaminants from the plastics materials is obtained.”
Patent application 20190351427; published Nov. 21, 2019
Decomposition. A method and system for breaking down contaminated plastics from municipal waste or marine debris is the subject of a patent application from BioCellection Inc., Menlo Park, California.
The invention transforms contaminated plastics into products such as dicarboxylic acid and other chemicals.
The method involves putting plastic scrap in a reaction vessel, adding one or more oxidizing agents, such as aqueous nitric acid, and subjecting the mixture to heat and pressure. During the reaction, the contents are agitated, and any vapors that are created are condensed back into liquid.
The system can include a separation unit with an evaporator. In some embodiments of the invention, via a screw conveyor, plastic scrap and aqueous nitric acid are continuously added to the reaction vessel and the decomposition products are continuously removed.
Patent application 20190322834; published Oct. 24, 2019
Mixed-plastics recovery. An Estonian company has invented a system to turn mixed, dirty plastics into boards that can be used to make landscaping products, furniture, noise barriers and building materials.
The system from Rolan Investment OÜ, Tallinn, Estonia, includes equipment for removing metal contaminants and incorporating additives and an extruder that melts and foams the mixed plastics in a continuous process. Additionally, the system includes a two-phase cooling stage, a controlled pultrusion process and cutting equipment.
To stabilize the production process, “the devised temperature curves and pressures caused by extrusion are monitored and controlled. … In contrast with the known solutions, the calibration matrices are divided into several parts. This ensures a stable extrusion process that can be controlled and directed,” according to the patent.
The system uses unsorted, unidentified and dirty, mixed plastics to make products that can be milled, sawed and nailed and are weatherproof and maintenance-free, the patent states.
Patent 10,486,352; issued Nov. 26, 2019
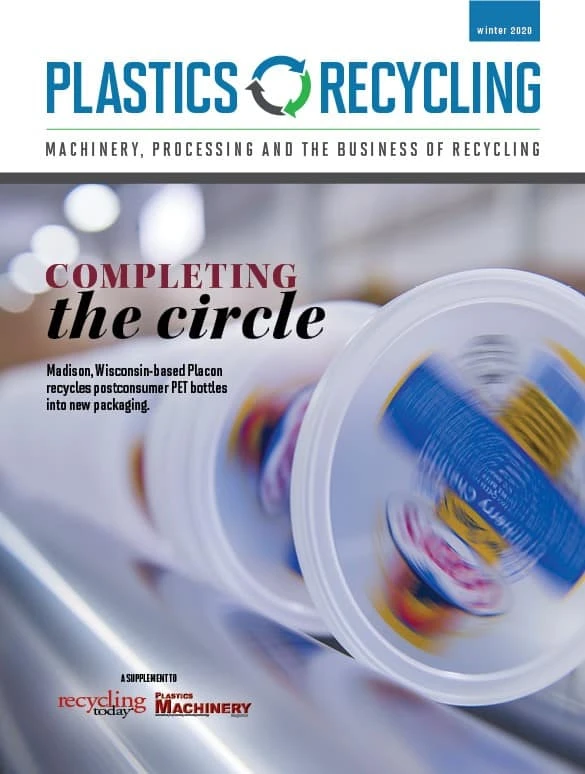
Explore the Winter 2020 Plastics Recycling Issue
Check out more from this issue and find your next story to read.
Latest from Recycling Today
- AF&PA report shows decrease in packaging paper shipments
- GreenMantra names new CEO
- Agilyx says Styrenyx technology reduces carbon footprint in styrene production
- SABIC’s Trucircle PE used for greenhouse roofing
- Hydro to add wire rod casthouse in Norway
- Hindalco to invest in copper, aluminum business in India
- Recycled steel price crosses $500 per ton threshold
- Smithers report looks at PCR plastic’s near-term prospects