
Having spent 15 years in the scrap industry as a safety professional, I have seen safety incidents ranging from deflagrations to bomb squad visits, and through all the chaos, we still managed to go eight years with only one lost-time accident. When I started with the company, its best record was 212 days without a lost-time accident, so I learned a lot in those early years.
I learned that managing safety with the brain in mind can be a game changer. I express this process with the acronym SCARF, and I think of this acronym as a kind of headgear an organization can wear to prevent exposure to safety dysfunction.
‘S’ stands for safety
Workers’ feelings about safety can significantly impact their well-being, productivity and overall job satisfaction. Contrary to the misconception that safety hinders productivity, research shows a safer workplace leads to a more productive workforce. Organizations should view safety, quality and productivity as goals to achieve together, rather than prioritizing one over the other.
Although a job often is regarded purely as an economic transaction in which people exchange their labor for financial compensation, the brain experiences the workplace primarily as a social system. Workers look at this social system in one dimension that is mostly production-related because workers find this is what managers are concerned about most.
For example, imagine workers in their vehicles, stopped at a traffic light. They likely are looking at the light and waiting for it to turn green, not necessarily paying attention to the traffic moving from left to right.
Now, view this scenario as a traffic circle instead of a traffic light. While driving around the circle, a manager might look at every single car attempting to enter that circle, or social system. Three streets merge into that circle: production, quality and safety.
When driving around this circle, a manager must pay equal attention to all three streets while also remaining in the circle.

‘C’ stands for causality
At many companies, resolving safety accidents/incidents can be a confusing maze of different tools, baffling terms and puzzling categories. An investigation should make a problem clearer, not more complicated.
In American culture, we always blame the worker first when an incident occurs. However, when looking at the causality of an incident we must ask what enabled it and what processes or procedures failed. Only when we establish that all processes and procedures were followed can we determine how an incident occurred.
‘A’ stands for autonomy
Stress undermines the ability to function. A perception of reduced autonomy—being micromanaged, for example — easily can generate a threat response. When employees feel a lack of control, their perception of uncertainty also is aroused, further raising stress levels.
Early in my career, I was sandblasting a machine I had not seen before. When I was finished, my supervisor asked why I blasted it that way. I replied that it was how I thought it should be done, and the supervisor reminded me to ask if I didn’t understand what to do.
A few weeks later, another machine I was unfamiliar with came into my area for me to blast. I asked the supervisor for guidance, and he replied, “How do you think it should be done?” After I gave him my answer, he replied, “Then why did you ask?”
Workers feel more autonomy when they are included in safety projects such as guarding the machine they work with or getting involved with a manager’s ideas. A good example was our Internal Traffic Control Plan, which had designated walkways for employees. Keeping them safe while transitioning from one location to another worked very well when they submitted input.
‘R’ stands for relatedness
Fruitful collaboration depends on healthy relationships, and that requires trust and empathy. However, in the brain, the ability to feel trust and empathy toward others is shaped by whether they are perceived to be part of the same social system. This pattern is evident in many domains.
In safety training courses throughout the years, I often would use the term “residual” to explain the dangers of automobile gas tanks. I started asking the classes if they knew what that term meant, and I was surprised to discover that a lot of new hires did not know the word. Employees who do not understand what you are saying cannot interact with you intellectually and will perceive that they are not part of your social system.

‘F’ stands for fairness
The perception that a safety event has been unfair because of a write-up or a drug test, for example, generates a strong response, stirring hostility and undermining trust.
In organizations, the perception of unfairness creates an environment in which trust and collaboration cannot flourish. Leaders who play favorites or who appear to reserve privileges for people similar to them can incite a threat response in employees who are outside their circle.
Leaders often underestimate the importance of addressing threats to fairness, and this is especially true when it comes to compensation.
Fairness in the workplace contributes to employees feeling safe and engaged. It involves fair compensation, equal treatment and appreciation for hard work by management.
When your workforce feels it cannot trust you while traveling in the roundabout or they see you going down one of those three streets too often, they likely see you as a threat to their social system.
If you want to manage safety with the brain in mind, you need to apply SCARF to keep you away from dysfunction. Keep workers feeling safe; have great causality investigations by not blaming the employee; give them autonomy by making them part of the decision-making process and do not micromanage; let workers relate to your social system, being fair in what you do.
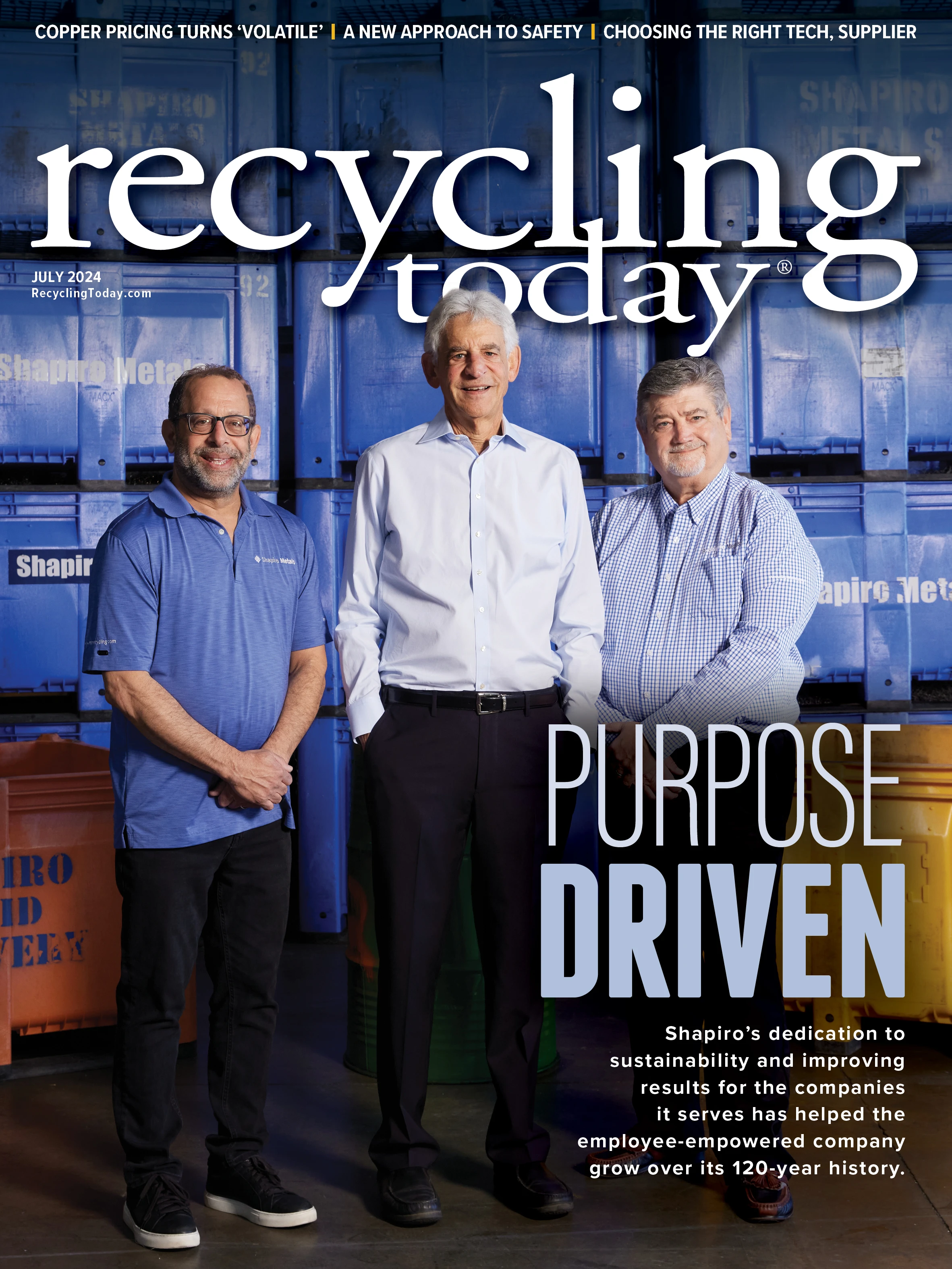
Explore the July 2024 Issue
Check out more from this issue and find your next story to read.
Latest from Recycling Today
- Green Cubes unveils forklift battery line
- Rebar association points to trade turmoil
- LumiCup offers single-use plastic alternative
- European project yields recycled-content ABS
- ICM to host colocated events in Shanghai
- Astera runs into NIMBY concerns in Colorado
- ReMA opposes European efforts seeking export restrictions for recyclables
- Fresh Perspective: Raj Bagaria