
Sustainability is more than just a buzzword; it also is the notion that we as a society must continue to look for meaningful ways to reduce the constant stream of waste that is being sent to landfills.
In 2015 The Food service Packaging Institute (FPI), Falls Church, Virginia, launched an initiative that takes an important step to ensure valuable reusable materials are being recycled instead of sent to landfills.
A dozen FPI members,including manufacturers, suppliers, distributors and operators/retailers in the food service and packaging industry, came together in 2014 to establish the Foam Recycling Coalition (FRC). The FRC’s purpose is to provide direct support for the increased recycling of food service packaging made from polystyrene (PS) and from expanded polystyrene (EPS) products. Items such as meat packaging and egg cartons from the grocery store often are made from EPS but go unrecycled. It is just as important to recycle these materials as it is to recycle plastic bottles.
With this in mind, in 2015 the FRC, in association with the EPS Industry Alliance (EPS-IA), Crofton, Maryland, announced a grant program to help businesses in the recycling industry increase their capacity to accept postconsumer EPS products.
WIDENING THE LOOP
Generally, in the past the bulk of EPS recycling efforts have focused on industrial sectors where commercial product distributors and vendors recycle large volumes of material collected from protective packaging from products like refrigerators or televisions. The FRC grants instead target entities that manage residential curbside and drop-off recycling programs to extend foam product recycling to consumers.
“The idea behind the grant program is to help material recovery facilities recycle EPS cost effectively,” says Lynn Dyer, president of the FPI. “Essentially it’s all about volume and economics. What can we do to make diverting consumer-level EPS foam products from the waste stream more appealing to the recycling industry from an economic perspective?”
Dyer points out that the obstacle always has been the sheer volume of space required to transport the recovered foam to a processor. The grants specifically provide funding for a specialized compactor, known as a densifier, used to compress the foam at material recovery facilities (MRFs). The densifier greatly reduces the volume of space required to store or transport EPS foam by squeezing out air, which represents roughly 90 percent of the product’s material composition by volume.
By way of illustration, a 48-foot truckload of baled undensified EPS weighs approximately 16,000 pounds. The same truck packed with densified foam weights approximately 40,000 pounds, greatly increasing the cost-effectiveness of collecting and redistributing EPS materials.
The FRC says it expects to significantly increase the amount of EPS that is returned to the manufacturing process by supporting postconsumer recycling at the MRF level. Ultimately, these EPS products will be reused to manufacture all kinds of things, such as crown molding, picture frames or plastic patio furniture. Presently, many EPS manufacturers work in a closed-loop process, meaning the excess foam produced stays in the manufacturing facility and is recomposed with no waste.
“It’s a continual process with dual objectives of creating opportunities to expand EPS recycling opportunities on the individual level and then increasing public awareness that those opportunities exist.” – Lynn Dyer, FPI president
For the EPS industry, regardless of what the foam is manufactured into, increasing public awareness of recycling opportunities is important.
ADDRESSING MISCONCEPTIONS
“We’re very interested in helping to inform the public that these products can and should be recycled,” says Mary Burk, corporate marketing with ACH Foam Technologies, Westminster, Colorado. “Increasing the volume of reusable foam on the consumer level is good for the environment, good for the public and good for the many different industries that use new and recycled EPS for everything from commercial insulation for construction to protective packaging for wine, medicine and refrigerated foods.”
Dyer agrees, adding that it is important to point out a few common misconceptions about recycling EPS food packaging products, the first of which is that foam cannot be recycled at all, which is not the case. The second relates directly to the food service industry, where many consumers are under the impression that PS foam packaging used to hold food products is more contaminated than other forms of packaging.

“It’s a continual process with dual objectives of creating opportunities to expand EPS recycling opportunities on the individual level and then increasing public awareness that those opportunities exist,” she says.
Sponsored Content
Labor that Works
With 25 years of experience, Leadpoint delivers cost-effective workforce solutions tailored to your needs. We handle the recruiting, hiring, training, and onboarding to deliver stable, productive, and safety-focused teams. Our commitment to safety and quality ensures peace of mind with a reliable workforce that helps you achieve your goals.
Dyer’s office was inundated with applications from MRFs across the United States and Canada when the FPI grant program was announced. Her team’s very specific selection criteria for the first grant recipient included level of innovation, market reach within the community and the ability to process a combination of commercial, industrial and residential foam products.
After an exhaustive review and evaluation, Alpine Waste & Recycling, a Denver-area company, was selected. Alpine Waste & Recycling has maintained a dedication to sustainable practices since the company’s inception in 1999.
“Alpine has a reputation in this market as the innovators of the waste and recycling industry while maximizing sustainability and helping to preserve the environment,” says Brent Hildebrand, Alpine Waste vice president of recycling. “The grant from the Foam Recycling Coalition affirms our place as leaders in the recycling community, and we’re very excited to promote this new efficiency in EPS recycling with the advanced technology in our expanded, retooled recycling plant.”
What is on the horizon for the FRC and its efforts to support EPS recycling is more of the same: more public information to make consumers aware of the opportunity to recycle products that are every bit as common and reusable as those made of other materials.
Get curated news on YOUR industry.
Enter your email to receive our newsletters.
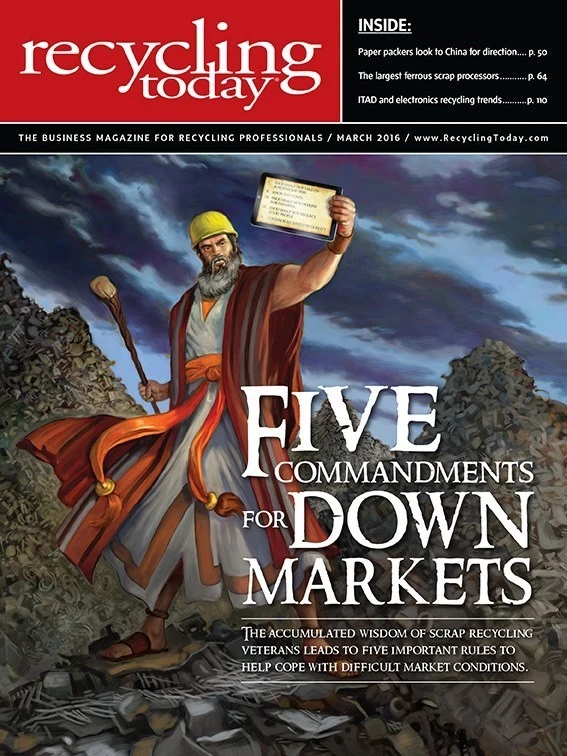
Explore the March 2016 Issue
Check out more from this issue and find your next story to read.
Latest from Recycling Today
- Nucor expects slimmer profits in early 2025
- CP Group announces new senior vice president
- APR publishes Design Guide in French
- AmSty recorded first sales of PolyRenew Styrene in 2024
- PRE says EU’s plastic recycling industry at a breaking point
- Call2Recycle Canada, Staples Professional expand partnership
- Circular Services breaks ground on north Texas MRF
- Tariff uncertainty results in choppy nonferrous scrap flows