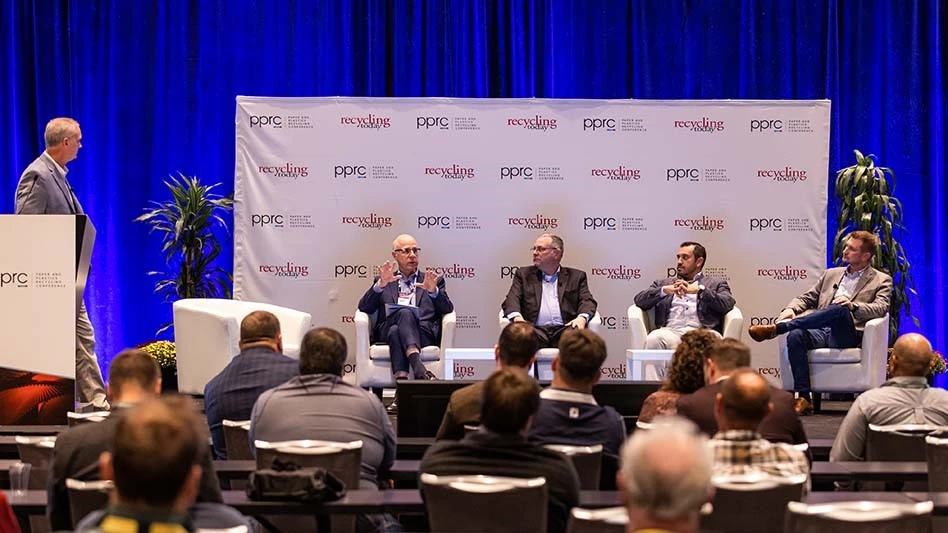
Photo courtesy Mark CampbellProductions
During the 2022 Paper & Plastics Recycling Conference in Chicago Oct. 19-20, experts spoke about factors operators should consider when designing material recovery facilities (MRFs).
The panel was moderated by Brent Hildebrand, CEO of American Recycling Holdings, Modesto, California, and included Nat Egosi, president of RRT Design & Construction, Melville, New York,; Kurt Schmitz, senior vice president for Pratt Industries, Conyers, Georgia; Stephen Miranda, vice president of recycling in North America for GFL Environmental Inc., Vaughan, Ontario; and John Sliwicki, senior vice president of MRF operations at LRS, Rosemont, Illinois.
For Egosi, deciding the technology that will go into a MRF starts at the tipping floor. Four factors operators should consider in the design phase include loading equipment, the material being processed and how it's being fed into the facility’s sorting process.
“The tipping area is a focus area from our point of view in designing these facilities. Were concerned about safety and operational issues,” Egosi said.
To start, operators should consider compartmentalizing their tipping floors, which Egosi said helps separate material and equipment. By organizing the tipping floor, operators can more easily access material to improve how each load is inspected and ensure the material is separated properly. It also separates the material from diesel equipment that could cause potential fires.
Compartmentalizing also allows operators to manage how material gets fed into a system. Egosi said by using walls to organize the material and equipment, operators can account for when material comes into the facility and better stockpile it for when it’s time to get processed, resulting in a better sort.
Schmitz added that operators should consider compartmentalizing the facility if it takes in commercial and residential streams.
“Ideally, you don't want commercial material running through this when you're just scalping one product,” Schmitz said. “A lot of consideration to how you compartmentalize the tip floor, residential versus commercial, and how you bale it at the end [should be taken].”
Sliwicki added that fire inspection technology and safety training were essential at his MRF in Chicago because of the lack of space on the tipping floor.
Once material is ready to be processed, it's time to consider what equipment should be used for sorting. For the panelists, one of the most effective types of separation equipment is screens, typically thought to be used primarily for sorting old corrugated containers. However, Miranda said screening should be used throughout the system.
Operators should consider what material is processed at the MRF, the volume they are processing and what they are trying to move before investing in screening equipment.
“If we're not understanding our stream and we're not creating [and] designing our systems for the proper mass balance of what's going through the lines, we're shooting ourselves in the foot right off the bat," Sliwicki said.
Performing composition audits upfront is where artificial intelligence (AI) learns what to sort from an operator's stream, Sliwicki said. As the AI works to identify the material composition of the stream, it can provide new data that will help a business manage its MRF more efficiently.
“Without that true composition data, you're never really going to truly understand the value of what's in front of you," Miranda said.
The trick is to teach plant managers what the data mean and how to apply it to the sorting process, Egosi said.
While the panelists agreed the data will get easier to read over time, Hildebrand suggested having a skilled analyst on staff could help read and understand the data points.
When it comes to financial modeling and justifying new equipment for a MRF, Miranda said his company looks at factors such as labor costs, maintenance costs, material supplies costs or lease costs.
Another way to factor in how much needs to be spent is by auditing the residue at a MRF. Schmitz said auditing the residue helps a company figure out what is being missed during sorting and thrown away and the contamination in the stream.
Egosi said it is necessary to track downtime when figuring out what equipment to purchase. Understanding what contributed to that downtime, be it the type of material being sorted or an operating error, helps operators find where improvements can be made to the MRF.
Once this data is collected, an operator must track it effectively using an enterprise resource planning (ERP) system. Schmitz added that an ERP can help operators track data from different facilities to learn what works better where and why.
Egosi added that using an ERP system, not just an offline way of tracking, can help put the data into a fully integrated cost structure that will allow operators to make informed decisions.
"If you're not able to convert that into the metrics of dollars, you don't know where you're at," Egosi said. "You need to be able to capture that in an accurate way."
Latest from Recycling Today
- Nucor receives West Virginia funding assist
- Ferrous market ends 2024 in familiar rut
- Aqua Metals secures $1.5M loan, reports operational strides
- AF&PA urges veto of NY bill
- Aluminum Association includes recycling among 2025 policy priorities
- AISI applauds waterways spending bill
- Lux Research questions hydrogen’s transportation role
- Sonoco selling thermoformed, flexible packaging business to Toppan for $1.8B