
Flexible plastic packaging material, while difficult to recycle, still can be recovered for energy, and it’s feasible to do so.
Those are the findings of a recent research project co-sponsored by Dow Chemical Co., headquartered in Midland, Michigan, in collaboration with chemical recycling company Agilyx Corp., Tigard, Oregon, and other interested stakeholders.
The 2014 Energy Bag Pilot Program sought to collect difficult-to-recycle plastics using existing infrastructure, converting the material into fuel.
Through the program, Dow and its partners also are helping to show that implementing such a project is not as complex as it sounds.
Despite expanded recycling programs, more than half of all U.S. trash—roughly 35 million tons—still ends up in landfills, Dow says. The Energy Bag project was designed to test the feasibility of implementing a waste-to-energy solution for some of these nonrecyclable materials.
The three-month Energy Bag program, co-sponsored by Dow and collaborators The Flexible Packaging Association (FPA), Republic Services, Agilyx, Reynolds Consumer Products and the city of Citrus Heights, California, was launched in the summer of 2014.
“Our goal was to develop a system where we could create alternative energy that was economically self-sustaining,” says Jeff Wooster, global sustainability director for Dow Packaging and Specialty Plastics.
For the program, the 26,000 households of Citrus Heights were provided with purple “Energy Bags,” in which they were asked to collect plastic packaging that was not eligible for recycling through the community’s curbside program. During the months of June, July and August, residents of Citrus Heights were asked to place their filled Energy Bags in their 96-gallon lidded recycling containers to be collected along with their recyclables during the community’s normal every-other-week schedule. “We used the motto, ‘If you don’t bin it, bag it,’” Wooster says.
Residents were told to collect such items as snack bags, salad bags, meat and cheese wrappers, foam serving containers, toothpaste tubes, drink pouches and plastic utensils in the purple Energy Bags.
The translucent purple bags were removed from the recycling stream at Republic’s Newby Island Resource Recovery Park in Milpitas, California. The bags, which Reynolds manufactured for the program, were designed to be easy for material recovery facility (MRF) operators to sort.
The bags were then sent to Agilyx, which at that time specialized in converting nonrecyclable and low-value plastics into synthetic crude oil through a patented pyrolysis system. Processing took place at Agilyx’s demonstration facility in Tigard, where the company was operating its Generation 6 continuous feed, automated, self-cleaning technology.
project partners
Wooster says Dow spent nearly two years developing the Energy Bag project and looking for partners before its launch in June 2014. Agilyx handled pyrolysis; Republic Services handled collection; Dow and FPA managed communications efforts; and Reynolds provided specially colored bags.
All of the partners, Wooster says, were greatly interested in furthering their existing recycling efforts and services. The community of Citrus Heights, for instance, already has a comprehensive curbside recycling program, accepting such things as clean pizza boxes, plastic containers Nos. 1 through 7 and plastic bags. Meat trays, plastic utensils and multiwall food pouches that aren’t accepted for recycling through the city’s program were targets of the Energy Bag program.
“We were very proud to be the first community in America to participate in the Energy Bag initiative,” said Sue Frost, mayor of Citrus Heights, after the close of the program. “The program demonstrated how communities nationwide can benefit by diverting typically nonrecycled plastics from landfills and give them new life as an energy resource.”
Agilyx, with its Tigard development facility, was identified as the closest pyrolysis facility with the capacity to handle the mixed plastics. “They were willing to participate and were geographically in the right location,” Wooster says.
Wooster says Agilyx is one of a handful of U.S. companies with technology that can process mixed plastics.
Some 8,000 bags were collected through the pilot, yielding 512 gallons, or 150 barrels, of synthetic crude oil. This equals about 3 tons of waste that was diverted from the landfill.
Ross Patten, CEO of Agilyx, says the 10-ton-per-day development and demonstration facility can process materials at a rate of about 16 pounds per minute. He says it takes about an hour for materials to be converted into synthetic crude oil, and the system runs constantly.
Agilyx sold the synthetic crude oil it produced to refineries.
This Generation 6 technology, as the company calls it, replaced an earlier batch process that was used in a North Portland facility that has since been closed.
“When we need material, we source it from generators in the area,” Patten says, referring to regional MRFs.
“We do have ways of analyzing all different types of plastics to see how they react in our process,” explains Mark Rumford, vice president of engineering for Agilyx.

In the case of the Energy Bag program, testing indicated that the plastics collected were suitable for the company’s process. Even polystyrene trays, largely shunned by recycling facilities, can be part of the mix. “It actually makes an extremely good oil when we put it in our system,” Rumford observes.
Patten says Agilyx’s process also can handle plastics containers Nos. 3 through 7, which are sometimes relegated to MRF residue. However, because the community of Citrus Heights accepts these materials for recycling, they weren’t part of the Energy Bag program.
Agilyx was pleased with the collected materials, he says. Having residents in effect presort the materials meant that further sorting did not need to occur at Newby Island.
“We didn’t have to worry about the contents at all because they were still putting all of their normal recyclables into the bin,” Patten observes.
For the process, Rumford explains, the Energy Bags were shredded to a 2-inch-minus size before heading to pyrolysis. The material was fed to a premelter to drive off the water, creating a black, toothpaste-like mixture. Next, the system’s reactor, using two interwoven, self-cleaning, rotating helical ducts, boiled off the usable plastic, which was then condensed into oil, he says, leaving behind a char byproduct.
“The whole thing is done in the absence of air, so there’s no combustion or burning,” Rumford says. “We are adding heat to boil the plastic to get the vapors, which rise out of the reactor, break down, are recombined and are condensed back into a liquid, which then is cleaned and conditioned.”
Agilyx holds an exclusive license to technology from Oregon-based Therma-Flite for its plastic pyrolysis, Patten says.
“The self-cleaning process is very important when dealing with plastic,” Patten explains, because the melted mix would otherwise stick to the equipment.
While Rumford says the pyrolysis process is relatively simple, challenges arise from dealing with feedstock that can vary from source to source and from day to day.
Earlier in the company’s history, he says, “We erroneously thought we could process any plastic. Now we’ve learned that is not the case.”
Even so, Rumford and Patten say Agilyx can accept most types of nonrecyclable plastics, with the exception of polyvinyl chloride (PVC). Furthermore, the material must be free of other contaminants.
“We want a material that has been preprocessed at the MRF and which meets a specification for our process,” Rumford adds.
Agilyx has developed a specification that Rumford says limits the amount of dirt and moisture that can be included. It calls for a minimum of 90 percent plastic that largely excludes polyethylene terephthalate (PET) and high-density polyethylene (HDPE).
PET and HDPE make a lower quality oil, Rumford says, adding “they have a higher value as a recycled feedstock.”
The specification also sets a limit on the amount of PVC in the feedstock.
“It’s not a very restrictive specification, other than we would like it reasonably clean and dry, and we would rather use the high-value plastic for a higher-value purpose,” Patten says.

While other companies or entities have processes to convert plastics to oil, Patten says Agilyx’s process is unique. “We’ve taken the process to the commercial level, and we’ve also learned how to do it with a mixed waste plastic,” he says.
communication challenges
While the program encountered few challenges, one limitation was communicating the project thoroughly to the community’s households, Wooster says.
Information about the Energy Bag pilot program was shared with residents through fliers that were included with their garbage and recycling billing statements. However, certain groups of residents, such as those on auto-pay programs or those living in rental units—didn’t necessarily receive this information.
Dow says the Energy Bag pilot program achieved a 30 percent participation rate, with 78 percent of Citrus Heights residents saying they would participate if given another chance.
Wooster says future programs would use additional communications channels, such as school campaigns and mass media, in an attempt to reach a participation rate that matches that of the community’s recycling rate.
Beyond the challenge of effective communications, however, Wooster says the program was a success and similar programs will be added to Dow’s sustainability initiatives.
“We were very pleased,” he says. “We were able to test what we thought might be the major bottlenecks, and so we proved that each of the major steps was workable and feasible and could work with existing infrastructure.”
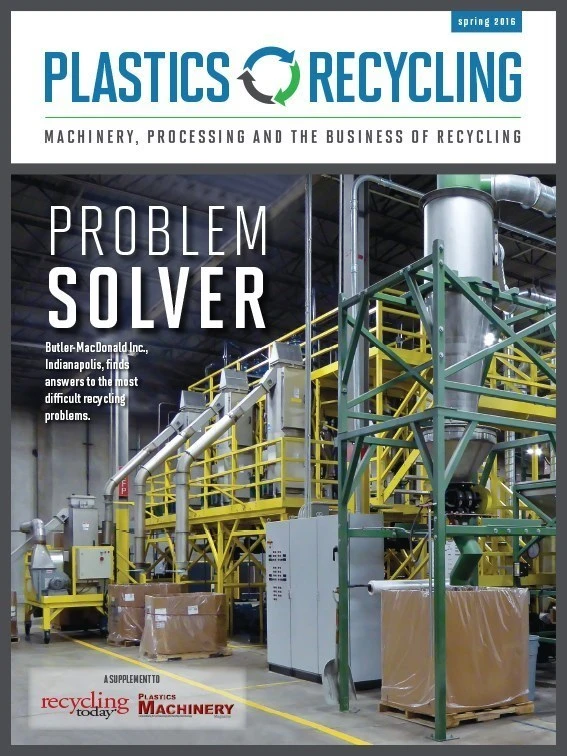
Explore the April 2016 Plastics Recycling Magazine Issue
Check out more from this issue and find your next story to read.
Latest from Recycling Today
- APR, RecyClass release partnership progress report
- Clearpoint Recycling, Enviroo sign PET supply contract
- Invista expanding ISCC Plus certification program
- Redwood partnership targets recycling of medium-format batteries
- Enfinite forms Hazardous & Specialty Waste Management Council
- Combined DRS, EPR legislation introduced in Rhode Island
- Eureka Recycling starts up newly upgraded MRF
- Reconomy Close the Gap campaign highlights need for circularity