
Aluminum is the final product of mined bauxite. An energy-intensive process refines bauxite into alumina, and even more power is required to refine alumina to produce aluminum in potlines across the world’s primary aluminum smelters. While energy costs always have been a factor in a smelter’s operating profits, a recent surge in the price of electricity has brought this previously nominal cost to the forefront.
Where it all began
An approximate timeline of the power crisis points to Rio Tinto’s New Zealand Aluminium Smelter (NZAS) being the first major smelter where operations were threatened by the cost of power. NZAS owns and controls the Tiwai Point smelter. Well before the global aluminum industry began grappling with the exorbitant energy costs, Tiwai suffered a loss of $29 million in 2019 related to the rising cost of power in the island nation. This forced Rio Tinto to question the viability of keeping the smelter running, its premise being that while an annual capacity of roughly 350,000 metric tons is considerable, none of it matters if no money can be made.
Soon after the COVID-19 pandemic broke out across Oceania in 2020, production was further hindered by absenteeism. Adding fuel to the fire, London Metal Exchange (LME) Aluminium prices dropped by 15 percent to reach $1,791 per metric ton. The smelter’s management did not see a silver lining in the near term. As a result, NZAS declared it would shut down in 2021 as it was no longer economically viable. Over the past two years, the government has stepped in with aid to secure reasonably priced power until 2024. That said, a new dip in global aluminum demand and prices arising from recessionary pressures continues to burden profitability at NZAS.
Where we are now
Asia and Oceania. It has been two years since the NZAS crisis, and it seems that the situation at Tiwai Point was a harbinger of the acute energy crisis being faced by the global aluminum industry today. In 2022, several primary smelters have had to curb production capacity or shut down in some cases, simply because the electricity it takes to make aluminum cannot be sourced at a viable price.
Take the example of China’s aluminum smelters in the second half of 2021. After the China-Australia trade war broke out, coal supplies began to run dry, and the Chinese government was forced to ration power, especially at large consumers such as steel mills and aluminum smelters. Therefore, several smelters either slashed capacity or decided to relocate to Yunnan province where hydropower meant no restrictions on electricity supply. However, this move meant that for around six months China reportedly lost between 1.5 million to 2 million metric tons of primary aluminum production capacity. Today, the country has completed tweaking its smelters’ locations and power allocations and restored most of this lost capacity. Still, while China, the world’s largest producer of primary aluminum, sorted out its domestic issues, a larger storm was brewing in the West.
Europe. Some well-documented examples in Europe are the San Ciprian, Slovalco and Trimet smelters that were forced to relook at their operations in light of the high energy costs.
Pittsburgh-based Alcoa, a giant in the aluminum world with multiple smelters across each continent, was the first to acknowledge the issue of high energy prices in Europe. The company’s San Ciprian smelter in Spain was idled in December 2021 because of this issue, which was only exacerbated by a tussle with local labor unions. San Ciprian is one of the largest smelters in Europe, with installed capacity of 228,000 metric tons per year. At the time of publication, Alcoa was planning to reopen the San Ciprian smelter in 2024, subject to a competitively priced power agreement with the region’s electricity provider Greenalia.
Norway-based Norsk Hydro owns Slovalco, the largest aluminum smelter in Slovakia, capable of producing 175,000 metric tons of primary aluminum each year when operated at full scale. In February, rising electricity prices forced Hydro to make some tough decisions at Slovalco. It chose to idle potlines gradually, losing 20 percent, 40 percent and finally 60 percent of its output capacity. In May, Hydro disclosed that it was contemplating a full closure if issues with profitability persist. In August, Hydro said it would terminate production at the site; however, the casthouse in Slovalco will continue its recycling operation.
Germany’s Trimet Aluminium decided to idle half the potlines at three of its five smelters in March because of surging power costs, namely at Essen, with an annual output of 165,000 metric tons, Hamburg with 135,000 metric tons and Voerde with 95,000 metric tons in capacity. Effectively, this move wiped out close to 200,000 metric tons from Western Europe’s primary aluminum supply chain. Here, profitability also was affected by the lack of alumina imports from Russia after the invasion of Ukraine and the sanctions that followed.
These curtailments, compounded by several more smelters decreasing capacity, led to 650,000 metric tons in primary aluminum-making capacity losses across Europe as of July, according to estimates by Bank of America. However, Brussels- based European Aluminium has indicated that the actual losses exceed 1.1 million metric tons.

North America. Primary aluminum production is dominated by a select few companies in the U.S. One of them is Century Aluminum, with a nameplate production capacity that exceeds 1 million metric tons. While electricity has never been a meager cost for smelters in the U.S., Century seemed to have solved this issue for a while. However, its struggle with local power provider Santee Cooper in South Carolina was public knowledge. In June, Century issued a Worker Adjustment and Retraining Notification (WARN) notice, stating that about 600 workers at the Hawesville smelter in Kentucky are being temporarily laid off. Operations are being curtailed entirely for a capacity loss of 250,000 metric tons.
Alcoa faced similar issues and decided to idle one of its five smelting lines at Warrick, Indiana, cutting the plant’s capacity by 52,000 metric tons. In the same city, Kaiser Aluminum, which had purchased the Warrick rolling mill from Alcoa in 2021, noted it will have to either delay or cancel deliveries of its rolled products by 30 percent to 40 percent from the lack of magnesium to alloy. This mill is now operating at 50 percent of its 310,000 metric tons annual production capacity.
How did all of this happen?
Electricity prices did not jump overnight but rose steadily since 2020. The story has two sides, one man-made and the other natural, but they are interlinked. The push for lower carbon emissions and, in time, cutting carbon footprints altogether is a major reason for this whole mess.
In the past decade, all base metal industries—steel, aluminum, copper and others—have been forced to lower their energy consumption and environmental impact through new environmental, social and governance (ESG) protocols.
Moreover, the EU signed and passed the European Climate Pact as part of its involvement in the UN Climate Change Conference in Paris. Since then, it continually has cracked down on industries with a large carbon footprint and devised a Carbon Border Adjustment Mechanism, or the carbon tax.
This duty was levied on all manufacturers and producers on its radar by placing surcharges on electricity. However, in time, this surcharge has begun to outweigh the actual retail prices for energy in the continent. This was evident in the case of Slovalco, which continues to negotiate with its national government to compensate for the tax in the form of subsidies.
Moreover, the Russia-Ukraine war has created a shortage of crude oil across the West, most evidently in Germany. This not only has increased the cost of power but also the cost of freight and trucking, spurring major inflationary pressure on the global economy.
A defining example of this trend was witnessed in July. Aluminium Romania (Alro) shut one of its alumina refineries as it couldn’t afford the cost of electricity and natural gas. The price of electricity surged eightfold from 60 euros ($61) per megawatt hour in Q1 2021 to a projected 500 euros ($509) per megawatt hour for Q4 2022. Meanwhile, natural gas prices multiplied tenfold to 18 euros ($18.32) per megawatt hour to 180 euros ($183.25) per megawatt hour in the same period under comparison.
Alro indicated that it was no longer profitable to keep its operations going. Therefore, it has idled temporarily for at least seven months to monitor and evaluate the situation.
The Climate Pact urged companies to use renewable energy sources and rebuke fossil fuels. Strained by the carbon tax, most companies agreed and began signing contracts for hydro, solar, geothermal and wind power.
Some companies in North America also have followed suit. However, renewable energy is nascent, and solutions for issues like droughts, cloudy days and a change in overhead winds are yet to be found for renewable sources such as hydropower, solar energy and wind farms.

How can recycling help?
Still, a silver lining remains on the horizon. It is common knowledge that recycling aluminum to make the primary metal uses 5 percent of the power needed to refine aluminum from bauxite. Similarly, the carbon footprint of recycled aluminum is minute when compared with primary aluminum. Bigger aluminum makers, already aware of the benefits of recycled aluminum, have invested vast sums in recycling infrastructure. Take Novelis, the world’s largest aluminum recycler, for example. The company uses around 57 percent recycled content as feedstock and produced nearly 1 million metric tons of rolled and extruded aluminum products in FY2022 (ending March 31, 2022).
Hydro also has various remelt cast and extrusion facilities in the U.S. and Europe, so does Alcoa. Both these companies have various product lines that guarantee a low-carbon footprint, well below the industry standard of 4 tons of CO2 per ton of aluminum. In fact, Alcoa is working on a new patented method of recycling called Astraea, wherein it will be able to process postconsumer scrap into a product that is above the primary aluminum production standard.
In this method, Alcoa will recycle shredded aluminum scrap from end-of-life cars, referred to in the industry as zorba, into P0101 (99.998 percent purity) which is considered more valuable than P1020 (primary aluminum, 99.7 percent purity). Once perfected, this method of recycling could revolutionize the aluminum industry.
Lastly, recycling also is a saving grace in the case of depletion of bauxite resources worldwide. Today, 75 percent of all the aluminum ever produced has been reintroduced into the supply chain through recycling. It also can solve the disparity of feedstock availability in different parts of the world.
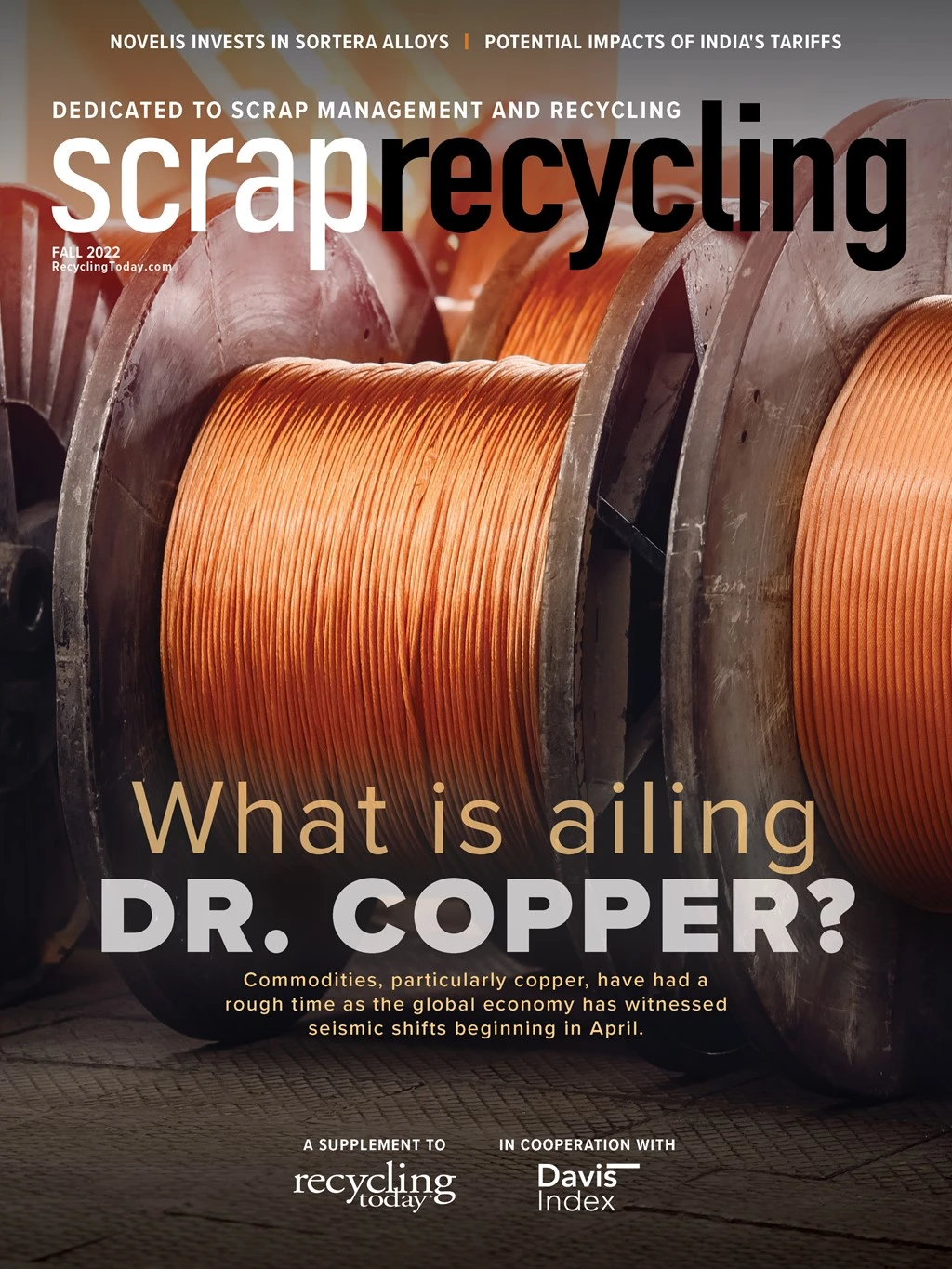
Explore the Fall 2022 Scrap Recycling Issue
Check out more from this issue and find your next story to read.
Latest from Recycling Today
- Steel Dynamics cites favorable conditions in Q1
- Hydro starts up construction in Spain
- Green Cubes unveils forklift battery line
- Rebar association points to trade turmoil
- LumiCup offers single-use plastic alternative
- European project yields recycled-content ABS
- ICM to host colocated events in Shanghai
- Astera runs into NIMBY concerns in Colorado