
Once the leadership team at Sterling, Virginia-based Potomac Metals Inc. (PMI) made the decision to expand its wire and cable processing capabilities, it was eager to have a system up and running as soon as feasible.
PMI Vice President Eric Zwilsky says the company’s search for technology quickly led the firm to Buffalo, New York-based Wendt Corp., which is the North American distributor of wire processing equipment made by France-based MTB Recycling.
By the time the calendar flipped to 2018, PMI, Wendt Corp. and MTB had completed what they refer to as a brief installation process, and the family-owned scrap company was ready to produce market-ready copper chops from material drawn from its network of seven mid-Atlantic region recycling facilities.
Space and time dimensions
_fmt.png)
In seeking a way to enter the wire chopping market quickly, Zwilsky says PMI judged the Cable Box produced by MTB to be “a plug-and-process model for us with very little site prep [needed].”
David Siejka, MTB business development manager for Wendt Corp., says the ease of installation and operation is one of the key selling points of the Cable Box. “Cable Box offers a plug-and-run solution that greatly reduces installation and site infrastructure costs,” he comments.
With diverse processing operations already taking place at its flagship Sterling, Virginia, facility, PMI could allot only a certain amount of space for wire processing, Siejka says. “Given that Potomac already had a building and a defined space where they wanted to put the chopping line, the smaller footprint of the Cable Box offered another advantage,” he says.
The smaller footprint also extends in the height dimension, Zwilsky notes. “We run our Cable Box completely indoors and are limited by the ceiling heights. We found [it] to offer the lowest profile wire chopper to meet our processing needs.”
Operating its new processing system involves deploying people at each end of the processing line, according to Zwilsky. “It takes us two to three employees to operate the Cable Box. One employee operates a material handler to feed the machine wire, while the other operator(s) check the flow off the vibration/separation tables and swap out boxes and hoppers of chop and plastic as needed.”
Like any size-reduction machine, the Cable Box has wear parts to be monitored and replaced and other necessary maintenance tasks stemming from ongoing metal-on-metal contact.
“The majority of the maintenance that needs to be done is for wear parts in the BDR model shredder and BAT model granulators,” Siejka says, referring to size-reduction machines found within the MTB Cable Box. He says those tasks include “replacing the grates in these machines when they become worn, flipping blades when they become worn, replacing the blades after all four sides have been used and setting the gap between the fixed blades and mobile blades.”
After four months of operation, Zwilsky says PMI has found that it flips or swaps its blades “approximately every 250 to 300 operating hours.” Other maintenance or operations tasks Zwilsky lists include the adjustment of tables, which is needed as input material and speed changes are made. “We adjust knives and blow out filters daily [and conduct] screen swaps as we change the input material.”
The goal of nearly all Cable Box maintenance, Siejka says, “is to ensure the machine is making clean cuts on the material.”
Clean, market-ready material as an end product is the goal PMI has pursued, and Zwilsky says the early results are promising.
Aiming for No. 1

“When we first started discussing the Cable Box with Potomac, the goal was to provide a solution that would be capable of chopping a high-quality No. 1 wire package,” Wendt Corp.’s Siejka says.
As of early May 2018, Zwilsky says, “PMI is currently processing high-grade No.1 wire, 65 percent [copper] recovery and up.” He says the MTB Cable Box has been able to process 6,000 pounds of input material per hour with material in that 65 percent copper-content range.
Zwilsky adds that the company has been able to process up to 14,000 pounds per hour of material that has 90 percent or more copper content.
“We are producing bare bright chops—heavies and fines,” he continues. “With inputting good wire, we are producing a good chop product [while using] no other equipment,” he says of the Cable Box.
PMI has been so encouraged by the results, Zwilsky says the company is likely to start running other materials through the Cable Box as it becomes convinced it can be done profitably.
“We also look to process high-grade No. 2 wire (70 percent-plus metal content), communication wire (category five twisted wire computer cable) and insulated aluminum in the coming months,” Zwilsky says. The activities should lead to the production of “tin plate chop (running tin plate wire) and electrical conductor chop (running insulated aluminum),” he adds.
Siejka says the Cable Box is the right piece of equipment for PMI’s aspirations. “The Cable Box offers versatility, allowing Potomac to process their No. 1 copper wire packages with ease, yet giving them the flexibility to process No. 2 wire, category five, aluminum and other types of cables that they may want to process in the future.”
Several months after installing the system, Zwilsky says he is confident PMI made the right decision and chose the correct suppliers. As promised, he says, “The MTB has been plug and play for us.”
In terms of reliability and end product quality, Zwilsky indicates he has been pleased with PMI’s investment in its new processing system. “The Cable Box has been reliable with daily operation since its installation,” he says. “The input and output [volumes] have exceeded our expectations.”
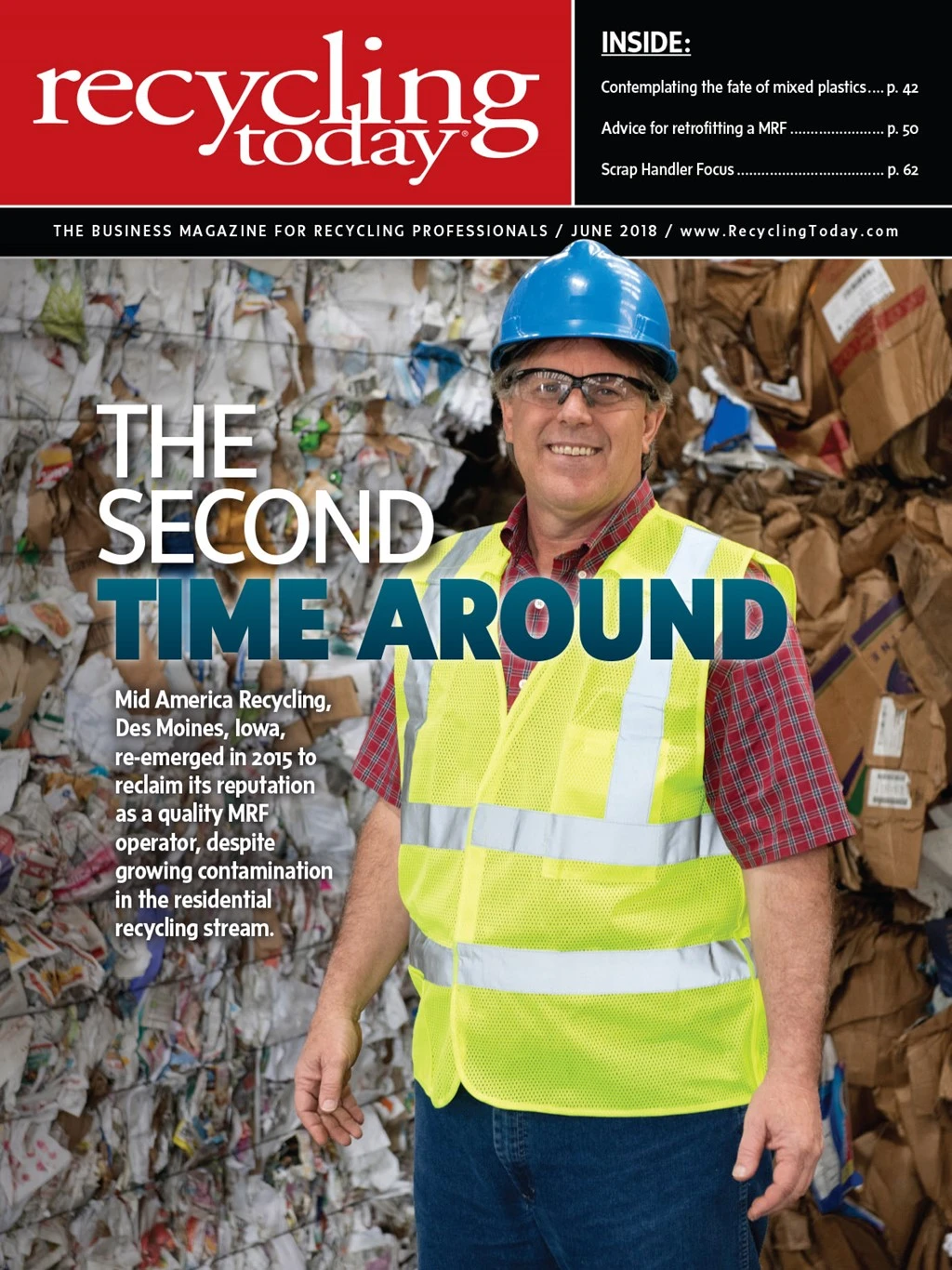
Explore the June 2018 Issue
Check out more from this issue and find your next story to read.
Latest from Recycling Today
- LumiCup offers single-use plastic alternative
- European project yields recycled-content ABS
- ICM to host colocated events in Shanghai
- Astera runs into NIMBY concerns in Colorado
- ReMA opposes European efforts seeking export restrictions for recyclables
- Fresh Perspective: Raj Bagaria
- Saica announces plans for second US site
- Update: Novelis produces first aluminum coil made fully from recycled end-of-life automotive scrap