A panel of speakers at the 2016 Paper & Plastics Recycling Conference, hosted by the Recycling Today Media Group Oct. 19-21 in Chicago, addressed opportunities and challenges associated with recycling postindustrial plastics.
“Postindustrial recycling has a strong origin in tolling,” said Kevin Cronin of Ultra-Poly Corp., Portland, Pennsylvania, referring to companies with specialized equipment that process raw materials for another company, either on-site or off-site.
One way Ultra-Poly offers these services is through two embedded operations at manufacturing facilities, which provide logistics savings as well as help to ensure product quality and consistency, Cronin said.

Brokers, or recyclers without processing assets, are an important part in the recycling chain, he added, noting their role in consolidating materials.
The services asset-based recyclers provide, on the other hand, can range from regrinding to creating specified compounds, as Ultra-Poly does.
However, a potential downside for reprocessors and brokers alike, Cronin said, is that “captive recovery operations” are increasing, reducing the amount of scrap available on the general market. “Increased internal usage can threaten material availability,” he added.
“The marketplace is very competitive,” Cronin said. “There is no more low-hanging fruit.”
Neil Gloger of InterGroup International, Euclid, Ohio, discussed how China’s Operation Green Fence changed the dynamics of the plastics recycling industry. As an example, he said that his company is now being charged to dispose of material it used to be able to sell for 5 cents to 7 cents per pound.
Gloger said InterGroup International had trouble achieving profitability in its reprocessing operations. Therefore, the company decided to leave the reprocessing business in favor of brokerage, consolidating and repacking material. However, InterGroup uses third-party processors when necessary.
Unlike paper recyclers, Gloger said plastics recyclers do not have a reliable source of pricing, such as RISI’s PPW Yellow Sheet, as a reference point for their transactions. “Every deal is a negotiation,” he said. “There is no benefit of a market indicator price.”
Instead, he said, plastics recyclers must use a percentage of the spot prime price to help determine pricing for their material.
“With the end of the commodity super cycle we need to rethink our business model,” Gloger said, adding that the company only purchases material based in purchase orders these days. He said that could be the case permanently or “at least for a long time.”
Vince Gupta of Prime Plastic Products, headquartered in San Diego, said that plastics recycling has “more drama” than paper recycling. He said it requires more space to accumulate the wide variety of plastics available on the market and can involve more secondary operations.
It also is important to know your materials and their potential contaminants, Gupta said. “Knowing what your buyers want is the most important spec,” he added.
Regarding pricing, he said supply and demand are the biggest factors at play.
“Quality plastics do have domestic and export markets,” Gupta said.
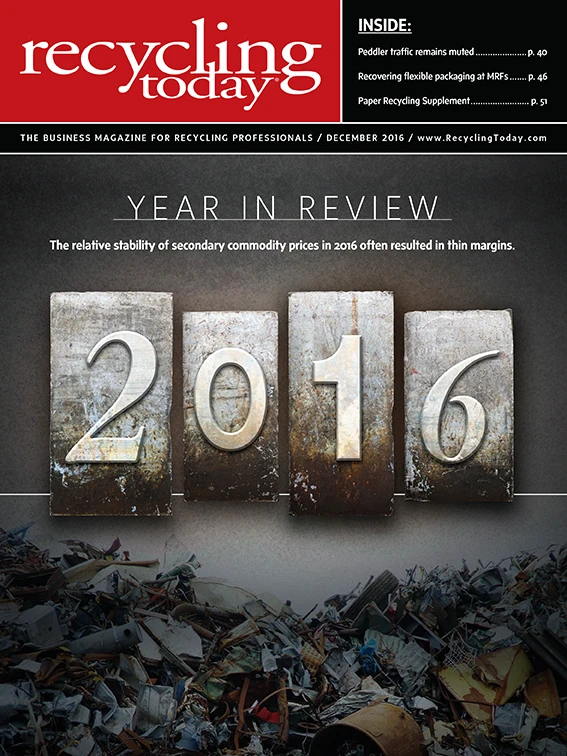
Explore the December 2016 Issue
Check out more from this issue and find your next story to read.
Latest from Recycling Today
- Two factors raise ferrous export questions in April
- Analyst: Scrap imbalance lost amid copper’s critical status
- AF&PA report shows decrease in packaging paper shipments
- GreenMantra names new CEO
- Agilyx says Styrenyx technology reduces carbon footprint in styrene production
- SABIC’s Trucircle PE used for greenhouse roofing
- Hydro to add wire rod casthouse in Norway
- Hindalco to invest in copper, aluminum business in India