
Recycling municipal solid waste (MSW) clearly provides numerous societal and environmental benefits, including conserving natural resources, decreasing the amount of material sent to landfills and reducing pollution. If done efficiently, some worthwhile financial rewards also can be realized.
Although the recycling rate in the United States has increased from less than 7 percent in the 1960s to 32 percent as of 2018, according to data from the U.S. Environmental Protection Agency (EPA), progress has stalled over the past decade. By many measures, the process on a national scale has fallen short of its potential and intentions.
The reasons for the stalled growth are complex and far-reaching.
For one, waste has negative value because its disposal costs money. However, if single-stream collected recyclables are separated into homogenous groups of paper, plastic and metal, for example, with minimal contamination, those materials now have value as commodities.
It takes great effort to separate that material, however, so it must be done efficiently and cost-effectively.
Second, material recovery facilities (MRFs) that process material for recycling have difficulty hiring and retaining employees to perform the physically stressful and potentially hazardous work of manual separation.
Making recycling profitable
To streamline MRF operations, National Recovery Technologies (NRT), Nashville, Tennessee, developed a robotically automated sorting system. Using vision and artificial intelligence (AI), the NRT system is designed to improve productivity while removing people from hazardous areas of the sorting process.
NRT was founded in 1981 and, in 2012, was acquired by Eugene, Oregon-based Bulk Handling Systems (BHS), an engineering and manufacturing company that has supplied MRFs worldwide.
NRT’s system uses Max-AI technology, a neural network-based AI platform used to identify objects in the material stream. The Max-AI vision system can be used as a stand-alone detection device, integrated with robotics or combined with near-infrared (NIR) optical sorting units to further improve a MRF’s material recovery, operational efficiency, system optimization and maintenance.
In early 2017, NRT installed its first industrial robot integrated with the Max-AI technology and has installed more than 225 robotic sorting units since across more than 75 locations.
Committing to robots
In 2021, NRT installed 23 IRB Flex-Picker delta robots from Switzerland-based ABB equipped with Max-AI at a Riverside, California, MRF operated by Burrtec, a Fontana, California-based independent disposal company with facilities across southern California. The facilities are of varying ages with equipment of varying levels of sophistication and condition.
The 15-year-old Riverside MRF needed to be upgraded, so Burrtec approached BHS seeking a proposal on how to improve the facility. BHS developed a plan to improve productivity and worked with NRT to determine if Max-AI-integrated robots were a viable option for what Burr-tec wanted to accomplish.
“The technology seemed to have advanced enough to be worth considering,” says Richard Crockett, director of MRF and transfer operations at Burrtec.
“NRT did some testing by putting vision systems on our MRF lines to develop a baseline of the material we were processing and to see if the AI-enabled robots could handle it. The results were very positive, so we signed off on the Max-AI system and the 23 sorting robots as a primary technology component of the project. Prior to the installation of the robots, all the waste sorting at the Riverside facility was performed manually.”
BHS also manufactured and commissioned many of the nonrobotic components installed at the Riverside MRF, including a significant portion of the new structures, conveyors and motors, while NRT worked on the technology package—the design, specification, installation and programming of the optical sorters, robots, Max-AI vision systems and the related system controls.

Operational overview
MSW is brought to the Riverside MRF and separated using a series of conveyors to route material through a multistep sorting process.
Material first passes through a series of disc screens that separates paper and containers from fines, then screens further separates two-dimensional material from three-dimensional material. Optical sorters then perform a secondary sort, using blasts of air to further separate material coming down the conveyors, routing material in one of two channels, depending on type.
The material then passes through stations comprised of AI-enabled robotic sorters that, depending on the nature of the stream, either remove contamination from a material stream bound for recycling or remove recyclables from material bound for landfill. The robots conduct a final quality control sort at lower throughput, providing an important final cleanse to assure materials are separated into homogenous streams.
The recycle-grade material, once sorted into commodity groups, is bunkered and baled for shipment to market.
Robots and material processing
The Max-AI-equipped FlexPicker robots are all labeled “AQC,” or autonomous quality control. They are deployed in groups of one, two or four robots, which are noted with designations of AQC-1, AQC-2 and dual ACQ-2, and are allocated based on how many robots are needed to handle the tonnage of a particular stream.
“The role of the AQC robots is to do what a human does in terms of ensuring that material streams are as free of contaminants as possible, or any valuable commodities in a material stream bound for a landfill are recovered,” NRT Chief Technology Officer Thomas Brooks says.
“The speed of the robot conveyors is set at 200 feet per minute, the conventional speed for manual sorters in the U.S. If you have a lot of material coming down, you don’t slow down the belt, you add robots. If there are 20, 30, 40 tons of material per hour, you design the system to handle it within the parameters of the budget, physical space, etc.”
The FlexPicker robots at the Riverside MRF are deployed as follows:
- Four Dual AQC-2s, or 16 robots, perform final quality control on the mixed paper stream spread across four conveyors, picking higher-value brown fiber and grouping it with cardboard as well as picking out plastic containers and contaminants missed by the previous processes.
- Three robot clusters sort contaminants from various plastic container streams. The material on these lines then goes beneath a magnet that pulls any ferrous material and an eddy current that picks out any aluminum.
- One AQC-2 is deployed on the high-density polyethylene (HDPE) plastic container stream, and one AQC-2 is deployed on the general plastic container presort stream.
- One AQC-1 is located on the polyethylene terephthalate (PET) container stream, one AQC-1 is deployed on the aluminum stream and a final AQC-1 is positioned on the residue recovery stream, taking a final pass at recovering recyclables.
Once a robot picks material from a stream, it drops it into a series of chutes on the side of the conveyors leading to either a bunker or a conveyor that carries it away from the chutes.
If the robots are picking commodities from the mixed material stream, that material is routed to be recycled with its appropriate material group. If the robots are picking misplaced material from a recycling line for a specific material, such as removing textiles from the PET line, that material also is routed to be recycled with its appropriate material group. If picking contaminates from the material stream, that material typically is routed to a holding area bound for landfill.
Developing a partnership
As NRT was developing its Max-AI technology, the company vetted a number of original equipment manufacturers before deciding on ABB.
“We were looking for a robotic supplier that could give us three core pieces, and ABB checked all the necessary boxes,” NRT’s Brooks says. “The most important is a global service reach, as we have installations on five continents. We are a small and lean operation, so the global support is critical.
“A close second is engineering support and ingenuity on the front end, and a big part of that is ABB’s RobotStudio design and programming software,” he continues. “Diversity of product line is also important. The Burrtec facility has all delta robots, but many of our other MRF installations utilize six-axis articulated arm robots and collaborative robots.”
RobotStudio provides simulations, using real robot programs and configuration files identical to those used on the facility floor. With RobotStudio, Brooks and his team were able to design an optimal AQC robot layout and verify its performance before integrating the robots into a particular operation.
To achieve scalability, NRT’s approach is to build a standard product and carry that forward to the material stream. The product might need some additional tailoring or adjustments made when it gets deployed in the field, but the core offering is standardized.
With RobotStudio, NRT is able to simulate the design and performance of a complex robot installation before an end user commits to making the capital investment. With the ability to test various design and set-up scenarios, NRT can determine the optimal system layout in addition to how well the robots can access and handle the streams of nonuniform materials.
“We use RobotStudio to basically test all the different fringe cases and setups and everything else,” Brooks says. “Even to the point of driving pick rates and dealing with kinematics in order to get close to the belt, it all gets modeled in the development stage of the system, rather than at the deployment stage.
“We leveraged RobotStudio to build an overlay application to simulate the variability of waste as it comes down the stream,” he continues. “We have used the overlay extensively to tie in the vision systems, and to map out the kinematic models of how to move waste from points A to B.”

The technology behind Max-AI
Max-AI is driven by a visual identification system (VIS) and a multi-layered neural network that identifies more than 256 categories of material. The neural network recognizes an object by millions of details inherent to a specific material and can infer differences in features to detect objects correctly.
The VIS camera is stationed above the conveyor and, ideally, the material passing below on the conveyor is singulated to a degree that the camera can get a clear picture. Different neural networks have been developed for different applications, so the one used on the robots is not the same as used on the high-speed units connected to the optical sorters.
“AI is really the eyes and brains of the operation,” Brooks says. “Just as a human sees something and uses its brain to take appropriate action with its hands, the robots sees, thinks and acts in much the same way. The VIS is the seeing, with the support of the neural network, the AI is thinking, and the robot is taking the action.”
Efficiency and environmental sustainability
The Riverside facility renovation has improved Burrtec’s efficiency, not only in labor savings and safety but also in the value of commodities the MRF is recovering.
“With respect to the efficiency of this new facility in Riverside, we get the benefit of a higher throughput from the system and an increased ability to process material,” Crockett says. “Prior to the upgrade, we were running our system anywhere from 20 to 22 tons per hour, and now we are doing 28 to 30 tons per hour.”
No employees were displaced as a result of the project, as Burrtec says it has always worked to “right-size” its organization. Employees who previously performed manual sorting were moved to other positions within the organization.
“We now have a more efficient operation from a labor standpoint,” says Trevor Scrogins, vice president of operations at Burrtec. “The robots come to work every day, and they’re not as susceptible to some of the things that could be found in the recyclables that could injure or sicken a worker, so there’s some definite benefits with the robots, believe me.”
From an environmental standpoint, diverting recyclable commodities from landfills positively contributes to material circularity and environmental sustainability.
“People may challenge how effective recycling is, but nobody is against it,” Brooks says. “You read stories where only 10 percent of plastic is being recycled, which may be true, but the denominator keeps getting bigger and, with more automation, I think that percentage will improve, and operations like ours will continue to make positive contributions to a more environmentally healthy society.”
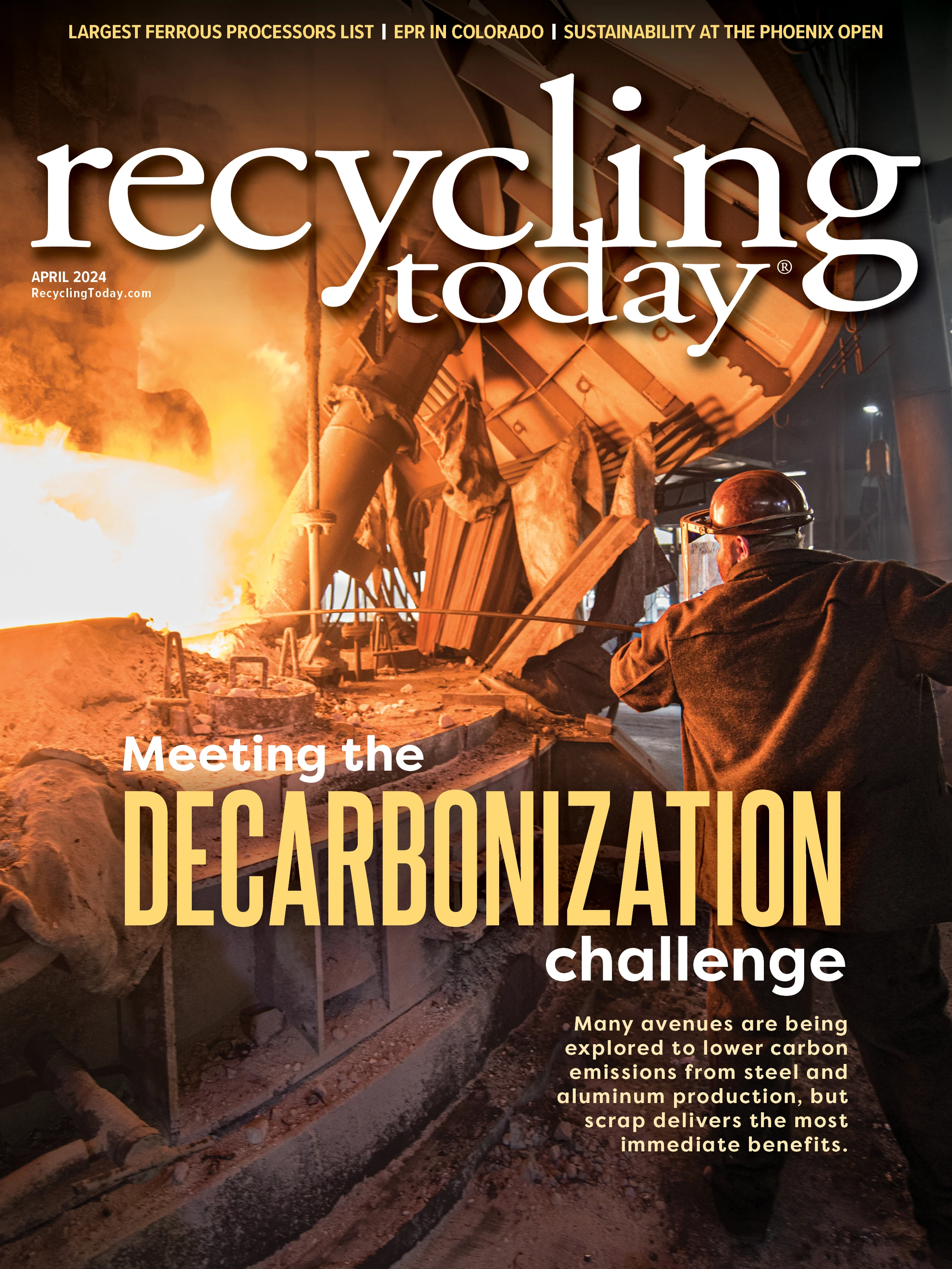
Explore the April 2024 Issue
Check out more from this issue and find your next story to read.
Latest from Recycling Today
- Joe Ursuy elected to NWRA Hall of Fame
- RRS adds to ownership team
- S3 Recycling Solutions acquires Electronics Recycling Solutions
- Nextek, Coveris to recycle food-grade plastic film
- Recyclekaro expands recycling capacity
- USTR hears comments on port fee proposal
- C&D World 2025 hits record attendance and exhibitor numbers
- Denali now offers mobile depackaging service