There are several factors to consider when buying a portable crushing unit.
The recycling of concrete and asphalt remains a viable, growing industry, especially when done at the construction or demolition site. Many people are considering new processing plants to join that market.
Four key factors to consider when selecting a road-portable concrete/asphalt recycling plant are efficiency, mobility, durability and maintenance. These factors determine the profit/payback expectations from recycling operations in a proposed recycling operation.
Types of Plants
The three main crusher types in concrete/asphalt recycling are horizontal impactors, jaws, and cones.
A horizontal impactor can have a large reduction ratio (as much as 30-to-1 in closed circuit), and may not require a secondary crusher to process material. In addition, an impactor can give more control over product size.
For minus 1-1/2-inch products, some material will need to be run through the impactor twice via a return conveyor going from the screen discharge to the crusher intake hopper. New, uncrushed material can be fed into the hopper at the same time. For minus one-inch and smaller products, a secondary impactor is usually used to relieve loading on the primary impactor and maintain maximum volume of uninterrupted material flow. Some impactors have been adapted for primary crushing in recycling applications by simply opening the crusher inlet to accept large materials. Some of these units may not hold up as well in recycling operations.
One advantage of having a single-stage crushing system versus a two-stage system can be the quickness of set up. While the two-stage system may bring higher production rates, especially to make smaller-sized products, it will usually take longer and be more expensive to set up and tear down than a single-stage system. The size of jobs to be processed can be an important factor that determines whether a one or two-stage plant makes sense for a buyer.
Another important factor to consider is the type of apron control on the impact crusher. Conventional aprons use their own weight plus springs to counteract crushing forces. Simplicity is the system’s advantage.
However, several impactors have a hydraulic apron control on them. Some equipment makers claim the hydraulically controlled impactor has a 15 percent greater production capacity than conventional impactors of the same size, and that they maintain good product size control.
The hydraulically controlled design allows the apron to retract in a smooth, controlled manner and return to its present position automatically. Further, the product can be more uniform since the desired impact gap setting will remain constant and will not open up as a result of material pressure build-up.
Using a vibrating feeder under the crusher can help protect the discharge conveyor belt. Discharging crushed materials directly onto the conveyor can cause undue belt wear and damage.
A powerful electromagnetic separator should be mounted atop the discharge conveyor to pull ferrous tramp metals from the crushed materials. The magnet can be mounted in line with the discharge conveyor for efficient material flow and to prevent clogging that can be caused by perpendicular mounting.
Most often, the magnet is mounted high enough on the discharge conveyor so that separated metals can be deposited directly into a truck or dumpster below to eliminate the extra handling required if metals are dumped on the ground. To crush demolition debris, the system should include such options as picking stations to remove certain loose materials and an air classifier for wood and paper removal.
Mobility is crucial. Most contractors prefer to make sure the crushing plant can be moved within the highway weight laws of the states the system will be working in. In many states, the crusher and feed hopper may have to be transported on separate chassis to meet weight requirements. If so, a crushing plant with a skid-on hopper that goes easily from flatbed trailer to the crusher chassis with the help of a block-and-tackle and front-end loader can make sense. Someplants require a crane for set up, which can take longer and cost more.
It is worthwhile for buyers to learn the set-up and tear-down times of the systems they are considering. Obviously, quicker is better, but learn about the different ways each piece of machinery sets up. Both hydraulic jacks and hydraulic legs can be used to set up the plant. Jacks support the plant until braces or blocks can be put in place. Hydraulic legs can enable faster set-up and provide support with precise and accurate height adjustments.
Power Factor
Power for the crushing plant can be supplied by a diesel engine or electric motor. Advocates of diesel engines say it is easier to regulate the crusher speed according to material types and product sizes when using diesel power.
Most electric motors run at one constant speed, and changes can require a power shut down and a change of the V-belt pulley sheaves. Diesel power puts constant noise at the operator station, and dust from crushing can damage the engine. The electric motor is quiet and basically unaffected by dust. In recent years the trend has been toward electric-powered crushing plants run from a generator or line power.
An important first step in developing a plan of attack for a new recycling system is, of course, market evaluation. Questions to be answered include:
• What types and sizes of materials will be processed? Concrete and asphalt rubble? C&D debris? Stone and boulders? Limestone? (Natural aggregate can be a profitable ancillary market for recyclers.)
• How much rebar and wire mesh will be in the materials to be crushed, as well as contaminants, such as wood and paper?
• How many tons-per-hour of capacity is needed?
Then choose a crushing/screening operation based on what is needed. If a manufacturer’s standard plant fits the needs, fine; but remember that the sometimes extra (often very little extra) cost of a plant customized to the market’s special needs can pay for itself many times over.
Work with the equipment supplier to determine the optimum size of the crushing plant and other components, based on the material mix, tons-per-hour requirements and other individual needs. An oversized plant can be wasteful in terms of the initial cost, and to a lesser extent, operating costs. But an undersized plant can be a disaster in terms of excessive feed preparation, inadequate production capacity, high downtime and lost profits.
Downtime is the biggest negative influence affecting profitability. When comparing comparable processing equipment from different manufacturers, it is important to know each manufacturer’s track record. See their equipment in operation and talk with their customers before buying any recycling plant. It is preferable to talk with customers who have operated their plants for some time, because major crusher problems may not surface for as much as a year after start-up.
Information for this article was provided by Grasan, Mansfield, OH.
Get curated news on YOUR industry.
Enter your email to receive our newsletters.
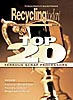
Explore the March 2002 Issue
Check out more from this issue and find your next story to read.
Latest from Recycling Today
- Hitachi forms new executive team for the Americas
- Southwire joins Vinyl Sustainability Council
- Panasonic, Sumitimo cooperate on battery materials recycling in Japan
- Open End Auto Tie Balers in stock, ready to ship
- Reconomy names new chief financial officer
- ICIS says rPET incentives remain weak
- New Jersey officials award $16.2M in annual recycling, waste reduction grants
- Linder Industrial Machinery announces leadership changes