Kinder Morgan needed a sizable and efficient material handler to unload incoming scrap from barges for the new SeverCorr steel mill.
The SeverCorr mill is one of North America’s newest steelmaking facilities, and it is being built in Columbus, Miss., about 8 miles from the Tennessee-Tombigbee waterway. (See "The Russian Bear Roars," in the September 2007 edition of Recycling Today.)
The SeverCorr plant will have the capacity to produce some 1.5 million tons annually of a variety of steel products, including hot-roll, hot-roll P&O (pickled and oiled), cold-roll and hot-dip galvanized/galvanealed steels.
SUPPLY LINEHouston-based Kinder Morgan is one of North America’s largest energy transportation and storage companies, with more than 37,000 miles of pipelines and 150 terminals for the storage of petroleum products, chemicals and dry-bulk materials, like coal.
The company also operates about 50 transload facilities that transfer product from one mode to another in a just-in-time fashion, helping sellers and buyers of these materials avoid the costs of moving such products into storage.
The nature of Kinder Morgan’s work meant that the team shopping for equipment to be used at the SeverCorr transloading facility had several requirements and strict guidelines in mind.
"We looked carefully at several manufacturers’ equipment, considering each machine from the standpoint of design, construction, reputation, service life and overall operating efficiency and economy, as well as parts and service backup," says Kinder Morgan director of operations and engineering Thomas Ruff Sr.
"Our choice was the E-Crane Series 1500-B, model 11264 high portal mounted on a rail lower," says Ruff. He cites several reasons why this particular configuration was ideal for the SeverCorr application.
"We wanted a hydraulic-electric material handler rather than a diesel-powered machine for economy, quietness and low maintenance," says Ruff. "There were environmental considerations, too."
Ruff and others at Kinder Morgan were familiar with E-Crane’s capabilities from previous experience, which helped them in their decision. "E-Crane wasn’t a difficult choice," he remarks. "We’ve had previous experience operating a similar model E-Crane at an installation in Venezuela for five years now, and it has performed as expected."
READY TO GOKinder Morgan purchased the crane for its Mississippi steel mill application from E-Crane International USA, Galion, Ohio.
That location helps North American customers order specifically tailored machines from E-Crane’s European plant to suit their particular applications. Almost every product E-Crane builds is a custom machine, according to E-Crane International USA.
For example, Kinder Morgan’s new material handler had to be built high enough so trucks could drive under it for
|
"Initially we sat down with the E-Crane people and suppliers of other components for our new facility and brainstormed all kinds of design and construction possibilities," says Ruff. "As far as the E-Crane machine is concerned, we basically told them what we wanted to accomplish, and they basically designed a crane specifically to meet our needs."
Kinder Morgan’s electric crane has an 18.2-ton duty-cycle capacity. It can be equipped with either a grapple, clamshell bucket or magnet with the goal of providing versatility to handle different forms of scrap and raw materials.
The unit includes a quick-change capability to switch between the three different attachments with the goal of causing the company the minimal amount of downtime or interruption in the transloading of the material.
Another feature of the electric crane is a counterweight that is actuated by a hydraulic cylinder so it pivots back and forth on its axis. This movement is transmitted to the stick by means of a rigid connecting rod. The idea, according to E-Crane engineers, is to have the machine nearly always in equilibrium during its working cycle.
Says Ruff, "Our E-Crane uses less power, and its durability and longevity will help keep our costs to a minimum."
The manufacturer has also attempted to use parts and components that are readily available in North America, making things easy for the people responsible for keeping the machines running at their peak efficiency.
"The maintenance is straightforward and we like that it’s compatible with many Caterpillar components, especially for the controls and hydraulics,"
Costly Loads |
Melt shop managers at steel mills throughout the world may well be handling materials with more value in 2008. If prices for pig iron, scrap iron and steel follow the lead of iron ore pricing, 2008 will be another bullish year for sellers of those materials. In early 2008, Brazilian iron ore mining firm Vale announced a 65 percent increase in iron ore prices for product supplied to Japanese steelmakers. Chicago-based steel industry analyst Michelle Applebaum projects that U.S. steel prices will rise not only because of raw materials costs, but also because of low finished steel inventories. "The inventory data supports our view that prices will continue to rise to new heights in the U.S. market as foreign tonnage available to U.S. buyers has been reduced, while pricing for this material has risen dramatically, despite a weaker U.S. economy," Applebaum writes in a recent news alert. Market analysts are also expecting steel prices in Asia and throughout the rest of the world to remain high, as raw materials purchasers for these companies will continue to pay historically high prices for their feedstock. According to a report from Puchasing.com, continued strong demand for steel in China will let steelmakers charge more for their products. Reuters and Bloomberg have reported that major steelmakers in Asia and Europe were expected to increase prices by 5 percent to 10 percent in late winter. |
Additional benefits cited by E-Crane include sufficient reach, height, visibility and load capacity for the big jobs; easy operation with two joysticks in a roomy, air-conditioned cabin; and a monitoring system that provides the operator with machine status reports in real time.
The installation at SeverCorr took place in the second half 2007.
"We have been using the E-Crane at Columbus, Miss., for a short time now, as it’s still in the start-up and testing phase; but we’ve unloaded approximately 15 to 20 barges, and everything looks great," Ruff says.
"We estimate we’ll be able to offload 400 tons per hour, depending on the product. Our new E-Crane can easily handle present loads with no problems, and it gives us extra capacity for growth down the road."
This story was submitted on behalf of E-Crane International USA, Galion, Ohio, www.ecrane-usa.com.
Sponsored Content
Labor that Works
With 25 years of experience, Leadpoint delivers cost-effective workforce solutions tailored to your needs. We handle the recruiting, hiring, training, and onboarding to deliver stable, productive, and safety-focused teams. Our commitment to safety and quality ensures peace of mind with a reliable workforce that helps you achieve your goals.
CHANGING OF THE GUARD |
As operations at the Severstal steel mill in Columbus, Miss., kicked in, the company announced management changes. In early January, Severstal announced that John Correnti, the original CEO of SeverCorr, will be leaving the company. Being ushered into top posts are several executives with ties to Russia’s Severstal organization, now the mill’s majority owner. Among members of the new senior management team appointed by Severstal are: • James Hrusovsky has been appointed CEO of SeverCorr and will be based in Columbus. He was formerly COO of Severstal North America Inc. (SNA), the firm’s overall U.S. division. • Sergei Kuznetsov, CFO of SNA, has been appointed the new CFO of SeverCorr. He will have financial management and reporting responsibilities for both SeverCorr and SNA and will remain based in Dearborn, Mich. Alexey Mordashov, Severstal CEO, says, "John Correnti and his team have been tremendous partners, and we wish them the very best in the future. In a relatively short period, they built from scratch one of the most technologically advanced mills in the steel industry that is strategically located to serve the fast growing Southern region of the United States." In addition to Correnti, a number of other founding senior managers of the mill will be leaving the company as Severstal consolidates the SeverCorr mill with its overall SNA operations. Severstal also will be acquiring ownership interest held by Correnti and other members of SeverCorr’s management team. SeverCorr will continue production ramp-up and its Phase II expansion, with plans to more than double the mill’s output to 3 million metric tons per year. "We’re proud of what we’ve accomplished at SeverCorr and I want to thank everyone who has helped make it possible," says Correnti. "As SeverCorr moves from an entrepreneurial venture into an operating steel mill, it made sense for me and other founding senior managers to transition executive management responsibilities. Severstal was a valuable partner in getting this mill to where it is today." |
Get curated news on YOUR industry.
Enter your email to receive our newsletters.
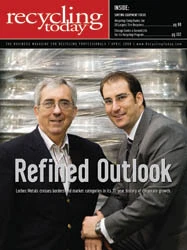
Explore the April 2008 Issue
Check out more from this issue and find your next story to read.
Latest from Recycling Today
- Athens Services terminates contract with San Marino, California
- Partners develop specialty response vehicles for LIB fires
- Sonoco cites OCC shortage for price hike in Europe
- British Steel mill’s future up in the air
- Tomra applies GAINnext AI technology to upgrade wrought aluminum scrap
- Redwood Materials partners with Isuzu Commercial Truck
- The push for more supply
- ReMA PSI Chapter adds 7 members