
Polypropylene (PP) ranks among the world’s most-used polymers. Its end markets include construction, consumer products, electronics and automotive, though
Despite PP’s popularity, the polymer suffers from a low recycling rate compared with some other plastics. However,
Disrupting the status quo
P&G patented (http://google.com/patents/US20170002116?cl=en) its technology for recycling PP in January 2017. The technology was developed in the company’s labs by Dr. John Layman, who works in the Materials Science division in P&G’s corporate research and development organization. P&G’s Global Business Development organization connected the company with Chicago-based Innventure, the parent company of PureCycle Technologies. Innventure has a track record of commercializing technology and building successful companies, says Stephen
The technology removes color and odor, producing a recycled flake with “virgin-like quality,” PureCycle says in a news release announcing the endeavor.
PP is the largest commodity resin that P&G uses,
“To get the volume needed,” he says, “you have to blend colors.” This means much of the available recycled material is in the gray-to-black range. “It’s hard to color that material,”
PureCycle’s technology, with its ability to remove color and odor from recycled PP in addition to decontaminating the material, has the potential to change that.
Introducing the technology
Sikra explains that while plastics recycling is generally a combination of mechanical and physical processes, PureCycle occurs at the molecular level. “It is a novel solvent-based extraction and purification process. No chemical reactions are involved. The solvent can be recycled and reused within the process.”
The process begins with postconsumer flakes of various colors and ends with a clear, odorless, contaminant-free pellet, he says.
Byproducts of the process include dyes and pigments, additives, contaminants and filter media,
“We still, of course, need to do the full life cycle assessment upon scale-up,” he says. “We have predicted numbers right now, but PureCycle is looking to validate those as they start up.”
PureCycle will be looking at the best uses for these byproducts as it commercializes the technology, Sikra adds.
PureCycle Technologies CEO Mike Otworth says the P&G-developed technology has the potential to “change market dynamics for the better” by producing a recycled product that can be used in higher value applications at a cost that is comparable to virgin material.
“Different processes have been tried in the past, and some have failed because the process is so costly, you can’t make the product at a cost the market will bear,” he says. That is not the case with PureCycle, Otworth says, adding that his company intends to sell its PCR “at price parity with virgin resin.”
He describes PureCycle’s technology as “robust,” noting that it can even separate other polymers in the feedstock. “Other resins in the feedstock don’t degrade the PP, they just limit our yield.”
Otworth says the technology has been optimized for PP but potentially could be used to recycle other plastics.
“What will improve the situation for plastics recycling over time will be the ability to make higher value products with recycled material,” he says. “Customers won’t have to make compromises. There will be more consistent demand for feedstock. The breadth of feedstock will be greater. We hope it improves the dynamics of recycling and that potential users will be more willing to use recycled material.”
Otworth points to a recent discussion he had with a representative of a major automotive manufacturer as evidence of this willingness. The man told Otworth that he originally didn’t want to talk with PureCycle because of issues the company has using recycled PP because its applications are appearance and odor sensitive. But, when he heard the company could make recycled PP with the same characteristics as
“It’s quite game-changing and will open up whole new opportunities for recycled material,” Otworth says of the technology.
Scaling up production
P&G licensed the technology to PureCycle Technologies. Otworth says it is an exclusive license, as long as the company meets certain requirements, such as expanding to specified geographies.
PureCycle will begin processing on a small scale in 2018 with a single unit. Otworth says the company will test and evaluate different sources of feedstock and will calibrate the process, with the intention of starting commercial-scale production in 2020. However, he says the initial unit will be used on an ongoing basis to evaluate new sources of feedstock even after commercial production begins.
PureCycle already has offtake agreements with a number of customers, Otworth says.
“We are talking to many about feedstock supply agreements,” he says. “We may even make some investments to control our own feedstock destiny.”
Koch Modular Process Systems (KMPS), Paramus, New Jersey, will be building the system components and delivering them to the Ironton site. KMPS was recommended to PureCycle by Phasex, Andover, Massachusetts, which worked with P&G to design the proof-of-concept systems for the process, Otworth says.
He says PureCycle’s current plans call for constructing nine plants. “The components are built modularly and easily sized by adding additional units,” Otworth adds, noting that gives the company “optimal flexibility” to build plants of different sizes in different locations.
Collaborating and cooperating
The Ironton plant will have 80 million pounds of production capacity, but P&G plans to use only a small portion of that material,
The Association of Plastic Recyclers (APR), Washington, says, it has identified 1 billion pounds of recycled PP demand in North American alone.
Sikra says P&G is working with trade groups and recyclers to learn more about plastics recycling and the issues affecting the industry. “There is a time to compete and a time to collaborate,” he says. “Expanding recycling infrastructure is about collaboration.”
To that end, P&G has been working with Materials Recovery for the Future (MRFF), Closed Loop Fund, The Recycling
“We like to think of recycling infrastructure as four buckets in the value chain,” he says. Those “buckets” are access to collection systems, participation by consumers, separation and end market demand. “Each of those buckets has to be worked.”
P&G recognizes that as a consumer of recycled plastics, it has a role to play in ensuring consistent demand,
“A vast array of companies across industries want to use recycled materials without having to compromise on appearance,” Otworth says. PureCycle can help these companies do so
He adds, “It’s a great global opportunity and an opportunity to do good with a broader utilization of recycled plastics.”
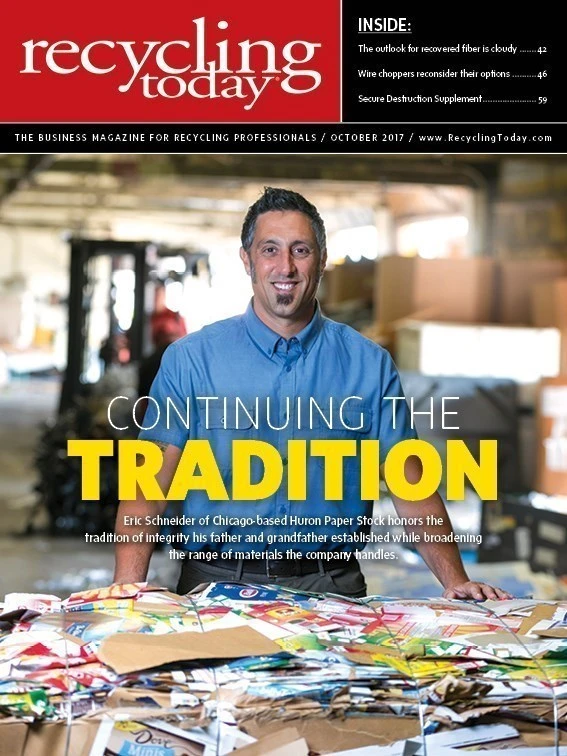
Explore the October 2017 Issue
Check out more from this issue and find your next story to read.
Latest from Recycling Today
- Aqua Metals secures $1.5M loan, reports operational strides
- AF&PA urges veto of NY bill
- Aluminum Association includes recycling among 2025 policy priorities
- AISI applauds waterways spending bill
- Lux Research questions hydrogen’s transportation role
- Sonoco selling thermoformed, flexible packaging business to Toppan for $1.8B
- ReMA offers Superfund informational reports
- Hyster-Yale commits to US production