
A company that manufactures outdoor furniture from recycled high-density polyethylene (HDPE) has become vertically integrated with the addition of a washing and shredding line for milk jugs.
Poly-Wood, Syracuse, Indiana, previously bought recycled HDPE flake from outside vendors. Now, it’s able to operate as a recycler and as a manufacturer.
“It was cost-inefficient, there were issues with handling of recycled material, and they had limited control on the quality,” says Tomas Kepka, vice president for Lindner ReSource America, Tucker, Georgia, of Poly-Wood’s purchasing of recycled flake.
“We had the fortune of planning our recycling plant from scratch,” Chad Rassi, process engineer at Poly-Wood, says in a news release from Lindner ReSource America. “The key aspect here was to ensure a high level of sustainability through the particularly efficient use of water, heating and energy power, as well as low-maintenance operation, maintenance-friendly design and a high nominal throughput in long-term operation. We wanted to achieve outstanding cost-efficiency so as to make the recycling of plastics a success for us both technically and economically.”
Poly-Wood asked Lindner to develop a combination of shredders and wash components to process milk jugs.
“Poly-Wood’s main concern was to find a solution for cleaning and washing of contaminated postconsumer milk bottles, with a compact design,” Kepka explains. “The system had to be designed to process postconsumer milk bottles and [turn] them into clean and dry HDPE flake with a specific size and moisture level.”
Lindner designed the Poly-Wood line to shred, wash and dry material in several steps to gently remove all contamination, including dirt, sand, other plastics and labels, Kepka says.
Lindner used its new mechanical dryer and air-wash system as the final stage of the washing line. “This combination will give us residual moisture of less than 1 percent” in the flake, Kepka says. “Despite this very low moisture level and the high supported throughput rates, the operating costs of this advanced washing system are fairly low because no thermal drying is needed.”
Throughput for the line is 4,000 to 5,000 pounds per hour, he says.
Lindner designed the complete washing line to meet Poly-Wood’s requirement that it be maintained easily and operate with a minimum number of employees. The complete system requires one maintenance worker and one operator to handle material input and output.
In the first step of the system, a Micromat Plus 2000 single-shaft shredder is fed by a chain conveyor. The powerful shredder consistently uses low amounts of energy and is highly efficient, according to the manufacturer. The point blade rotor, which is 78 inches in length and 22 inches in diameter, comes with 104 2.6-inch-by-2.6-inch blades. The point blade rotor and its configuration are designed to ensure precise cutting and high throughput even when processing abrasive materials. The shredder also features a large inspection and maintenance flap that allows for easy adjustment and replacement of the blades and counter-blades and simplifies cleaning the hopper and removing foreign objects.
Lindner customized the line using new components for high-efficiency washing from the Lindner washTech business unit. Poly-Wood uses a friction washer, a combination of Floater (a preseparation unit) and Twister (a friction washer) technology that removes paper label residue and other contamination.
A specially designed wet grinder is used to achieve the required flake size. The system directs a jet of water onto the rotor so the friction generated during the grinding process is used to remove the remaining dirt. The amount of water can be regulated to ensure uniform and controlled material discharge.
The next cleaning stage involves the Graviter, a sink-float separation tank that removes heavier plastics, which can include polyethylene terephthalate (PET), acrylonitrile butadiene styrene (ABS) or polyvinyl chloride (PVC).
Next, a Lindner loop dryer, which has a rotor diameter of 48 inches, a rotor length of 78 inches and a 120-horsepower motor, dries the material before the remaining fines are separated in an air-wash system. The material then can be moved to octabins, big bags or storage silos before entering the recycling line.
The system produces flakes that are ideal for turning into pellets because of their purity, residual moisture and size.
“Two important factors provided us with the basis that enabled us to comply with Poly-Wood’s requirements quickly and completely,” Kepka says. “Firstly, the Lindner systems have a modular structure. This enables us to meet a wide variety of different demands simply through the clever combination of standard and new components. Secondly, we benefit from our long-lasting cooperation with main suppliers of plastics recycling [machines]. As a result, we are very familiar with their demands made on the input material for their recycling process. From this experience, we know without extensive preliminary trials how we must configure our systems to provide them with a clean, shredded and dried material optimized for these machines.”
The system began running in September 2016, after only six months of lead time.
“We know that our decision to accept the offer from Lindner was absolutely correct,” Rassi says. “Water and energy consumption are even lower than expected, and the performance and end product [are] outstanding.”
For more information: Lindner ReSource America LLC, 770-349-6319, www.lindner-resource.us; Poly-Wood LLC, 855-935-5550, www.polywoodoutdoor.com
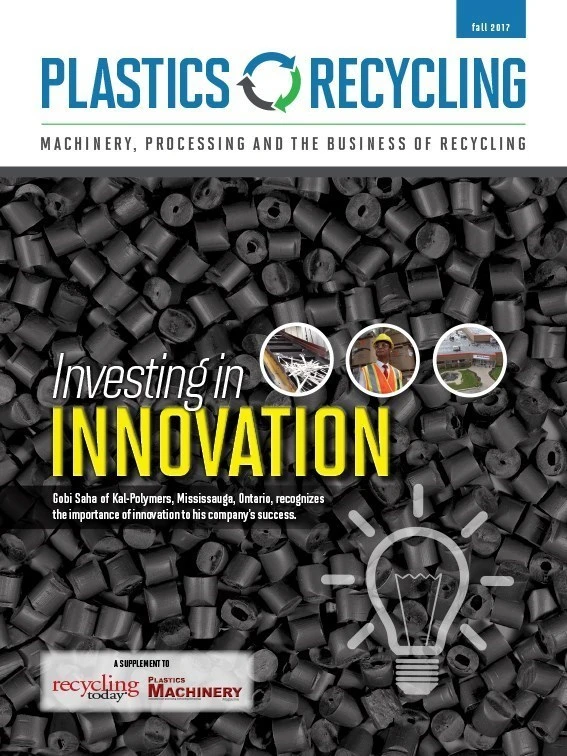
Explore the October 2017 Plastics Recycling Issue
Check out more from this issue and find your next story to read.
Latest from Recycling Today
- AF&PA report shows decrease in packaging paper shipments
- GreenMantra names new CEO
- Agilyx says Styrenyx technology reduces carbon footprint in styrene production
- SABIC’s Trucircle PE used for greenhouse roofing
- Hydro to add wire rod casthouse in Norway
- Hindalco to invest in copper, aluminum business in India
- Recycled steel price crosses $500 per ton threshold
- Smithers report looks at PCR plastic’s near-term prospects