
At the onset of 2017, as the Chinese government undertook its National Sword program aimed at blocking what it considers substandard imported shipments of scrap materials, it became clear the plastics recycling sector would be the most dramatically affected.
The late November 2017 announcement that Paris-based Suez intends to work with a multinational chemical and polymers firm to upgrade plastic scrap has been one of several investments by recycling firms reacting to the new restrictions.
The previous month, Germany-based Alba Group announced it would site a facility in a region of western Germany that has an abundance of petrochemical facilities, with the intention of working with such firms to seek optimal compound blends and processing measures to handle its plastic scrap.
With China’s central government
Ron Sherga, founder of Arlington, Texas-based EcoStrate, says the change is long overdue. “China became nothing more than a glorified landfill for many countries,” states Sherga, whose company converts several types of plastic scrap into street signs and other manufactured items.
“MRFs (material recovery facilities) will need to explore more vertical solutions and formal partnerships with those making end products,” he continues. “Some of this is already taking shape. I’m already seeing evidence where those facilities that were dependent on China are suffering or will be out of business soon.”
As Sherga points out, stockpiles of plastic scrap have been building in some places. Also growing, however, is the number of news releases announcing investments in new ways to upgrade plastic scrap.

Big splashes
The Suez partnership is with Houston-based LyondellBasell, a multinational company that bills itself as one of the world’s largest plastics, chemical
QCP is a plastics reprocessing and compounding company with a facility near Maastricht, Netherlands, that has been designed to convert
The transaction marks one of the first times a major plastics and chemicals company has partnered with a leader in resource management to contribute to circular economy objectives, the companies say.
“As the circular economy increases in prominence and importance, we believe that demand for recycled materials will continue to grow,” LyondellBasell CEO Bob Patel and Suez CEO Jean-Louis Chaussade say in a shared statement announcing the joint venture. “This acquisition combines LyondellBasell’s European market presence and technical capabilities with Suez’s ability to collect and recover waste into new materials. We believe that this new venture will provide a strategic platform for future sustainable growth.”

LyondellBasell will market QCP materials following the completion of the transaction, which is subject to regulatory approval. LyondellBasell and Suez were seeking to secure regulatory approval by the end of 2017. However, as of press time the deal had yet to be approved.
LyondellBasell sells products into approximately 100 countries and describes itself as the world’s largest licensor of polyolefin and PP technologies.
Suez, which operates on five continents, recovers some 17 million tons of discarded materials per year and produces 3.9 million tons of secondary raw materials.
The Berlin-based Alba Group, meanwhile, is constructing a new production plant for recyclables at Chemiepark Marl in the state of North Rhine-Westphalia in western Germany.
The new plant is being built on roughly 55,000 square meters (13.5 acres) in the south of the Chemiepark Marl (Marl Chemical Park). Alba Group indicates the plant will combine “state-of-the-art digital technology (Sorting 4.0) with the Alba Group’s almost 50 years of expertise.”
Chemiepark Marl is one of the largest chemical sites in Germany, covering an area of more than 1,480 acres. It is home to facilities operated by Evonik Industries AG, its subsidiaries
The new plant will process lightweight packaging
“With our new plant, we are not just a leader in terms of sorting technology in Germany and Europe, we are also well-equipped to achieve the high-volume requirements of the new Packaging Act in Germany,” says Axel Schweitzer, CEO of Alba Group. “With our
“We are proud that we have been able to attract another internationally renowned company for our park with the Alba Group,” says Jörg Harren, site manager of Chemiepark Marl. “With
The construction of the plant in Marl, which was slated to begin in late 2017, has a projected cost of more than $70 million (€60 million). The commissioning of the plant is planned for the beginning of 2019.
Changing habits
The major investments by the two firms are likely to be followed by others, as the flow of plastic scrap from China appears to have been severely pinched in 2017, with no turnaround in sight in 2018 or beyond.
Speaking at the 2017 Paper & Plastics Recycling Conference Europe, held in Warsaw, Poland, in November, John Paul Mackens of Switzerland-based freight forwarding firm Kuehne + Nagel said the Chinese government’s increased scrutiny of imported scrap materials had been “a huge headache” for the freight industry. He added that he had to reposition some 50 containers away from China because of the National Sword program there.
In 2016, Europe sent 89 percent of its outbound plastic scrap to Chinese ports. In September 2017, he said just 46 percent went to Chinese ports, with Malaysia receiving 12.6 percent, Hong Kong receiving 10.7 percent and Vietnam 9.5 percent.
Other speakers at the conference expressed doubt that the flow of plastic scrap from Europe or North America to China would ever return in the same form.
Thijs Cox of Netherlands-based
Cox said China’s government had good reason to introduce some of the restrictions, and 2017 likely marked “the end of an era” in terms of the ease of sending lower quality shipments to that nation.
Many recycling firms seem to have reached that conclusion, in addition to Alba and Suez. In Canada, Cascades Inc. has announced a $21 million investment in its Cascades Inopak and Plastiques Cascades plants to increase production of recycled-content food packaging.
The company’s investment will help it acquire equipment to increase its production of food packaging, primarily for the fresh protein market. Of that investment, $15 million will go toward the Cascades Inopak plant in Drummondville, Quebec. The funds will be used to expand the company’s existing building and to install a high-performance recycled polyethylene terephthalate (rPET) film manufacturing line that includes a built-in decontamination unit.
Nearly $6 million will be invested in the Kingsey Falls, Quebec, Plastiques Cascades plant to modernize equipment, notably by adding a new extrusion line and two recycling lines, which will increase production capacity by 25 percent and double the plant’s internal recycling capacity. The Kingsey Falls plant produces Evok, a polystyrene (PS) foam tray that contains at least 25 percent recycled materials.
It is unclear whether consumer products companies will offer pressure or support to recyclers faced with an abundance of postconsumer plastic packaging.
In January 2018, Atlanta-based Coca-Cola announced a goal to recycle all of its
The company indicated it aims to make bottles with an average of 50 percent recycled content and stated it would launch efforts with new partners at the regional and local level “to help motivate consumers to recycle more packaging.”
Coca-Cola also named several partners that will help the company achieve its goals. However, none of the partners was MRF operators or plastics reprocessing firms but rather nongovernmental organizations, such as the London-based Ellen MacArthur Foundation’s New Plastics Economy Initiative, the Ocean Conservancy/Trash Free Seas Alliance and the Cascading Materials Vision and Bioplastic Feedstock Alliance of the World Wildlife Fund.
Cincinnati-based Procter & Gamble (P&G), meanwhile, has researched and funded technology being commercialized by PureCycle Technologies at a plant that is under construction in Ironton, Ohio. P&G’s patented technology will be tasked with recycling PP containers, which are used heavily
Such investments in plastics recycling may become increasingly common as the hundreds of thousands of tons of plastic scrap that formerly headed to China no longer make that ocean voyage.
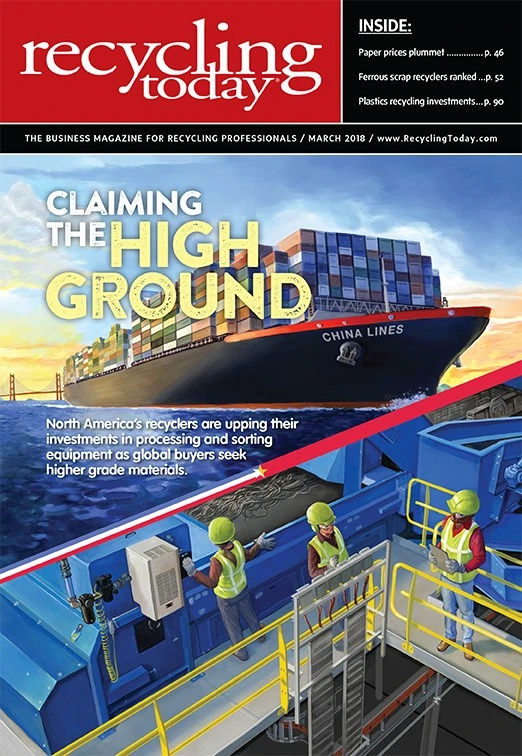
Explore the March 2018 Issue
Check out more from this issue and find your next story to read.
Latest from Recycling Today
- Lautenbach Recycling names business development manager
- Sebright Products partners with German waste management equipment company
- WasteExpo transitions to biennial format for enhanced experiences
- Study highlights progress, challenges in meeting PCR goals for packaging
- Washington legislature passes EPR bill
- PureCycle makes progress on use of PureFive resin in film trials
- New copper alloy achieves unprecedented high-temperature performance
- Gränges boosts profits and sales volume in Q1 2025