
Gobi Saha,
“I started with
The early days
Saha emigrated to Canada from his native India in 1983 after having earned a bachelor’s degree in chemical engineering followed by a master’s degree in business administration from the Indian Institute of Foreign Trade. The young Saha used his education to get a job at a packaging company, where he says he was first exposed to the issue of plastic waste. He saw the need to find a better solution for this material and realized it offered him the opportunity to fulfill his desire to work in a field that also helped him to protect the environment, which led to the formation of Kal-Polymers in 1992.
In 1993, the company opened its first warehouse in Mississauga. Soon after, it began adding processing equipment. Within three years, Kal-Polymers, which now employed 15 people, would outgrow this 18,000-square-foot facility. In 1996, the company moved to a 32,000-square-foot location in Brampton, Ontario. In addition to offering more warehousing space, the new location offered ample room for the company’s manufacturing equipment and related activities.
Kal-Polymers eventually outgrew the Brampton facility, moving to its current location on Wolfedale Road in Mississauga. At 185,000 square feet, this facility offers four times the space of the company’s previous warehouse in Brampton, which has enabled Kal-Polymers to further expand its reprocessing capabilities. With this most recent relocation, Kal-Polymers also added a laboratory to test the properties of incoming feedstock and of outgoing raw materials.
During the last decade, in addition to expanding its blending capabilities, Kal-Polymers expanded its grinding and reprocessing proficiencies. By 2014, the company was able to recycle painted parts and to demetallize and
Kal-Polymers also expanded its laboratory during this time, creating solutions for challenging materials, such as difficult-to-recycle postindustrial plastics.
The present
The ISO: 9001 certified company says it is “continuing on a path of development and growth,”
While Kal-Polymers handles a variety of postindustrial plastic scrap, including thermoplastic olefin (TPO), polyvinyl chloride (PVC) and acrylonitrile butadiene styrene (ABS), Saha says the company specializes in polypropylene (PP), polyethylene terephthalate (PET) and polyethylene (PE). He describes these polymers as being “highly versatile” plastics that are used by manufacturers in large volumes and that enjoy a “wide customer base.”
Saha says Kal-Polymers converts and adds value to these postindustrial scrap plastics, transforming them into reusable pellets. “We also compound by adding fillers and colors to meet customer requirements.”
According to the company’s website, it serves a variety of industries, the largest of which
The company processes more than 20 million pounds per year of packaging scrap in a variety of forms, including film, sheet, fiber,
In the automotive sector, Kal-Polymers serves Tier One, Tier Two and Tier Three suppliers to the industry and is certified by the Canadian Aboriginal & Minority Supplier Council (CAMSC). The company says it also is ISO certified for quality management, which is among the attributes that make it an attractive supplier to this sector. Among the

Processing innovations
Kal-Polymers says it has invested in human resources and technologically advanced equipment so that it can recover and reuse challenging materials. Additionally, the company says it has introduced cost-effective additives, such as
Saha says Kal-Polymers has invested millions of dollars in equipment to depaint bumpers so they can be processed into unpainted reusable pellets with properties near to the unpainted bumper grade TPO. Its proprietary manufacturing process, developed by its technical staff, uses a dry process to depaint the bumper scrap, avoiding the use of any chemicals/additives, the company explains on its website. Kal-Polymers describes the technology as “cost-effective and environmentally friendly.”
"We have to innovate, upgrade and expand not only to succeed but also to survive.” – Gobi Saha, owner and president of Kal-Polymers
Another troublesome material from the automotive industry that the company has developed a recycling process for is dashboard skin, which normally contains cross-linked foam. The Kal-Polymers lab has found a solution to remove this foam without the use of chemicals, and the company says trials are underway with commercialization expected soon.
Kal-Polymers also says it has begun trials to process trunk liners, which are made from a combination of PP and PET.
In the packaging sector, the company says it has developed a solution for films and
Saha says Kal-Polymers also can reprocess PE/nylon and PE/EVOH (polyethylene vinyl alcohol copolymer) blown film and that the pellets can be reused for the same application.

Factors shaping the market
Saha describes consuming markets for recycled plastics as being “quality driven, highly competitive and price sensitive.”
The lower prices for
He adds that another issue facing the plastics recycling industry currently is the accumulation of challenging forms of plastic scrap as a result of China’s National Sword policy and its crackdown on plastic scrap processors in that country.
“This will create a glut in the North American market,” Saha says. “This will force the scrap generators and recyclers to find solutions for such scrap by investing in technology to find its reuse. It will be observed more so in the
Saha says legislation mandating the use of recycled content by manufacturers, as California has done, for example, could help to ensure this material is recycled and reused in North America.
In addition to the innovation that Kal-Polymers has shown over the course of its 25-year history and its willingness to invest in technology, Saha says other factors that have contributed to his company’s success are avoiding over-speculating and keeping his ears to the ground.
“We have to innovate, upgrade and expand not only to succeed but also to survive,” Saha says. “We aim to be known as an organization that thrives on taking up challenges to find cost-effective solutions in recycled raw materials with consistent quality and volume commitments.”
For more information: Kal-Polymers, 905-273-7400, http://kalpolymers.com
Get curated news on YOUR industry.
Enter your email to receive our newsletters.
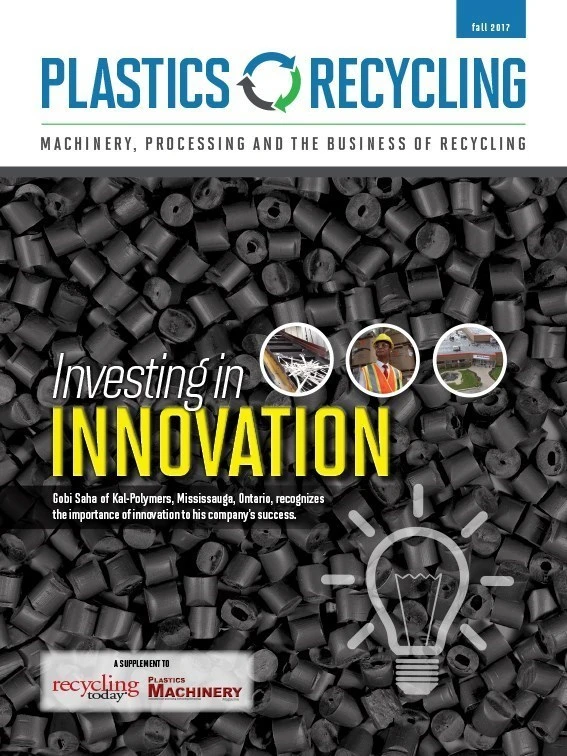
Explore the October 2017 Plastics Recycling Issue
Check out more from this issue and find your next story to read.
Latest from Recycling Today
- Republic Services, Blue Polymers open Indianapolis recycling complex
- Altilium produces EV battery cells using recycled materials
- Brightmark enters subsidiaries of Indiana recycling facility into Chapter 11
- Freepoint Eco-Systems receives $50M loan for plastics recycling facility
- PET thermoform recycling the focus of new NAPCOR white paper
- Steel Dynamics cites favorable conditions in Q1
- Hydro starts up construction in Spain
- Green Cubes unveils forklift battery line