Unifi opens its Repreve Bottle Processing Center

Unifi Inc., headquartered in Greensboro, North Carolina, celebrated the official opening of its Repreve Bottle Processing Center in Reidsville, North Carolina, Sept. 7, 2016. Unifi says the $28 million-plus investment will help the company achieve its goal of vertical integration for its Repreve recycled product line, adding flexibility, expanding production capabilities and supporting volume growth. The Repreve Bottle Processing Center will add 87 new jobs in the Reidsville area, ranging from salaried managers and engineers to hourly operators, material handlers, electricians, mechanics and more.
“This expansion of Unifi’s Repreve business will bring jobs to our state and furthers North Carolina’s leadership in high-tech manufacturing,” said Gov. Pat McCrory at the grand opening celebration. “I am proud that our efforts to improve North Carolina’s business climate, invest in infrastructure and encourage building reuse have helped companies like Unifi grow and succeed.”
The 150,000-square-foot Repreve Bottle Processing Center is at the company’s facilities in Reidsville. According to Unifi, the recycling center is one of the most advanced in the United States, with the capacity to produce 75 million pounds of clean bottle flake annually. The plant includes a front-end polyethylene terephthalate (PET) sorting system, designed, manufactured and installed by Eugene, Oregon-based Bulk Handling Systems (BHS).
Unifi will purchase baled PET bottles from material recovery facilities (MRFs) across the eastern United States for processing at the Repreve Bottle Processing Center. After the bottle sorting process, Unifi will remove labels, debris and caps from the remaining PET bottles. These bottles will be chopped into flake, washed, dried and bagged for use in the production of Repreve, or sold to other companies for consumer packaging applications.
“The vertical integration of our Repreve manufacturing process highlights an important next step in Unifi’s continued path toward sustainability and producing high-quality, value-added products,” said Tom Caudle, president of Unifi, at the grand opening. “The Repreve Bottle Processing Center uses custom-designed, cutting-edge technology and provides increased flexibility that will allow us to better serve our customers, as well as create a new channel of revenue. We are also proud to support manufacturing in North Carolina and to add new jobs in our communities.”
Ravago completes deal for Michigan plastics recycler

Ravago Holdings America Inc. (RHA), Orlando, has completed the acquisition of Industrial Resin Recycling Inc. (IRR), headquartered in Howell, Michigan. IRR specializes in recycling postindustrial plastics.
Ravago says the acquisition expands its recycling platform by providing a greater number of regional service points in the southeastern and upper Midwest and by giving it greater access to feedstock for its portfolio of recycled resins, including its Echo line of recycled polypropylene and polyethylene.
Additionally, Ravago says the acquisition further cements its position as a leading supplier and service provider to the automotive sector.
“We welcome IRR as the newest member of the Ravago Group,” says Jim Duffy, CEO and president of RHA. “As we expand and build upon our commitment to recycling, we see this acquisition as a critical next step in our ability to offer customizable solutions to the market where we can manage the entirety of the recycling ecosystem, including collection, conversion and the sale of recycled resins.”
RHA is part of Ravago Group, a Belgium-based supplier of plastics, rubber and chemicals representing more than 4 million metric tons of annual polymer sales and serving more than 40,000 customers through 230 offices in more than 55 countries. The company also operates 30 manufacturing facilities, 19 of which are recycling and compounding plants.
APR seeks nominations for Plastics Recycling Showcase
The APR Plastics Recycling Showcase, a program designed to highlight and promote innovations that have a positive effect on plastics collection and recycling, is accepting nominations.
Developed by the Association of Plastic Recyclers (APR), Washington, the second annual program focuses on recently commercialized innovations developed by APR member companies. The APR has added a category focused on community engagement to the 2017 Showcase. The nomination deadline is Oct. 31, 2016.
“This program is part of APR’s Champions for Change Program, which was created to encourage innovators to address technical challenges facing plastic recyclers,” says John Standish, APR technical director. “We recognize that innovation drives the growth of recycling and is essential to the success of the plastics recycling industry,” he adds.
Possible candidates include the following types of recently commercialized technologies or programs:
- packaging products;
- processing equipment;
- recycling process step improvement;
- bale capability;
- collection or supply capability for postconsumer plastics;
- postconsumer resin (PCR) products, products with high PCR content or new applications of PCR;
- community education programs;
- demonstration programs within communities to identify new approaches to collection or materials processing; and
- studies and reports that benchmark current capabilities and that identify best practices or opportunities for improvements.
Showcase recipients are selected by a committee made up of APR members representing a variety of roles within the value chain. The selected innovators will be recognized during The APR Technical Forum, held in conjunction with the Plastics Recycling Conference, March 6, 2017, in New Orleans. Showcase innovations will be displayed at the APR booth during the 2017 Plastic Recycling Conference and during other trade shows throughout the year. They also will be featured on the APR website and in an APR Educational Web Seminar.
More information and applications are available at www.plasticsrecycling.org/champions-for-change/programs.
APR survey reveals polypropylene PCR demand

Demand for recycled polypropylene (PP) resin by major consumer brand companies is approaching 300 million pounds annually, according to a study by the Association of Plastic Recyclers (APR), the international trade organization based in Washington that represents the plastics recycling industry. Twenty-one major consumer brand companies responded to the survey and also provided quality and quantity information for potential PP postconsumer resin (PCR) use in nonfood-contact applications. These companies identified demand of more than 280 million pounds of the recycled resin annually, the APR reports.
Liz Bedard, APR Rigid Plastics Recycling Program director, says, “We recognize the combination of factors impacting the current market for recyclables; however, consumer brand companies specifically outlined potential demand for this material. The challenge remains providing recyclers the feedstock to meet that demand.”
All respondents’ demand is current or expected within the next three years, according to the APR. The survey also provides information on qualitative PCR components, such as melt flow index, odor, color and demand time frame.
“APR’s two main goals are to increase supply and enhance the quality of the plastics recycling stream,” says J. Scott Saunders, general manager of KW Plastics, Troy, Alabama, and chairman of APR. “Through work to achieve those goals, The APR Rigid Plastics Recycling Program and the Polypropylene Market Development Subcommittee have become one of the primary drivers to move the marketplace forward through stimulating growth and increasing availability and use of polypropylene PCR.”
Applications for PP PCR include tubes, rigid packaging, closures, containers, pails, crates, disposable cutlery, pallets, hangers and tubs.
Full survey results are available on the APR website at www.plasticsrecycling.org/resources/pp-pcr-demand-survey. The full list of company respondents and contact information is available to APR members.
Get curated news on YOUR industry.
Enter your email to receive our newsletters.
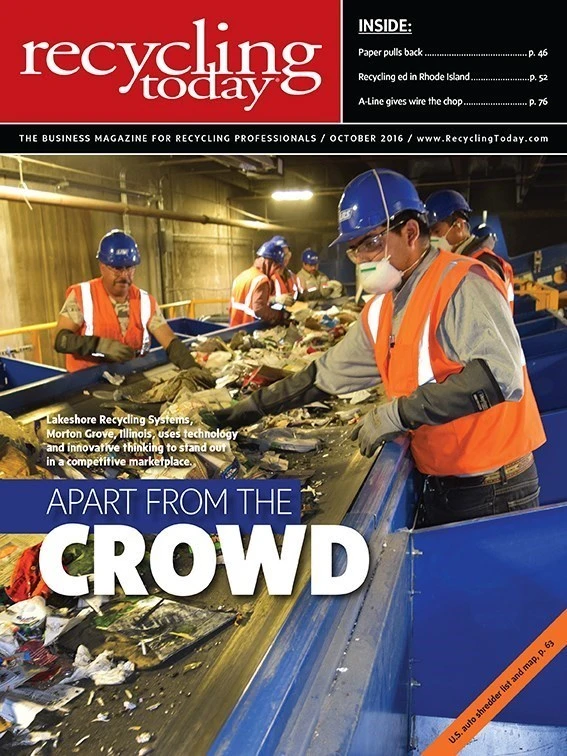
Explore the October 2016 Issue
Check out more from this issue and find your next story to read.
Latest from Recycling Today
- Call2Recycle Canada launches program in Alberta
- The history of SAS Forks: Celebrating 50 years
- SAS Forks partners with NED at Green Recycling in Houston, Texas
- DRKhorse’s RCC series at Gorick Construction in Endicott, New York
- Balar Equipment to operate under Enviro-Clean Equipment name
- Li-Cycle reports 2024 financials
- Wisconsin Aluminum Foundry acquires Anderson Global
- PureCycle, Landbell Group working to advance PP recycling in Europe