
Agilyx to develop styrene monomer production plant in Oregon
Agilyx Corp., Tigard, Oregon, has announced that it has secured project financing and is constructing a 10-ton-per-day production facility near Portland, Oregon, that will convert various types of polystyrene scrap (foam cups, packaging materials and Styrofoam) into a styrene monomer using the company’s proprietary pyrolysis process. The finished product will be a liquid that will be sold on the open market to refiners, the company says.
Ross Patten, CEO of Agilyx, says it will be the first plant of its kind in North America.
The plant is scheduled to begin production in the second quarter.
“We’re very pleased with the support we’re receiving from key industry players to bring this viable economic pathway for reuse of plastic waste to market,” Patten says. “Agilyx is excited to be part of a full-circle solution that aligns with what’s needed so urgently.”
Agilyx says it is targeting the food packaging and the horticultural sectors for feedstock.
The module on which the 10-ton-per-day operation is being built can be expanded to produce 25 tons per day or even 50 tons per day, Patten says.
Modules of various sizes can be sold in different regions of the U.S. that are interested in pursuing polystyrene recycling projects, he adds.
Previously, the Agilyx facility consumed mixed plastics, converting them into a VGO (vacuum gas oil) quality synthetic oil.
Trex recycled pellets receive ICC Certification
Winchester, Virginia-based Trex, a manufacturer of wood-alternative decking and railing and recycled plastic, has announced that its linear-low-density polyethylene (LLDPE) pellets have achieved certification with the International Code Council (ICC), Washington. The certification recognizes that Trex Spartan and Cardinal lines of LLDPE pellets contain 100 percent postconsumer content.
“Trex LLDPE pellets are an ideal material for plastic product manufacturers to incorporate into their manufacturing process as a means of increasing both the recycled content and cost efficiency of their products,” says Dave Heglas, senior director of material resources, Trex. “With this certification, companies can be assured that using Trex pellets can help meet their recycled-content requirements and sustainability goals while reducing their reliance on virgin and off-spec resin.”

Launched in 2015, Trex’s LLDPE pellets are made from the surplus recycled postconsumer and postcommercial polyethylene that Trex regularly collects for manufacturing its composite decking.
The recycled pellets are designed to partially displace virgin and off-spec resin.
Trex says it has four lines for recycled pellet production.
“As one of the country’s largest plastic recyclers, Trex is able to deliver the quantities and consistent quality manufacturers need at a lower price and with the added convenience of a single-source provider,” Heglas says.
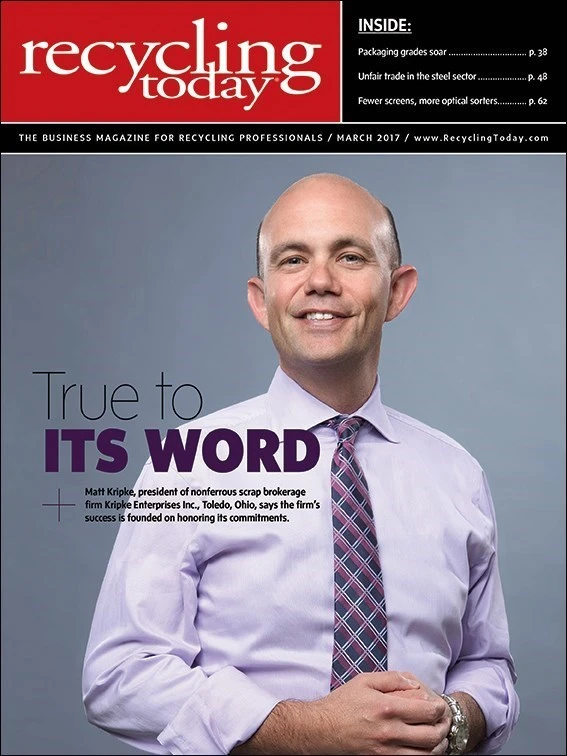
Explore the March 2017 Issue
Check out more from this issue and find your next story to read.
Latest from Recycling Today
- ReMA opposes European efforts seeking export restrictions for recyclables
- Fresh Perspective: Raj Bagaria
- Saica announces plans for second US site
- Update: Novelis produces first aluminum coil made fully from recycled end-of-life automotive scrap
- Aimplas doubles online course offerings
- Radius to be acquired by Toyota subsidiary
- Algoma EAF to start in April
- Erema sees strong demand for high-volume PET systems