
Eastman invests in methanolysis plant in Kingsport, Tennessee
Eastman Chemical Co., headquartered in Kingsport, Tennessee, has announced that it will build a “molecular” recycling facility for end-of-life polyester products and packaging at its existing site in that city. Eastman board Chair and CEO Mark Costa made the announcement in a press conference Jan. 29 that also was hosted online. He was joined by Tennessee Gov. Bill Lee.
Eastman’s Kingsport site is one of the largest integrated chemical manufacturing plants in North America. Costa tells Recycling Today, “We evaluated a number of possible locations, and, ultimately, we made the decision based on our scale and integration in Kingsport. Also, we were able to work together with Tennessee state officials to make this investment here.”
The company says it will use methanolysis to convert end-of-life polyester products and polyethylene terephthalate packaging that are difficult to recycle by mechanical means into recycled raw materials that will be used to produce the company’s specialty plastics.
Over the next two years, Eastman says it will invest about $250 million in the facility, which will support its commitment to addressing the global waste crisis and to mitigating challenges created by climate change while also creating value for its stakeholders. Using the company’s polyester renewal technology, the facility will consume more than 100,000 metric tons of end-of-life plastics that cannot be recycled by mechanical methods.
“The plant will be able to process a variety of feedstocks from the packaging, carpet and textiles markets,” Costa tells Recycling Today. “We are already purchasing polyester from multiple sources for our molecular recycling technologies and are making plans with our partners to increase volumes as the plant startup approaches. With this technology, Eastman will divert waste that would otherwise be landfilled, incinerated or end up in our waterways. And we can do this an infinite numbers of times.”
In the press conference, Costa noted that California is a leading supplier of end-of-life carpet currently through the company’s partnership with Circular Polymers, which densifies the fiber, enabling its transport by railcar to Eastman’s Kingsport site.
“Innovation has been at the heart of Eastman since we began,” Costa said during the press conference. He added that the methanolysis plant will be a “huge new vector of growth for us in the circular economy” and involves “significant infrastructure announcements that require cooperation from everyone in the state.”
Costa said Eastman also plans to deploy the technology more broadly in the future.
Eastman says using end-of-life plastics as the main feedstock is a material-to-material solution, reducing the company’s use of fossil feedstocks and its greenhouse gas emissions by 20 to 30 percent relative to fossil feedstocks.
The facility, which is expected to be completed by year-end 2022, will contribute to Eastman achieving its sustainability commitments for addressing the plastic waste crisis, which includes recycling more than 500 million pounds of plastic waste annually by 2030 via molecular recycling technologies and becoming carbon neutral by 2050, according to the company. Eastman says it has committed to recycling more than 250 million pounds of end-of-life plastics annually by 2025.
For more details on Eastman’s plans, see www.RecyclingToday.com/article/eastman-chemical-recycling-plastics-investment.
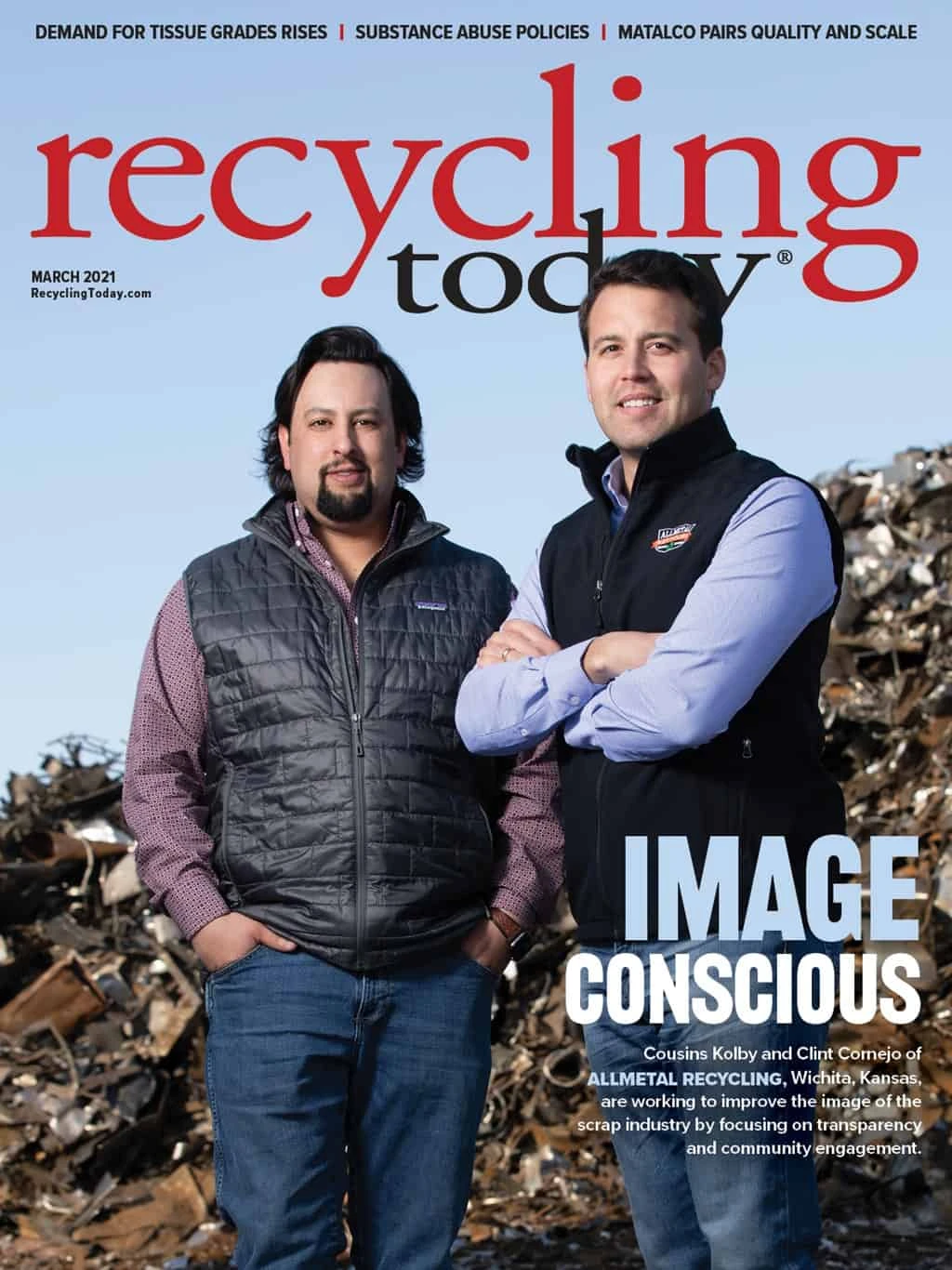
Explore the March 2021 Issue
Check out more from this issue and find your next story to read.
Latest from Recycling Today
- Aqua Metals secures $1.5M loan, reports operational strides
- AF&PA urges veto of NY bill
- Aluminum Association includes recycling among 2025 policy priorities
- AISI applauds waterways spending bill
- Lux Research questions hydrogen’s transportation role
- Sonoco selling thermoformed, flexible packaging business to Toppan for $1.8B
- ReMA offers Superfund informational reports
- Hyster-Yale commits to US production