With strong plastics markets, there is increasing interest in plastic sorting and processing equipment.
With the market for recycled plastic products booming, fueled in part by renewed consumer awareness and state regulation, materials handling is becoming a challenge for recycling center operators.
Simply sorting out the more valuable PET – polyethylene terephthalate, used in soda bottles – and HDPE – high density polyethylene, used in milk bottles – from the other types of plastics found in commingled lots is becoming an economic challenge for recyclers. Along the way, there are still the hurdles of putting the recycled material into usable form before it is processed and having it come out in a compact, clean, easily handled form at the other end of the process.
"The biggest change we will see down the road will not be in granulating or size reduction, but in optical sorting," predicts Rustin Ross, director of operations for Alan Ross Machinery Corp., Northbrook, Ill. Optical sorters, unlike the electrostatic separators which remove caps and other metals from the plastics stream, will add a degree of sophistication previously unheard of in the recycling market. Several variations on the theme have been tested by a variety of manufacturers.
It has been an open secret in the industry that FMC’s Corporate Technology Center in Santa Clara, Calif., was working on such an optical sorter. FMC was assaying a system to classify either glass or plastic by color and density. "FMC is not pursuing that business any longer," according to Don Christian who was on the development team. However, the saga of the FMC sorter does not end there.
Andy Chang, Los Altos, Calif., expressed an interest in taking over the technology from FMC to use for sorting green, amber and clear glass products, but not for sorting plastics. "Negotiations fell through," Chang says. He now is pursuing options outside of the recycling field. So, for the time being, that avenue is closed.
Pure Tech APR has been using two optical sorting units in its Long Island, N.Y., operation. Their primary function is to sort colored plastic from clear. But the company prefers not to comment about the equipment and its effectiveness in their operation.
Another negative review comes from the Rutgers University Center for Plastics Recycling Research in Piscataway, N.J. There, they have all but written off the idea of optical sorting. "We worked on it for a number of years," the center’s Tom Nosker says. "We feel it has limited applicability to increase the number of plastics that can be recycled from the waste stream."
Their research shows that sorting out soda and milk bottles from the waste stream will remove less than half of the material. "However, the material left is high-cost to sort out," says Nosker.
Most of that plastic material is HDPE, with only about 10 percent being other plastics. Included are colored HDPE and bottles with non-standard closures. They don’t separate easily, so they are treated as waste and landfilled in most places.
Environmental Products, Fairfax, Va., has a patent on a sensing device which will sort PET from other plastics. The firm developed the product to use in its own reverse vending machines which are deployed in bottle deposit states. "We are working on how we can commercialize the sensors," says Geoffrey Bobsin, executive vice president. "It is a cheap solution relative to X-ray equipment."
Under test right now is a system using an array of 20 sensors to sort PET at the head-end of a material recovery facility line. "This might be cost effective for the smaller operator who can’t afford $100,000 for sorting equipment," he explains. Johnson Controls has a similar device. Bobsin says their sensors were developed in response to consumers who would take the barcode off a PET soda bottle and paste it on a polyvinyl chloride bottle to collect the deposit. PVC is a contaminant to PET that must be removed.
Long ago, the company decided to shred rather than compact its PET, and is now working to make its shredder commercially available to replace granulators.
Bobsin says the company has a project going with Union Carbide for some preliminary equipment to shred rather than granulate. They also are working on a project in Riverside, Calif., to produce 30 million pounds per year of bottle-grade clean flake.
NEW PET PROCESS
Although optical sorting may be a bit far off, there will likely be more rapid advances in other areas, especially in the equipment being used today in recycling operations. "The big change we are seeing in granulators is in the decrease in horsepower required," Ross says, adding that manufacturers are increasing the degree of angle to the blade. "This high shear means less horsepower is needed."
The knives on older granulators traditionally were built to hit the bed head-on, Ross notes. Newer granulators have a higher angle. In addition, manufacturers are staggering the blades on the knives which gives a better slice.
"Another thing people underestimate is the amount of a role that screens play in size reduction," he says. "Up to 30 percent of size reduction in granulators is due to the screens. The knife shoves the material over the screens like moving cheese over a grater. A good, sharp set of screens can be a great help in efficiency."
Although machine efficiency will likely improve, prices are not expected to drop to any significant degree. George Tedder, vice president of sales for Conair Group’s Reclaim Division, predicts that pricing will go no lower. He says that post-industrial reclamation is doing quite well and that post-consumer processing is not a prime area for his company. "Recycling is kind of flat right now," he says. "We are de-emphasizing the post-consumer reclamation equipment."
Don Graveman, CEO of Magnatech Engineering, St. Charles, Mo., notes that prices could well rise for the newer equipment. "Steel prices are going up. That will force up the prices of shears," he says. Magnatech’s manufacturing lead-time is at 16 to 20 weeks for the 10- to 400-horsepower mechanical and hydraulic units which are used extensively in the recycling industry for pre-shredding.
The Magnatech plant is running at two shifts and undergoing plant expansion to meet demand, not only for its plastics recycling equipment, but for its full product line.
There are many more manufacturers entering the field. Ross warns buyers to stick with known quantities and to beware of fly-by-night operations, noting that service down the road may be a more important factor than a cheap purchase price today.
SHEAR POWER
A new process for recycling PET claims to overcome the limitations associated with mechanical recycling. Called UnPET, the process patented by United Resource Recovery Corp., Spartansburg, S.C., uses caustic soda to react with the PET to yield ethylene glycol and terephthalic acid. Next is a heating step which evaporates the EG, reduces organic impurities to carbon dioxide and water and leaves solid terephthalic salt.
The firm says the technology opens vast potential for post-consumer reclamation of the five billion pounds of recoverable PET generated from the 30 billion pounds of PET produced worldwide each year.
Another firm which both builds systems for sale and uses its own system in-house is Graham Engineering, York, Pa. The system is engineered at a nominal handling capacity of 2,000 pounds of post-consumer HDPE per hour. "Demand in the United States has been slow recently," says Sandy White, vice president of marketing for the engineering company. However, overseas, things are moving a bit better as Graham recently completed a project in Turkey and is looking at installations in Asia and Europe.
The company’s York location is running three complete lines, processing about 50 million pounds per year. "The system is based on a sorted, post-consumer feedstock," White explains. "We make flake, wash and dry the material, then re-pelletize it." The system is sold only as a complete package, not as components, to ensure the processing is done in the most efficient, high-tech manner possible.
"There is a definite move toward higher technology with cleaning and separating equipment," finds Steve Bunke, sales manager with Prodeva, Jackson Center, Ohio. His firm has partnered with Plasticycle Industries of Eau Claire, Wis., to produce a pre-shredder for their equipment which opens the bottles for cleaning before they are granulated.
There has been progress in pelletizers, too. Gala Industries, Eagle Rock, Va., produced underwater pelletizers which can process from 20 to 6,000 pounds per hour of polymer, according to the company’s recycling product manager John Linkenhoker. The firm recommends them for processing, compounding, scrap recovery and pilot operations.
A complete Wash and Dry Recycle System, consisting of a washer, dryer, exhaust blower and electric or gas air heater also is available from Gala. It is designed to remove surface moisture from plastic scrap. This system is able to handle from 20 to 10,000 pounds per hour, depending on the product type and size. A fines removal sieve to extract plastic particulates, paper or other particles, with a priming pump and internal piping standard, is part of the package. However, under some conditions, gravity flow can be used.
Cal-Sierra Machine, Pomona, Calif., offers a densifier which shreds the raw plastic material into pea-sized granules with a density of 20 to 30 pounds per cubic foot. Raw material is fed manually, or by conveyor, into a tub.
The processed material can then be fed directly into an extruder to make new products or the material can be pelletized in preparation for sale or storage.
The densifier can process low density, linear low density, medium density, and high density polyethylenes; acrylonitrile/butadiene/styrene (ABS); PVC; styrenes and polypropylenes. To size your needs, Bruce Becker, manager for Cal-Sierra, suggests a 50 horsepower machine output will process 300 pounds per hour; 100 horsepower, 750 pph; 150 horsepower, 1,000 pph; 200 horsepower, 1,500 pph; 250 horsepower, 1,800 pph. He says the 200 horsepower unit is the most common size ordered but he is seeing more demand for the 250 horsepower version.
Municipally-sourced scrap today contains a lot of contaminants, and the M.A. 700 series granulators from M.A. Industries, Peachtree City, Ga., are designed to handle the sand, dirt and other non-plastic trash that can spell headaches in recycling operations.
The rotor is 4140 steel, heat treated, and the bearing journals are heat treated for strength and durability, according to Keith Smith, mechanical designer for M.A. The standard cutting chamber includes replaceable bed blade decks, air-purged bearings and Chevron-style cutting action.
The company also offers a full line of bale breakers, spin dryers, trommels and complete HDPE and PET post-consumer plastic recovery systems.
With markets booming and technology adding a solid base for progress, the current plastic market could be atop the perfect market wave.
The author is an environmental writer based in Strongsville, Ohio.
Get curated news on YOUR industry.
Enter your email to receive our newsletters.
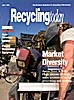
Explore the July 1995 Issue
Check out more from this issue and find your next story to read.
Latest from Recycling Today
- Toppoint Holdings expands chassis fleet
- Lego creates miniature tire recycling market
- Lux Research webinar examines chemical recycling timetables
- Plastics producer tracks pulse of wire recycling market
- Republic Services, Blue Polymers open Indianapolis recycling complex
- Altilium produces EV battery cells using recycled materials
- Brightmark enters subsidiaries of Indiana recycling facility into Chapter 11
- Freepoint Eco-Systems receives $50M loan for plastics recycling facility