Cornell University scientist develops polymer additive to facilitate recycling
During his presentations on plastics and recycling, Geoffrey Coates, a professor of chemistry and chemical biology at Cornell University, Ithaca, New York, often begins with the question: What percentage of the 78 million tons of plastic used for packaging actually gets recycled and reused in a similar way?
The answer is just 2 percent, Coates says, adding that nearly one-third of these plastics are leaked into the environment, around 14 percent are used in incineration and/or energy recovery and 40 percent wind up in landfills.
One of the problems is that polyethylene (PE) and polypropylene (PP), which account for two-thirds of the world’s plastics, have different chemical structures and cannot be recycled together.
A discovery from Coates’ lab might have the potential to change that, according to Cornell University. Coates and his group have collaborated with a group from the University of Minnesota to develop a multiblock polymer that, when added to a mixture of the otherwise incompatible materials, creates a mechanically tough polymer.
The two groups’ work is detailed in the paper “Combining Polyethylene and Polypropylene: Enhanced Performance with PE/iPP Multiblock Polymers,” published online Feb. 23, 2017, in Science.
James Eagan, a postdoctoral researcher in Coates’ group, is lead author of the paper. Other collaborators included researcher Anne LaPointe and former visiting scientist Rocco DiGirolamo.
By adding a miniscule amount of their tetrablock (four-block) polymer—with alternating PE and PP segments—the resultant material has strength superior to diblock (two-block) polymers the researchers tested, Cornell University reports.
Coates explains his team’s development in a video that can be accessed online through https://cornell.app.box.com/v/Polymer/1/19899475139/139302146831/1.
CarbonLite to build PET recycling plant in Dallas
CarbonLite, with corporate headquarters in Los Angeles and a manufacturing facility in Riverside, California, has announced that it is building a $62 million plant to recycle postconsumer polyethylene terephthalate (PET) bottles in Dallas. The company’s second processing facility will be able to process 100 million pounds of PET bottles annually using 100 percent green power, CarbonLite says.
The 230,000-square-foot facility is scheduled to start up at the end of the second quarter 2017, according to Leon Farahnik, chairman and CEO of CarbonLite.
With the addition of the Dallas facility, CarbonLite will become the largest producer of food-grade PET in the world, processing more than 200 million pounds of postconsumer bottles annually, the company says.
The primary equipment suppliers for this project are Bulk Handling Systems (BHS), Eugene, Oregon; Italy-based AMUT S.p.A.; Austria-based Erema Recycling Systems; and Pelletron, Lancaster, Pennsylvania.
CarbonLite says Nestle Waters North America and Pepsico are the main consumers of its raw material.
InterGroup International closes its doors
Neil Gloger, CEO of Cleveland-area-based InterGroup International, says the company’s bank, Fifth Third Bank of Cincinnati, has sought receivership for the company under the Ohio Revised Code.
In an interview with Recycling Today in mid-February, Gloger says, “Over the last 18 months, we have had five customers go bankrupt or just disappear.” This left the Euclid, Ohio-based company with $1.2 million in uncollectable receivables, he says, which put InterGroup International in default of the loan covenants with its senior lender.
“Our agreements with the bank expired, and they notified us they would seek receivership under the Ohio Revised Code,” Gloger adds.
InterGroup International did not have cash available to fund a Chapter 11 restructuring of the company, he says. In addition, Gloger says he was not given that option by the bank.
Gloger says he takes ownership of all the decision-making that led to this point, adding that he would make “virtually all of the same decisions.”
Gloger says, “I wish the bank would have looked at it with a different lens, but they didn’t, and that’s that.”
He expresses dismay at the situation the receivership creates for vendors and customers of InterGroup. “I appreciated the support of vendors and customers and other service providers who are going to pay a price for our demise,” he says. “I sincerely wish that were different.”
Gloger says he will help Fifth Third Bank wind down the company in an orderly fashion to achieve the best outcome for the InterGroup’s creditors.
Gloger founded InterGroup International in 2006 as a brokerage firm for postindustrial plastics. (See the profile on the company from the November 2010 issue of Recycling Today at www.RecyclingToday.com/article/sky-limit-recycling-today-november-2010.) InterGroup International added processing capabilities shortly after its founding and also had toll processing arrangements in place.
More recently with the general downturn in recycled plastics markets, InterGroup exited the processing space, opting to use toll processors for all of the plastic scrap it handled.
The company was named to Inc. magazine’s list of the fastest growing companies for three consecutive years from 2010 through 2012.
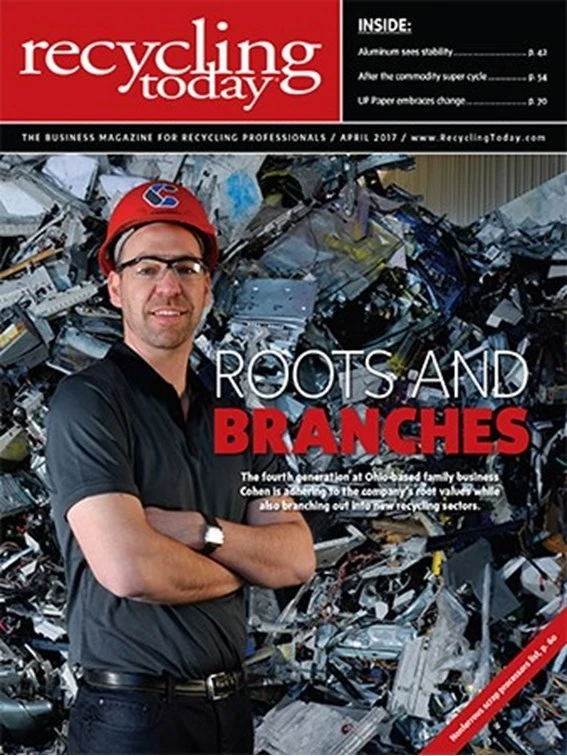
Explore the April 2017 Issue
Check out more from this issue and find your next story to read.
Latest from Recycling Today
- Recycled steel price crosses $500 per ton threshold
- Smithers report looks at PCR plastic’s near-term prospects
- Plastics association quantifies US-EU trade dispute impacts
- Nucor expects slimmer profits in early 2025
- CP Group announces new senior vice president
- APR publishes Design Guide in French
- AmSty recorded first sales of PolyRenew Styrene in 2024
- PRE says EU’s plastic recycling industry at a breaking point