
Most material recovery facilities (MRFs) operating today were designed to process a commodity composition that no longer exists. Complications created by the evolving ton are compounded by run-of-the-mill problems inherent in previous-generation processing equipment that is approaching end of life. Equipment retrofits can revitalize a MRF by introducing modern solutions to address these problems.
The strategic addition of cutting-edge equipment can correct a MRF’s most significant deficiencies, and the capital investment can be recovered quickly. However, no two retrofits are the same, and careful analysis and planning are required for success. The most effective retrofitting processes emphasize analytical methods and system modeling from start to finish to maximize the value of capital dollars and ensure that retrofits are well-integrated and beneficial from day one.
Identify the opportunity
We begin a retrofit by broadly identifying an opportunity that can be addressed. Questions like “Why is this investment necessary?” are discussed with the operator at a conceptual level. Project goals should be quantified to some extent and could include improving throughput, recovery, quality or safety; adding materials; changing output specifications; reducing residue; or a combination of these. Challenges to achieving these goals typically will be external factors that are out of the operator’s control, such as inbound material quality or composition; market conditions; internal storage and logistics issues; or existing equipment becoming obsolete.
For example, quality requirements are dictated by market conditions. If commodities consistently are being sold but profitability is lacking, a retrofit can target recovery rates or throughput by increasing automation. This type of thinking can be applied to individual commodities or to an entire system and can act as the catalyst for a further retrofit investigation.
A systemwide quantitative analysis should be performed to verify that an opportunity exists and has cost-effective solutions. While operators might be hesitant to perform a thorough analysis of their MRFs, without quantitative analysis, they make retrofit decisions based solely on observations and rudimentary inbound/outbound shipping information. Although useful, this information does not tell the full story. Analytical approaches such as process flow diagrams and mass balance analyses can identify cost-saving opportunities that might not be obvious.


Do the analysis
Characterizing a MRF in a mass balance analysis requires an accurate process flow diagram (PFD). A PFD is a block diagram that tracks commodity paths through divergent points in the MRF and identifies each place where automatic or manual sorting is performed and materials are either positively or negatively sorted. Each divergent point in the process line is represented by a block, and arrows indicate the branching paths of commodities. Many operators are familiar with PFDs and might already have an accurate PFD of their MRFs on hand.
Next, a mass balance model is developed. Flow rates of each commodity are benchmarked at the divergent points of the PFD in tons per hour. Both the input and output composition percentages are calculated. Determining the mass balance at each divergent point in the processing line is achieved through sample testing at every point or at specific points of interest within the system. Sample testing can be supplemented by careful observations of the material flows, reducing the need to shut down the line.
The mass balance at each divergent point can be adjusted based upon a range of equipment performance levels. The total MRF inbound tons per hour must equal the total MRF outbound tons per hour. Mass balances at each divergent point are calculated in an iterative process until overall mass balance is achieved. These calculations will include a factor of safety that allows MRFs to specify either a range or maximum performance criteria for a new equipment retrofit.
The resulting mass balance model provides MRF operators with an accurate representation of how each commodity flows throughout the facility. This is an invaluable tool for identifying deficiencies and specifying the right equipment.
Manipulating parameters of the model, such as inbound composition, quality or quantity, can provide insight into the flexibility of the system by projecting performance under varying external conditions. Unforeseen problems, such as bottlenecks, might present themselves, allowing the operator to act preemptively. This methodology is useful and necessary during the issue identification stage of the retrofit.
Mass balance modeling also allows detailed financial analysis to be performed in anticipation of a retrofit. From this mass balance model, a fiscal value can be determined at each divergent point, and the least profitable components can be identified as potential targets for a retrofit. The potential for removing or replacing manual sorting positions or equipment can be examined, and the cost savings and return rates of various retrofit ideas can be evaluated.
The financial impacts of downtime, overtime or anticipated service disruptions should be incorporated into the financial model. This could include costs to reroute incoming material if the existing tipping area cannot house material that will accumulate during the disruption.
Once practical retrofits are identified, the mass balance model should be modified to include the proposed new equipment. The model can test the robustness of the retrofit design by analyzing the effect that changing system parameters has on the return rate. In the same way, equipment specifications (throughput, size, recovery percentages) can be optimized. These will form the basis of the “performance guarantees” to be met by equipment vendors.
Detailed financial modeling will make it easier for an operator to obtain capital funds for the retrofit by providing a predictable return rate. When calculating return rate, it is important to remember that it should compare the cost of the retrofit to the cost of operating the system without the retrofit. In most scenarios, if no retrofit is performed, the operation and maintenance costs will increase rather than remain constant.
Generate a model
The integration of new equipment into the processing line is uniquely demanding. Especially in older MRFs that have already seen their fair share of retrofits, space is limited.
In these scenarios, state-of-the-art on-site 3D scans can be used to generate models of the existing conditions. These scans generate 3D computer-aided design (CAD) drawings that are accurate to one-quarter of an inch. The CAD drawings of proposed equipment and associated components (platforms, stairs, compressors, electrical panels and so on) can be placed virtually in the MRF so that potential locations can be evaluated.
This step allows for a detailed installation plan to be developed and also reduces the likelihood of time-wasting integration problems, such as interference from existing infrastructure, at a later date in the project.
Collaborate freely
It is important to foster a team environment among the operators, equipment suppliers and contractors. When operators and equipment suppliers can collaborate freely, the risk of unplanned disruptions or finger-pointing drops. All parties need a clear definition of the scope of work; problems can arise where the scopes overlap.
Progress meetings that focus on open communication among all parties should be frequent. Schedules should be updated regularly, and the operator should be given sufficient notice to plan for disruptions. To help foster a team mentality, we have found it helpful to invite members of the operations staff to tour equipment installations that are similar to the retrofit.
In a recycling industry with razor-thin margins, it is imperative to maximize the value of a capital investment. And with more and more MRFs aging out of effectiveness because of internal and external factors, retrofits have become a common tool for bolstering a sorting system.
To properly execute a retrofit, system designers must contend with rapidly changing technology, inbound material and market demands. If not performed properly, a retrofit is an expensive mistake that can either hurt chances of receiving capital funds in the future or, worse still, require the immediate injection of additional capital to fix new problems that were introduced by the retrofit.
When done correctly, a retrofit identifies and examines deficiencies throughout a system and applies the most cost-effective solution as verified by analysis and quantitative models. Proper preparation ensures that the right equipment, with the right specifications, is integrated into the system with minimal downtime.
In our 30 years of experience in designing and retrofitting MRFs, RRT has performed hundreds of successful retrofits on behalf of MRF owners and operators. In each of these projects, we have found that the key to our success has been our ability to apply analytical methods and system modeling to a problem.
Investing time and resources into analysis will pay off. Stakeholders will know that their goals are being addressed, and operators will be confident in the success of their retrofits.
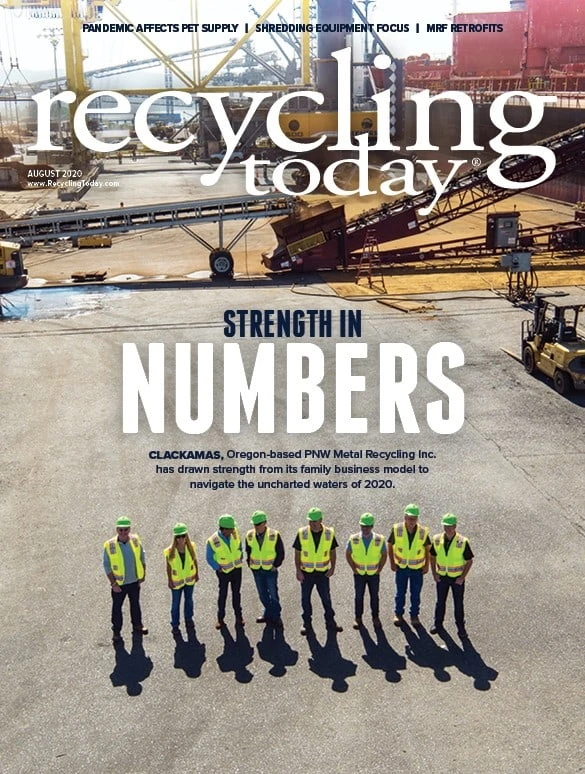
Explore the August 2020 Issue
Check out more from this issue and find your next story to read.
Latest from Recycling Today
- ReMA opposes European efforts seeking export restrictions for recyclables
- Fresh Perspective: Raj Bagaria
- Saica announces plans for second US site
- Update: Novelis produces first aluminum coil made fully from recycled end-of-life automotive scrap
- Aimplas doubles online course offerings
- Radius to be acquired by Toyota subsidiary
- Algoma EAF to start in April
- Erema sees strong demand for high-volume PET systems