Carthage, Mo.-based L&P Wire Tie has developed what it is calling the industry’s first removable tying module as part of a new L&P Pinnacle Wire-Tie System. It is designed to interface will all major baling machines, and L&P Wire Tie 330 and 340 models can be retrofitted with the new system.
The L&P Pinnacle Wire-Tie System featuers a removable Core module within the Pinnacle Knotter. Specifically, a SafeLatch enables operations personnel to access the Core, remove debris and insert a replacement module. This design allows 80 percent of the wear parts to be replaced in less than five minutes, according to the company.
“As the final step in the baling process, the wire-tie system simply cannot slow down the bundling of materials,” says Jim York, president of L&P Wire Tie. “In many instances, the market has come to accept downtime of the entire system while the wire-tie component is repaired. It’s not acceptable anymore with the availability of a product that directly improves the efficiency and productivity of the recycling center.”
The L&P Pinnacle Wire-Tie System is capable of handling bundles of various sizes requiring 13 to 18.5 feet of wire per bundle, the company says. L&P’s four-twist knot approach enables waste managers and recyclers to use wire with greater yield that delivers the same performance as more expensive wire diameter options, according to the company.
L&P Wire Tie Systems is a division of Leggett & Platt Inc. More information is available at www.lpwiretie.com.
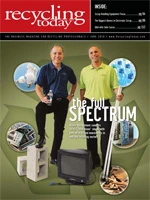
Explore the June 2010 Issue
Check out more from this issue and find your next story to read.
Latest from Recycling Today
- IDTechEx sees electric-powered construction equipment growth
- Global steel output recedes in November
- Fitch Ratings sees reasons for steel optimism in 2025
- P+PB adds new board members
- BlueScope, BHP & Rio Tinto select site for electric smelting furnace pilot plant
- Magnomer joins Canada Plastics Pact
- Out of touch with reality
- Electra names new CFO