
Middlefield, Ohio-based Resource Material Handling and Recycling Inc. was looking for a way to speed up its method of turning bulk shipping containers and pallets into regrind. The answer officials found is an Avian G80/160 extra-heavy-duty granulator, made by Avian (USA) Machinery LLC, West Chicago, Illinois.
“Before we had the Avian, we were having to cut [the container] bases in half or quarters, and it was just a slow process. We were probably getting 8,000 pounds a day if we were lucky,” says Josh Jones, CEO and owner of the company (pictured above), which also is known as Resource MHR.
Resource MHR sells, leases, repairs and recycles reusable collapsible shipping containers and pallets throughout the U.S. The collapsible containers are made of high-density polyethylene (HDPE) structural foam, while pallets are made of polypropylene (PP) or HDPE and often have fillers, such as talc or glass. Typically, the bulk containers that Resource MHR granulates have bases that are 48 inches by 45 inches.
“Right now, because of the throat of the machine and how powerful it is, we can take the sizes that we normally had to cut on the band saw, like a 48 by 64, and the whole base will go down the throat of the machine,” General Manager John Nemet says. “It’s awesome. We’re very happy with it.”
The G80/160 has a hopper opening of 67 inches by 40 inches, a chamber opening of 32 inches by 64 inches and a maximum output of 5,000 pounds per hour. According to Avian, the 320-horsepower machine can handle HDPE pallets, agricultural film and thick sheet, along with other materials.
Resource MHR typically repairs about half the containers it takes in, mainly from the automotive market. Broken container bases often can’t be fixed, so they are granulated. Container walls usually can be repaired. The company now grinds 1.5 million pounds of structural foam monthly. Resource MHR sends its regrind to outside injection molding companies to be made into new containers.
“All our regrind generated from collapsible containers goes back to the molders to make more containers, and all our pallet regrind goes back to the molders to make more pallets,” Jones says. “Our customers love it because they’re made of 100 percent regrind. There’s a lot of containers out there that you can buy that are made from virgin resin, which makes it recyclable but not made of recycled material.”
Speed has been a big advantage with the new machine, which Resource MHR has had for about a year at its Parkman, Ohio, facility. “It’s crazy how fast it can eat the container and spit it out,” Jones says. Before, “we didn’t have a machine that could put out the regrind we needed to send to our molders to keep up with the production we needed to mold our containers for our leasing pool.” The entire reduction process takes about 20 seconds.
Before acquiring the Avian machine, Resource MHR relied on a shredder and grinder combination, which it is still using to process non-HDPE products, including hard plastics, such as nylon. The shredder reduces the material to about the size of a softball; then it goes to the grinder. “So it’s two size reductions,” Jones says.
“With this one, you just throw it in, and it takes them from a base down to a half-inch piece of regrind in seconds,” he says of the Avian machine.
The shredder has about 80 teeth that need to be replaced frequently. Material can get stuck underneath the conveyor between the shredder and grinder, causing jams or rips in the conveyor belt. “Then you’re down for a week.”
With the Avian machine, he says, “There’s less to worry about here, less moving parts. I just want to simplify this place as much as possible. And Avian has helped us do that,” Jones says.
The only challenge Jones and Nemet have seen with the new machine is a variable that most equipment is prone to: operator error. “We’ve had people throw metal in there,” Jones says. “Which, thank God for the horsepower, that it can usually chew the metal up, and our magnets catch it.”
By contrast, he says, the shredder/grinder cannot handle metal. “This grinder is only 75 horsepower; if you threw metal into it, it would just come to a screeching halt.”
Nemet says many workers at the Parkman operations handle the containers before they enter the machine. “They break down a container, they make sure everything’s stripped from it,” he says.
Resource MHR also employs dust collectors and magnets. “They’re pretty simple machines,” Jones says. “There’s not much preventive maintenance that goes into them.”
The Avian machine also has been good for Resource MHR because of the infrequency of blade changes, which now are necessary only after processing 160,000 to 180,000 pounds, Nemet says. “That’s unheard of. Normally, after 40,000 pounds, you are switching blades out depending on what you’re grinding. With this thing, the blades are very strong, and we’ve had some good luck with them.”
Resource MHR is starting a new leasing and recycling operation in Charlotte, North Carolina. The company will ship the shredder/grinder to Charlotte during the beginning of this year. It plans for the Charlotte site to do the same work as the Parkman plant. Resource MHR also has sister companies in Birmingham, Alabama, and in Laredo, Texas, to keep shipping rates low for its customers.
Jones, who has been in the plastics recycling business for 15 years and has been working with grinders for the last six, is seeing a positive trend toward making more products out of regrind. “Over here, I think the government should get involved and make people use regrind. But they don’t. But it’s become safer, there’s a lot of good technology that puts out a good product. People really aren’t afraid to use regrind as much as they were.”
For more information: Avian (USA) Machinery LLC, 630-687-9876, www.aviangranulator.com, Resource Material Handling and Recycling, 888-934-0905, https://resourcemhr.com
Get curated news on YOUR industry.
Enter your email to receive our newsletters.
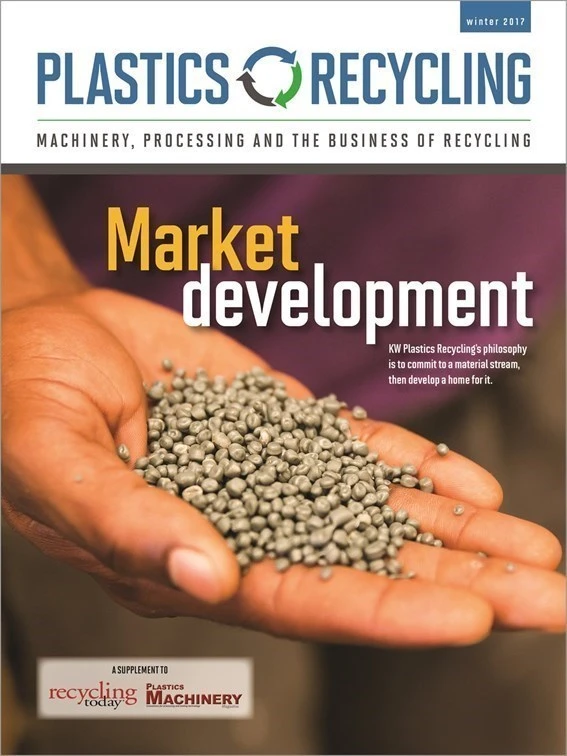
Explore the February 2017 Plastics Recycling Issue
Check out more from this issue and find your next story to read.
Latest from Recycling Today
- Circular Services breaks ground on north Texas MRF
- Tariff uncertainty results in choppy nonferrous scrap flows
- CATL, Ellen MacArthur Foundation establish battery partnership
- Greif announces price hike for all grades of URB products
- Ascend Elements appoints new president, CEO
- Culligan International to provide aluminum water bottles at Chicago running events
- Returpack reports increased DRS activity in Sweden
- Trade groups align against European export restrictions