
A story parents share with young children envisions three pigs building houses for themselves as protection against a big, bad wolf.
Of the three building materials they try—sticks, straw and brick—only brick is left standing.
Too bad they didn’t consider plastic.
Two companies in Canada—Ecoplast Solutions Inc., with locations in British Columbia and Alberta, and its partner, JD Composites, Meteghan, Nova Scotia—are writing a new chapter for used water bottles, using them to create structures that fight climate change. The modular homes they produce are warm, strong and resilient, thanks to integral foam cores made of recycled polyethylene terephthalate (PET).
“So far, there’s six in Canada, with about six or seven more to go up by the end of this fall between our partners out East and ourselves,” says Kelly Rogers, managing partner of Ecoplast, who is based out of Lloydminster, Alberta. “There’s six in the world here so far, and each house has about between 600,000 to a million bottles.”
Using a proprietary process, JD Composites shreds, pelletizes and melts down plastic bottles that otherwise would be sent to landfills or incinerators. It then extrudes the recyclate into foam boards and bonds them with special in-house laminates to create sealed monolithic structures.
Homebuyers can work with designers at JD Composites or Ecoplast to create their own storybook houses or choose from designs that already have gone up. Prior designs bear names like Prairie Paradise Bungalow, which might look at home in a middle-class, postwar subdivision, and Saskatchewan Sunrise, which features a second-story deck and a generous helping of windows to exploit the sun’s rays.

Flat-roof models typically feature a rooftop deck or terrace.
In addition to breathing new life into end-of-life plastics, Rogers says the structures offer a number of advantages over homes built with more traditional materials.
They are well-insulated and immune to rot, mold and bugs, such as termites, he says, and also offer the potential for an attribute not often associated with home construction: speed.
“We make all the panels in our facilities, so it’s all controlled indoors,” Rogers says. “All the openings are precut; everything’s planned out. And then, when we go on-site, we just stand them up, put them together, and it’s just quick.”
Workers can assemble the frame of a home in just 14 to 17 hours, he adds.

As long as a customer has purchased land, Rogers says the homes can come together, from drawings to move-in-ready condition, in two or three months. That includes a couple weeks for the design and engineering process, four to six weeks for the manufacturing process, a week for shipping and another week or so for on-site work, including finishing.
The foam cores are compatible with many exterior finishes and building materials, including vinyl, cladding and paint.
A heating, ventilation and air-conditioning specialist, Rogers joined Ecoplast because he was intrigued by plastics’ insulating potential. The process delivers—with 6-inch foam cores providing an R-value of 30, he says. That’s significantly higher than the levels of insulation Canadian province building codes require, contributing to levels of energy efficiency nearly double other newly built homes. Depending on the structure and jurisdiction, other homes in Canada can have effective R-values of 17, Rogers adds.
“If you’re in the house, you’d never know that it was made from PET plastics,” he says. “It’s your building envelope, so, it’s your structural [frame], your insulation, air barrier, vapor barrier, all in one.”
According to Ecoplast, the homes are resilient against many issues associated with climate change, including floods, storms, Category 5 hurricane-force winds and extreme temperatures. The company says the foam cores can achieve a Class A fire rating, depending on the exterior treatment process, meaning they will not release incandescent particles or allow flames to spread. Compared with other insulation materials, the cores burn with less energy and release less toxins.

Cost depends on a homebuyer’s particular requirements, but Ecoplast homes are comparable with other new builds.
“It depends on the design, but a 1,600-square-foot home … might be around $130,000 for the building envelope, assembled on-site. … And then you add your windows and doors and finish it out,” he explains. “It’s on par in a lot of areas with stick-build and other conventional building methods.”
Four years after JD Composites began building PET-foam-core homes, Rogers still expresses admiration for plastics’ insulating capabilities. But the project’s potential goes far beyond those benefits.

Rogers says, “The opportunity to make an environmentally friendly product” drives him. “And having the flexibility to turn it into something, to create someone’s dream home and be creative. It’s something that works really well.”
Ecoplast is poised to grow, he says.
While the company aims to build about six to 10 homes per year, it says feedstock is nearly endless, even considering how much PET already is recycled.
“There’s enough out there in Canada above ground that we could build 3,500 homes a year for 40 years,” he says. “That’s just currently, and there’s a lot more made every day.”
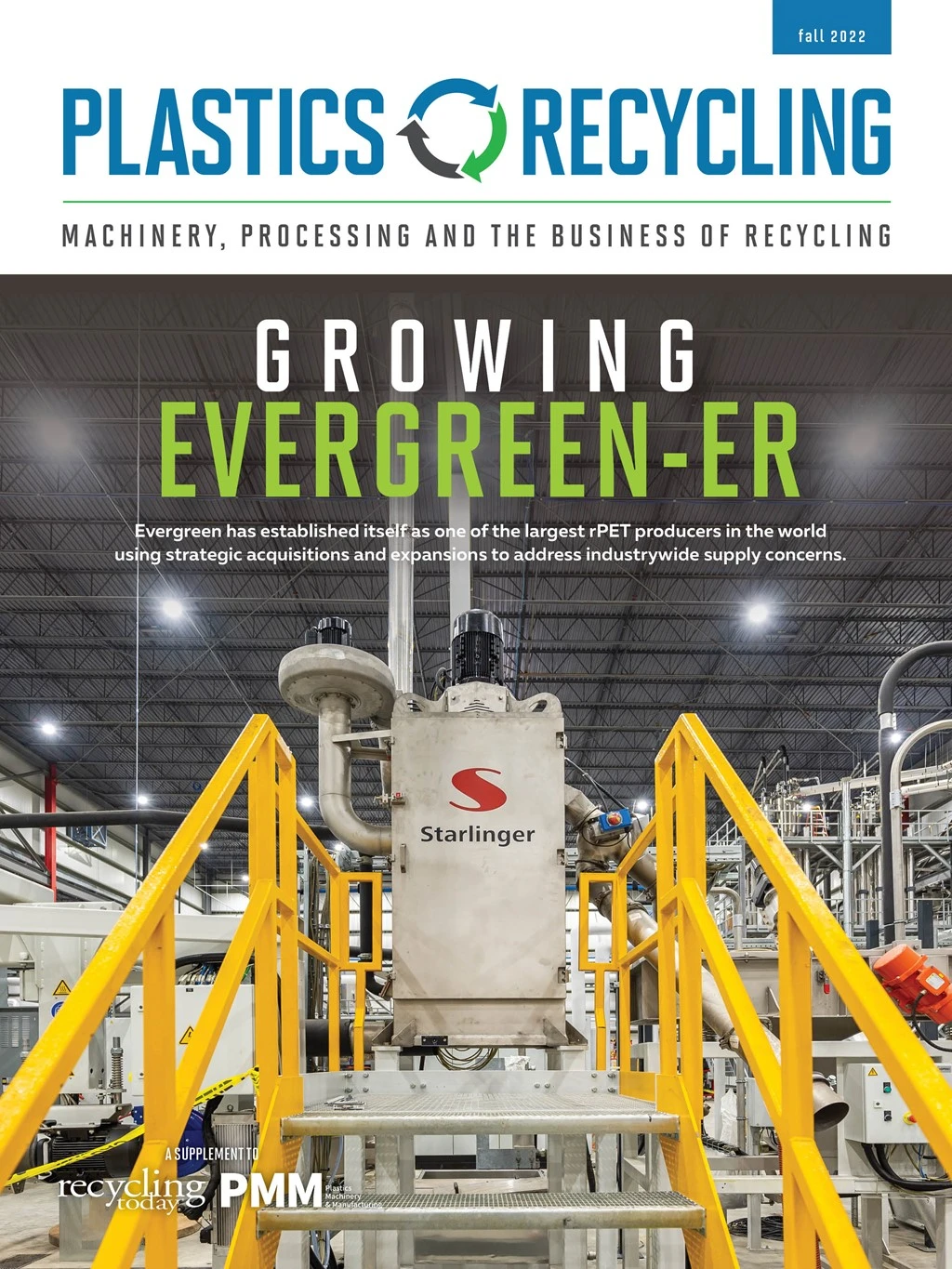
Explore the Fall 2022 Plastics Recycling Issue
Check out more from this issue and find your next story to read.
Latest from Recycling Today
- APR, RecyClass release partnership progress report
- Clearpoint Recycling, Enviroo sign PET supply contract
- Invista expanding ISCC Plus certification program
- Redwood partnership targets recycling of medium-format batteries
- Enfinite forms Hazardous & Specialty Waste Management Council
- Combined DRS, EPR legislation introduced in Rhode Island
- Eureka Recycling starts up newly upgraded MRF
- Reconomy Close the Gap campaign highlights need for circularity