
When reviewing the recent successes at Penn Waste, York, Pennsylvania, much of the company’s achievements can be credited to its ability to adjust to new market conditions. Being adaptable has helped Penn Waste to weather the storm of China’s import bans on specific scrap commodities and stringent specifications for incoming material by creating a new recovered paper grade—what the recycling industry calls a hard mix—that is sold into new markets beyond China.
In January 2018, Penn Waste set a record for the number of tons recovered in a month at its 96,000-square-foot single-stream material recovery facility (MRF). At 16,000 tons in January, Tim Horkay, Penn Waste director of recycling operations, says the MRF’s volume grew 100 percent from the 8,000 tons per month it processed when it opened in 2015.
The company completed a $3.5 million retrofit project at its Manchester, Pennsylvania, MRF in July 2017 to allow it to adapt to the container-heavy composition of the incoming residential material stream created by the reduction of newspapers and other papers.
The upgrades included one of the first investments in Max-AI artificial intelligence (AI) technology from Bulk Handling Systems (BHS), Eugene, Oregon, and a re-engineered container line, which includes three new optical sorting units that complement the MRF’s three original optical units, among other updates.
“The retrofit has allowed us to increase throughput, increase material capture and reduce
China changes all
While the MRF attempted to comply initially with China’s strict standards, the measures it took weren’t enough to meet the 0.5 percent prohibitive requirement. Penn Waste slowed its machines down by 10 tons per hour and added workers, all after its retrofit had been completed.
Horkay explains, “The annualized cost was significant for us to slow the belt down and add to the
He continues, “We switched gears and actively went out and marketed hard mix, combining packs, and sped up the machines again.
Penn is producing around 4,100 tons per month of hard mix material, which is comprised of more than 30 percent old corrugated containers (OCC), “other papers” and an unidentified amount of prohibitives, Horkay says. About 80 percent of this material is sold to the Indian market.
“Penn Waste has conducted numerous trials [with the hard mix], but it’s part of being adaptable to these markets,” he says. “We have to continue to dive into new markets and make a product that’s accepted.”
“The retrofit has allowed us to increase throughput, increase material capture and reduce head count.” – Tim Horkay, Penn Waste director of recycling operations
A vision for sorting it out
Penn Waste’s upgraded MRF sits on a purpose-built recycling campus. More than 100 trucks leave Penn Waste’s South Central Pennsylvania terminal each day to collect recyclables and waste from 185,000 residents and 4,500 commercial accounts, which include front-load services as well as industrial compactor services. (In the flow-controlled county of York, Penn Waste cannot landfill material and instead sends residue from the MRF to a nearby Covanta waste-to-energy facility.)
The Max-AI technology is designed to improve container line performance. At Penn Waste, the Max-AI Autonomous QC (AQC) unit works in conjunction with an existing NRT SpydIR optical sorter, targeting polyethylene terephthalate (PET) plastics. The technology uses AI to identify non-PET items for the AQC to pick and return to the container line’s onset.
In addition to the Max-AI AQC, Penn Waste added three new NRT optical sorters coupled with an NRT MetalDirector. The company also added a Nihot SDS 800-i to clean larger volumes of glass.
Glass makes up about 16 percent of Penn Waste’s total incoming material stream. Horkay says about 90 percent of this material is removed early in the sorting process with screening technology.
Penn Waste markets the cullet to a Pennsylvania company that color sorts it with optical equipment and then sells it.
On its “last chance” residue line, Penn Waste added an optical sorter to remove containers and metals.
The optical sorters enable the automated separation of additional plastic commodities, including polypropylene (PP) and colored and natural high-density polyethylene (HDPE).
In two nine-hour shifts five days per week, 67 workers
Horkay says the AI technology is driven by a vision system, which collects data as material passes by on a belt. “The future of the vision system will allow the robots to see the material coming in and adjust the system downstream to handle it by slowing belts and talking to the robots in front,” he explains.
Other advantages of the robotic and AI system include a cleaner material stream on the back end and more yield per pound for plastic, Horkay says.
New opportunities
With new equipment throughout the MRF, Horkay says Penn Waste is looking ahead to other new opportunities.
The robot and AI system offer new ways to recover material as well as new job classes. For every three robots, one technical
Horkay explains, “It is creating another job class for us—a more technical job class—so we’re hiring more skilled employees to run these.”
Entering new markets and recovering additional materials to sell also are goals for the Mid-Atlantic company. Beyond its hard mix grade, he says the MRF is figuring out how to generate additional revenue “by digging deeper into the stream to see what we can recover and make money on.
“Building a sellable product has been the cornerstone of Penn Waste since commissioning the system,” Horkay adds.
Lastly, the company can now offer more insights to its customers through data collected daily on its new system.
“We believe in data and we believe in selling
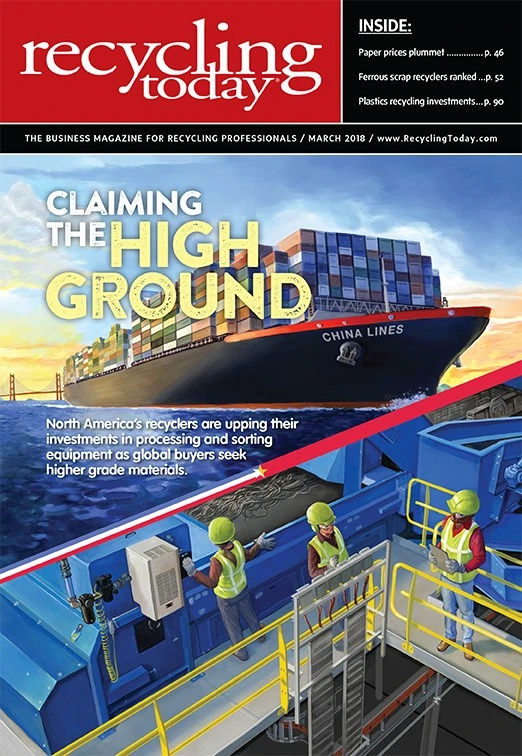
Explore the March 2018 Issue
Check out more from this issue and find your next story to read.
Latest from Recycling Today
- PCA reports profitable Q1
- British Steel mill subject of UK government intervention
- NRC seeks speakers for October event
- LME identifies Hong Kong warehouses
- Greenville, Mississippi, launches aluminum can recycling program
- Cotton Lives On kicks off 2025 recycling activities
- Georgia-Pacific names president of corrugated business
- Sev.en Global Investments completes acquisitions of Celsa Steel UK, Celsa Nordic