
Recycled asphalt roofing shingles have been used for many years by hot mix asphalt (HMA) contractors. HMA contractors have what they call the three "Es" of using any scrap material in HMA:
• Engineering (can we make it work?)
• Environmental (can it be used safely?) and,
• Economic (does this make economic sense?).
Engineering and production issues were discussed in a previous article in this publication ("The Road To Shingle Recycling," C&D Recycler, Volume 4, Number 4, July/August 2002,).
This focus is on economic issues that contractors must consider when using recycled asphalt shingles in HMA. The three key costs for consideration of using recycled asphalt shingles are handling, materials, and processing.
HANDLING COSTS
In many urban areas, high landfill tipping fees have driven the roofing industry to search for alternate uses for scrap roofing shingle materials. Landfill fees can be in the range of $30 to $100 per ton of scrap shingles, depending on the area of the country. Contractors must consider the landfill costs in their area of operation as an element in the establishment of their own tipping fees if they are going to accept shingles for HMA use. The contractor’s tipping fee will generally be somewhat less than the landfill fee.
Transportation costs will often be the critical decision-maker as to whether or not to use recycled asphalt shingles. Trucking costs vary widely across the country. At each location, an analysis will need to be done to determine the economic viability of shipping the shingles. This analysis may be done by the generator of the shingles or the contractor, or both.
MATERIAL COSTS
Recycled asphalt shingles can be generated from a manufacturing facility (manufacturing scrap) or from removal during residential re-roofing operations (tear-offs).
It must be remembered that a typical HMA plant can produce several hundred tons of HMA per hour. If the plant is using shingles in a 5 percent by weight formula, the total amount of shingles required for a typical working day could be 50 or more tons. It takes a lot of material to keep an HMA plant running.
Manufacturing scrap has less contamination, and generally a stable supply of product is available. The HMA plant planning to use manufacturing scrap will need to be relatively close to the shingle manufacturing facility to make the relationship economically feasible. As a relatively "clean" material, the manufacturing scrap can be readily processed for use in the HMA.
But without question, the largest supply of recycled asphalt shingles is from re-roofing operations that produce tear-offs and cuttings. From 6 million to 7 million tons of such material is generated annually. The contractor wanting to use tear-offs will generally be located in an urban or suburban metropolitan area in order to have an adequate supply of material.
The contractor must be prepared to have an employee committed to the shingle operation. It may not be a full-time position, but there must be someone "in charge," particularly when recycling tear-offs. Then, each load of material inbound to the HMA plant must be inspected to ensure that only shingles are being received. Some roofing contractors may attempt to dump "guts, feathers, and all" at the plant to save themselves a trip to the landfill. Contamination in the shingle stream (lumber, concrete, bricks, etc.) can cause significant production problems.
Incoming materials must also be checked for potential presence of asbestos. While not very likely to be present, testing for the substance provides an important safety net for workers at the HMA plant. The person checking the incoming loads will earn his or her keep!
PROCESSING
When the contractor starts to process the recycled asphalt shingles, key issues will arise that can affect the overall economics of the operation. The first decision that has to be made is what type of shredder will be used and how ownership will be handled. Several shredders are available. Contractors must do their homework to determine which is correct for a particular operation. Many of the shredders will produce an acceptable product, so much of the decision is based on equipment availability, local dealer relationships and service availability.
To rent or to buy—that is the question. This is strictly a business issue for the contractor. Some purchase and maintain all their own equipment. Others own nothing: They lease or rent everything. Both business models work–it is strictly an issue of preferences.
Now it’s time to get down to the work of processing the shingles. As was discussed in the previous article, shingle handling is an important part of the proper processing of the materials Any stone products in the recycled asphalt shingles will cause significant wear problems for the shredding operation. Downtime costs the contractor by the minute, so it is critical to keep the shredding operation going. Remember, if the plant is producing 200 tons of HMA per hour, about 10 tons of shredded shingles are needed per hour.
Blending of the shredded shingles with either recycled asphalt pavement (RAP) or crusher fines lets the product be stored and also enhances the handling characteristics of the product. The blending can be done with a front-end loader, or specialized equipment can be used to achieve the proper proportions. How to best blend depnds on availability of equipment, volume of shingles to be used, and specific economic issues for the contractor.
Depending on the type of equipment and the personnel involved, the contractor may be able to produce somewhere between 25 and 75 tons of processed shingles per hour. A good effort for an efficient operation is probably in the 40 to 50 tons per hour range.
The contractor must include in the operating costs cleaning the drum, which is used for heating, drying, and mixing the HMA. This might need to be done two to three times per year, and maybe more with a double-barrel plant. This expense is typically about $1,000 per cleaning.
PUTTING IT ALL TOGETHER
Given these considerations, an overall handling expense generally is in the $12 to $14 per ton range. As contractors get more familiar with the processing, this cost may be reduced at a 5 percent application rate, or about $0.70 per ton of mix.
Tipping fees can be an important part of the financial equation. Tipping fees for scrap shingles can often range from $15 to $35 per ton for manufacturing scrap and from $24 to $45 per ton for tear-offs. The reason for the difference in tipping fees is the amount of effort that the contractor must use to make the shingle product useable. For tear-offs, there will always be some effort to keep contaminants out of the stream of shingles.
Shredder costs depend on the production capacity of the equipment. Low production shredders cost about $200,000, and high production units at least $450,000. The contractor must decide what type of unit will meet the plant production schedule and be most cost effective for the operation. As previously discussed, the contractor must also decide whether to purchase, lease or rent the equipment.
There is a relationship between the percentage of shingles used in the mix and the value of the asphalt in the shingles. Asphalt prices are currently in the $200 or higher range, so as an example, a 5 percent shingle formula for $200 per ton HMA asphalt cement, the value of the asphalt in the shingles is $3 for a shingle that has 30% asphalt. At 3 percent shingles in the mix, the value is $1.80. Shingles also vary in asphalt content.
Using recycled asphalt shingles in HMA can be a win-win proposition. The shingle scrap is put to good use in a product that has good performance, and the contractor can produce a cost-effective product.
Dale Decker is a consulting engineer based in Bailey, Colo. He can be contacted by e-mail at dale@dsdecker.com.
Get curated news on YOUR industry.
Enter your email to receive our newsletters.
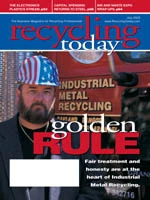
Explore the July 2003 Issue
Check out more from this issue and find your next story to read.
Latest from Recycling Today
- ReMA opposes European efforts seeking export restrictions for recyclables
- Fresh Perspective: Raj Bagaria
- Saica announces plans for second US site
- Update: Novelis produces first aluminum coil made fully from recycled end-of-life automotive scrap
- Aimplas doubles online course offerings
- Radius to be acquired by Toyota subsidiary
- Algoma EAF to start in April
- Erema sees strong demand for high-volume PET systems